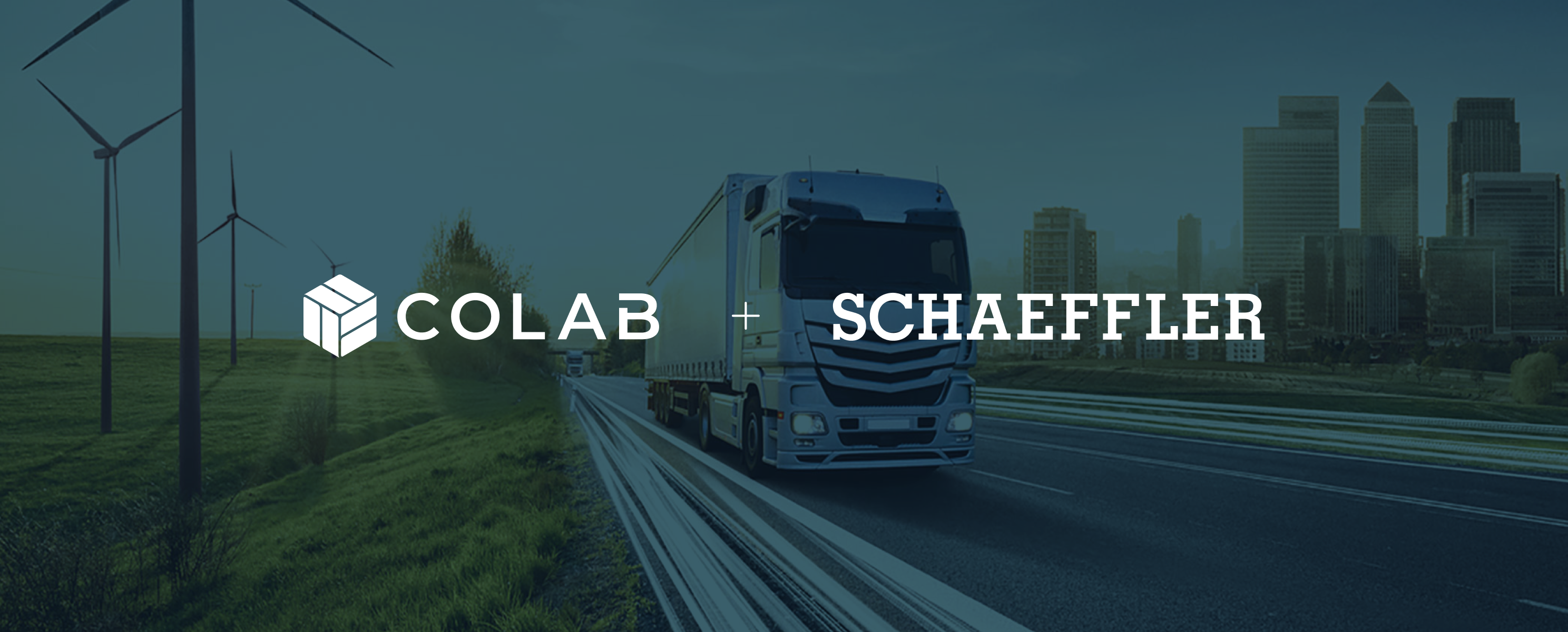
Schaeffler balances design quality and efficiency, with help from CoLab and PTC
Schaeffler is a motion technology company serving major industrial and automotive OEMs worldwide. They are focused on solidifying their market position as a supplier of choice through innovation, agility, and efficiency. The engineering organization will play a critical role in achieving this vision.
In early 2022, Schaeffler entered into a strategic partnership with PTC, deepening their commitment to initiatives such as Model Based Enterprise and Enterprise Traceability. In 2023, Schaeffler kicked off a pilot with CoLab to increase design review speed and effectiveness. Because CoLab is a PTC partner, Schaeffler can take advantage of robust integrations between CoLab’s Design Engagement System and PTC’s Enterprise PLM Windchill.
The Challenge
To achieve their vision of innovation, agility, and efficiency, Schaeffler is investing in improving business processes and collaboration. Because design review quality is a strong predictor of both product development speed and manufacturing efficiency, Schaeffler chose to focus on optimizing design reviews.
Schaeffler’s digitalization team saw three specific opportunities to improve their design reviews:
First, they wanted to maximize the amount of valuable feedback and action items captured in these reviews: "I've spent a lot of time in design reviews and I’ve seen how information can fall through the cracks,” explains R&D Business Analyst Lewis Bragdon. Documenting and tracking design review feedback is a major challenge for many engineering teams. A 2023 industry survey of 250 engineering leaders showed that 42.8% of all feedback generated in reviews is never documented or actioned.
Second, Schaeffler saw an opportunity to simplify review management, driving speed and efficiency:
“Time is a really big issue–managing everything: all of the information, action items, who is responsible, the deadlines,” explains Bragdon. “We saw the opportunity to have all the information in one place, not have information in so many different locations.”
Finally, the digitalization team wanted to give Schaeffler engineers an easy way to reference historical design decisions. They envisioned a system where any engineer could look up why a decision was made, with the context of the CAD version used to make that decision: “There’s confusion that happens when you don't know which iterations of CAD files were considered or when a specific design decision was made,” says Bragdon. “Especially when the only documentation you have was in emails or Teams chats, or a verbal discussion in a conference room.”
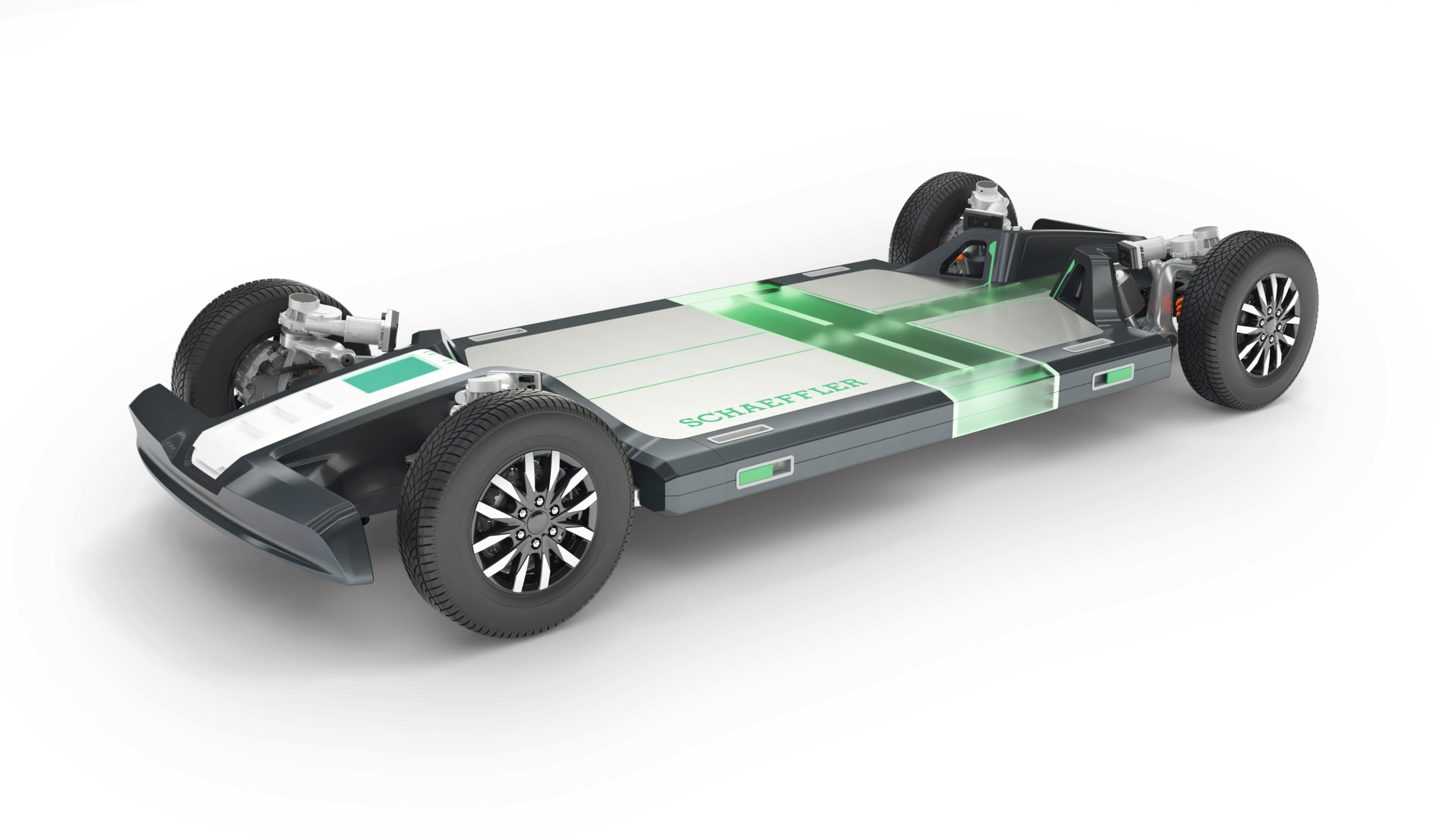
The Solution
Schaeffler’s digitalization team initially launched CoLab to 50 users focused on design review, tooling review, and approval of design guidelines. Before, all of these activities would happen in meetings. Someone in the meeting would have to keep track of what was said, as well as any action items: "You’d get meeting notes in Excel format, with everything sort of decentralized,” explains Bragdon.
Now, Schaeffler teams can review designs either live or asynchronously by interrogating CAD and creating feedback in CoLab: “The way that the conversation happens on the model–it is sort of effortless,” says Bragdon. “The interface is easy to use and the tasks can be assigned right there on the model geometry.”
Design conversations take place in CoLab discussion threads, which are associated with a 3D model and a specific view state. CoLab also keeps track of which version of a file any comment was made on. “It makes it easy to understand why the design decisions were made and be able to go back and reference that information," explains Bragdon.
With CoLab, feedback generated during reviews is automatically documented and organized into a database of action items. That means design reviews, plus any discussion of follow up actions all happens in one place. As a result, Schaeffler engineers can easily capture customer feedback and ensure that it gets resolved by the next revision: “If the customer remarks something about the model, I leave a comment in Colab and assign a designer to review,” explains Max Podschwadt, a member of Schaeffler’s engineering team. “This can be used as a record to check before sharing a new model with the customer. Before, I would have a separate sheet to track the markups from the customer.”
“One thing that our teams really liked about CoLab: everything was in one location,” adds Bragdon. “The whole design discussion happens all in one place, and it makes everything easy to document.”
While Schaeffler’s engineers are enjoying a smoother, faster review process, the digitalization team is ensuring that CoLab integrates seamlessly with other enterprise systems. With their long history of innovation, Schaeffler is especially vigilant about IP security. The digitalization team worked closely with CoLab to plan a phased roll out of CoLab’s Windchill integration. Access controls set up in Windchill will be mirrored in CoLab:
“We will implement some attribute-based access controls, so that our users are very carefully validated with the files that they're accessing in CoLab against the authorizations that they have in Windchill,” explains Bragdon.
Schaeffler is also looking forward to implementing some of CoLab’s upcoming AI features, including AI generated review summaries: “An AI recap of a meeting can give a summary that a stakeholder who may not have deep technical knowledge of the product can read over in five minutes to get an update."
The Impact
CoLab is making it easy for Schaeffler’s engineering team to capture feedback from more of their subject matter experts. As a result, they’re building a better end product: “Colab helps to improve quality,” remarks Podschwadt. “It provides more team members with easier access to review models and prints, which leads to overall better reviews.”
By giving their team better tools to document, discuss, and track design feedback, Schaeffler is also eliminating non value added activities. “Colab helps to avoid waste, like duplicate mark-ups or waiting for models to load,” says Podschwadt. “You also avoid unnecessary emails by putting comments right on the feature.”
As a result, their engineering team can complete reviews faster, while generating thorough documentation. For the industries Schaeffler serves, robust documentation is critical: “In our industry, we have a lot of audits,” explains Bragdon. “At any time, our customers could ask to see evidence that we follow a process to create a solid design. So that documentation must be readily available.”
Detailed process documentation can be time consuming and admin intensive. For the digitalization team, balancing customer requirements with the push for efficiency was key: “There has to be a system that provides evidence of our process, and the system has to be the most efficient that it can be in order for us to be productive," remarks Bragdon.
By automatically documenting design decisions as a part evolves, CoLab is helping Schaeffler achieve robust design quality, without the admin headache. This is one of the reasons that Schaeffler’s 50 user pilot quickly grew to 300 users.
“It exceeded our expectations quite a bit, on the scale of participation,” says Bragdon. “Our users are very excited about it. It's just word of mouth between the teams."
It doesn’t hurt that CoLab has been easy to learn: “There was a very short learning curve. A team could start learning CoLab and then actually start working with CoLab within a one hour time slot." With several teams across the Americas region onboarded and successful, Schaeffler is looking to roll out CoLab to new teams in Europe in 2024.