Past, Present, Future: Tracking the Changes in How Engineering Teams Work Together
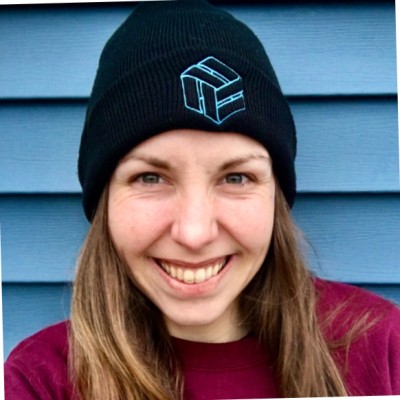
Meagan Campbell
July 8, 2021
7
min read
Mechanical engineering’s greatest innovations are accomplished by teams, not any one engineer alone. The more complex a design gets, the more complex the design process gets, too. And as an organization grows and takes on more projects, that complexity gets compounded.
Clearly defining the engineering challenge, outlining the requirements, designing and developing the right solution, and moving a project all the way along from being an idea to becoming a real, actual, physical thing—even if communication and productivity and efficiency are optimal, it’s still no small feat. Design work is often challenging. But it’s also challenging to get your team in sync and keep them there, instead of letting chaos and confusion reign.
Over the past few decades, as technology and software evolve, the way engineers work together has also evolved. From fully paper-based processes to the early days of digitalization to the rapid shift to remote work brought on by the Covid-19 pandemic, mechanical design teams have hit an inflection point. Agile processes that have long been standard in software development are now coming to the hardware world. Formerly familiar barriers to higher levels of collaboration and innovation have changed. And things are only going to keep changing, as teams that adapt to new ways of working together pull ahead of the pack while teams that stick to “the way we’ve always done it” find themselves struggling to keep up.
This post looks at the evolution of collaboration in mechanical design and engineering—from the changes that have already taken place in recent decades to insights on what’s next in the coming years.
Then: “Throwing Paper Across Oceans at Each Other”
With the introduction of computer-aided design (CAD) in the 1950s, CAD software programs continuously grew more popular and common among engineering teams. Yet so many large CAD files, with multiple versions, created a new challenge for organizations that now needed to manage all this information. In the early 1980s, Product Data Management (PDM) tools were built to organize product data, followed by the first Product Lifecycle Management (PLM) systems. By the early ‘90s, American Motor Company’s 1992 Jeep Grand Cherokee became known as “the first complex product to be designed and produced entirely with the use of PLM tools.” However, across the industry, paper was still crucial to most teams’ daily operations.
In 2001, Mechanical Engineering Magazine published an article about changes at the Brooks instrument division of Emerson Electric Co. Brooks had facilities around the world that were each working together using “their own manual systems for tracking critical product information documented and exchanged mostly on paper.” Sending an engineering change from designers at the company’s US headquarters to team members in Japan or Mexico or the Netherlands meant sending paper copies by snail mail that took days to arrive.
Brooks’ vice president of engineering at the time, Tim Scott, compared it to having each facility operating as a separate company. “There was no real collaboration going on,” he is quoted as saying. “Just throwing paper across oceans at each other." Brooks had just implemented a web-based PDM system with a price tag of more than half a million dollars, launching primarily at the US headquarters with about 250 users—with others at international facilities to be brought on later.
As the first two decades of the 21st century progressed, more and more companies moved legacy paperwork into PDM and PLM systems. Email became standard. Software programs shifted away from floppy disks and CD-ROMs as web-based tools and cloud-based SaaS applications steadily took over. New capabilities for teams to work together emerged, with video-conferencing and instant messaging being slowly incorporated into more and more organizations.
Yet change was not instantaneous. Even on teams using CAD and PLM software, it wasn’t uncommon for drawings to still be printed off and redlined by hand. Global travel to bring people together for meetings was still a norm. And much of the time, engineering collaboration and project coordination was still happening largely in spreadsheets and slide decks.
Now: A Giant Leap for Digital Transformation
While spreadsheets and slide decks haven’t necessarily gone away, the onset of the Covid-19 pandemic in 2020 pushed the industry to speed up digital transformation out of necessity. Exchanging paper or flying internationally for meetings was suddenly not an option. Ready or not, engineering teams had to rapidly find new ways to work together to keep projects moving forward. A McKinsey Global Survey of executives in late 2020 found that companies had “accelerated the digitization of their customer and supply-chain interactions and of their internal operations by three to four years.”
Although the global pandemic made it necessary for companies to adapt sooner than they otherwise might have, many teams quickly began to notice benefits from working together in new ways. Shipbuilding leader Genoa Design shifted their production drawing reviews to a digital, remote process—and, after just a few months, they were completing reviews twice as fast as they had when working together in-office. Other teams have adopted new tools and processes that have opened engineers’ eyes to more possibilities for even greater collaboration and productivity.
On the flip side of that, some organizations are seeing the limitations of outdated software and technology. When pandemic restrictions caused offices to shut down and employees to work from home, the disadvantages of on-premise systems became clear as teams scrambled to find solutions to the lack of access to needed programs and data. With files being sent over emails or instant messages and employees logging in from home or public Wi-Fi networks, the idea that “the cloud” is not a secure place for company data and intellectual property is finally falling to the wayside. Cloud-based systems are delivering higher levels of security and business continuity for organizations, while allowing teams to collaborate more efficiently and seamlessly from anywhere in the world and at any time of day. While cloud computing was already being accepted in different organizational areas, letting engineering data live in the cloud, too, is now being seen as an advantage.
Next: Unlocking New Levels of Engineering Innovation
So what now? Where does engineering collaboration go from here? CAD programs allowed designs to come to life faster, at higher quality. PDM and PLM systems created databases for teams to manage that vast volume of product information. Basic digital communication tools like email, chat, and video calling are now widely used, letting globally dispersed teams exchange messages and data quickly—no longer “throwing paper across oceans at each other.”
Looking at the last few decades, the way engineering teams work together has come a long way. The acceleration of digitization across the industry (and across all industries) coming along at the particular point in time that it did, we truly are at an inflection point where change will only continue to accelerate. New levels of engineering innovation are about to be unlocked by unprecedented abilities for engineers to collaborate on design challenges. From the first passenger Hyperloop pods being predicted to start commercial operations in 2027 to the first electric air taxi aiming to launch in 2024, teams around the world are taking advantage of greater connectivity to push the boundaries of engineering design and innovation.
To get there, organizations will need to choose the right tool for the job when it comes to their needs. That’s why companies in every industry have been trending toward a best-of-breed approach to technology and away from the single-vendor software suites of the early 2000s. “A best-of-breed system enables businesses to mix and match specialized technology services from multiple vendors,” Lindsey Bly explains in this article. “By taking a best-of-breed approach, businesses can handpick applications based on the features and functions that they require… Selecting a suite of products is a big commitment, and organizations taking that route risk being locked into a system that isn’t fully tailored to their needs or becomes outdated quickly.”
When it comes to breaking new ground in engineering, teams that find the most agile and efficient ways to communicate on tough design problems are going to innovate the fastest. Being able to take a co-design approach that enables all stakeholders to be an effective part of the process will create better products. Moving beyond the ways CAD and PLM software has created efficiencies in design and data management, the next frontier for mechanical design teams is replacing inefficient communication methods like email and PowerPoint with purpose-built solutions that let engineers focus on engineering. In a report from the Project Management Institute, research found that, $135 million is at risk for every $1 billion spent on a project. Of that $135 million, 56% of that amount—$75 million—is at risk directly due to ineffective communications.
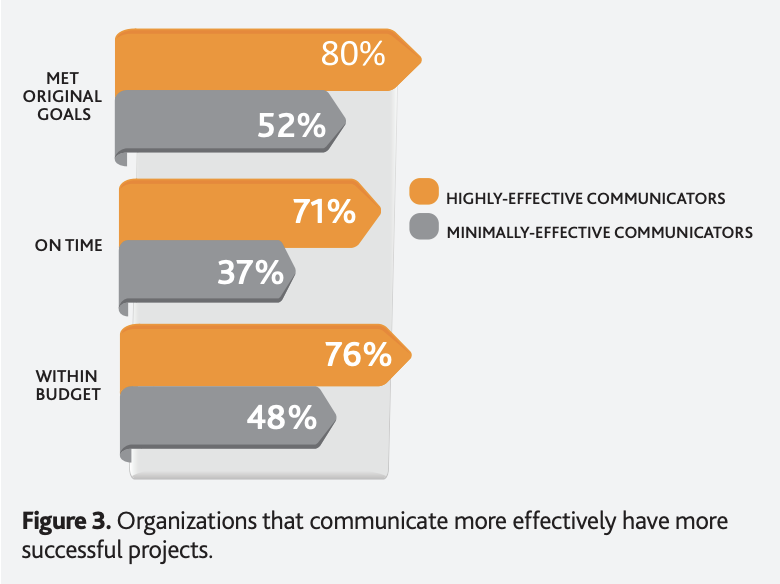
Throughout every stage of the engineering design process, communication plays a huge role. The way that engineering teams work together ultimately comes down to how well they communicate. Trying to collaborate efficiently and effectively on mechanical design—whether it’s with your internal team, globally distributed colleagues, external vendors and suppliers, or any stakeholder at all—is the next problem for engineering organizations to solve if they’re going to survive, adapt, and push innovation forward.
As the world’s first product designed and produced with PLM tools, the Jeep Grand Cherokee continued to dominate its category in the automotive industry for decades afterwards. Brooks Instrument ditched their paper processes for a web-based PDM over 20 years ago and is still a global industrial leader today. It just goes to show that, whenever there is change, there are leaders who embrace it and reap the rewards and there are those who wait to see everyone else go first.