Pros & Cons of Using SharePoint for Your Engineering Design Processes
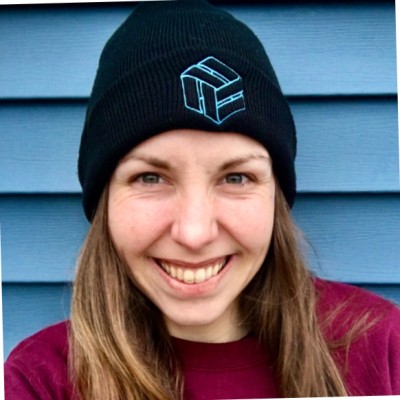
Meagan Campbell
August 5, 2021
7
min read
SharePoint has been around for a couple of decades now. As the onset of the Covid-19 pandemic drove higher usage for Microsoft Teams, SharePoint grew along with it. With over 200 million monthly active users, plenty of teams are using the platform to store and share files across different industries.
But how well does SharePoint fit into engineering design processes?
Gartner classifies SharePoint as a content services platform for functions like document management and other content-focused services. Microsoft describes it as “a secure place to store, organize, share, and access information” and a way for organizations to create websites for their team. Basically, it’s a place to put files and folders where they can be shared with others.
While SharePoint can work well as a generic content management system, it’s not purpose-built for engineering teams to collaborate on complex design projects. In the short term, SharePoint was a fast way to get a solution in place for organizations that needed to quickly shift to remote work in 2020. But looking ahead, engineering leaders are already evaluating the sustainability and scalability of general-purpose tools like SharePoint.
This post explores some of the pros and cons of having SharePoint as part of your engineering design processes.
The Pros
If your design workflows already heavily involve Word documents, Excel sheets, and/or PowerPoint decks, using another Microsoft product for file storage and sharing does make sense. Although SharePoint is less-suited to storing and managing CAD files, it does have the versatility to accept a range of file types beyond Microsoft formats alone. For sharing outside your organization or outside a technical team, widespread familiarity with Microsoft products means SharePoint links can be sent to anyone without worrying if they have a particular software licence or technical knowledge.
Here are three benefits of using SharePoint within your mechanical design processes:
1. A single location for files
One reason teams use SharePoint is that it creates a single location where multiple people can add and view files. Unlike a shared network drive that’s tied to a physical location (office), anyone can access SharePoint from their web browser without needing to be in a particular place. This enables internal teams to continue to work together even while working remotely, as well as making it easier for external partners to get access to the latest documents.
Folders can be set up and organized however it makes sense for your team(s) and workflows. With SharePoint, there’s less need for documents to be saved to personal harddrives or sent as email attachments. For a given project or customer, all the relevant documents can be kept together in a SharePoint folder and accessible from anywhere.
2. Simple file sharing
SharePoint can be configured with different permissions and access based on your needs. Files can be shared across a specific team, across your entire organization, or externally. From within SharePoint, all it takes is clicking “Copy Link” to generate a URL that can be pasted into an email or a direct message.
Because the options for sharing externally with SharePoint are so flexible, it’s important to consider the structure for sites and folders within the platform. That way, you are only giving external users access to the information you want them to be able to see and access—and not the information you don’t. It’s also easy to toggle between “Edit” access and “View” access, depending whether you want to allow someone to make changes to the document or not.
3. Usable by anyone
As a Microsoft application, SharePoint makes it easier to share designs with a wide range of people. Internally, there may be non-technical colleagues outside the design team that need to be able to give input on a project. Externally, there are a number of stakeholders who need to be able to review the design but may or may not have the same technical background as your team.
SharePoint offers a way to share design information without requiring specific technical knowledge to open the file. It also provides a workaround way to share designs without the receiver having a CAD seat or access to a particular type of licensed software. Although it may require exporting a design file to a neutral format, the fact that essentially anyone can use SharePoint is one of the platform’s advantages.
The Cons
SharePoint may have millions of users worldwide, but the platform wasn’t made for mechanical design work. While some organizations have incorporated it into their engineering design processes—potentially as a stopgap solution versus a truly strategic decision—it doesn’t take long for a busy team to run into shortcomings. The more people get involved, and the more complex the design work gets, the harder it becomes for SharePoint to be an effective part of your team’s workflow.
Here are three downsides when using SharePoint within your mechanical design processes:
1. Clutter-prone
Let’s face it: it doesn’t take much for SharePoint to become a disorganized mess. Having a strong and clear process in place for how your team and/or organization uses the platform is a big help, but it can require a great deal of time and effort to keep a SharePoint site clean, orderly, and efficient to navigate. Not to mention, as a catch-all for so many different files, storage limits can quickly become… well… limiting.
The search function is helpful when you know what you’re looking for and what search terms will bring up the right file without returning 100s of results—but it’s easy for crucial information in SharePoint to get missed. There’s also no way to prevent multiple copies of the same slide deck or PDF from being uploaded or scattered across different folders. While the link-based sharing can help reduce the risk of working from an out-of-date file, it’s not always easy to get a clear picture of a project’s history when there are multiples of the same document in SharePoint.
2. Made for storage, not productive collaboration
There’s a reason Gartner categorizes SharePoint as a content services platform. As a document management tool, it’s ideally suited for storing files. While Microsoft does describe the app as a way for teams to collaborate, it’s not actually built to make engineering collaboration more productive.
Sharing files might be easier using SharePoint, but collaborating on mechanical design goes far beyond multiple people working on the same Word document. It’s up to the engineering team to develop, define, and manage how SharePoint fits into their processes such as how feedback is given, received, and tracked. There’s still a significant amount of manual admin work involved that SharePoint doesn’t take care of, and there’s no way for team leads or managers to maintain oversight.
3. Not created with CAD in mind
Just like SharePoint was created for content management rather than for productive collaboration, it was created primarily for certain types of content—and not for CAD files or engineering design work. It’s clunky, time-consuming, and often difficult to try to communicate design intent and share information about a 3D model using SharePoint. The opportunity costs and productivity loss add up quickly when engineers are stuck taking screenshots of a 3D model from various angles, pasting them into a PowerPoint, sharing over email or Teams, and then pulling together feedback from comments scattered throughout the slide deck.
While putting in the time and energy to develop and define a robust process around SharePoint can definitely improve its effectiveness, the platform is ultimately a generic tool. It’s not industry-specific. It’s not purpose-built for engineers. It’s just a simple, cookie-cutter application that can be used by any team for practically anything. And although there are pros to that fact, as mentioned above, it’s also a con for teams trying to move fast and deliver on complex design projects. SharePoint simply isn’t built for that.