.webp)
How Mainspring used CoLab to achieve a 50% cost reduction redesign in half the time
Mainspring Energy is delivering a breakthrough new category of clean power generation with its linear generators for commercial, industrial, and grid-side customers. Founded in 2010 by three Stanford engineers, Mainspring focuses on accelerating the arrival of the clean electric grid by delivering local, scalable, low-cost, and fuel-flexible power.
The Challenge
In 2022, Mainspring Energy was actively looking to more than double their development speed.
Kevin Walters, Mainspring’s Senior Director of Hardware Engineering, had been given a mandate by the company’s COO to make it happen.
“That was something that was always on my mind,” Walters says. “I'm often thinking, what can I do to make the team more efficient? I can hire as many people as I can justify, but it's a competitive job market and adding more people to the team isn't the only thing we need to do to go faster.”
Then, while trying to source candidates on LinkedIn, Walters stumbled across CoLab. Although he wasn’t necessarily looking for a design review solution, the pain points on CoLab’s website resonated.
“The way we were doing our work is, I think, the same way that everyone else has traditionally been doing their work,” Walters remarks. “An engineer comes up with a design based on the requirements they have, and they do that design in their CAD tool; we use SolidWorks. Then they're going to take screenshots from SolidWorks, put that into a slide deck, and send that slide deck around for comments.”
While the team uses the Google ecosystem for internal collaboration, most communication with suppliers was happening via email. Slide decks would be converted into PDFs and design input would be emailed back and forth. “It all ends up being a slow process,” recalls Walters.
“It can be so hard to get the right screenshot that really gets the design intent across.”
“It also forced a lot of live meetings because it can be so hard to get the right screenshot that really gets the design intent across,” Walters continues. “So then you’re getting 10 people in a conference room for an hour. You're going to have your doc up on the screen and you're going to try to load it up in SolidWorks. And with really big CAD models, that doesn’t always work smoothly or fast.”
This process — driven by screenshots, slide decks, and live meetings — is familiar for most engineering and manufacturing teams today. As Walters puts it: “That's how we were doing things, but we knew there had to be a better way.”
Mainspring realized there was a big opportunity to speed up product development by streamlining their design review and engineering collaboration processes.
“This is a really deep cross-functional problem because it's not just mechanical engineers designing things, but we have other engineering teams that we're interfacing with — electrical, software, systems, controls — and then we also have our supply chain team and our suppliers,” explains Walters. “Those are all stakeholders in the design process.”
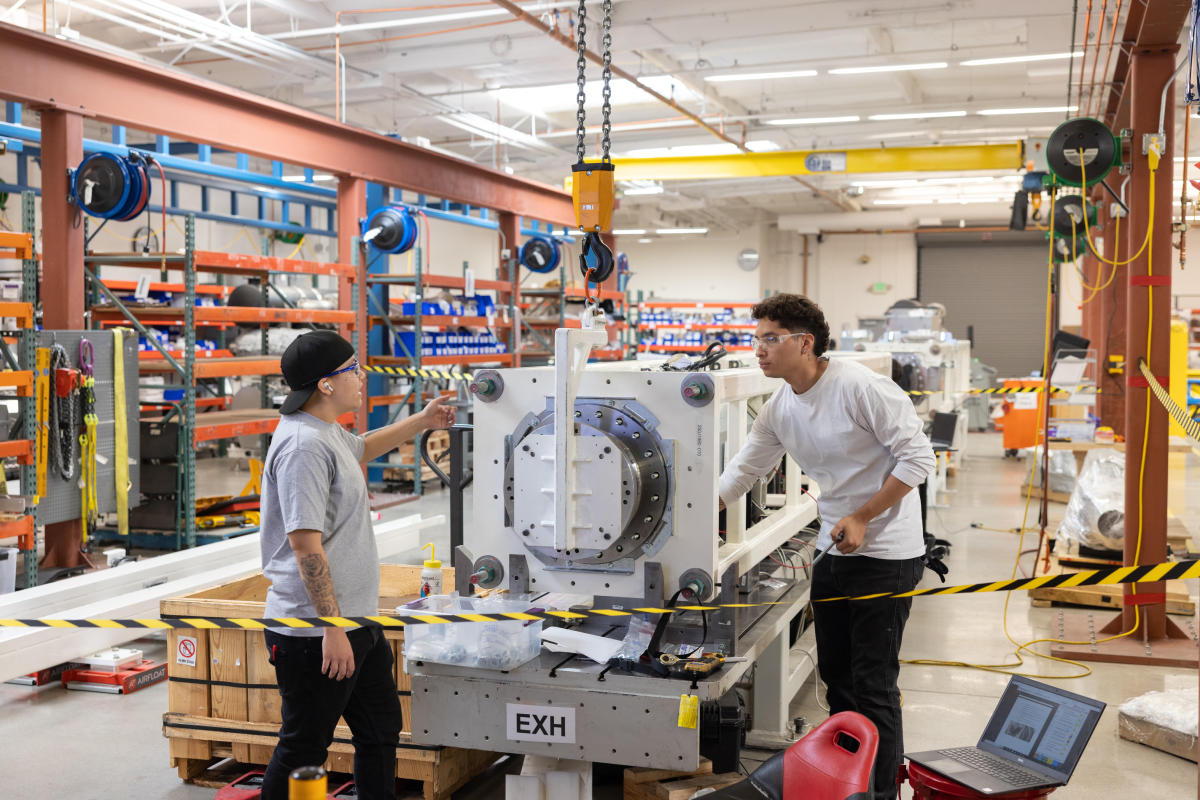
Working so closely with other engineering teams, it was also hard to ignore the difference in collaboration tools for hardware versus software. “I sit next to our head of software and controls, and I see the tools that they use for tagging issues and branching and merging and managing their code, and doing agile development,” Walters notes. “It really drove home how the mechanical side could be better automated and made far more efficient.”
So, after closely evaluating CoLab and comparing it head-to-head with another solution, the Mainspring team decided to move forward with adopting CoLab.
The Solution
As part of Mainspring’s overall efforts to double product development speed, CoLab provides a repeatable process for faster and more effective design reviews.
“From my perspective, if it's not going to help us double our speed — then we're not going to do it,” emphasizes Walters. “I don't do things because they're fun or they sound cool. I need to have a really sound reason to think that it's going to help us go faster, help us succeed.”
The company’s linear generators are complex, with over 3000 unique parts in the bill of materials. There are roughly 30 mechanical engineers on the direct team, 10 to 20 external resources doing design work, plus a range of multidisciplinary collaborators and external suppliers. With so many moving parts (literally and figuratively), strong communication is essential.
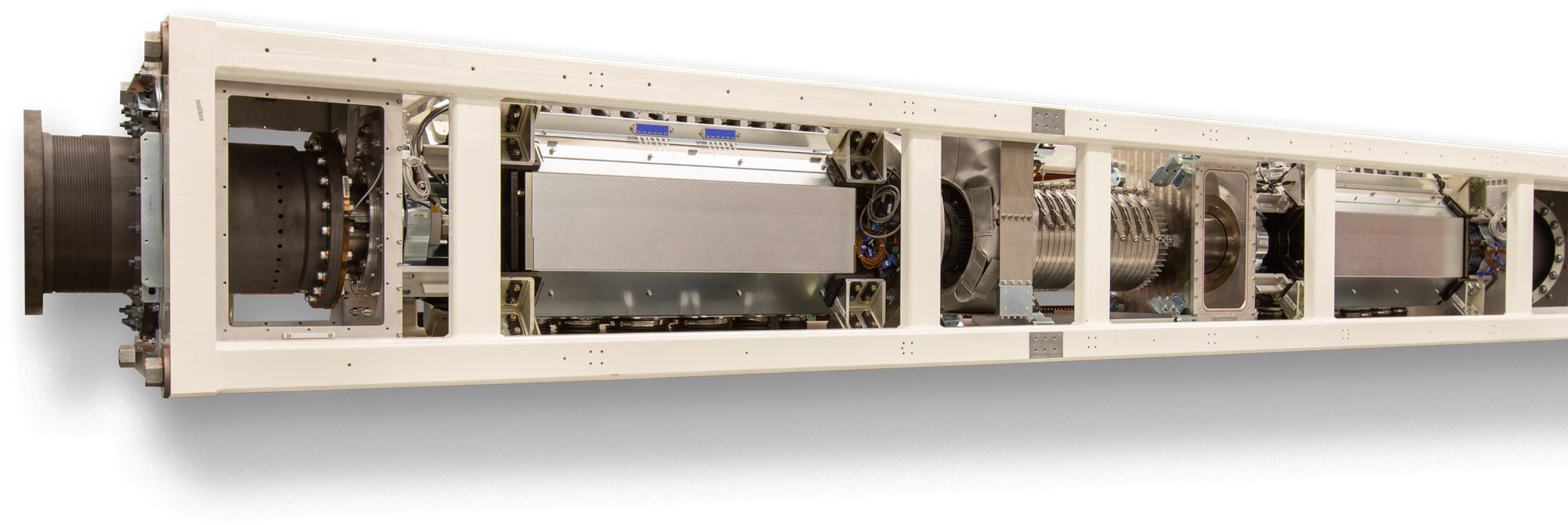
Instead of all those stakeholders needing to swap screenshots and manually track comments, the Mainspring team has now simplified and centralized design conversations within CoLab.
“We don’t need to have a meeting. It’s really quick. And it’s collaborative, which is the way that we work.”
“One of the most obvious selling points was that CoLab is very similar to workflows we're already using in Google Docs,” Walters observes. “When I'm collaborating in a Google Doc, I can ask someone in another department to take a look and give me their feedback. They'll go in and ask some questions, suggest some things. I'll get notified right away, and I can go in and take a look. We don't need to have a meeting. It's really quick. And it's collaborative, which is the way that we work. This is not a siloed company. Everybody works together very well and very naturally, and CoLab was very similar to other things that we're doing.”
Not only can collaborators exchange design feedback in real-time, CoLab also makes it possible to pin comments directly on 3D models. That means discussions can happen with full mechanical context, so there’s no confusion and no need to send extra emails back-and-forth for clarification. With clearer communication the first time, designs can move forward much faster.
“We’re able to get real-time feedback on the design from suppliers,” says Walters. “The suppliers are domestic and international, so now we don't need to have phone calls at odd hours. We can send them a model and just point to specific things to ask, ‘Hey, is this okay? Does this work? Can we use this material here?’ Then we get that direct feedback and it's clear.”
That ability to easily share design feedback and communicate clearly has also been crucial for engaging with contractors. “When we have a new person who's in a remote office, we need to get them onboard and help them get up to speed quickly — and the work product needs to be no different than if it was the person sitting at the desk next to me,” Walters explains. “Being able to have everything in one tool that's integrated into our CAD platform is a key part of that.”
Beyond enabling better asynchronous collaboration, CoLab has become a go-to for the team’s engineering communication in general.
“We do still have live design review meetings or design brainstorms, and CoLab's become a standard tool to use in those because it's incredibly stable,” Walters points out. “I haven't found a 3D CAD viewer that’s as efficient and robust. Using CoLab during live meetings gives us a way to easily capture all of the comments, questions, and action items that come up in the review.”
The Impact
It didn’t take long for Mainspring to get up and running on CoLab — and they’re already seeing the results.
During the first six months, the team has created over 500 reviews in CoLab and review time has decreased by 27%.
“In six months, the key success point was that we did a cost reduction redesign of our product enclosure,” notes Walters. “We realized we'd landed a 50% cost reduction on that, and our overall design cycle was half the time of prior design cycles.”
“Something that used to take a full year, we got it done in six months,” Walters continues. “And I personally have never overseen a cost reduction redesign of that scale — in terms of the number of parts and the amount of complexity — and been able to hit a 50% cost reduction on it.”
During the redesign process, the team used CoLab for internal design review before shipping to production. “When we released all the manufacturing prints, it was about 300 individual PDF documents and we reviewed them all in CoLab,” explains Walters. “It's safe to say that it was the cleanest design release that we've done. It was really, really quick and clean… We didn't have any mistakes that made it out to the supplier. We caught everything internally and we did it faster than we would have otherwise.”
“We didn’t have any mistakes that made it out to the supplier. We caught everything internally and we did it faster than we would have otherwise.”
The Mainspring team has also been able to move much faster when onboarding new contractors. “CoLab is the key part of enabling scalability and consistency with the outside design resources that we engage,” emphasizes Walters. “We've been able to successfully scale up. That outside design group went from three people to 20, and their output scaled pretty linearly with that. I don't think we could have done that with screenshots and slide decks.”
Plus, for internal and external engineers alike, CoLab provides new levels of visibility and insight that weren’t possible before. “As a people manager, it's actually given me a good tool because I can see, Oh this person isn’t providing a lot of feedback,” Walters describes. “Then I can go and talk to them and give them a little bit of coaching and encouragement. As we're growing a team, it's really enabled having that data, especially with a somewhat distributed team.”
However, CoLab’s impact has reached beyond the mechanical team alone. Mainspring currently has more than 85 active users in CoLab.
“Initially I thought this was going to be a tool that the mechanical design engineers and the supplier development engineers were going to use, and that was it,” comments Walters. “But it got adopted really broadly across the company.”
“The electrical engineering team loves it because it's lightweight,” Walters adds. “Our technical writing team, the people who write our user manuals, they love it… Our senior operating execs like it because they can check in on details easily when they’re looking for a quick update.”
CoLab has made it quick and easy for anyone to access CAD and interrogate models for themselves. “They can go in, they can open up CAD, they can spin things around, see where things are. We have our whole product in there,” says Walters. “It saves everyone a lot of time and it enables them to go and find information.”
The same benefits hold true when collaborating externally. “Suppliers like it more than I thought they would,” Walters observes. “We've had really good engagement from suppliers on being able to quickly onboard outside people, and also have high confidence in the security and data integrity.”
.webp)
Overall, the Mainspring team is happy with the value CoLab delivers.
“It's been great so far. I'm looking forward to seeing where we take it,” comments Walters. “It's only been six months and so there’s actually still a lot more we can do with it, and we can continue to improve the way we're doing it.”
“The thing that really sealed it was seeing that the CoLab team was as passionate about their product as we are about linear generators,” Walters elaborates. “Mainspring and CoLab are a similar size, which is big enough to be fast and impactful but also small enough to be pretty nimble. So seeing people who care about the product, that was really important to us.”
“If you're using it right, it’s going to make you a lot faster and make your work product a lot better.”
For other engineering leaders looking to improve product development speed, Walters’ advice is to see for yourself: “I think the first thing I’d tell someone considering CoLab is, try it. Because assuming that you'll get the same warm welcome and easy setup for a demo that we did, then once you see it, you’ll believe it.”
“For me, the ROI is really easy to make a case for,” adds Walters. “The cost per user is very reasonable within the scope of what engineering software tools cost, so it only needs to make you a little bit faster or a little bit better for that ROI to pay off. And if you're using it right and paying attention, it can make you a lot faster and make your work product a lot better.”