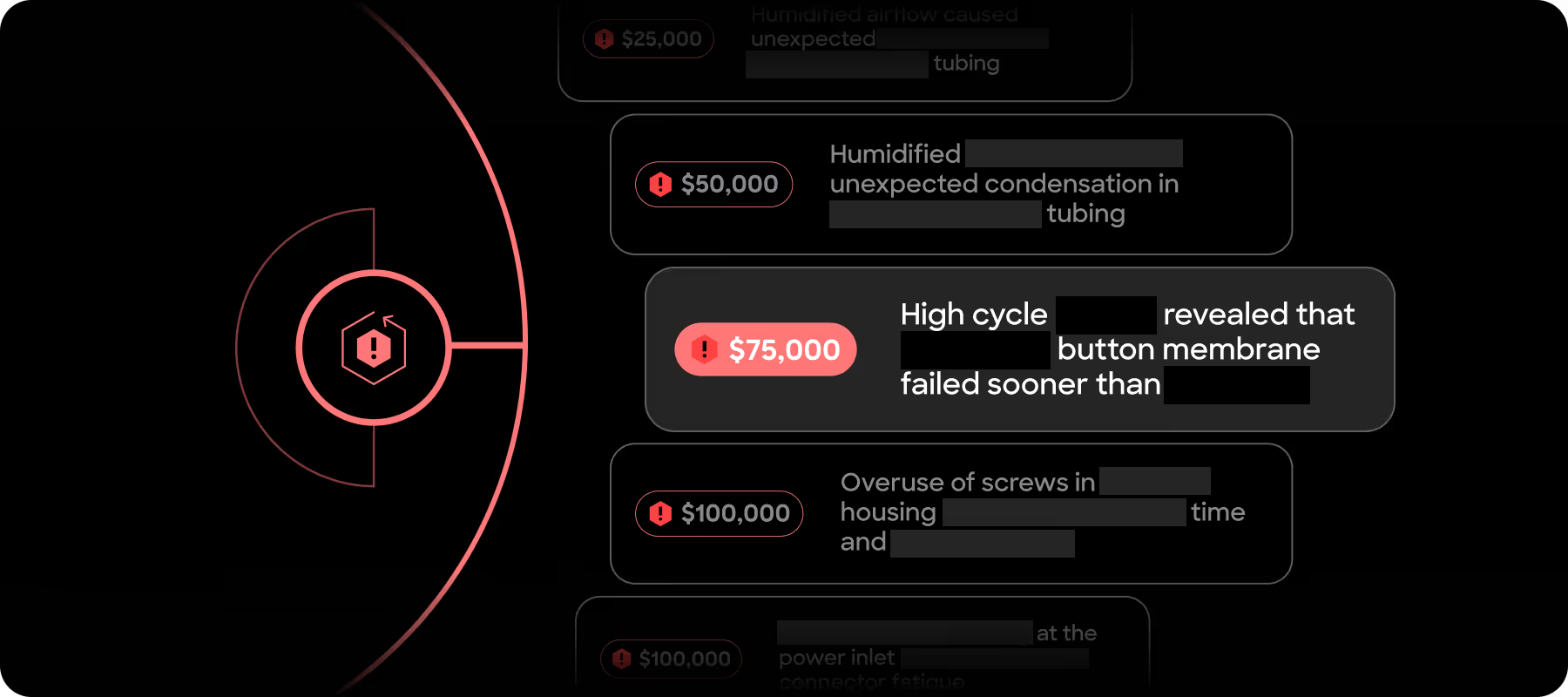
Lost design review feedback is the multi-million dollar problem you’re ignoring
Lost design review feedback is the multi-million dollar problem you’re ignoring
This article is part of the CoLab Research Reports series, where we publish findings from both engineering leader surveys and aggregated, anonymized CoLab data. To subscribe and receive reports to your inbox, click here.
A recent survey of 250 manufacturing engineering leaders exposed a shocking reality.
90% of companies delay some percentage of their product launches due to late-stage design changes.
This isn’t an annoyance affecting a couple NPD programs. This is a systemic issue spanning multiple manufacturing industries at the largest companies in the world.
And when the survey asked these same leaders how they could prevent late-stage design errors, the answer was clear. Better design reviews could solve for 72% of late-stage design changes.
This is not just an engineering problem. It's a business problem with serious financial consequences.
When design review feedback is lost and poorly managed, the costs echo through the entire value chain, leading to:
- Increased cost of poor quality (COPQ): In the form of rework, scrap, warranty claims, and regulatory penalties.
- Delayed or missed revenue: Prolonged time-to-market doesn’t just delay revenue, it causes missed revenue opportunities and lower product profitability.
- Lost market share: More agile competitors crop up every day and they’re starting to cut into the market share of the largest companies in the world.
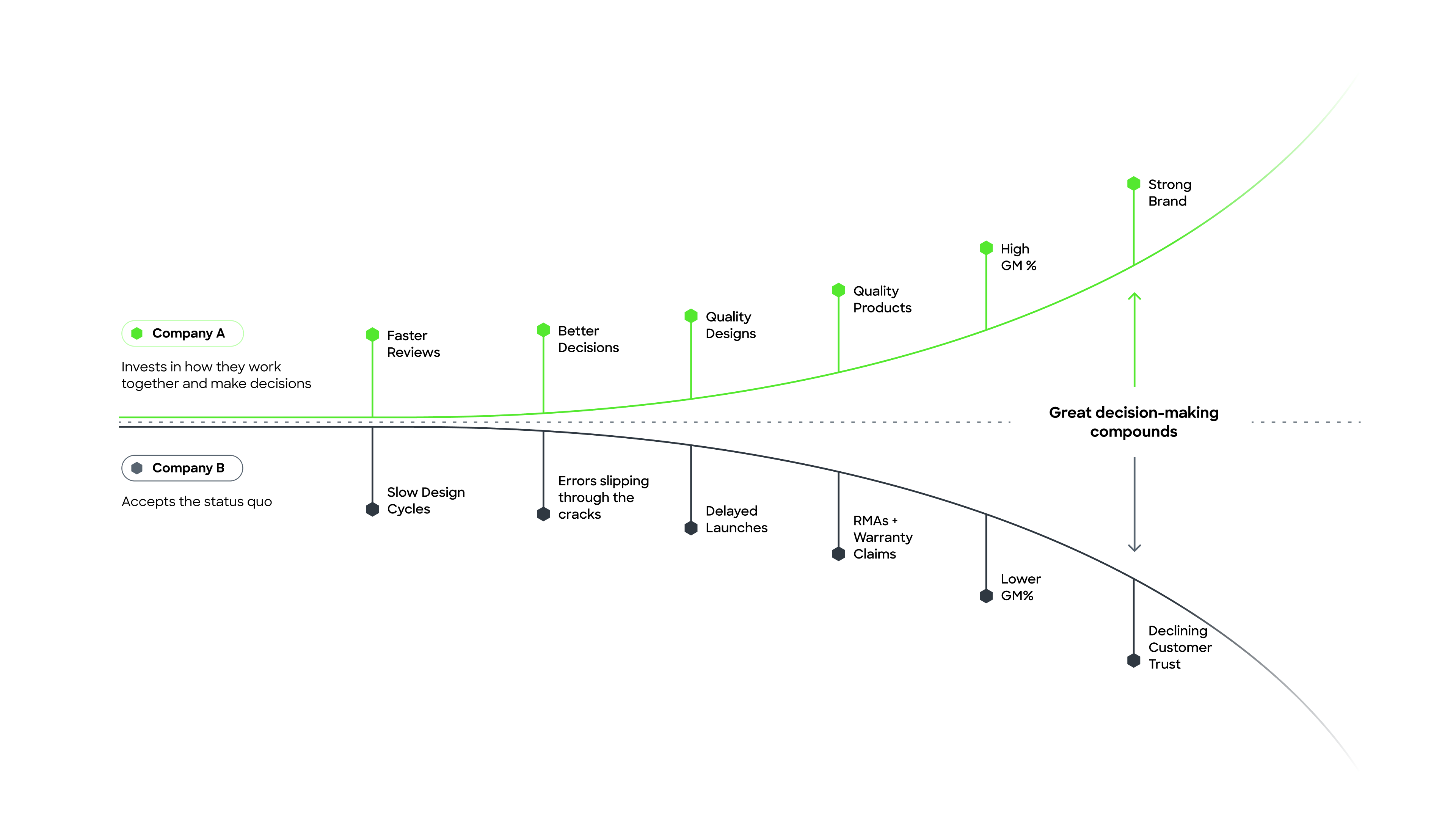
The data is clear. Engineering leaders must re-evaluate their early-stage product development processes if they want to improve key business metrics.
In this article, we’ll quantify how poor design review processes affect the bottom line. Then, we’ll outline the steps you can take to address this challenge today.
It’s not too late to solve early product development process failures. But, as AI and machine learning creep into hardware development, the time is now to make the shift.
How lost design review feedback costs millions
From the survey one storyline is clear:
- Too many companies delay product launches
- Those delays occur due to late-stage design changes
- Lost and undocumented design feedback cause late-stage design changes
Each of these problems causes its own quantifiable business impact.
Let’s dive in.
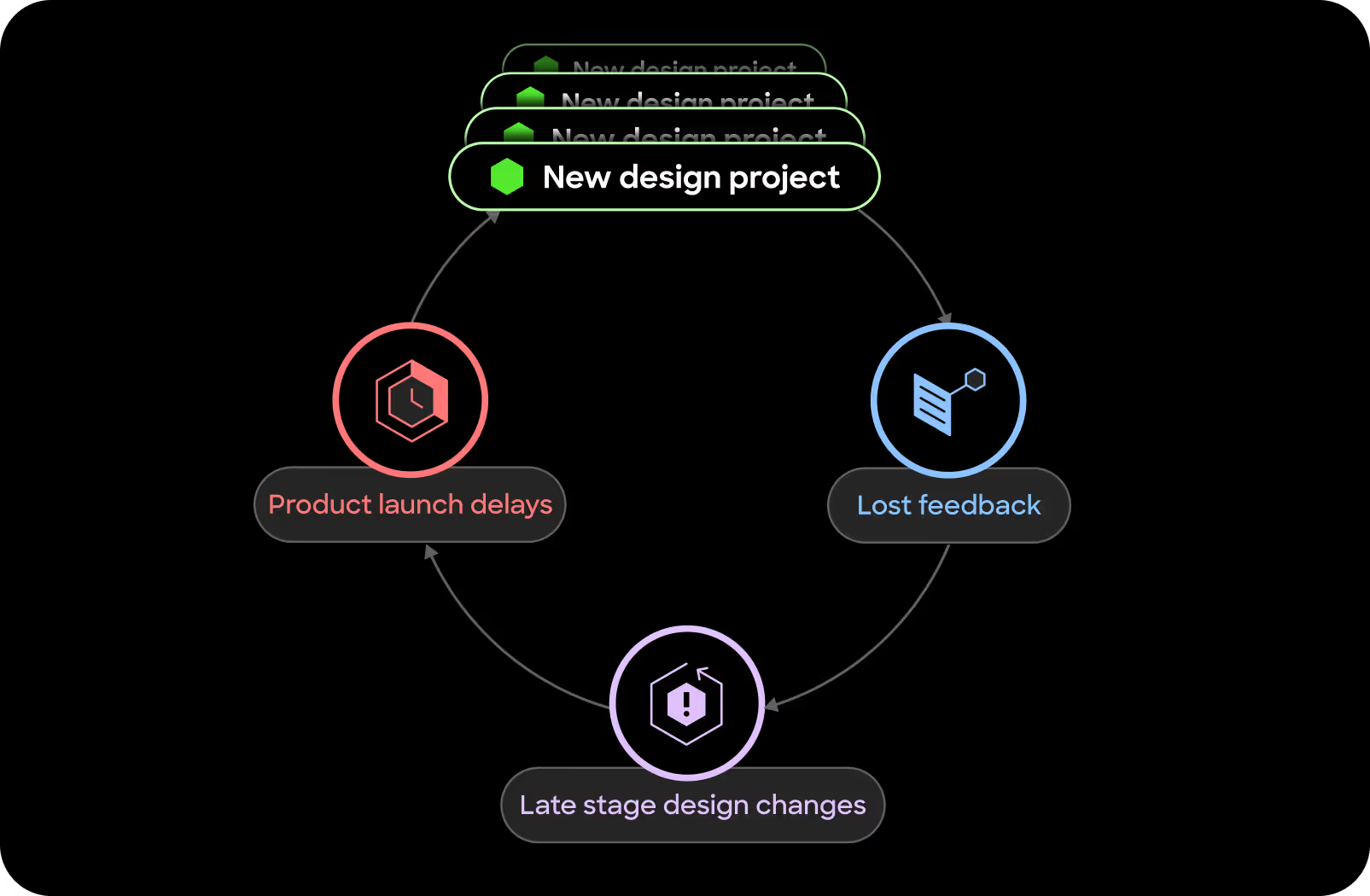
Delayed product launches cause lost profitability
McKinsey research shows that launching a product six months late reduces its lifetime profits by 33%. Meaning time-to-market is the one of the most critical factors for long-term product success.
A delayed product launch is not just a missed deadline, it’s a direct hit to the bottom line. And it keeps hitting the bottom line over and over for the long term.
Now, let’s reverse this statistic. What if launching a product 6 months early could increase its lifetime profits by 33%+. In manufacturing, where gross margins and profitability are already razor-thin, this should be the most important product initiative.
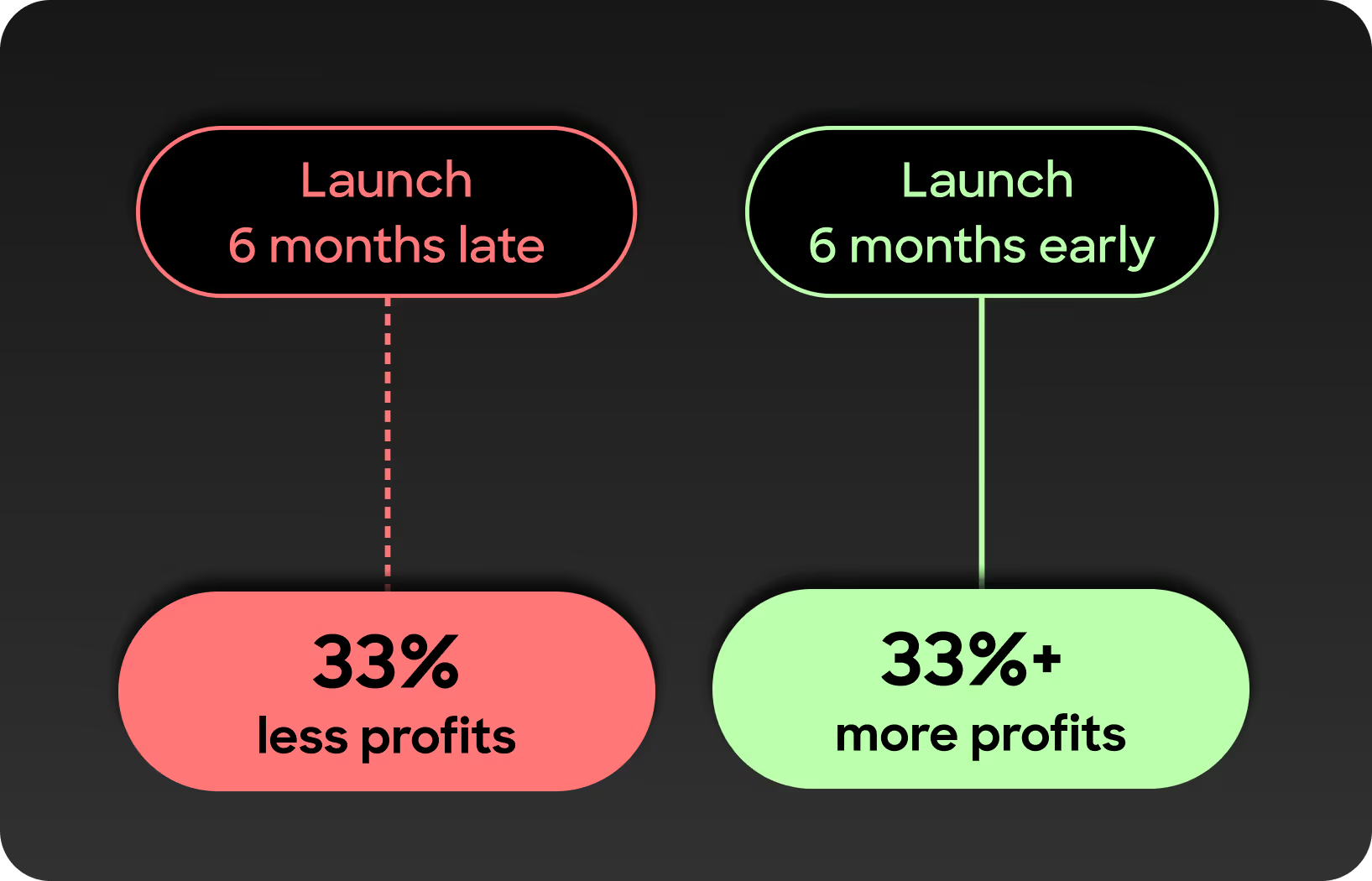
And, for most manufacturing companies, it is. But, how they go about it differs.
Co-creating with their supply chain, aggressively diversifying supplier networks, investment in automation and AI are all corporate manufacturing initiatives geared towards two major goals:
- Get to market faster
- Increase product quality
But, these initiatives only focus on late-stage development.
Next, we’ll dive into why bringing the magnifying glass (and the resources) to early-stage product development could be the most beneficial way to both get to market faster and increase product quality.
Late-stage design changes exponentially increase costs
According to the survey, late-stage design changes cause, on average, a 7% delay in total product launches and cause 90% of all companies to delay some portion of their launches.
Late-stage design changes also compound as products and global supply chains get more complex. The cost of these changes escalates exponentially the later they occur:
- If a design issue is caught in the concept phase, the cost to fix it is negligible.
- If it is caught during prototyping, costs increase by 10x.
- If it is found post-production, it can be 100x more expensive due to recalls, service costs, and lost brand trust.
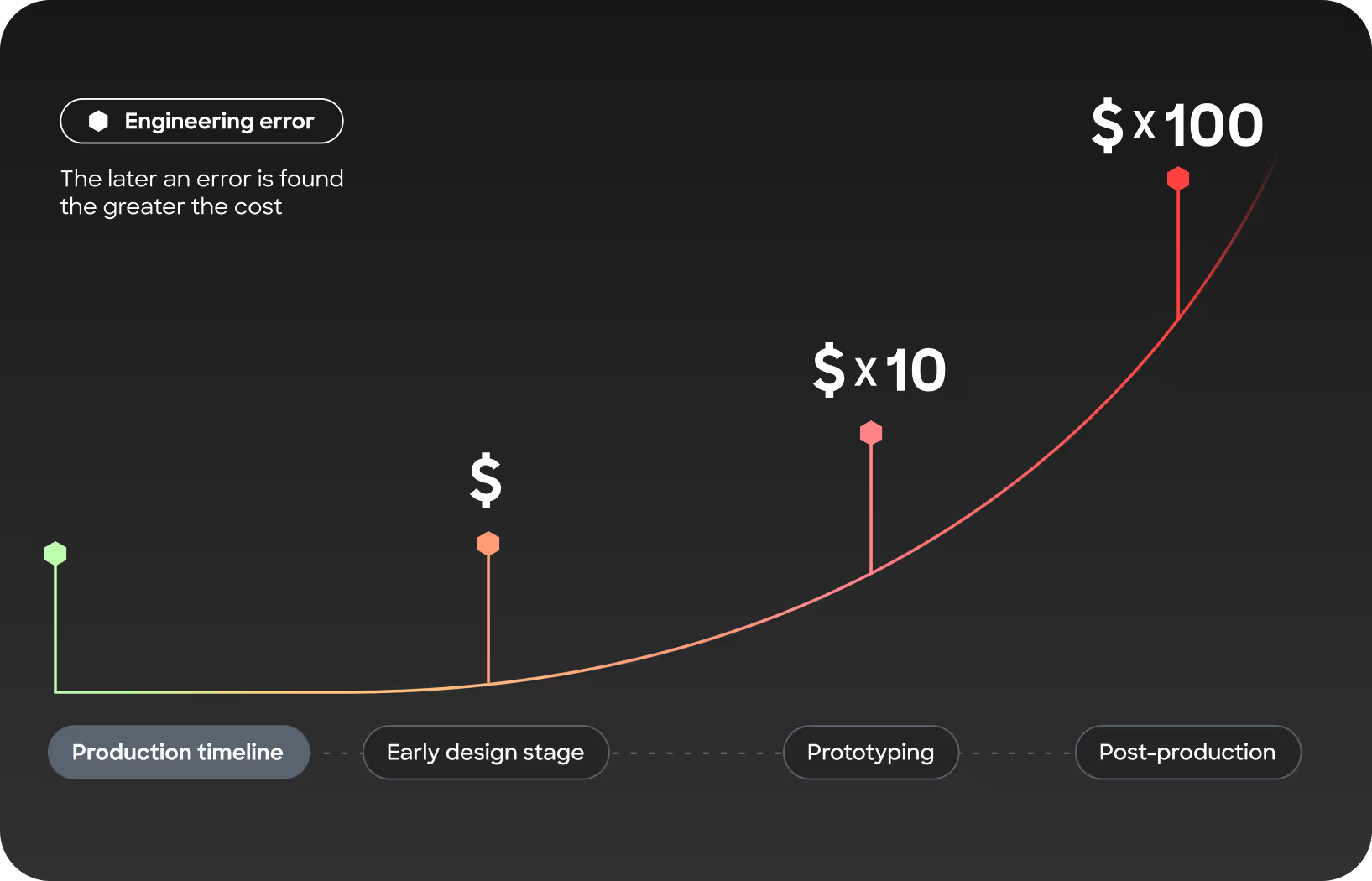
The Boeing 787 Dreamliner program is the perfect representation of this compounding problem.
By the end of this program, Boeing experienced significant production delays and cost overruns, with development costs ballooning from an initial projection of $5 billion to over $20 billion.
These cost overruns were directly correlated with late-stage design changes, supplier misalignment, and manufacturing rework. All challenges that could have been mitigated with more rigorous early-stage design reviews.
Lost design feedback as the root cause of product failures
So, we know most companies experience product launch delays. And we know late-stage design changes cause this issue. We also know these problems combined result in cost overruns and lost profitability. The next question is: what causes late-stage design changes?
The answer is so simple, it feels too easy: Lost design review feedback.
In the research survey, engineering leaders admit that 43% of all design review feedback is lost and never documented. Nearly half of all design review feedback: gone.
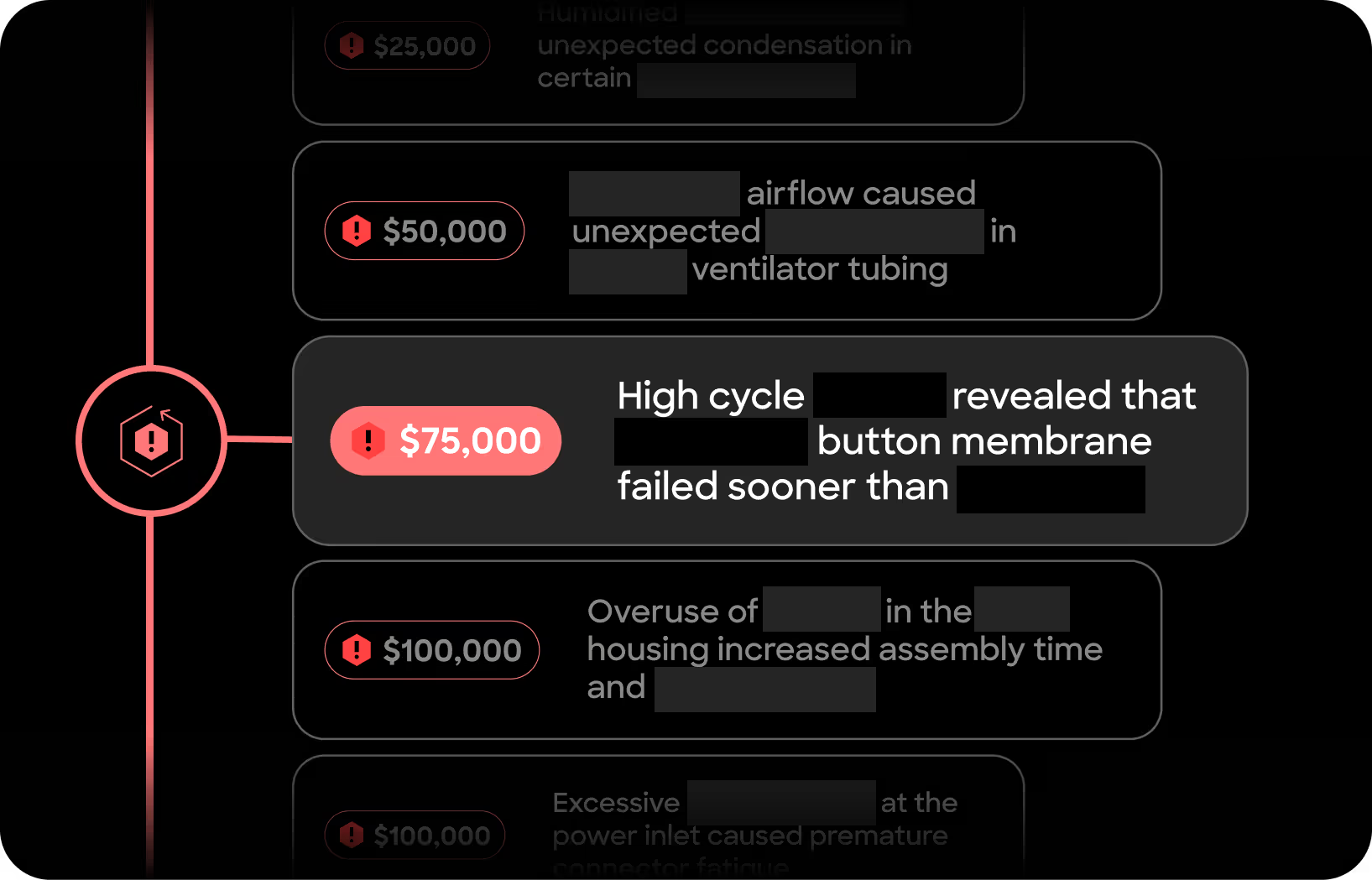
This missing information, of course, leads to late-stage design changes and product delays. But it can also lead to safety-critical failures, cost overruns, and wasted engineering hours.
In a recent research study on “Reasons and costs for design change during production,” the findings show that design change costs are anywhere from 2.1% to 21.5%. And, on average 8.5%, which is the cost of an entirely new design project.
The financial impact of lost feedback extends beyond direct costs:
- Engineering teams waste hours re-hashing past design decisions
- Design miscommunication leads to warranty claims and compliance failures
- Cross-functional misalignment results in costly redesigns
These inefficiencies add up, making poor design review processes – and, most importantly, lost design feedback – one of the most underrated profit drains in modern manufacturing.
How to recoup those lost millions through better design reviews
According to the original survey, engineering leaders ranked design review quality as the most critical factor for on-time product development (24%).
Why? Because high-quality design reviews minimize lost feedback and reduce late-stage changes – the core issues causing the domino effect of product launch delays, lost profitability and cost overruns.
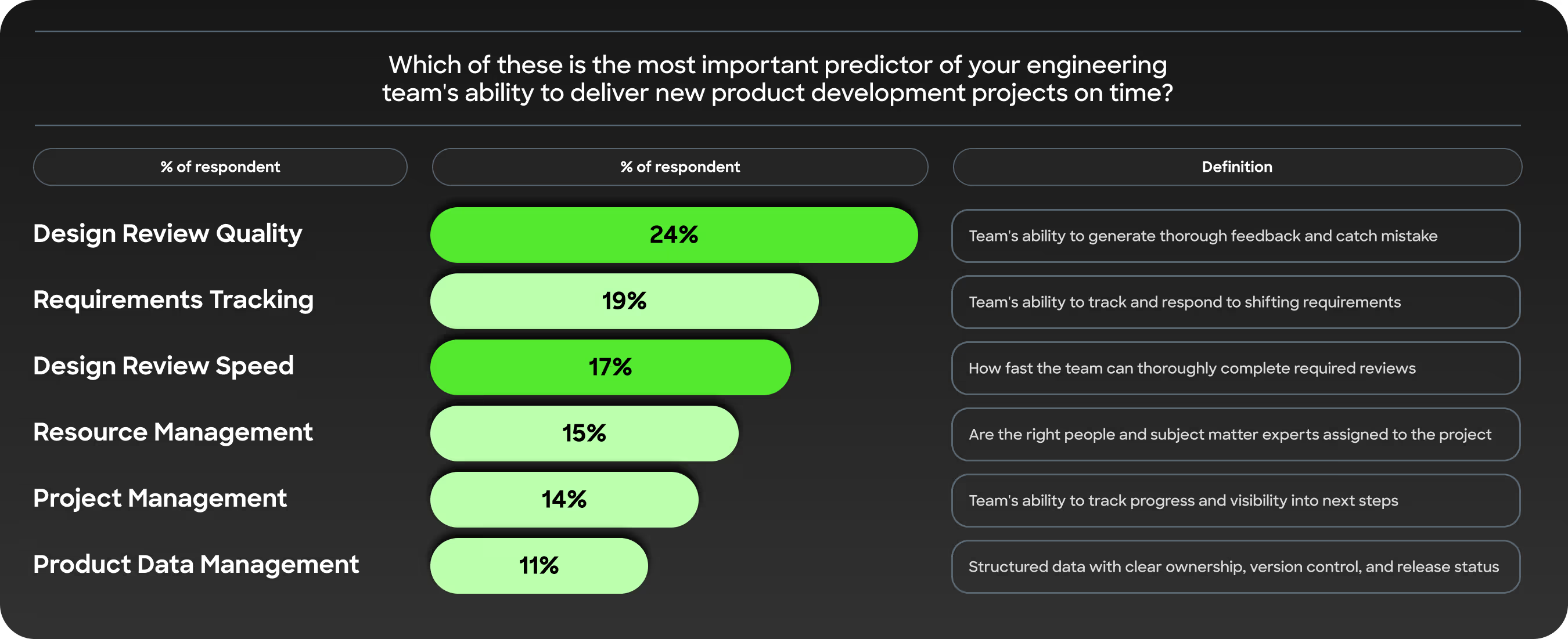
McKinsey emphasizes that companies excelling in early-stage design reviews are 2x more likely to meet their product launch deadlines. They also experience a 30% reduction in COPQ, improving overall margins.
By improving design reviews, companies can unlock millions in cost savings across multiple areas:
.png)
How to fix your design reviews
So, we’ve discussed why your design review process is costing millions and how you can recoup that money through better design reviews.
Now, let’s outline how, exactly, you can fix the design review process to capture all design feedback, eliminate late-stage design changes and launch products on-time.
✅ Implement a structured, data-driven design review process
- Move away from outdated tools like email and spreadsheets—64% of companies still rely on these, despite their inefficiencies.
- Implement centralized design review platforms that integrate directly with PLM/PDM systems.
- Standardize review templates to ensure completeness and accountability.
✅ Centralize design review feedback
- Deploy automated tracking systems to ensure feedback is not lost.
- Use AI-driven analytics to identify recurring design issues.
- Require clear action items after every review, with assigned owners and deadlines.
✅ Align engineering, manufacturing, and supply chain early with one platform for design reviews
- Engage manufacturing and supplier teams during the design phase, not after.
- Leverage collaborative 3D model annotation tools to improve communication.
- Adopt cross-functional design sprints to address manufacturability early.
A Design Engagement System as the better tool for design reviews
Engineering leaders predominantly agree: they need better tools to improve design reviews. A tool that implements a standard process, centralizes design feedback and aligns all product stakeholders on design.
That tool is a Design Engagement System (DES). A DES, like CoLab, lets engineers and any other design stakeholders:
1. Build a review process as a byproduct of using the tool.
A DES can be used to create a variety of reviews, from informal peer checks to structured gate reviews to VA/VE events. By building a review, attaching predefined checklists and even segmenting by team, your team is building a review process just by using the tool. Reviews in CoLab let you capture feedback asynchronously, address minor issues outside of meetings, or document and organize feedback during meetings.
2. Reference the right files, feedback, and design history every time you make a decision.
Assembling engineering files for a design review can take hours. Sometimes, key files are left out of a package. Not to mention design history, which may be buried in old emails, slide decks, or spreadsheets. This is what leads teams to lose 43% of all design feedback.
By doing your work in CoLab, you’ll automatically create a centralized database of reviews and feedback across every revision of every file. Need to bring a new SME up to speed? Reviewers can quickly toggle between files and see all relevant feedback in the context of the model.
3. Replace sequential workflows with engaging reviews.
Reviews are often sequential, with one person creating markups, then sending them to the next person. This can lead to duplicate feedback, comments that contradict one another, and even late stage errors.
With CoLab, you can review files together and see other people’s feedback populate in real-time. Instead of sending static markups back and forth, reviewers can interact with each other via discussion threads.
4. Automate the design review admin.
Documenting feedback during a design review is manual and time consuming. And the more context you capture, the more admin work it takes. It’s no wonder that 43% of all feedback from design reviews is never documented at all.
That’s why CoLab automatically tracks and organizes design feedback, as you do the work. Leaving feedback during a review creates a unique object that is automatically organized into a database and assigned its own URL.
Now, what?
If you’re ready to stop losing design feedback, and as a result, profits and revenue, learn more about CoLab here.
Quantifying the impact of design review methods on NPD
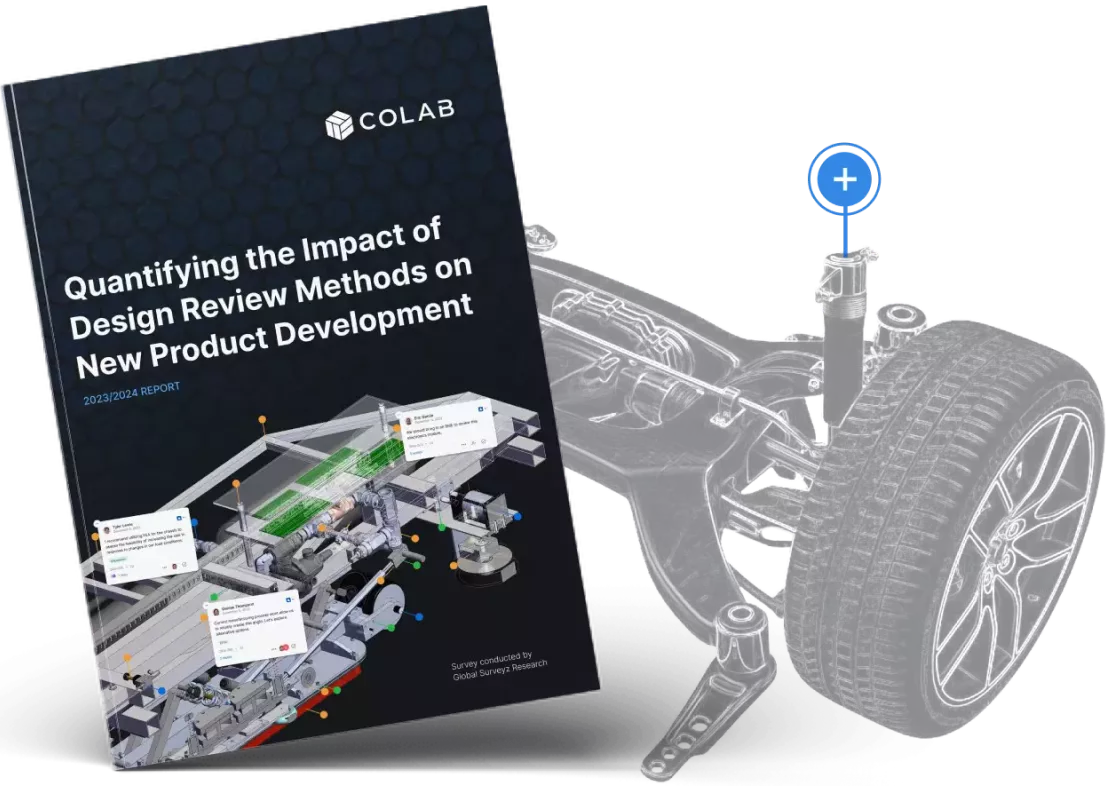