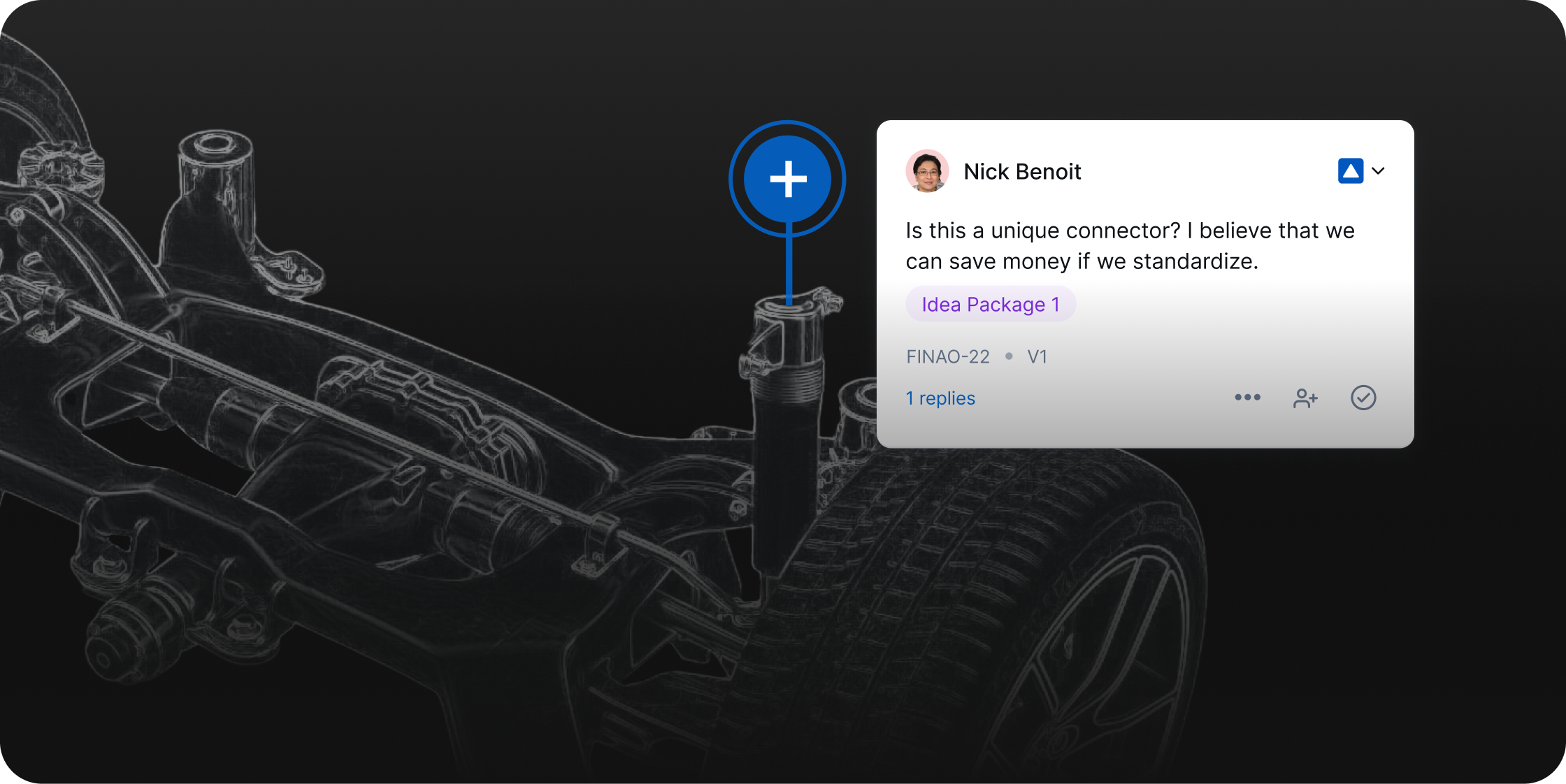
43% of design review feedback is never tracked or addressed
43% of design review feedback is never tracked or addressed
This article is part of the CoLab Research Reports series, where we publish findings from both engineering leader surveys and aggregated, anonymized CoLab data. To subscribe and receive reports to your inbox, click here.
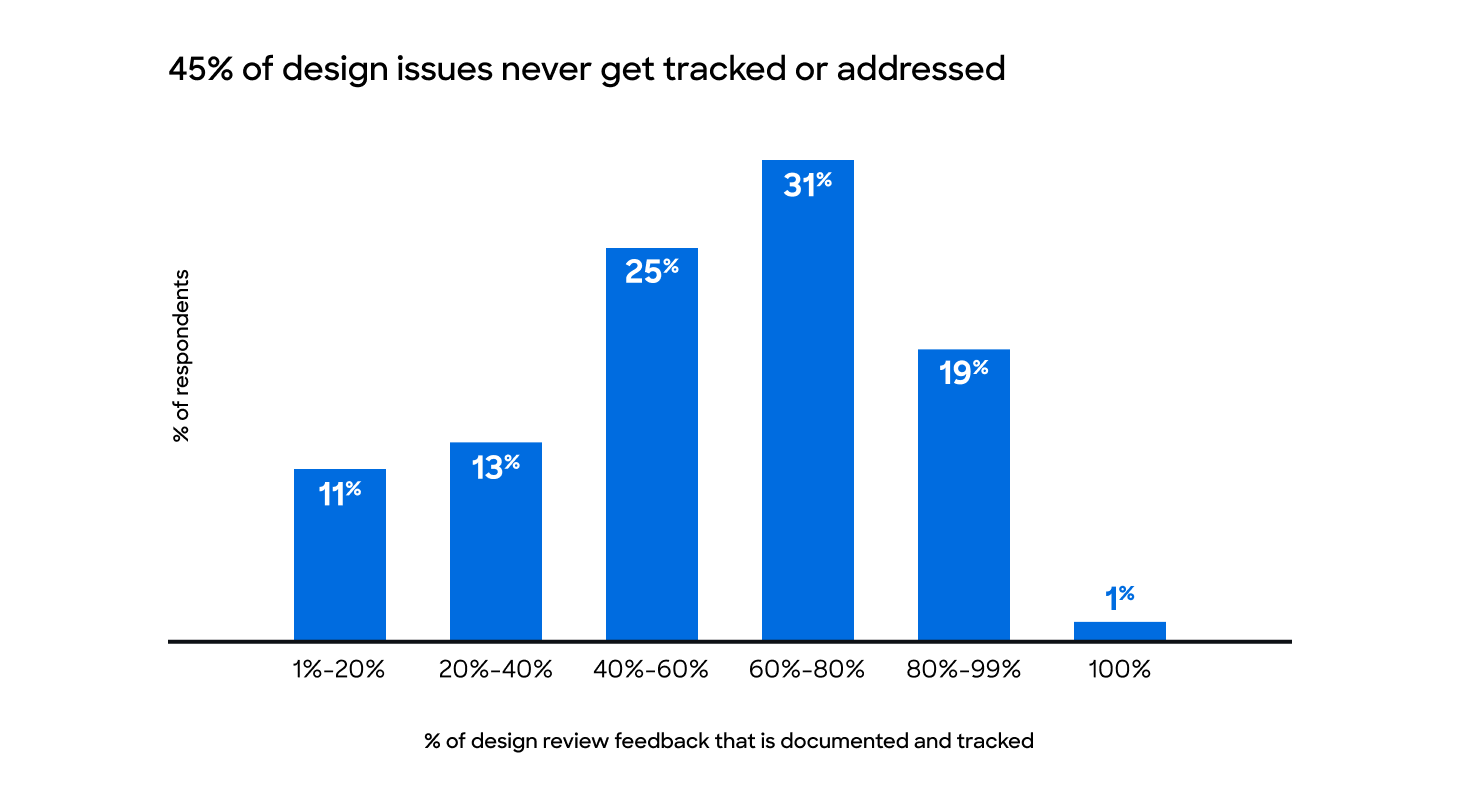
This is a sobering statistic.
Nearly half of all design review feedback is never documented or tracked.
All those meetings, all those hours spent screenshotting CAD, all those meticulous PowerPoint markups to communicate design intent, all those phone calls, Teams messages and emails – 43% of that effort is for naught.
This is on average.
1 in 4 engineering leaders estimate that 60%+ of design review feedback is never documented or tracked.
The natural question is: does this matter? If most teams lose 43% of design review feedback, is it even an issue?
Let’s break it down.
The hidden cost of unaddressed feedback: A thousand tiny cuts
In another report, we investigated a different sobering statistic: 90% of teams delay product launches due to late stage design changes.
For the most part, late stage design changes are completely in the team’s control. They’re simply missed design errors that crop up during prototyping or a pilot build – or worse, during production.
Except in extreme circumstances, late stage errors are rarely safety-critical issues or major assembly blockers. Instead these issues are like a thousand tiny cuts. Each error leading to a PPAP rejection, another rework cycle or a change to a frozen design. And each of these add up to project milestone delays and, eventually, a product launch delay.
In an engineering environment where teams only get more downward pressure to launch products faster, fixing these tiny cuts is more important than ever.
What’s in those tiny cuts?
The most common cuts engineering leaders experience are:
- Missed regulatory issues: For industries such as automotive and heavy equipment manufacturing, unaddressed feedback can translate to safety risks. But this is rarely an issue that passes through to production. Instead, these small safety issues mean failed regulatory standard checks, like PPAP and ISO.
We often hear comments from engineering leaders like, “We don’t bring the right people into design, so when we’re PPAP-ing things, our PPAPs often fail.”
Something as simple as the incorrect file version leads to a regulatory rejection and a rework cycle. Expand this across multiple assemblies and 10+ NPD projects and it’s not difficult to see how tiny inefficiencies in the early stages of product development mean delayed project timelines.
- Ignored cost efficiencies: Unresolved feedback often includes suggestions to eliminate unnecessary costs. This is especially true when manufacturing engineers add feedback during design. They often suggest ways to reduce BoM costs and engineer components for better manufacturability.
Ignoring these insights results in higher production costs and impacts gross margins. Not to mention, that manufacturing engineer is a lot less likely to provide helpful feedback if they think it’ll just get ignored next time.
- Missed opportunities for innovation: If there’s one thing great engineering leaders pride themselves on, it’s fostering a culture of innovation.
However, innovation during product development is complicated and difficult to render from idea to action. And, that 43% of overlooked feedback often includes the “nice to haves” and ideas that don’t necessarily mee the requirements.
Meaning the feedback that contains groundbreaking ideas and a competitive edge often gets ignored.
Furthermore, because design reviews are often conducted during meetings, quieter engineers don’t actively participate in idea generation – already a source of missing feedback. And, when they do, that complicated innovation idea is a lot less likely to make it into the next revision. Which, in turn, only makes it less likely the quiet engineer participates again.
Why fix ineffective issue tracking now?
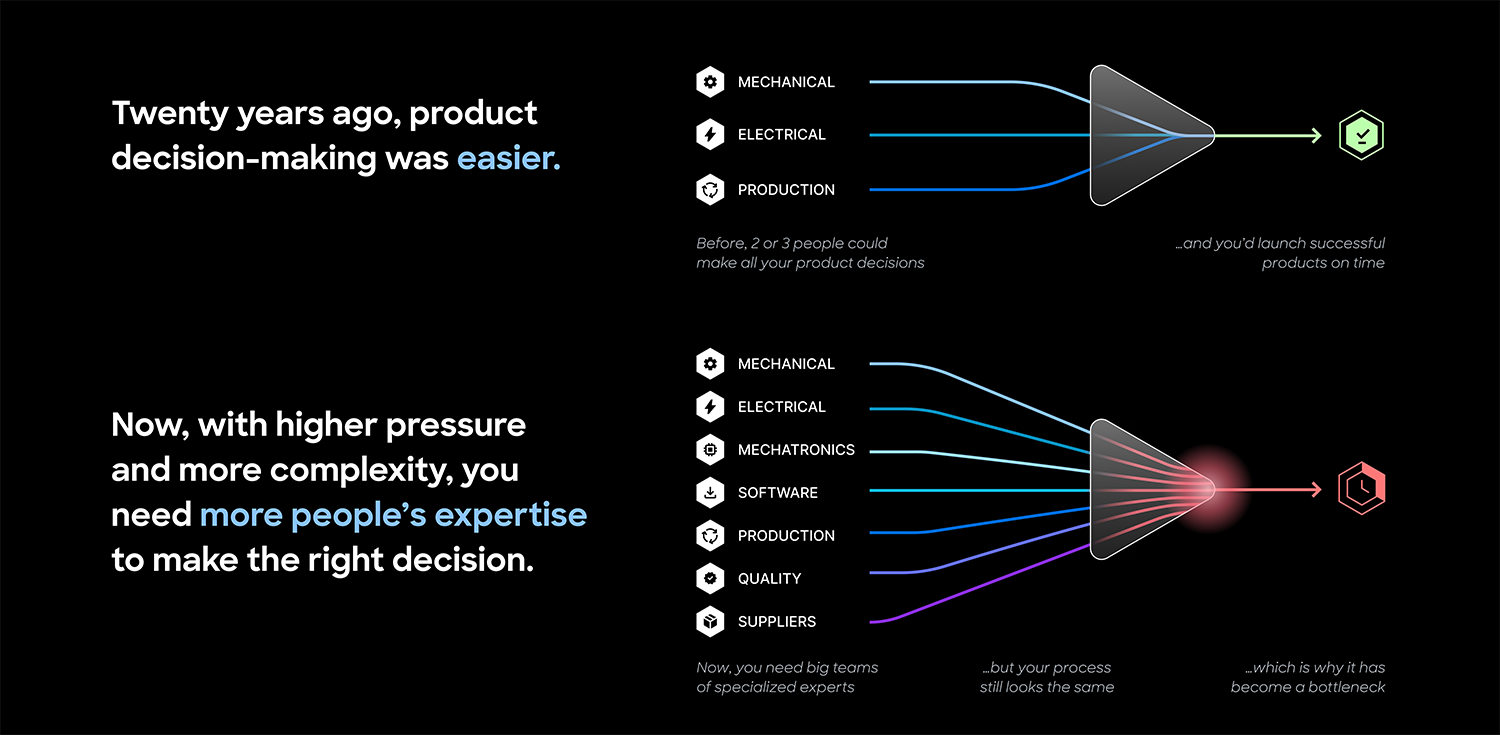
Like we mentioned earlier, engineering teams are under more pressure than ever to launch products faster. In competitive markets, even a few weeks’ delay can mean lower gross margins and reduced market share.
It’s even in the news. Multimillion dollar contracts with long-standing customers: canceled. Because OEMs and suppliers can’t deliver fast enough and keep delaying product launches.
But with more stakeholders than ever involved in product development, engineering teams struggle to adapt the same tools and processes from 10 years ago to a very different product development environment today.
The companies that have prioritized this gap are winning. By linking manufacturing excellence downstream to engineering excellence upstream, they realize fixing product development delays means fixing design review.
Size matters: how company size affects issue management
Data shows that larger companies (5,000+ employees) capture and resolve design issues much more effectively than smaller companies (1,000-4,999).
These organizations document 70% of feedback compared to just 50% in slightly smaller companies. This disparity raises an important question: What are large companies doing right?
More resources, more success: Design feedback best practices from large companies
It’s no secret. The larger the company, the more extensive the resources. Large companies also benefit from long-term strategic planning. Projects are done in 3, 5, 10 year increments.
This means large companies have both the experience and the resources to invest in long-term strategic investments – like improving engineering excellence upstream to positively impact manufacturing excellence downstream.
Here are the top three best practices large companies use to capture and resolve more design review issues:
1. Culture and people
Change management requires the right leader and the right support from upper management. For a shift like giving more resources to engineering so they can fix their design review process, the company needs a strong leader to see it through and the right leadership team to provide resources. No one likes change. The right culture will help guide the team to see the long-term benefits of a change for them.
2. Well-defined processes
Having a structured, well-defined process for design reviews is crucial. Unfortunately, this is a rarity more often than the norm. However, some companies do it right. And when they do, the design review process involves setting clear objectives for each review, assigning responsibilities for tracking and addressing feedback, and ensuring that there is a systematic approach to follow-up. Regularly scheduled reviews, combined with clear documentation and accountability, help ensure that feedback is both captured and resolved.
Relying solely on meetings to evolve designs is also not enough. Large companies often have additional processes in place outside of formal meetings to track and address feedback. This might include dedicated teams or roles focused on design quality, continuous integration of feedback into the design process, and robust project management tools to ensure nothing slips through the cracks.
3. Supplemental tools
Large companies are more likely to use defined tools within a process. This might be free or paid CAD viewers to document feedback effectively or other tools to visualize and markup CAD. Such tools allow for precise, visual feedback that can be easily tracked and managed. The ability to annotate directly on designs ensures that feedback is clear and actionable, reducing the risk of miscommunication or oversight.
We say this to preface that large companies often come to CoLab lacking this third component. They have the people, they have the processes (in different stages of maturity) but they often don’t have the tools to match.
The engineering tool gap
Let’s do a quick recap:
- 43% of design feedback is never tracked or addressed
- 90% of companies delay product launches due to late stage design changes
- Large companies pave the way with better culture and processes, but…
- There is still a lack of dedicated design review tools to address the feedback gap
The right tool, according to this study, should do a few key things:
- Make it easy for many design reviewers to access the system. This should also include making it easy to get data, like files and feedback, into and out of the system. Both these tasks should be done while maintaining critical security protocols.
- Let reviewers leave feedback in the context of the model or file. Like we mentioned earlier, most design review happens in meetings and, because of this, much design feedback is lost. The same goes for PowerPoint, email, spreadsheets and Teams chats. Lots of back-and-forth, very little follow-up, almost zero tracking. A design review tool should let you leave comments where it matters and let you track where those comments live.
- Track every bit of design feedback – automatically. We’ve seen it over and over in this exploration: design review feedback gets lost because it’s done in untrackable places. An effective design review tool should track all design feedback in one place – so teams can implement that feedback. Because isn’t this the goal of design review: to catch errors early, so teams get better products to market faster?
Until recently, such a tool didn’t exist. But today, it does. And it’s called a Design Engagement System.
And the engineering teams who adopt this as part of their design review process see:
- NPD cycles cut in half
- 10x+ more feedback during design review
- Eliminated rework cycles
Ready to see how it could work for your team?
About the survey
To get greater insight into the state of complex product development processes, we commissioned a survey of 250 full-time employees, 50% of which are Engineering Managers or Directors, and 50% of which are VPs or C Level Executives.
Respondents work in the manufacturing industry, specifically in industrial equipment, heavy machinery, automotive, and consumer hardware, and are split across the US, the UK, and Western Europe.
All respondents work at companies with 1,000+ employees that have already invested in a PDM or PLM system.
This report was administered online by Global Surveyz Research, a global research firm. The respondents were recruited through a global B2B research panel, invited via email to complete the survey, with all responses collected during October 2023. The average amount of time spent on the survey was 5 minutes and 44 seconds. The answers to the majority of the non-numerical questions were randomized, in order to prevent order bias in the answers.
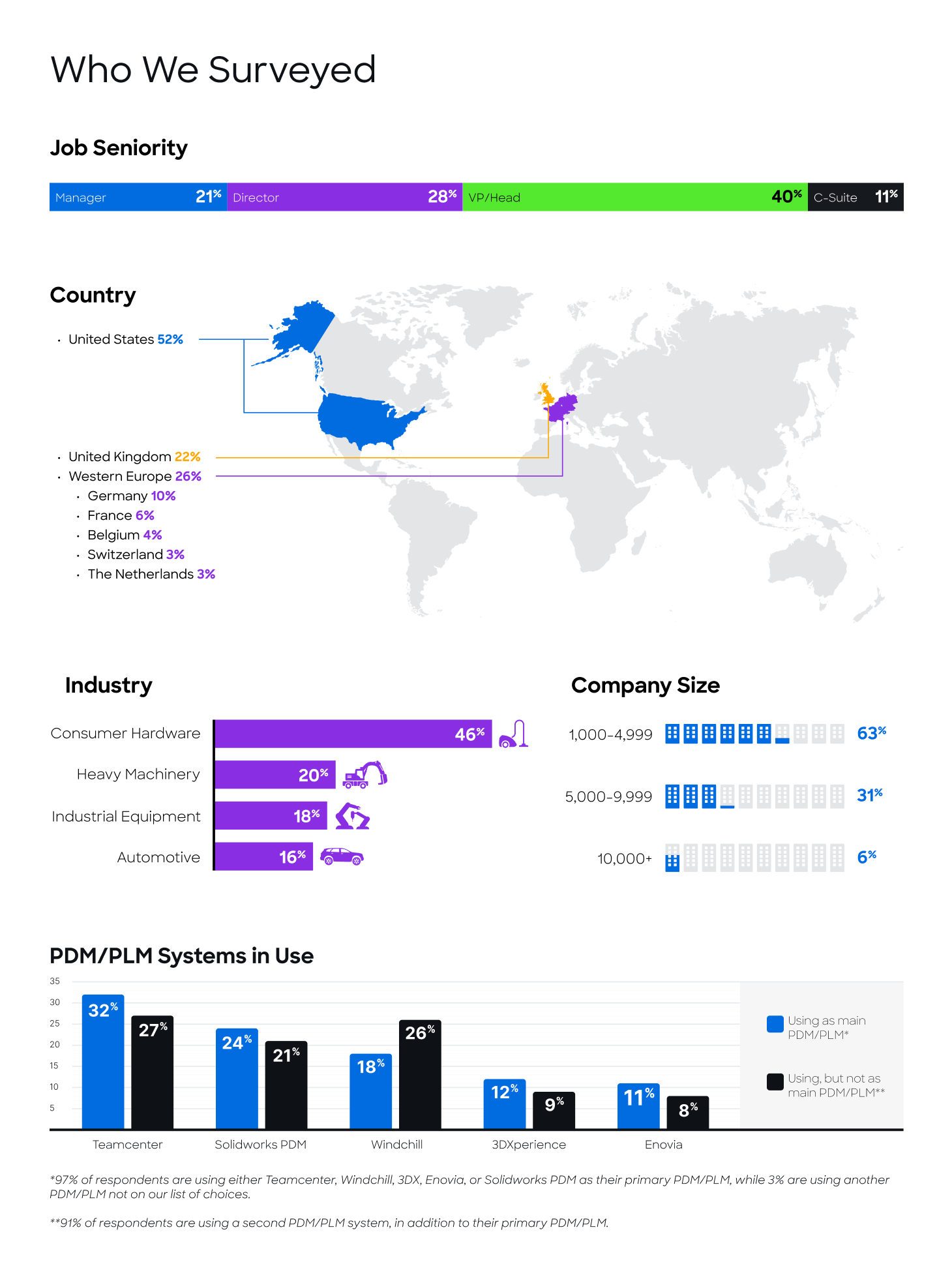
Quantifying the impact of design review methods on NPD
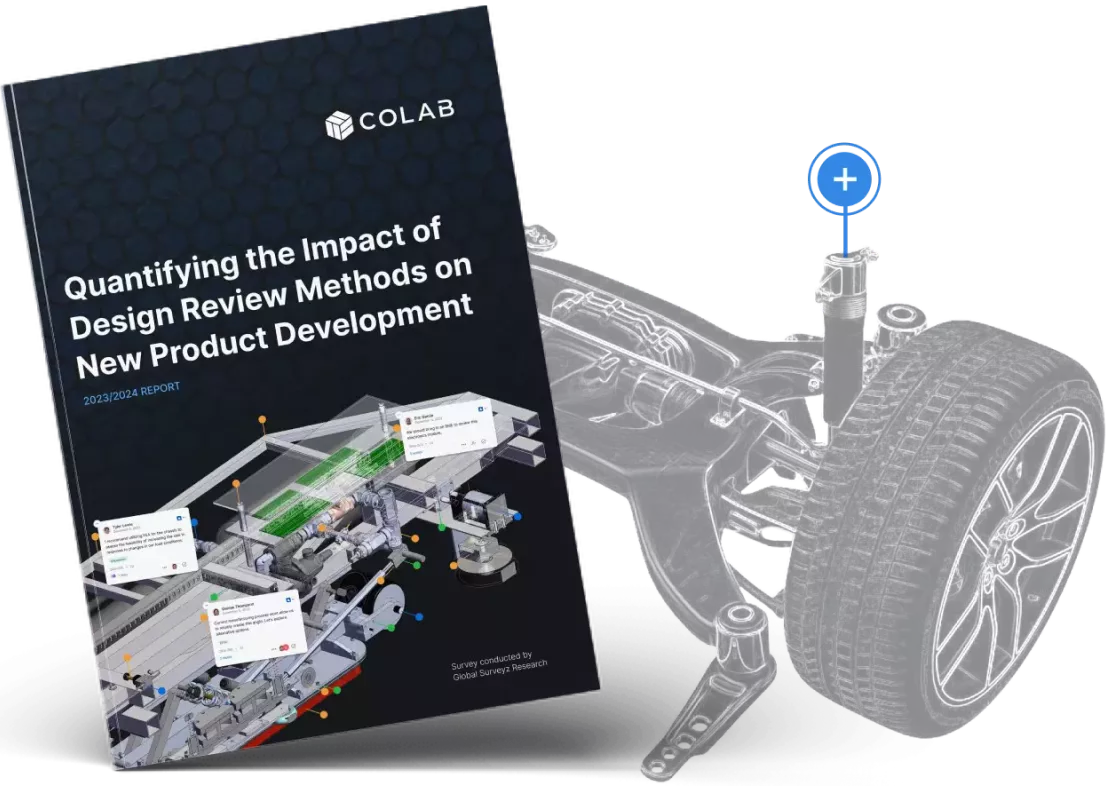