Still “unfreezing” design freezes? There’s a better way.
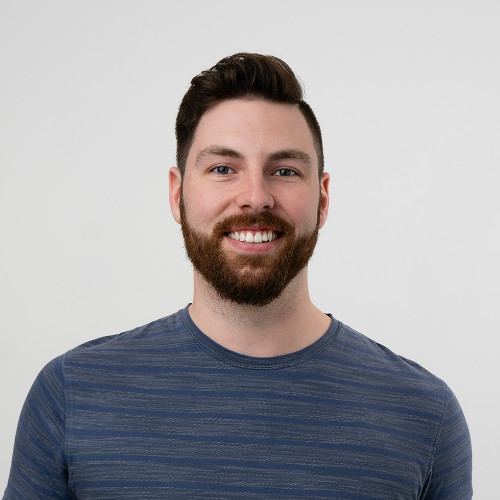
Adam Keating
December 12, 2023
7
min read
Most NPD and sustaining engineering projects endure the dreaded design freeze unfreeze.
After passing multiple stage gates, sitting in on endless design review meetings and building a working final prototype, engineering teams freeze the design for production…
… Only to find a supplier will need new tooling to address the design. Or, the production team wants to adjust a component for manufacturability. Or, your supplier can’t work with a specific material.
So, what happens? Production and supplier challenges force the team to unfreeze the design and move back to square one.
This isn’t just an engineering headache. It’s a massive time and capital expense costing companies months of product design reworks and thousands of dollars in R&D.
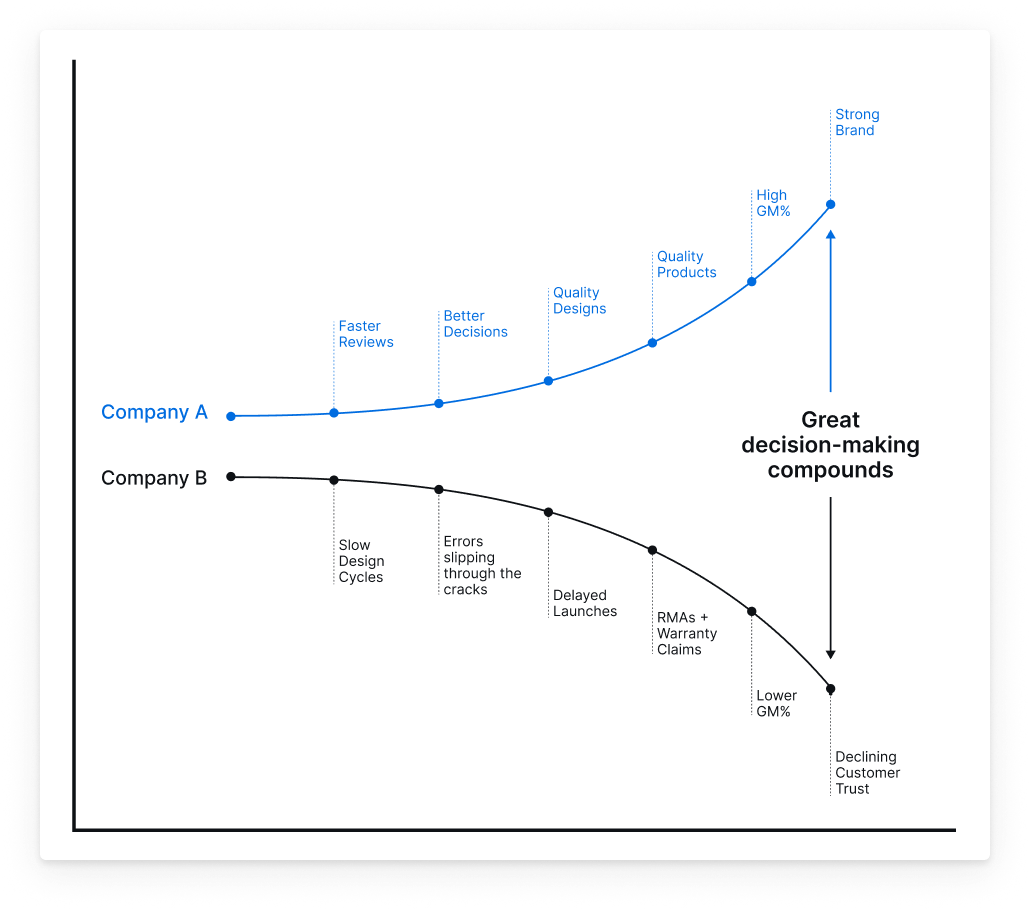
So, what’s the solution? What if, making the design review process - from component engineering to final prototype - simpler and more collaborative could (finally) obsolete the dreaded design freeze unfreeze.
Internal processes are not set-up to encourage collaboration
It’s no wonder that most engineering teams don’t actively involve their suppliers or production team throughout the design review process. That “process” usually looks something like this:
- Take screenshots of all the useful views of a 3D model and paste them into Powerpoint, so that you and the supplier can mark it up
- Send as attachment via email
- Wait for mark-ups from suppliers, internal team members and (sometimes) leadership
- Consolidate mark-ups back into the original CAD file
- Make a new Powerpoint, with new screenshots…
Or, worse, they involve major stakeholders in an hours-long meeting, where one engineer gets stuck making manual notes. And most of the true iteration is lost.
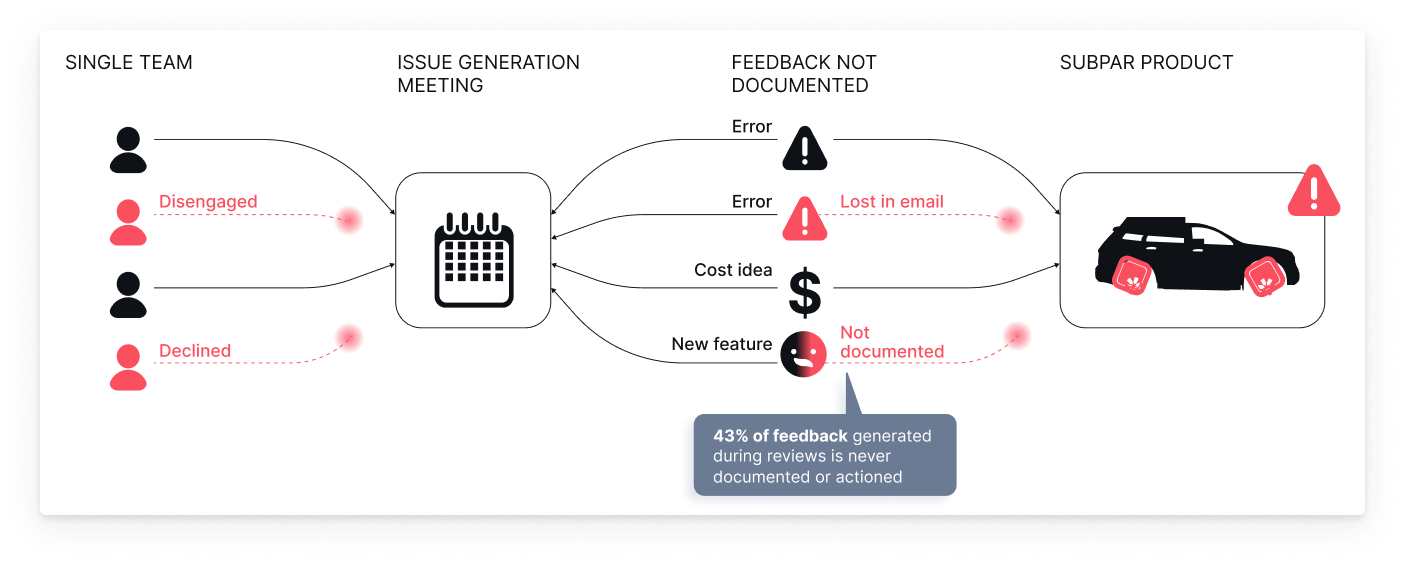
When you look at the cost of product development, you know any change you make early is going to save a ton of time and money. But we still wait until the very end, when making a change is more difficult. I felt this pain acutely while a member of an NPD engineering team.
So what happens is: you get a pack of drawings and the first time a supplier sees them is at the 11th hour and all of a sudden, there’s a breaking change.
Or worse, you get through the final prototype gate, it gets approved, and then it comes back that there’s a problem. Now you’re going back to a design that’s ‘frozen’ and having to make changes.
When I was asked during a recent panel talk why this happens, my answer was simple: Because it’s not easy.
It’s not easy for engineers to look at the same model. It’s not easy to share the same BOM across suppliers. The rate of change during development is so high, that there isn’t a good way to collaborate between engineering team members and suppliers in a simultaneous, asynchronous way.
So, what happens? You get nothing upfront and everything at the end.
Internal software systems make collaboration impossible
Aside from the broken internal processes, internal software systems are not equipped to handle engineering, supplier and production collaboration.
If we look at the product development process through a software lens, we see three major “systems” in use: CAD, DES and PLM.
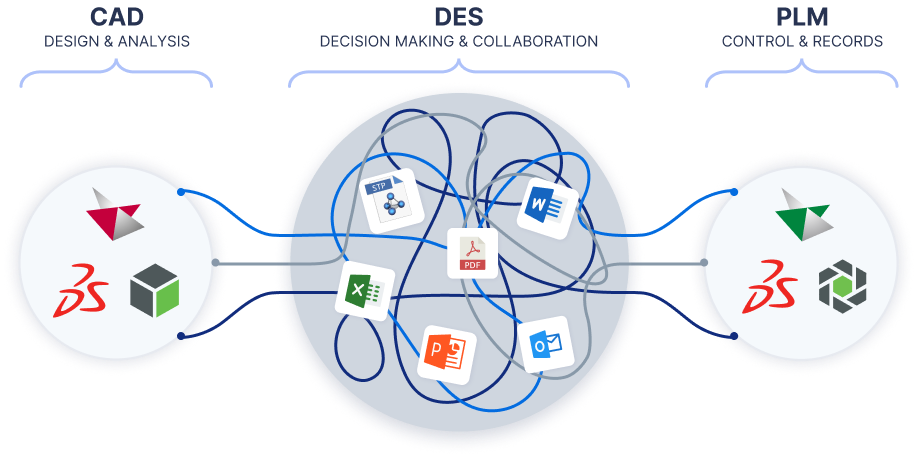
CAD
For initial conceptual design and analysis, engineers use CAD. And it works. During the typical stage gate process, CAD makes the most sense in the early stages. Engineers interface with a specialized tool for product design and analysis.
At this early stage, there are also fewer team members involved and the process is engineering-heavy. Therefore, CAD makes the most sense as the software system of choice.
As conceptual designs get more and more refined and the product passes key gates, it’s time to move to component engineering, system engineering, and prototyping. This is also where design reviews and collaboration across teams becomes more critical. With more stakeholders involved in the product development process, the software needs evolve beyond CAD only.
DES
DES stands for Design Engagement System. If we look at CAD based on how and where it’s leveraged in the stage gate process, model creation starts in the early stages and the CAD evolves as the design evolves. DES is leveraged in the critical middle stages where collaboration among engineering teams, suppliers and production teams is most critical.
You can use a DES to evolve a design using feedback from key stakeholders. Once an engineer creates a first CAD design revision, they need feedback from SMEs to improve that design.
A Design Engagement system like CoLab is purpose-built to let SMEs review CAD and provide feedback. Teams that don't use a dedicated DES system, typically use a mix of other tools like:
- PowerPoint
- Excel
- Word
- Notebooks
Rather than using a dedicated DES, most teams are using the above mix to perform critical design reviews.
As a result, product development teams experience the following design review headaches:
- Teams are forced to rely on meetings to generate feedback because sharing CAD files is too difficult.
- The alternative to a meeting is building a Powerpoint with screenshots, which is admin intensive and occasionally fails to communicate design intent.
- When a meeting does occur, documenting the feedback from that meeting is admin intensive: you need the Powerpoint or you use a spreadsheet and lose all the visual context of the 3D model.
Because the design review process is so painful, we're relying on people to brute force product development. When people inevitably start to burn out, issues and errors slip through the cracks. Either because they were not properly documented and tracked (43% of feedback gets lost, according to a survey of 250 engineering leaders). Or because the right SMEs were never engaged to provide their feedback in the first place.
It’s no leap, therefore, to conclude that poor DES substitutes cost companies years of product development time and up to millions of dollars. It’s also no surprise when a design freeze is unfrozen ahead of production. With so much feedback lost, quality issues slip through the cracks, too.
Instead, a properly implemented DES encourages rapid, iterative and asynchronous design well ahead of a design freeze. To accomplish this effectively, companies properly using a DES also include essential product development stakeholders, like suppliers and production well ahead of key gates (including the design freeze gate).
In the end, it’s a DES that prevents design freeze unfreezes.
PLM
PLM systems are a vital cornerstone for engineering and manufacturing teams, particularly within large-scale enterprises.
Companies revere PLM systems for their ability to house official documents, manage various workflows, and safeguard access to vital information.
However, PLMs are rigid - as they should be. But, they are too rigid for middle stage gate steps when processes and reviews are more fluid. PLM instead should fall much later in the product development process.
In fact, in a recent survey of 250 engineering leaders, 71% report they do not use their PLM for product development. Despite 100% of survey respondents having a PLM or PDM in place.
Unfortunately, many companies still think they can replace a DES with a PLM in the critical middle stage gate steps.
Research conducted by Valery Merminod and Eric Blanco at the International Product Development Management Conference sheds light on the issue, concluding that PLM excels in project management but falls short in daily collaboration, especially during preliminary design.
So, what's the root cause of this limitation?
It's anchored in PLM's fundamental structure. PLM software's strength lies in creating standardized workflows, but this can become a weakness when the design process needs to be more fluid. As a result, PLM tends to become inflexible and difficult to use daily.
The early design stages require rapid changes, and the tools supporting this process must be just as agile. A post from WhichPLM explains this drawback, noting that the "restrictive nature of the underlying structure" means designs often don't enter a PLM system until nearly complete. This creates extra burdens for design teams and hinders early collaboration.
All this to say: when it comes to the product development process, using the right tools for the job at hand helps teams avoid costly mistakes, like unfreezing late stage design freezes.
A DES environment as the solution to unfreezing late stage design freezes
It’s easier said than done to simply retool your stage gate process by replacing what you have now with a system for collaborative feedback and iteration during the middle stage gate steps.
But it’s critical for teams experiencing frequent design freeze unfreezing in their NPD processes.
Like eliminating waste in a lean manufacturing facility, teams can replace their antiquated multi-step processes with a DES where this is possible.
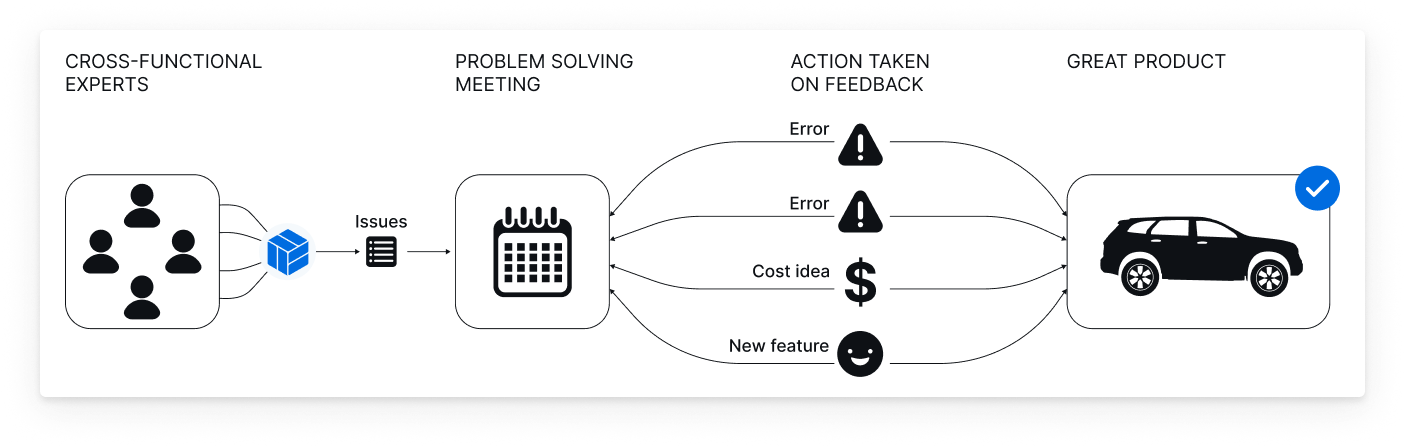
As a DES designed to work with your PLM and CAD systems, CoLab makes it easy for SMEs to provide useful design feedback and automate all documentation and tracking.
Moreover, aside from eliminating, or at least reducing, design freeze unfreezes, a dedicated DES can solve other symptoms of poorly adopted systems and processes.
- Promote collaboration between teams and people in complex environments. The world is different today. In-person design review meetings, manual mark-ups and on-prem software are relics of antiquated product development processes. Engineering teams have adequately addressed challenges like conceptual design and analysis with CAD. And, controls and data housing with PLM. But the way engineering teams collaborate during the design process needs to evolve with how humans interact and collaborate online today.
- Bring risk forward. Everyone wants to catch preventable mistakes earlier in the stage gate process, but few companies actually avoid late stage design changes. Much of the collaborative design review process happens too late. Production teams aren’t consulted until the final prototype. And suppliers have only a few opportunities in the stage gate process to add real value. But with a DES, companies can move much of the risk associated with design changes forward into the middle product development stages.
- Reduce expensive design changes. Often because production teams or suppliers aren’t brought on until later in the stage gate process, they find expensive errors too late in the design review. This means the engineering team is forced to unfreeze the design and move back to an earlier stage.
- Remove administrative barriers within the review process. Yes, design reviews should be thorough and intense. But the administrative burden of it can be drastically reduced. You can intelligently automate non-value added work (like documenting and tracking feedback), so your team can focus on the value added aspects of a design review.
We’re not saying the transition to a DES will be easy. We’re saying the most forward-thinking companies today are moving to DES environments as their preferred method for design reviews. See for yourself.