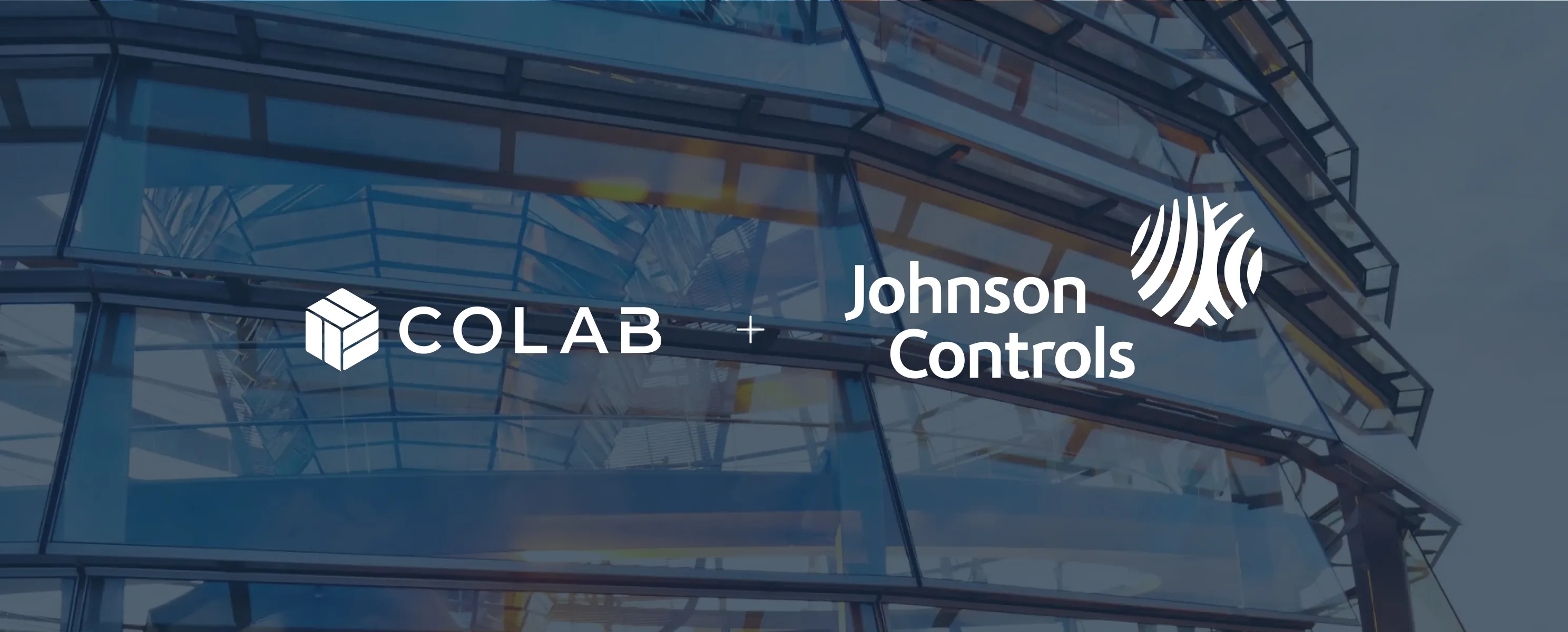
How JCI hits ambitious cost reduction targets with virtual VA/VE in CoLab
Johnson Controls (JCI) is a global technology and industrial leader that’s been transforming environments and making buildings smarter since 1885. With billions of dollars in worldwide sales and thousands of employees across hundreds of locations, JCI offers the world’s largest portfolio of innovative building products, technologies, software, and services.
In 2018 CoLab approached the Johnson Controls team with a question. What is your biggest pain point in product development? The answer: Communication.
The Challenge
When the pandemic first hit, Johnson Controls needed to make a quick pivot. Up until that point, JCI’s cost reduction strategy had revolved around in-person VA/VE events requiring global travel. Suddenly travel was no longer an option, yet it was more important than ever to stay on track with cost reduction targets.
“VA/VE is one of our big priorities,” says Brian Stauffer, Global Product Design Manager. “With the pandemic, we had a unique situation where we weren’t able to travel to the factories anymore but we wanted to continue the VA savings that we’ve been getting.”
“We needed a way to communicate globally with a large number of folks at the same time.”
Although JCI’s Applied HVAC Equipment division had started using CoLab for design reviews prior to the pandemic, they hadn’t yet considered adopting CoLab for VA/VE.
“We used to do VA events live at the factories,” explains Stauffer. “When we did this in person, like we used to in the past — we dedicated a couple days to it, we flew people in, and they focused their time for that day or two to come up with as many ideas as they could.”
With global travel off the table, JCI needed a solution that would allow them to move to a digital model so they could continue holding VA/VE events. “Because of Covid, our travel budget had been cut to pretty much nothing,” notes Stauffer. “We needed a way to communicate globally with a large number of folks at the same time.”
To make the shift from in-person events to virtual VA/VE, the Johnson Controls team needed more than just a communication tool. They also needed a way to make design data easily accessible to everyone involved, especially those with no access to Creo and/or limited experience with CAD in general.
However, given the complex and 3D nature of JCI’s product line, basic tools for file sharing and collaboration simply didn’t cut it.
“Having the real model and actually being able to measure things and hide things — with other tools, that’s been a pain,” remarks Brian McMaster, Mechanical Design Lead. “Our engineers had to just look at PDFs and get their best view possible. Some would ask for 3D PDFs, but they’re still not great.”
So JCI turned to CoLab for a virtual VA/VE solution.
The Solution
The Johnson Controls team moved quickly to identify what they truly needed in a solution.
“We wanted a tool we could access independently and collaboratively to do these reviews. That was something we were looking for,” comments Stauffer. “Getting more familiar with the software, I started thinking CoLab was the perfect solution. It seemed like the best fit for hosting VA/VE events that were virtual instead of in person.”
As a browser-based cloud tool, CoLab makes it simple for everyone to stay in the loop — whether working together in real-time, asynchronously, or a hybrid combination. “Multiple people can be in there at the same time, which is very beneficial for us,” observes Stauffer. For any file, the full history of revisions and discussion is easily viewable and automatically kept up-to-date.
“With a global engineering and manufacturing organization, it’s critical that we can keep all parties on the same page,” says Mike Zamalis, VP Global Chiller Product Engineering. “With CoLab we have that ability to have various functional groups around the world all reviewing and commenting, live or around the clock, on the same exact model.”
“With CoLab, we can have groups around the world all reviewing and commenting on the same exact model, live or around the clock.”
Compared to the traditional in-person model, doing VA/VE virtually in CoLab also makes it possible to include a broader range of people and perspectives. “With CoLab, now we can open this up to a lot more people than we could when traveling to the factories,” Stauffer points out.
By eliminating the travel costs associated with VA/VE events, CoLab allows JCI not only to include more people — but also to hold events on a more frequent basis, rather than a couple times per year.
Additionally, CoLab lets the JCI team take a more continuous approach to the events themselves. “We were able to extend the timeframe to come up with ideas, so people can actually work at their own pace,” says Stauffer. “Instead of being trapped in a room for two or three days, this lets you do it over more of a two-week period.”
Another way CoLab makes it possible for more people to participate in VA/VE events is by lowering the technical barrier to entry.
“Being a web-based tool, there is no software distribution nor installation and very little training,” Zamalis comments. “It is VERY intuitive with easy-to-understand icons. We typically ‘train’ during one of our event kickoff sessions.”
“Users that aren’t familiar with Creo, or don’t have access to Creo models, can now actually spin the models around individually,” adds Stauffer. “You can spin the model around, you can isolate components, you can explode things, you can do cross-sections — things that, typically, you wouldn’t get to see when primarily on the factory floor.”
Along with wider participation and greater access to 3D models, using CoLab to communicate about design helps minimize the potential for miscommunications and mistakes
“The ability to actually pinpoint an issue, like this pipe or this sheet metal or this whatever is the problem, and CoLab takes you directly to that component — that’s big,” emphasizes McMaster.
As McMaster puts it: “Being international, we have different terms for the exact same part between China, US, Mexico, wherever. So in the past you might spend a day going back and forth on email, just because you say a part and they don’t understand what you’re talking about because they call it something different. Now, being able to pinpoint a part, there’s really no way to confuse that anymore.”
Yet beyond making it possible to generate more (and better) ideas, CoLab also makes it easier to prioritize actions and get ideas implemented.
For any drawing or model, a side panel will display all feedback associated with that file. For each piece of feedback, users can enter and update as much information as they need. “We can set priorities, we can set statuses, and we can assign due dates,” describes Stauffer. “You can attach JPEGs, you can attach PDF files, and even snapshots of the actual model itself.”
And since CoLab’s Track table offers a bird’s-eye view of all your feedback and reviews, it’s easy to zoom out and prioritize your next steps.
“Basically we take all the ideas at the end of the event, and we have product management and our lead product engineer go through the activities and suggestions that were made,” explains Stauffer. “Then we actually come up with priority lists and cost targets and stuff like that. We identify which ideas we’re going to implement, and what order we’re going to implement them in.”
The Impact
Just by making the switch from in-person events to virtual VA/VE in CoLab, JCI started seeing tangible value almost right away.
“We’ve been using this for over a year now for VA/VE events,” Stauffer notes. “And what we’ve actually seen is: we get a better benefit out of doing it virtually than we would have typically on the factory floor.”
With CoLab, it’s easier and more cost-effective to facilitate VA/VE events than it was before. Which means:
- VA/VE events can happen more often, with greater flexibility for asynchronous and/or hybrid work
- More people can participate, from different locations and different departments
- Anyone can now view and interrogate the relevant 3D models, including those who otherwise wouldn’t have access to CAD
As a result of using CoLab, the Johnson Controls team has seen an uptick in idea generation. “We’re getting a lot more ideas coming forward,” says Stauffer. “Now, we’re not limiting the timeframe to a two-day window. We’re not spending money to send people around the world to be able to do these events. And we’re actually getting more content, by having the ability to let people just do this at their own pace.”
“We’re not spending money to send people around the world to be able to do these events.”
Beyond the upfront savings on travel costs, shifting to a virtual format has made it possible to open up VA/VE participation to a much bigger and broader group. That means more people able to contribute ideas, and more diverse perspectives being included.
“Adding additional people has really expanded our collection of ideas,” remarks Stauffer. “We can have people included in the events now who typically wouldn’t have been able to be there before. So we’re getting more ideas, coming from a broader group of people and a more cross-functional team.”
Not only has CoLab made it easy to involve more people, it’s also opened up new ways of collaborating.
By bringing everyone’s ideas together in one spot — easily accessible to all and updated in real-time — CoLab creates space for more collaborative interactions to happen. “People can actually see what others are suggesting, and maybe add onto it, where we didn’t really have that interaction in the past,” Stauffer explains. “Now you can actually see the comments that others have already made, as you go and as you review on your own. And that may spark other things in your head, now that you saw somebody else’s ideas.”
Plus, by giving more people a way to view and explore 3D models, CoLab makes it possible for everyone to engage meaningfully and get the information they need to contribute their expertise. As Stauffer observes: “People that didn’t necessarily have access to the 3D data before, they now have the ability to open up a model, spin it around, make comments, et cetera. That’s been fantastic.”
.webp)
It’s also easier now to communicate both quickly and clearly. Ideas are always shared with full context, right on the design file, so there’s no confusion about what’s being discussed.
“It’s been great. It’s a better communication tool. It’s looking at models, looking at drawings, and people can make comments right on them, so there’s no misinterpretation of what we’re talking about,” emphasizes Stauffer. “We all speak the same language when we’re looking at a model. Right?”
Overall: virtual VA/VE in CoLab has helped Johnson Controls to thrive in challenging conditions, rather than just survive.
Even with ambitious targets and rising external pressures, the JCI team has used CoLab to continue consistently hitting their numbers. “CoLab has proven to be successful,” reflects Stauffer. “Using this for VA/VE events has been a big savings on our part.”
“Using CoLab for VA/VE events has been a big savings.”
More than the software alone, Johnson Control values their partnership with CoLab. “I definitely think we’ve had a good working relationship. Anything that we throw at CoLab, they’ve been able to respond very quickly,” Stauffer notes. “CoLab is more than willing to jump in and help anywhere they can, which is a huge deal for me.”
And, given the success JCI has found with CoLab so far, it’s a partnership with definite potential for growth. “We’re looking at ways we can utilize this more on a day-to-day basis rather than just VA/VE,” states Stauffer.
“I’m excited about getting it in more people’s hands,” adds McMaster. “It makes everybody so much more efficient. With times being the way they were, there was a huge opportunity for us to get worse at efficiency, and I feel like this tool has allowed us to do the opposite.”