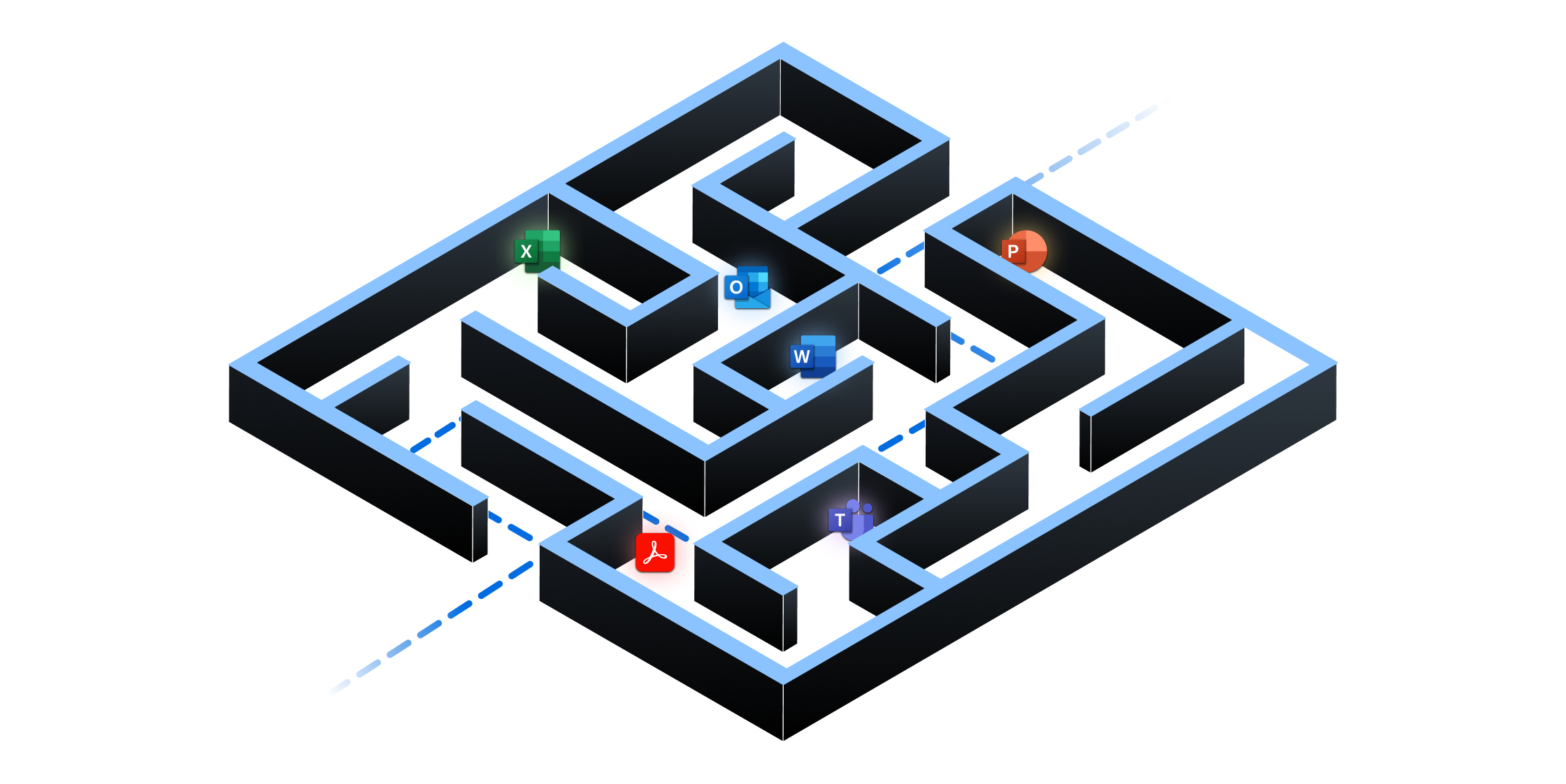
Engineers Spend Hours Understanding the Rationale Behind Decisions
Engineers Spend Hours Understanding the Rationale Behind Decisions
This article is part of the CoLab Research Reports series, where we publish findings from both engineering leader surveys and aggregated, anonymized CoLab data. To subscribe and receive reports to your inbox, click here.
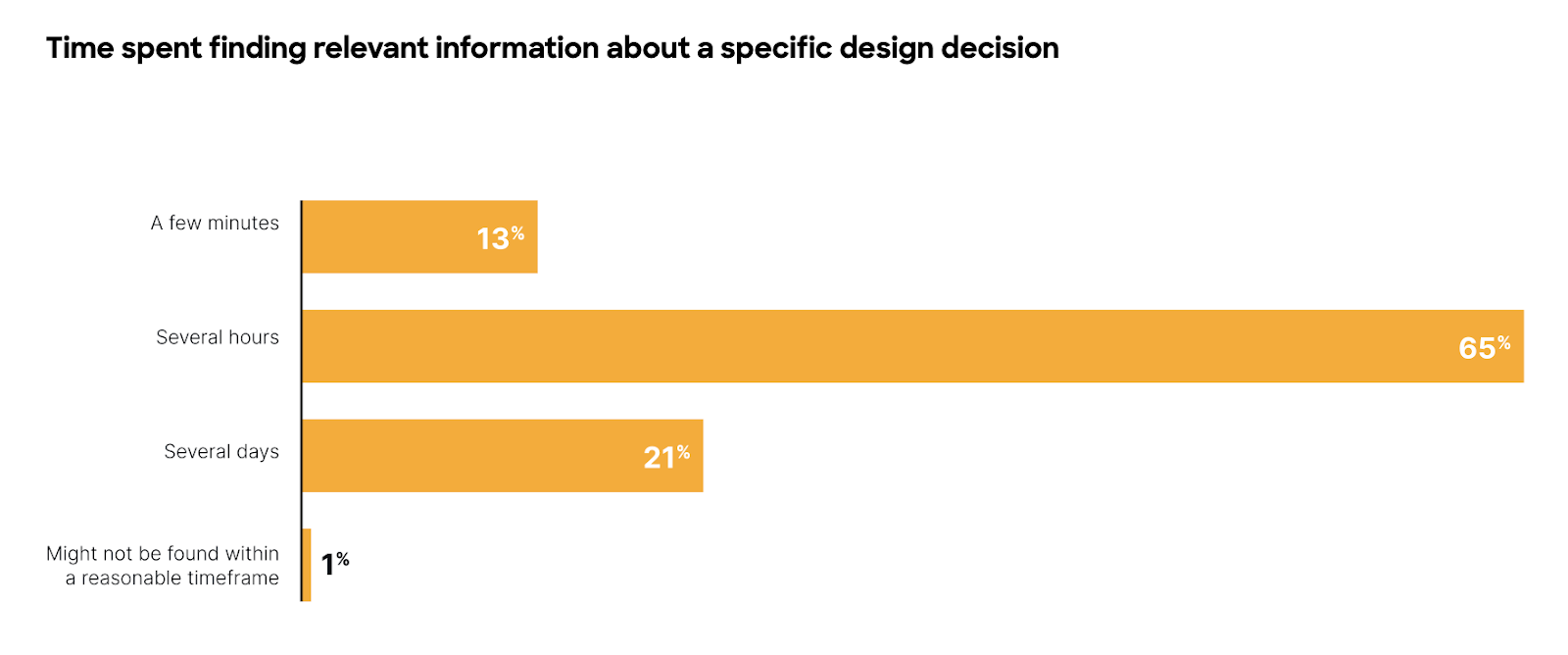
When this finding was first revealed, it wasn’t that shocking.
We’ve heard how hard it is and how long it takes for engineering teams to track down design decisions:
Tier 2 Global Tooling Manager: “You need to be Einstein to track design decisions. Was it a Teams chat or an email? Maybe in a PowerPoint someone sent as an email attachment?”
Director of New Product Development: “With all the tools and the way we work today, it’s impossible to track design data so you can actually access and use it.”
You might not be that surprised either. Thinking on the last design review issue you had to search for, it probably took a couple hours.
But what we’re all missing is two-fold:
- How systemic the problem is
- The downstream implications of hard-to-track-down design decisions
How did design review workflows get this bad?
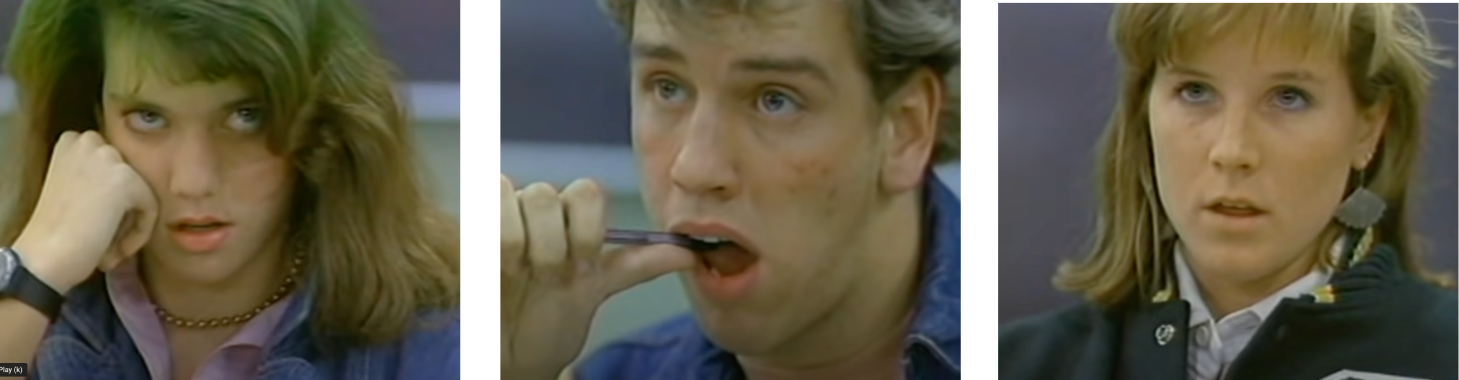
According to this research, 87% of engineering leaders estimate it takes several hours to multiple days to track down the justification for a single design decision.
This problem has become so prevalent that most engineers, especially those who’ve been in the field for a decade or two, just accept it rather than fight it.
Considering the way most teams execute design reviews today – this isn’t all that surprising.
For most engineering teams, a design review workflow looks something like:
- Schedule a meeting with engineering team to flag issues
- Track issues manually in a spreadsheet or notebook
- Resolve high-priority issues
- Schedule another meeting
Or maybe you’re really advanced and there’s a CAD viewer or PowerPoint deck with CAD screenshots in there somewhere.
The problem is exactly this: there’s 3, 4, 5+ places where design decisions live. Not to mention some of those places: phone calls, meetings and desk banter don’t get documented at all.
And here’s the larger problem: this process hasn’t changed in 10-20 years.
Assemblies have never been more complex. The pressure to launch higher quality products faster has never been more intense. And the magnifying glass is starting to shift upstream from manufacturing processes to engineering processes.
Yet, your engineering team is still using disjointed tools that were never meant for early product development decision-making.
What happens when engineers brute force product development
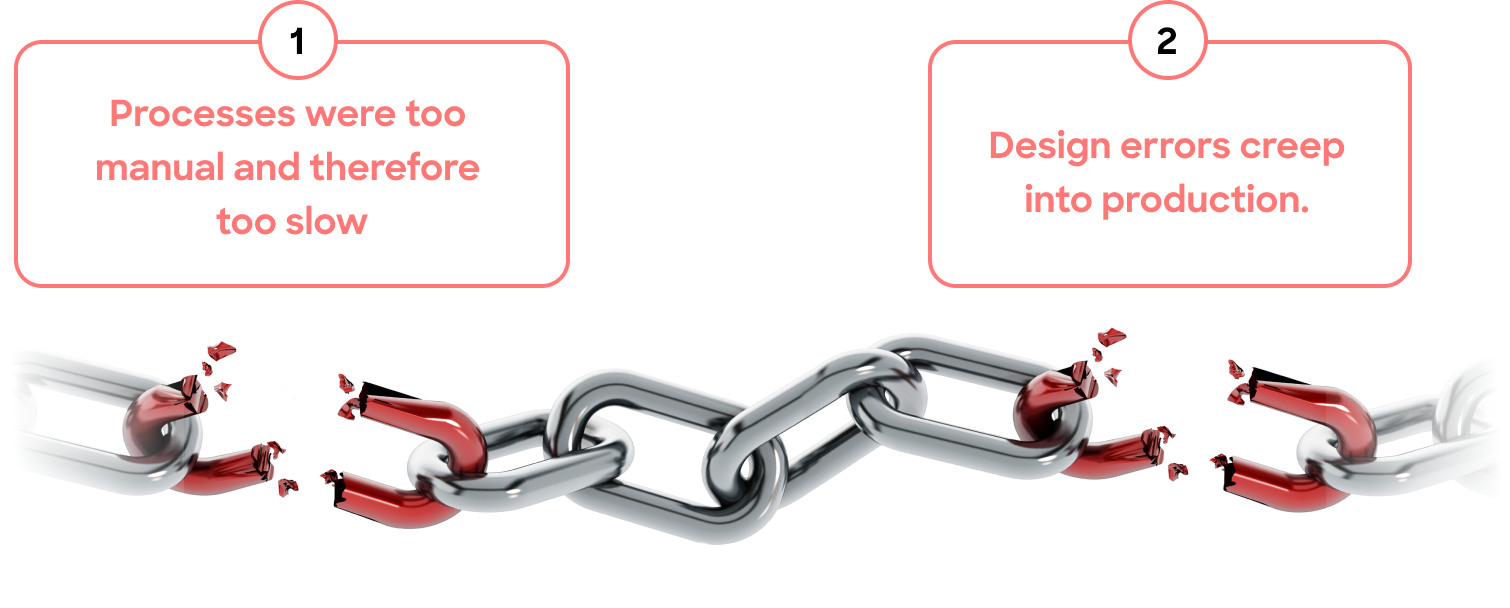
This disjointed workflow is not your engineering team’s fault. And it’s not yours. There hasn’t been a reliable, demonstrable tool, workflow or process to fix design reviews.
That’s why design reviews have gotten this bad. And it’s why your engineering team continues to brute force product development with outdated tools.
And it’s why it takes you several hours to track down that one design decision.
But there’s an unseen problem here.
When it takes several hours or multiple days to find the justification for a single design decision, engineers just stop looking.
If the issue is high priority, they’ll put in the time to find the information. But, if finding the issue is holding up the timeline or risks missing a project milestone, they’ll just let it go.
And when engineers stop looking for enough of these issues:
- 43% of design review feedback never gets tracked or addressed
- 1 in 5 delays are due to miscommunication
- 90% of companies delay product launches due to late stage design changes
This is what happens when engineering brute force product development.
And it’s a vicious cycle:
🔄 Engineering teams conduct design reviews in too many tools
🔄 Then, when it comes to finding a decision made during design review, it takes several hours to multiple days
🔄 So, engineers stop looking and 43% of design feedback is never tracked or addressed.
🔄 And then we hear from engineering leaders that 90% of companies delay product launches die to late stage design changes.
What’s the opportunity cost of hard-to-track-down design decisions?
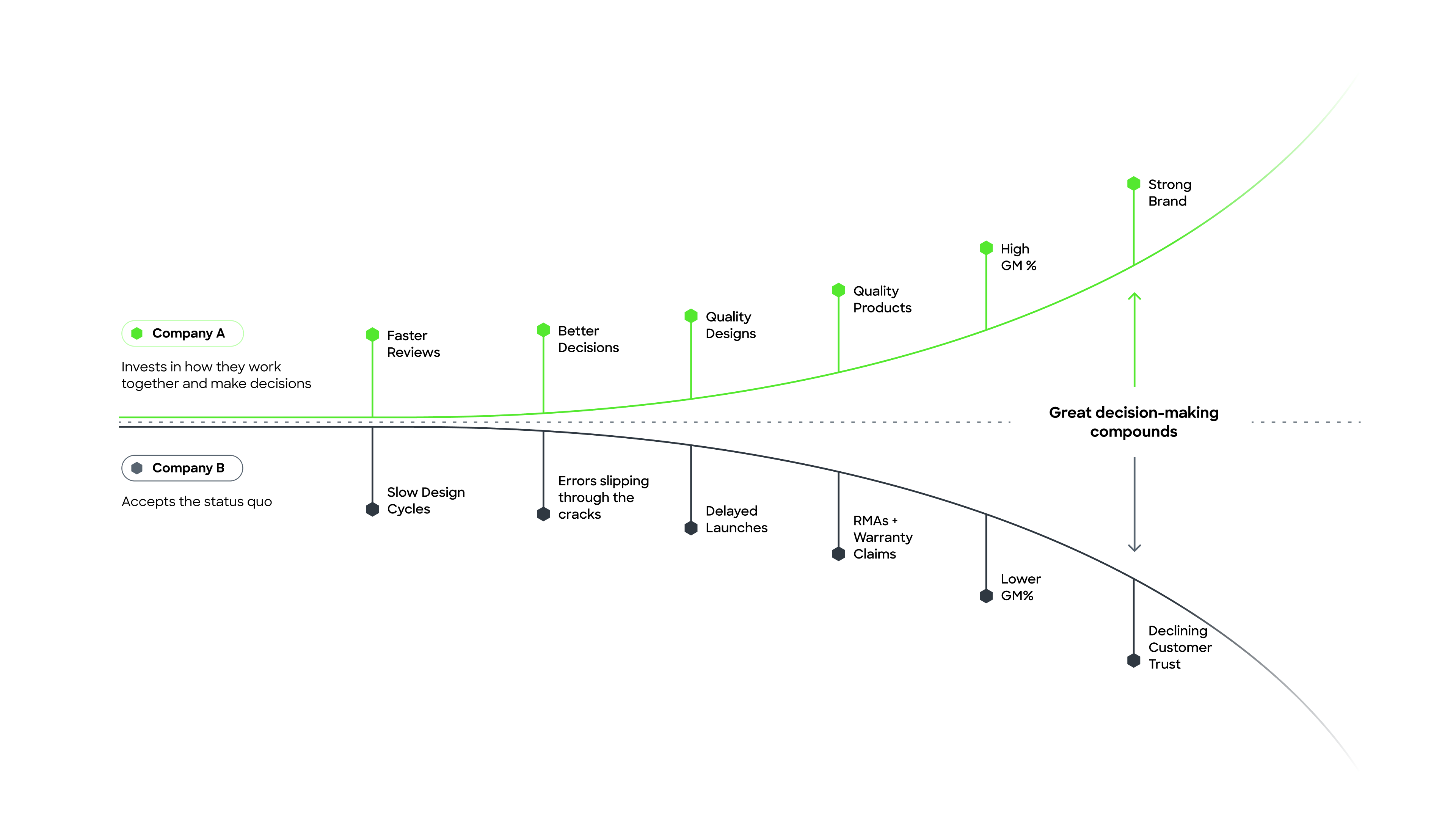
A single product launch delay might not catch the attention of company leadership. Late stage rework might just be a normal part of your NPD cycle.
The opportunity-cost of these frustrations is just not well known.
As a result, downstream manufacturing failures tend to get more attention. Warranty claims, declining gross margins, production failures – these are all tangible metrics that connect to dollars and cents.
However, as companies get more efficient at preventing these failures, the focus starts to move upstream. Declining gross margins can only be tied back to slower time-to-market when activities like reducing unnecessary production costs, negotiating better contracts with suppliers and optimizing the procurement process have already been tackled.
This is where we’re at today.
Manufacturing leaders realize this is no longer enough. Gross margins are still stagnating – or worse, declining. And products are consistently slow getting to market.
So, what’s the solution?
Engineering design review quality is the upstream metric we need
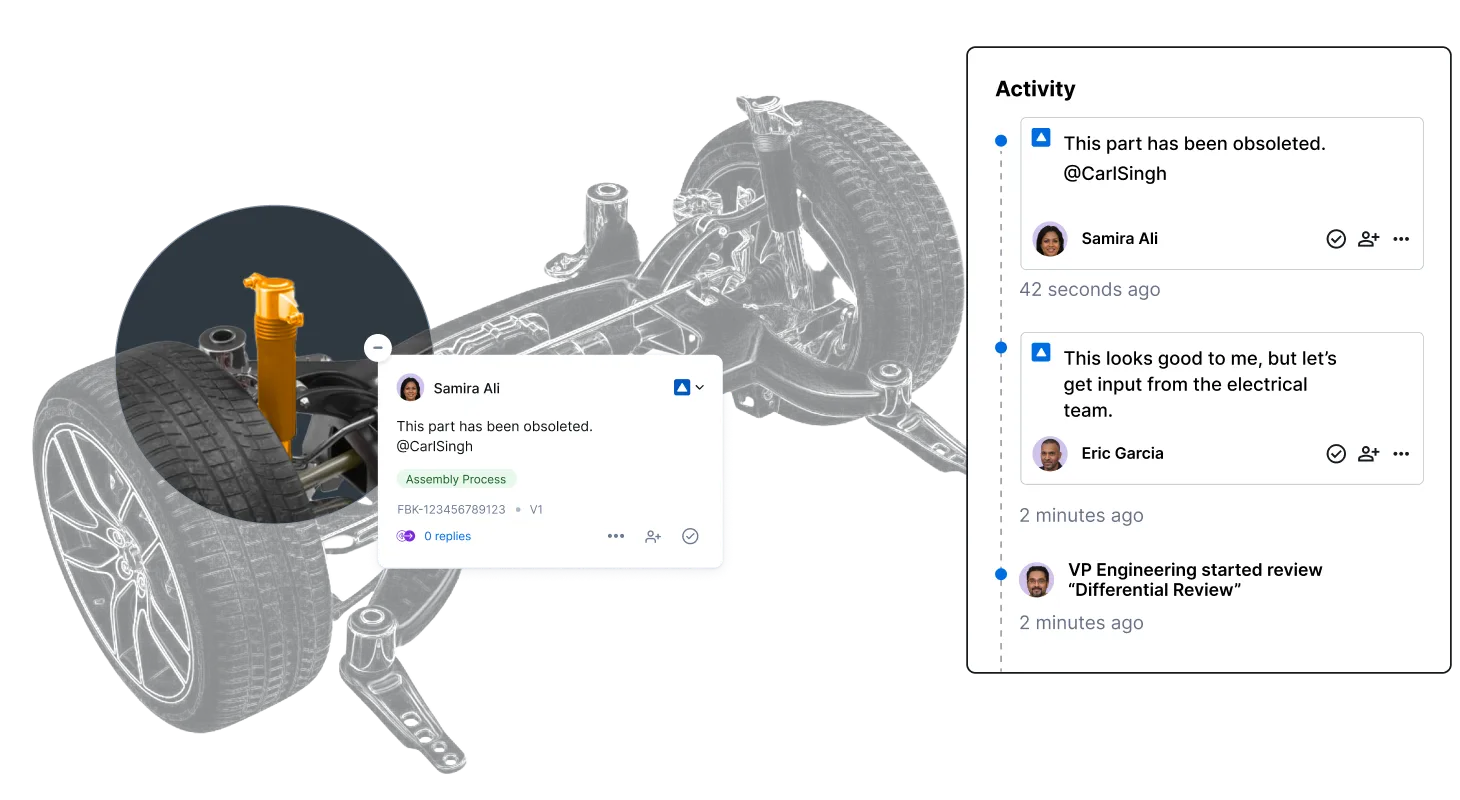
We’re finally paying attention to the metric few others scrutinize: engineering design quality.
The leaders investing in upstream engineering processes, like improving design review or reducing the design review workflow burden focus on engineering excellence.
These companies unlock new levels of effectiveness, cost reduction, and time to market.
Ford Pro saw 30% faster time to market when they started bringing customers into engineering design review.
Hyundai Mobis improved supplier cycle efficiency by 4x.
Mainspring Energy reduced costs by 50%, in half the time, with zero defects.
If you’re like the leaders frustrated with the same strategies for improving design review – more meetings, better PLM use, better project oversight – then now is the time to shift your focus.
Stop settling for hours spent searching for a single design decision.
Stop letting your engineers brute force product development.
Now is the time to invest in design review quality.
Now is the time to invest in engineering excellence.
About the survey
To get greater insight into the state of complex product development processes, we commissioned a survey of 250 full-time employees, 50% of which are Engineering Managers or Directors, and 50% of which are VPs or C Level Executives.
Respondents work in the manufacturing industry, specifically in industrial equipment, heavy machinery, automotive, and consumer hardware, and are split across the US, the UK, and Western Europe.
All respondents work at companies with 1,000+ employees that have already invested in a PDM or PLM system.
This report was administered online by Global Surveyz Research, a global research firm. The respondents were recruited through a global B2B research panel, invited via email to complete the survey, with all responses collected during October 2023. The average amount of time spent on the survey was 5 minutes and 44 seconds. The answers to the majority of the non-numerical questions were randomized, in order to prevent order bias in the answers.
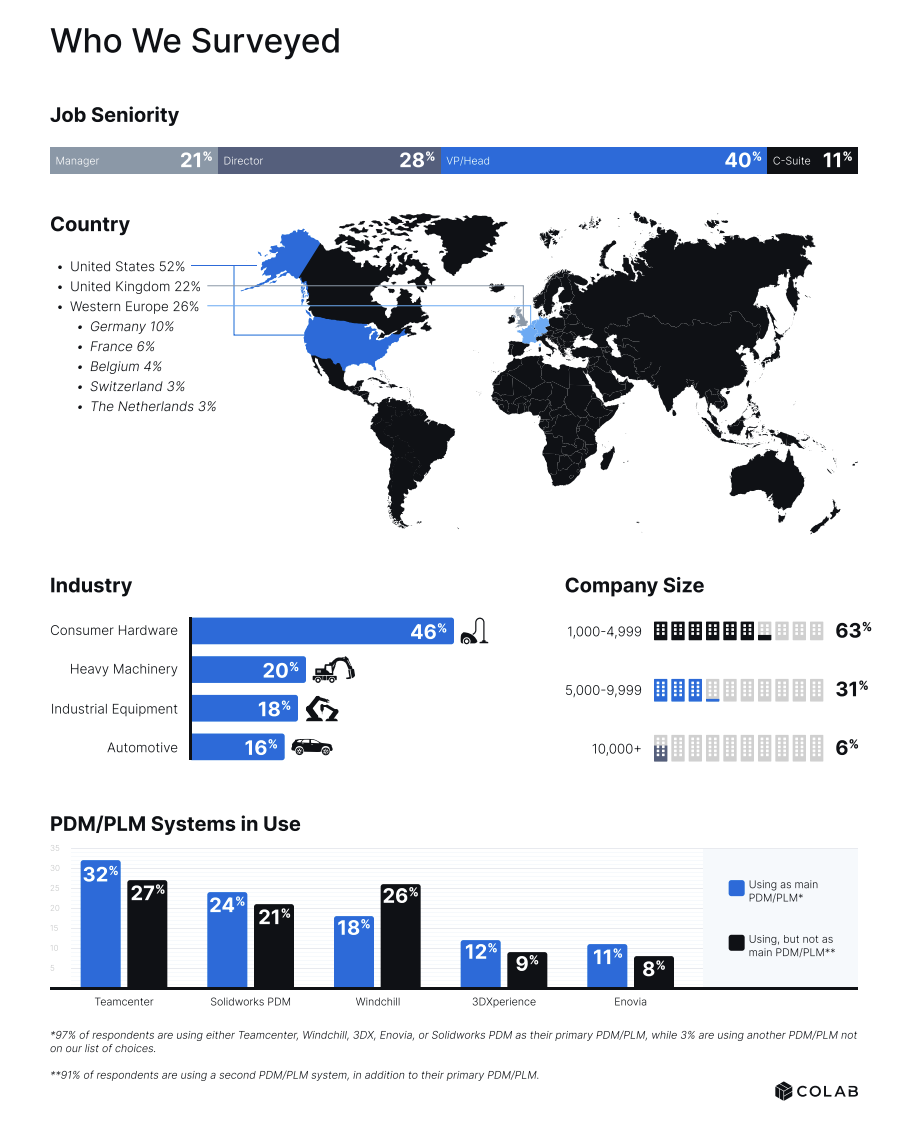
CoLab Research Hub publishes the latest research, tech data and trends to give engineering leaders the resources they need to launch better products, faster.
Quantifying the impact of design review methods on NPD
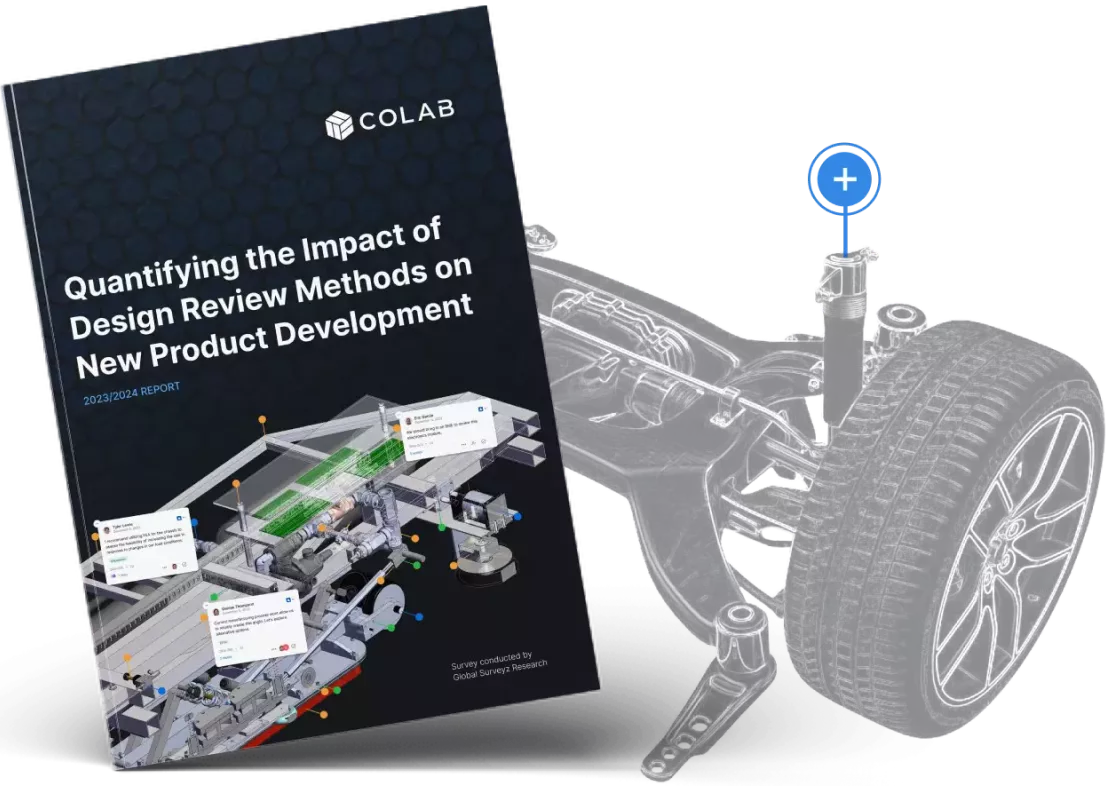