Post-COVID Recovery Isn't Over: How to Reduce Costs with Value Analysis and Value Engineering
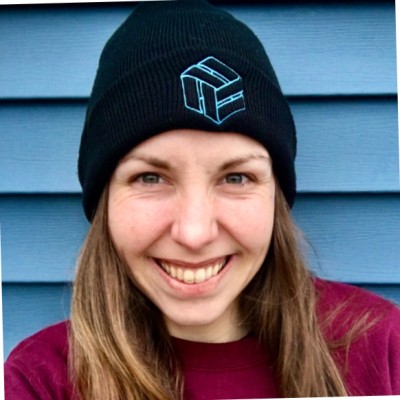
Meagan Campbell
May 20, 2021
6
min read
More than two years have passed since COVID-19 was first officially declared a global pandemic by the World Health Organization (WHO). Businesses and individuals everywhere have been affected by the outbreak in numerous ways, and the ripple effect will continue to play out for years to come. Yet in many ways, the manufacturing industry was particularly hard hit by the rapid changes to workplaces, supply chains, and global markets.
By its very nature, there are limits to how fully the manufacturing world can convert to digital modes of work. Physical goods require physical production. Industrial equipment cannot simply shift to workers’ kitchen tables or home offices. It has been essential for manufacturing work to continue, but there have been significant obstacles to overcome for manufacturers to make this happen. At the same time, new levels of economic uncertainty altered the revenue forecasts that businesses had anticipated at the beginning of 2020.
To navigate these challenges, manufacturing leaders have had to focus on building more resilient organizations while accelerating plans to innovate, automate, and digitize their operations. But this presents yet another challenge: the sheer volume of options for manufacturers to find the right path forward for their business, one that is leaner and more efficient than ever before.
This post examines key data on how the pandemic has impacted manufacturing, how businesses have responded, and how strategically-implemented value analysis and value engineering (VA/VE) can play a strong role in the post-COVID comeback for manufacturers looking to speed up their recovery — by improving both new and existing products while reducing baseline costs across the business.
The pandemic’s impact on manufacturing businesses
Directly before the WHO reclassified COVID-19 from a public health emergency to a global pandemic, the National Association of Manufacturers (NAM) surveyed its member companies to gauge the outbreak’s impact on manufacturers. Between February 28 and March 9, 2020, manufacturing businesses responded to NAM’s survey about the anticipated effects on their supply chain, operations, finances, and emergency planning. Over 78% responded that uncertainty due to the COVID-19 outbreak was likely to have a negative financial impact on their business.
When PwC surveyed CFOs across the US in April 2020, respondents were asked to share their top 3 concerns regarding the COVID-19 pandemic. 71% indicated that “financial impact, including effects on results of operations, future periods and liquidity and capital resources” was a top concern — a higher proportion than any other concern, with potential global recession (64%) coming in second.
It’s not surprising that, in the earliest months of the pandemic, businesses were already predicting negative financial effects. For some organizations, the first quarter of 2020 may not have reflected the changes that would show up later in the fiscal year. However, the need to take quick and decisive action was already apparent as Q1 came to a close.
Still, in November 2020, Creditsafe’s State of the Manufacturing Industry report looked at the impact of COVID-19 during Q3 and confirmed there had been good reason for concerns. The study focused on which specific manufacturing sectors and US states would be hardest hit by the effects of the pandemic. The report found over $413.6 billion of revenue was at risk in the top 10 most affected states alone. The study’s authors attributed this loss of manufacturing revenue to “shutdowns, preventative health and safety regulations, purchasing habit changes, restrictions on imports and exports, and the overall economic uncertainty.”
“Five years of innovation in... 18 months”
In May 2020, Anna-Katrina Shedletsky — CEO of manufacturing tech company Instrumental and a Senior Contributor on Manufacturing for Forbes — predicted the manufacturing industry would see massive acceleration in existing technology trends. “Between solutions that leverage the power of the cloud for visibility and automation that optimizes work, necessity will drive invention: manufacturers will do five years of innovation in the next 18 months,” Shedletsky wrote.
Then, in April 2021, Shedletsky published another article in Forbes with an update on her predictions for the manufacturing industry. After speaking with over 500 manufacturers throughout 2020 and 2021, Shedletsky summarized insights from engineering and operations leaders on how the industry has adapted and responded to the significant impact of the COVID-19 pandemic. From these conversations, she makes a new prediction for the next six months, seeing a new trend she describes as a “cultural shift towards building hardware like software.”
She also highlights three key ways that manufacturers have embraced change and innovation over the course of roughly one year:
- Unlocking the Cloud has unlocked the supply chain
- Automation has taken more forms than just robotics
- Necessity drove a hunger for solutions instead of technology
While it hasn’t been easy progress, the pandemic has indeed forced manufacturers to step away from “business as usual” mindsets and to take big strides toward more innovative ways of doing business. In May/June 2020, the Thomas Industrial Survey on COVID-19's Impacts on North American Manufacturing reported that — although 90% of respondents confirmed their business had been affected by the pandemic — 91% believe recovery is possible for the manufacturing industry in North America. In the same survey, across nine categories, an average of 40% of respondents indicated they were “likely” or “very likely” to invest further in automation processes over the next 12 months.

How does Value Analysis and Value Engineering (VA/VE) fit into the picture?
In a November 2020 article published by the World Economic Forum, manufacturing experts urge for greater global collaboration. They point out that the industry’s vital societal and economic roles have become clear during the COVID-19 pandemic. Yet, at “the same time, it has caused an unprecedented financial hit to the industry, making cost reduction and the creation of transparent, flexible supply chains urgent priorities.”
Value Analysis and Value Engineering (VA/VE) has always been a way for companies to not only reduce costs — but to maximize the value their products provide, typically through functional advancements or improvements to the product design and/or its manufacturing process. As a set of problem-solving techniques, when VA/VE is rigorously applied, it can uncover inefficiencies, unnecessary manufacturing costs, and opportunities to improve a product’s overall value.
The idea of reducing manufacturing costs through VA/VE is nothing new. After all, value analysis and engineering is a powerful approach that has been used all over the world for decades. However, for some organizations, VA/VE processes have had to adapt to the pandemic’s impact, just like so many other aspects of operations. For example, Johnson Controls (JCI) previously applied VA/VE techniques primarily through annual, global, in-person events. When the pandemic made it impossible for this key business activity to proceed the way it usually has, JCI shifted to a digital model.

As with other digitization advancements, the virtual VA/VE events have revealed that they’re not simply an adequate substitute for the traditional VA/VE methods — they’re actually proving to be more efficient when done using a collaborative software tool. “With our normal in-person events we’d find more than 100 opportunities for value-add on the models we’re reviewing,” says Brian Stauffer, Global Product Design Manager for JCI. “This year with our virtual events in CoLab, we’re averaging over 200.”
Continuing along the road to recovery
There’s still a long road ahead for manufacturers to recover from the financial impacts of COVID-19, but there’s also many reasons to be optimistic about the industry’s future. Businesses have made huge leaps forward when it comes to technology and innovation. The world has recognized the importance of manufacturing as an essential industry, including the role of manufacturing as a vital producer of vaccines and health supplies.
Within the industry there’s a greater understanding of the advantages that can be gained through technology, software, automation, and other innovations. There’s less fear of change, less fear of advances like “the Cloud.” There’s new excitement and optimism about the possibilities for manufacturing’s future, and how we can move forward with greater collaboration across the industry.
That’s why it’s important to look at tried-and-true techniques like Value Analysis and Value Engineering, and examine how we can update our reliable manufacturing processes so they’re adapted for the 21st century. It’s not about reinventing the wheel. It’s just about making sure the wheel keeps up with other advancements. After all: the wheels that worked for a horse-drawn carriage aren’t going to hold up on a Tesla. Make sure you’re not expecting your manufacturing processes to work that way, either.