Why Your Bill of Materials is as Critical as Your Design Data
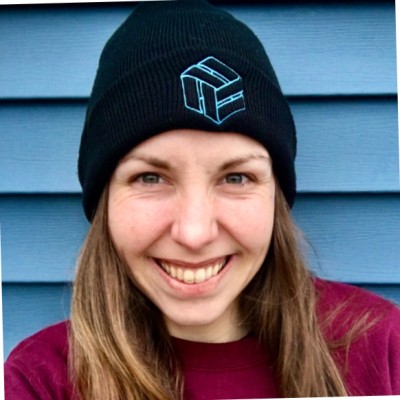
Meagan Campbell
August 26, 2021
6
min read
CAD is just one piece of the puzzle when it comes to creating physical products. While you may already understand that the Bill of Materials (BOM) plays an important role in product development, it’s worth taking time to consider where this critical item fits within your existing processes. After all, even with flawless design data, if your BOM isn’t right—your product won’t be, either.
Since your BOM is more than the physical parts alone and encompasses everything you need to make your finished product, it’s a critical tool to capture information that 3D models don’t. And, of course, when reviewing a design thoroughly, you need to examine both your CAD and your BOM together. In some instances, the BOM is all that’s necessary to define an assembly. For example, by using a 3D product catalog, it’s possible to specify complete jigs and fixtures without designing any custom parts yourself—rather, you’re indicating part numbers to use. You might create something by just creating a Bill of Materials and instructions on how to arrange them to achieve some useful purpose. So it’s important to have solid processes around both your BOM and your CAD.
What can make things tricky, though, is the lack of universal standards around BOMs. While “Bill of Materials” is often the language used, sometimes the same item might be referred to as a parts list or an assembly list. There’s no single, common way of creating or looking at a BOM. An engineering Bill of Materials (eBOM) might be created in CAD, while a manufacturing Bill of Materials (mBOM) might be created in a spreadsheet or an ERP system. But with the right process in place, you can make sure your BOM gets reviewed alongside your design data—and that stakeholders both inside and outside your organization are able to provide crucial feedback, early and often.
This post explores why the Bill of Materials is so critical to consider from the outset of your design projects, and how your team can improve by incorporating the BOM throughout your review process.
Non-Designers Rely on the BOM for Essential Info
Your Bill of Materials acts as the single source of truth between many different systems and stakeholders—from engineering to production to sales and service. It defines the final word of the product, which is why it’s just as important (if not more) than the CAD for that product. At minimum, the information in your BOM also impacts the information in your PDM/PLM, ERP/MRP, and CRM systems.
Not everyone who interacts with a BOM will need to see the design data. A service technician doesn’t look at the CAD for a product; they use the Bill of Materials. They need to know the right part or assembly number to order, not the geometric design. The BOM becomes a means of communication between engineers and technicians, users, or other stakeholders. It’s a handoff point for critical knowledge about the product.
Your Bill of Materials needs to be correct. Without a good BOM, other business systems cannot operate in concert with your engineering team. You can have the best Enterprise Resource Planning software in the world—but if the BOM is wrong, you’re planning for the wrong resources.
Your BOM Should Evolve Along With Your Product
Even if you’re at the earliest stages of a design project, it’s a good idea to lay out your preliminary BOM. This can have you thinking about the BOM earlier in the process, without having to commit to it. Although you’re still figuring out the design and you don’t know precisely what you’ll need for each part, assembly, or material—roughly listing out what you do know will help you in organizing your work.
Just like writing a report or essay, it’s easier to start by creating an outline even though you don’t know yet what each individual sentence will say. Your Bill of Materials is your outline for the product you’re designing. It helps you see what you’re going to need, even if you’re at a stage where you only have a rough idea. As you progress through your work, it evolves along with the product design and becomes more concrete. But by starting from the rough outline, you have a clearer idea of the end result you’re trying to work toward.
Considering the BOM from the outset helps you to consider not only the different components of the design, but the relationship between them all. It can help you organize your design work more effectively. And if you wait until later in the design process to start creating the BOM, it actually ends up taking more effort versus having the BOM evolve along with your product as it’s being developed.
Plan Better by Creating Your eBOM and mBOM Earlier
In many cases, creating your BOMs at the outset of a project is a good way to find out what you don’t know. It’s a way to bring in more stakeholders early on and enable everyone to plan better. Although the mBOM is derived from the eBOM, it’s a smart move to consider both from the get-go.
How something gets put together is a big part of designing it. Creating your eBOM early on is helpful, but when you also start creating your mBOM early in the design process—it causes you to consider the bigger picture such as what work instructions will be required to get to a completed, shippable product. Thinking about your mBOM while you’re still figuring out the design lets you plan the work needed to actually make the thing. Whether it’s planning for manufacturing fixtures and process flows, identifying long lead time items, or planning for in-process inspection activities, building up an mBOM early lets you consider what will be needed to manufacture the product once it’s designed. This allows you to plan proactively around external lead times, capital, and personnel you’ll need for production.
It also helps you avoid mistakes or potential concerns that don’t show up in your CAD. When reviewing a mechanical design, it’s natural for us to focus our attention towards the mechanical components described by CAD geometry. But things that aren’t modeled in CAD can often have just as much potential to become a source of failure, if not more. Whether it’s paint, coolant, lubricant, or another non-geometric aspect of the product, it’s crucial to look at these together with the product geometry in order to develop a successful product.
So when you’re looking at how your organization operates, it’s important to ensure design data is getting reviewed alongside the Bill of Materials. Your BOM is far too critical to be an afterthought in the engineering design process. But when your CAD and your BOM evolve together as your product is developed, it lets every single stakeholder work together better—right from start to finish.
***
Are you evaluating your current engineering processes to see where they can improve? This one-hour webinar focuses on how to update your design review process to take advantage of today’s technology. Learn how you can modernize the way your team works, speed up your review cycles, and catch mistakes before they hit the production floor.