How to Infuse Supply Chain Optimization into Your VA/VE Strategy
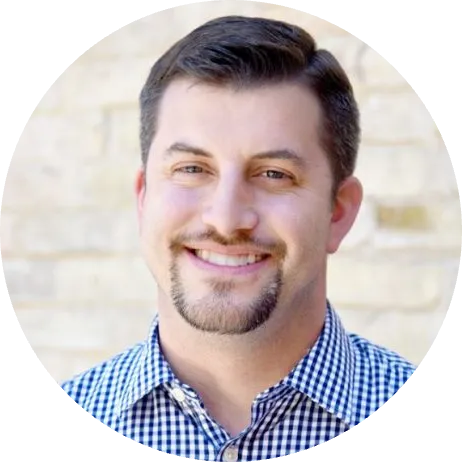
Adam Kimmel
October 21, 2022
4
min read
Supply Chain has been an important theme in our daily lives since the pandemic's beginning and still presents significant hurdles today. It is all about flow: the process takes raw materials, moves and converts them several times, and produces an accessible finished good for the end user or consumer.
While the concept is simple, a break in just one of the many links in the chain can disrupt the entire process. As a result, we've learned to prioritize resiliency to avoid supply disruption, which often adds inefficiency and inventory cost, which hurts, especially during unyielding inflation. So how can you increase your ability to fulfill customer orders without destroying profitability?
Enter value analysis (VA) and value engineering (VE).
VA/VE should be less a lever to pull when you need to improve profitability and more a strategic mindset shift in the approach to extracting the most value from a product's total cost of ownership (TCO). Given that emphasis, VA/VE principles are ideal tools to unlock profit while optimizing the supply chain.
VA/VE process overview
VA/VE methodology seeks to increase the value ratio of a component or process by increasing function, decreasing cost, or both. The concepts differ because VE targets an initial [pre-launch] product, and VA assesses a commercialized product for optimization. After selecting the product to optimize, the cost Pareto uncovers primary focus areas, not just in the product itself, but its manufacturing process.
The VA/VE project team can extend their assessment to add the total cost of ownership (TCO) across the entire supply chain to the manufacturing process and product design analyses to find areas to remove waste. These factors are additive to the cost savings potential, but team members must consider potential interdependencies or conflicts between procurement, manufacturing, and design before proposing a cost savings idea.
Examples of VA/VE in supply chain
Material procurement
Procurement is a broad discipline and has several levers for value optimization. One area is purchasing terms, where negotiating reduced supplier lead times can increase throughput. This action shifts the limiting step to another part of the supply chain. In addition to receiving material faster, reducing obsolete inventory can reduce the warehousing overhead cost inherent in every piece.
Resiliency is essential to reducing process waste, so creating automatic reorder thresholds at desired inventory levels can reduce the risk of a force majeure. Another necessary step to de-risk supply is building a dual-source supply strategy for every component. While volume levels help reduce piece-part costs, relying on one supplier reduces your leverage and puts you at the mercy of your supplier's resiliency strategy.
A final procurement strategy is monitoring your SKUs and product mix. Applying the Pareto (80/20) thinking, looking at the cost, complexity, and ROI at the SKU level can uncover ideas for optimizing material purchases. Is there an aspect of lower-profit SKUs that should influence material buying? This evaluation can also influence product development.
Manufacturing
A critical component of a VA/VE project is the manufacturing process go-and-see, where the project team observes the manufacturing process. But before diving into the process, the team should analyze setup and changeover time, in addition to the capital situation. Setup and changeover are non-value add steps, so organizing multiple-component runs on the same asset to reduce setup and minimize changes can increase daily throughput.
Another opportunity for VA/VE in the supply chain is capital expenditure, often a considerable investment. The team can look at depreciation schedules and expected replacement timing to tie product design changes to the new equipment. Considering capital during VA/VE improves the ROI of a VA/VE idea substantially and helps the business know when to execute the change.
Finally, observing the manufacturing process itself may uncover opportunities. Any operator movement outside of the direct task at a station is waste. The process should flow smoothly from the intake of one step to its output with minimal wasted movements.
Tools to integrate VA/VE thinking in supply chain
Supply chain visualization/map – visual aid showing how the parts travel through the process. Assessment questions can include:
- Does a component cross the ocean multiple times?
- Does a globally-centered or regional supply strategy make more sense?
- Can the procurement team leverage component pricing for one element to improve another?
CoLab – advanced software for VA/VE engineering-led design. This step enhances collaboration to accelerate value-engineered solutions that feed your supply chain strategy.
.webp)
Cost Pareto – cost waterfall to illustrate where cost components are highest and which aren't worth pursuing.
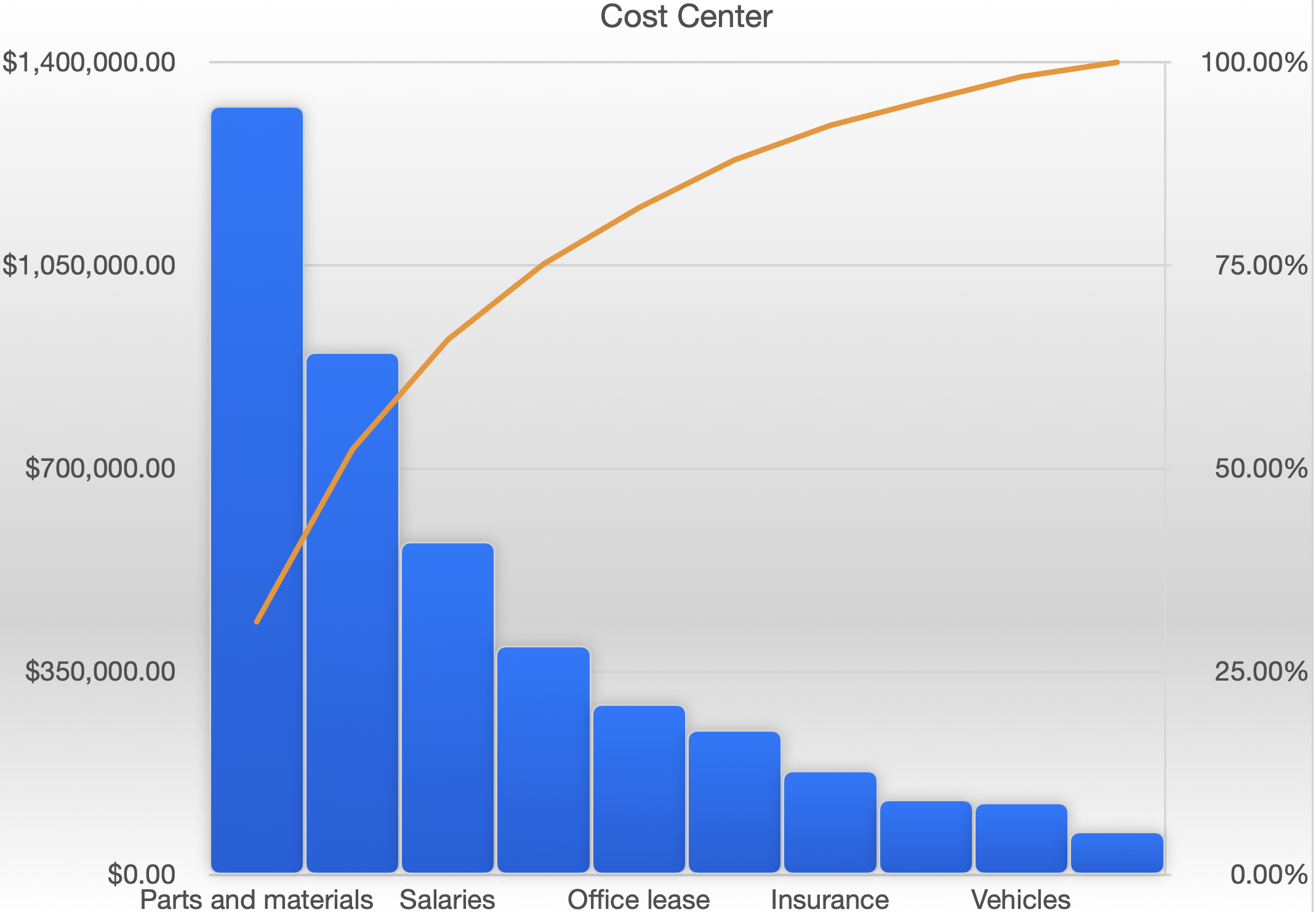
Process observation – watching part manufacturing may show an apparent headache hindering efficiency. Points to consider:
- Is batch, just-in-time, or a combination ideal for the process (and how is the part manufactured today)?
- Can manual steps be automated, repurposing skilled labor to more complex tasks?
- Could the team eliminate a process step with different technology or integrate product features into fewer components?
- Does the packaging appear overdesigned, or can the team recommend integrating or reducing packaging components?
Takeaway
An efficient supply chain is integral to producing the components consumers and businesses use every day. Supply chain optimization presents a significant opportunity for VA/VE with how complex many components are to make.