The secret to boosting gross margins
2024 hasn’t been easy for manufacturing. Labor shortages, rising raw material cost and the push for digitization have put more pressure on gross margins than ever. But what if the secret to increasing gross margins isn’t about manufacturing at all – it’s about engineering.
Gross margins need a reframe
The tried-and-true method for increasing gross margins used to be simple: efficient cost management.
- Identify and reduce unnecessary production costs
- Optimize procurement processes
- Negotiate better deals with suppliers
- Increase product sales cost
However, more and more manufacturing leaders realize this is no longer enough. Supply chains need to be optimized for resilience more than cost. Reducing production costs and raising sales prices only go so far. Procurement has been overly optimized for efficiency.
And gross margins are still stagnating – or worse, declining.
So, what’s the solution?
The manufacturing leaders unlocking new gross margin growth are paying attention to the metric few others scrutinize: engineering design quality.
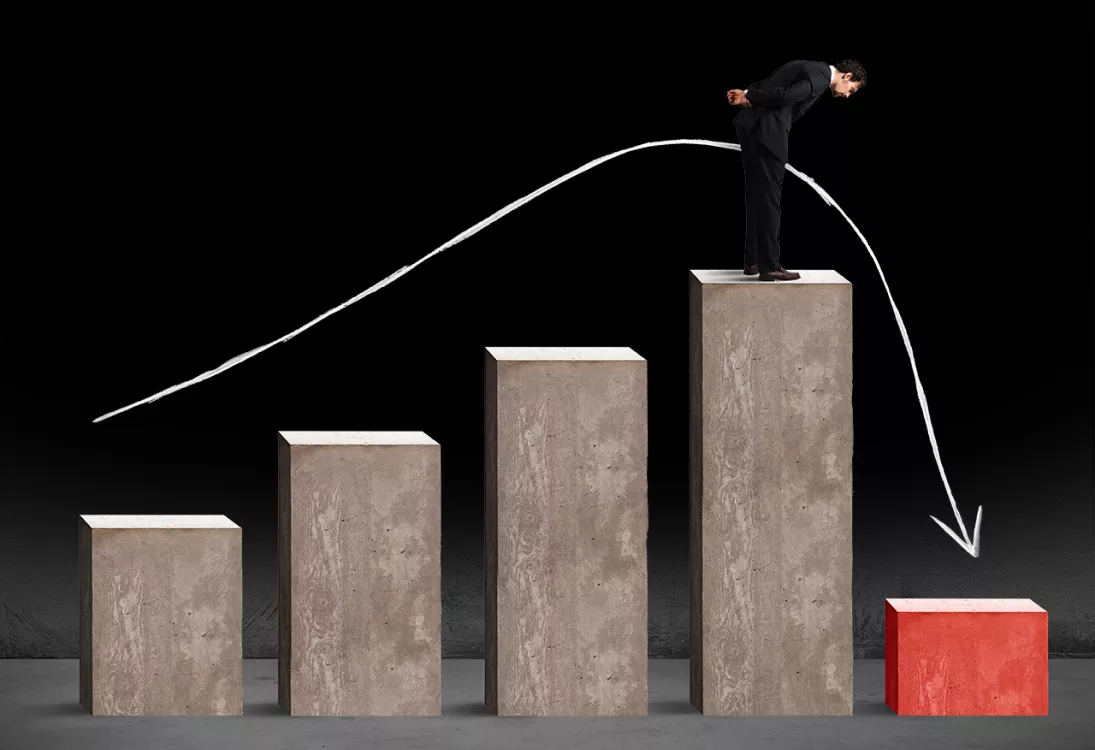
Where engineering design quality goes wrong
Before we dive in, let’s take a deeper look at engineering design.
Your products are the heart of your business. But the way your engineers develop products hasn’t changed in decades. With higher pressure to deliver products faster and more complex assemblies to work with, your engineering team needs more experts from more disciplines to make critical product decisions.
And these decisions are made everyday in engineering design reviews. The problem is the default method for engineering design review is meetings. And with the need to involve more people from more disciplines across the globe, these meetings often take weeks to schedule. Then, when the team finally gets together, most feedback isn’t heard. The feedback that is heard isn’t tracked and critical product decisions are lost.
The case for better engineering design quality
So, some product decisions are lost. What’s the big deal, right? The big deal is there’s a direct tie between the quality of engineering design reviews and higher gross margins.
Engineering teams have been feeling the bottleneck of poor design review for a long time. But the manufacturing businesses that win are investing to solve this now.
These companies realize that engineering excellence upstream is a strong predictor of manufacturing excellence downstream. Design quality drives product quality.
Because your most important product decisions are made in design reviews, when you invest in making those reviews great, you end up with better design quality, better product quality, and the downstream effects of that like fewer warranty claims and better gross margins.
You can see how the effects compound -- either into a sustainable competitive advantage or a ditch to dig out of.
The metrics that matter
The leaders investing in upstream engineering processes, like improving design review don’t settle for 5-10% efficiency gains any more.
These companies unlock new levels of effectiveness, cost reduction, and time to market. All of which positively impact product line gross margin.
Ford Pro saw 30% faster time to market when they started bringing customers into engineering design review.
Hyundai Mobis improved supplier cycle efficiency by 4x.
Mainspring Energy reduced costs by 50%, in half the time, with zero defects.
There will always be a time and place for efficient cost management. But if you’re like the leaders frustrated with the same strategies for stagnating gross margins, then now is the time to invest in engineering design quality.
Now is the time to drive engineering excellence.
Ready to invest in engineering excellence?
Assessing your team’s current design tools and processes is a great place to start. Here’s why engineering teams choose CoLab to drive better design reviews.
Why CoLab?