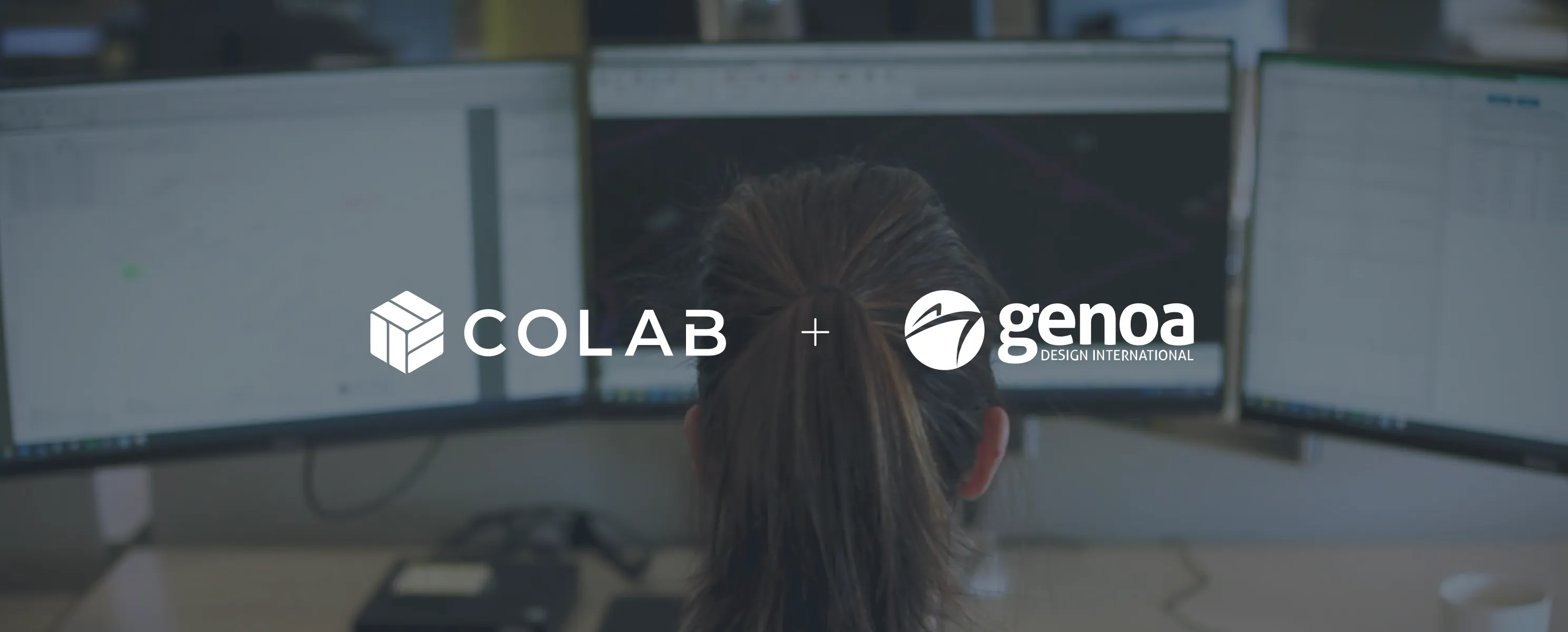
Genoa Sets the New Shipbuilding Production Drawing Review Standard With CoLab
GET A DEMOThe Challenge
Genoa Design International has been providing production design and 3D modeling services to shipbuilding and offshore industries from Newfoundland and Labrador since 1995. In that time, they’ve become one of the most sought-after production design firms in the North American shipbuilding market with a commitment to quality and a cornerstone of collaboration. Currently, Genoa is active in major programs such as Canada’s National Shipbuilding Strategy (NSS) as well as commercial and government contracts in the United States. Genoa is proud to play an important role in the NSS, which includes the design of multi-task ships for the Canadian Navy such as the Joint Support Ship and modern, first in class vessels, such as the Offshore Fisheries Science Vessel for the Canadian Coast Guard.
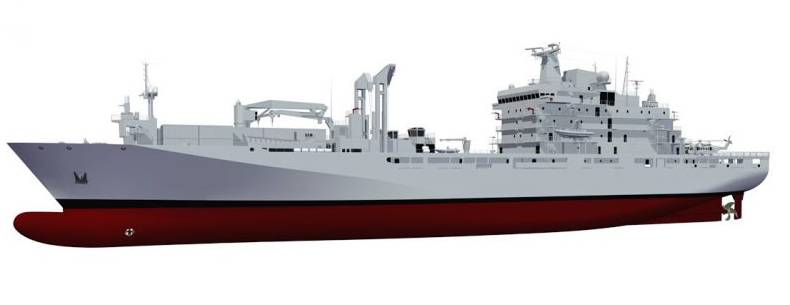
In March of 2020, like much of the world, Genoa was tasked with a new challenge - safely transition their team to work from home and master remote work, immediately. Slowing down was not an option. Genoa had to continue to deliver for their customers as the vessels they work on are critical for both Canada and the United States. They had to do what they do best - innovate.
Genoa immediately began working on a solution, digitizing their production drawing review process on several key projects and engaged CoLab to help make it happen. Genoa didn’t miss a beat - hitting their goals, moving faster than ever before, and achieving best-in-class quality. Genoa delivers for its customers - even in the most uncertain of times.
Together, Genoa and CoLab delivered unprecedented success for these projects, mastered remote drawing review, reduced paper, delivered quality, pushed continuous improvement, and achieved efficiency excellence. And the numbers speak for themselves!
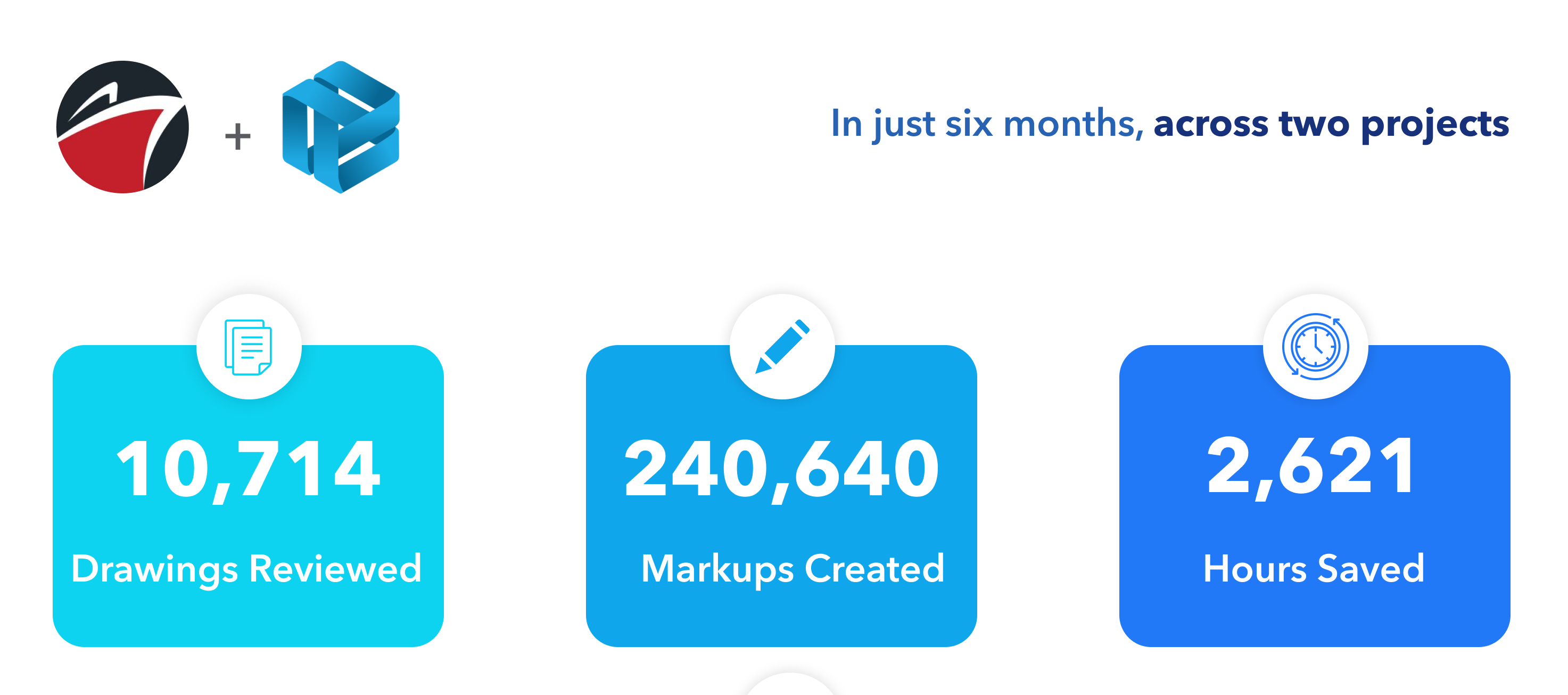
The Solution
Digitizing & Automating Genoa’s Review Process
Today, Genoa uses CoLab to drive their drawing review process. From self-checks to QA Review, they now complete their full drawing review process collaboratively within their digital CoLab hub.
.webp)
Massive Vision, Instant Impact
With the implementation of CoLab, Genoa has achieved powerful results, quickly. In just a few short months, they’ve become so efficient with their remote review process, that they now complete their production drawing reviews twice as fast as their previous process, with no disruptions.
Genoa has also eliminated paper and email attachments from their review process, adopted an automated digital thread for each of their reviews, achieved unprecedented efficiency, and so much more.
Master Remote Collaboration
As Genoa decided it was in the best interest of their team and communities to work from home, they needed to find a new way to collaborate. While the way Genoa teams had to work and collaborate changed dramatically, their goals did not. They had to deliver excellence for their customers.
Genoa has always leveraged the 3D model, the associated drawings, and high quality review processes to collaborate effectively with their customers and partners. Like many design teams, Genoa’s review process employed the industry-approved tools: screenshares, model exports, in-person reviews, email, PDFs in disconnected desktop tools, and printed drawings. With a new distributed work environment, Genoa had to pivot quickly. That’s where CoLab came in.
Together, CoLab and Genoa analysed the existing process, designed a new digital one, complementing their existing agile framework, got the team up to speed, implemented CoLab and started executing. All in about one week.
Scott Greene, Designer II with Genoa Design shared: “I could see CoLab’s potential immediately. The pandemic had no end in sight, so we started to check our drawings on the cloud using CoLab. In just a few months, CoLab has evolved into a tool I want to use into the future.“
What began as a challenge to match their previous in-office efficiency, quickly became something much bigger. With CoLab, Genoa has not only achieved their previous drawing review efficiency, but created a new process that was even faster than before.
“I really don’t think we would have delivered the quality we did without CoLab. We have at-home figured out and we’re really efficient. We can get a block from a client and back to them in a week and I don’t think any other team could do that without CoLab.”
- Jessica Chiasson, Designer III / Lead
Digitize Drawing Review: Eliminate Paper, Rogue PDFs and Email
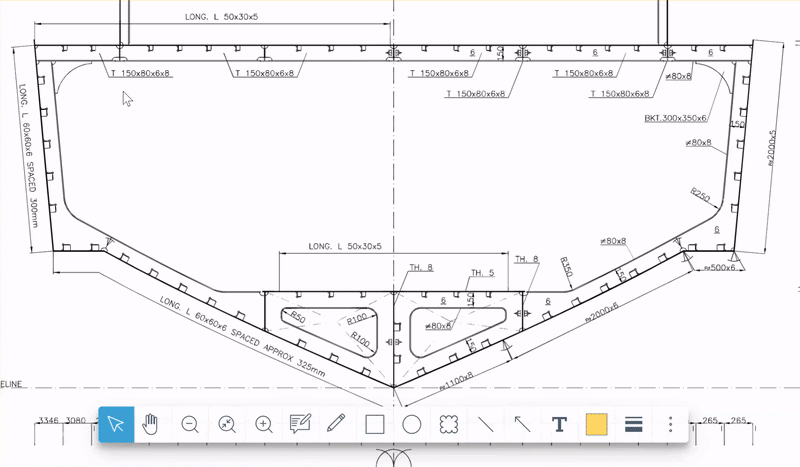
Genoa’s been pushing the bounds of 3D model collaboration for years. So, it’s no surprise that they weren’t satisfied with the industry standard drawing review processes that are typically conducted on paper or within desktop PDF tools paired with emails and manual work. Genoa wanted to be agile and lean, and embed their quality processes into every stage of their reviews. CoLab provided a digital, automated and connected way to move through their design process.
Today, Genoa safely stores their production drawings in CoLab, in one central hub. When a drawing is ready for feedback, they simply share it for review and begin the markup process. Reviewers are instantly notified, and brought directly to the file where they can add markups, make comments, and address feedback. If a drawing is sent back with changes, the designer simply makes the modifications in their CAD tool, and pushes a new version. This version control process is built directly into CoLab reviews, and the history is automatically stored.
Once a document has passed through its final quality check, a final clean copy is stored in CoLab. Just like that, the review cycle is complete!
This new process has become the favored approach even with designers returning to physically distanced office environments. Bill Norman, Designer with Genoa shared: “My aha moment was I could find any drawing at any time, when I wanted to look at it. I didn’t have to go through stacks of paper. I love CoLab!” And this doesn’t just enable a paperless process. A central digital hub means version control and comprehensive digital threads are managed directly in CoLab, without manual effort or report creation.
“Not having to share around paper is a huge time savings. If a designer asks me to go look at something I can be there in seconds. CoLab is always open on our computers and it tracks the work from the review to construction stage.”
- Jessica Chiasson, Designer III / Lead
The Impact
Deliver Quality; Maintain Continuous Improvement
Genoa is an ISO 9001:2015 certified quality-leader, and has built their work around quality excellence - from concept to final design.
The team is constantly improving their process for two key reasons:
- To make better designs
- To make better designers
Key CoLab functionality including version control between revisions, comprehensive histories and audit trails and real-time communication allows Genoa to standardize process, automate reporting and streamline record-keeping while actually learning more from one another.
In early 2021, Genoa will add integrated CoLab checklists and sophisticated analytics tools to their QA workflow, allowing them to automate QA and identify areas for further improvement. Quality is a critical component of Genoa’s work, and one that they take very seriously. With a culture of continuous improvement, Genoa is always striving to improve their quality processes. This made Genoa a perfect partner to help build CoLab’s soon-to-be-released quality tools, benefiting design and manufacturing teams worldwide.
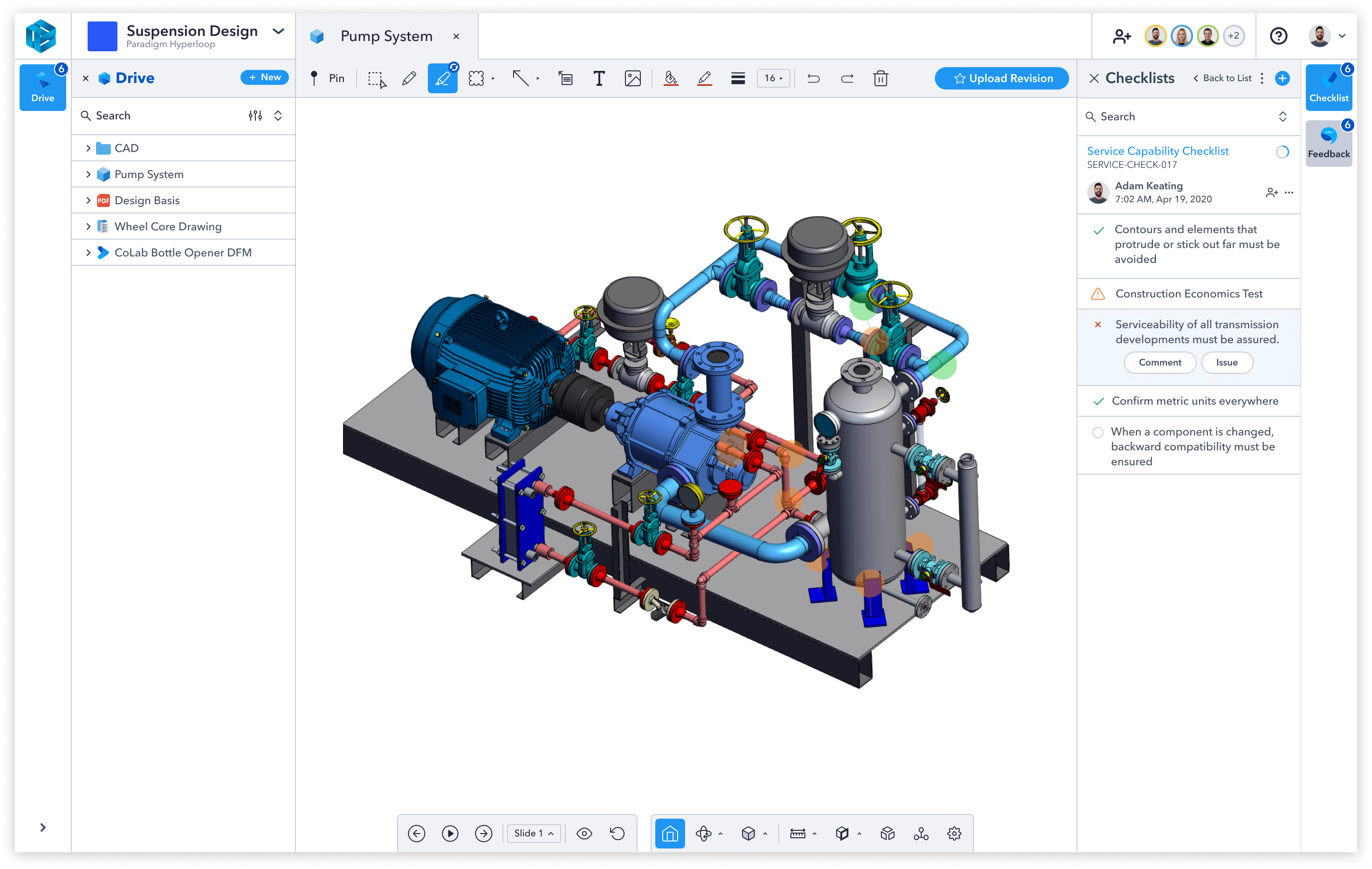
Achieve Efficiency Excellence
CoLab and Genoa had an initial goal of matching the team’s previous in-office drawing review efficiency. It quickly became clear that not only would the team reach that goal, they’d blow it out of the water. And today, they’ve done just that!
With previous steps like printing drawings, sending follow-up emails, searching through emails and versions are eliminated, Genoa can move faster than ever before.
“What took me 40 hours before, now takes me 32. I save 8 hours in a 5-day work week.”
- Bill Norman, Production Designer
Building the Future, Together
Genoa has seen immediate results from their CoLab implementation, and they’re not slowing down. Genoa has proven that with the right tools, they can hit even the most ambitious goals.
Like much of the design and manufacturing world, Genoa projects were impacted by COVID-19. Now, Genoa and CoLab are evaluating how to take the lessons learned and results achieved through the initial CoLab integration and share it across the rest of their project portfolio.
Genoa is now focused on implementing CoLab for their 3D review process, and expanding to their external partners to create a unified process and hub for every review required to design their next ship. Their team is positioned to lead the industry into the next generation of digital innovation, and are on track to become the most sought-after partner in shipbuilding.
Together, CoLab and Genoa are building the future of design and manufacturing collaboration, leading the shipbuilding industry forward.