How to improve supplier relationships with stronger technical reviews
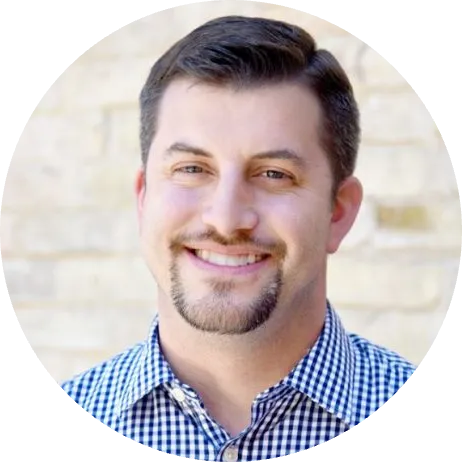
Adam Kimmel
February 13, 2023
4
min read
If the last three years have taught complex manufacturers anything, it's this: you are only as good as your supply base.
When we rely on someone else for support, they hugely impact the success of a product launch. If only one component isn't right, the entire timeline to launch can be affected. Or worse, product quality issues can crop up, causing product rework and damage to brand equity.
Supplier relationships carry natural friction points driven by commercial activities. These include multiple suppliers or combining products with other business units to improve negotiation leverage. Other procurement-driven tactics include pre-buying bulk raw materials at a favorable price to lock in pricing (hedging) and to require cost-reduction ideas or annual credits as part of supply agreements.
So, as important as the supply base is, how can you bulletproof the material supply in the face of the friction points? Maintaining a solid technical relationship is one of the best ways. Often, strong customer-supplier relationships can even repair bridges seared during commercial negotiation. One of the best ways to build strong supplier relationships is through a supplier technical review, setting both sides up for success.
What is a supplier technical review?
Supplier technical reviews are formal, structured technical meetings between the design and process teams specifying the part and the manufacturer that produces it. Technical reviews (also called design reviews) are a subset of supplier evaluations, which include:
- Production capacity
- Financial health
- Delivery timing
- Customer service
- Environmental impact
- Performance
- Product quality
Those last two are what the technical review aims to deliver.
At a minimum, participants in the tech review should be a representative from each area of the business that the product affects. Ideally, they should have decision rights to approve or reject a recommended change. At least, they should offer tradeoffs to decisions and can carry a design change back to their group for the final decision.
The team is made up of members of the customer design team, like engineers and CAD designers, along with quality assurance, project leads, subject matter experts, product marketing, and operations. Supplier manufacturing, processes, and other stakeholders participate as well. Design and quality functions are obvious, but product marketing is an under-appreciated group to have in the room.
Marketing owns the customer (or consumer) experience and look of the product. A product representative can share why features that do not affect a part's fit, form, or function are critical to the design.
Just imagine if someone proposed changing the shape of the Nike swoosh to simplify tooling, and product marketing didn't get to weigh in.
Why perform a technical review?
There are many reasons to perform technical reviews – some proactive and some reactive. Both types are valuable to an effective product.
Proactive outcomes
Alternate manufacturing approaches – reviewing across multiple functions allows team members who didn't participate in the design actively to consider other ways to manufacture it. They can consider tolerance requirements, flow paths for material, and estimated production volume to think through other manufacturing techniques that may be better suited.
Product quality – looking at the design from different perspectives before making prototypes can catch opportunities to make the part easier to manufacture, increasing efficiency and quality. The construction may be technically acceptable, but it could cause headaches for the builder.
Complying with standards – team members have different experience levels with standards. Reviewing the design with a group of experts in other functions allows the design team to use their knowledge to compare the design against a standard.
"Extra" innovation – anytime experts come together, innovation can occur. Technical reviews are a rich source of creative ideas from team members able to apply them to the design.
Reactive outcomes
Identify and correct design defects – more eyes equal more checks. CAD models may allow features in the model that are not technically possible, such as line-on-line fit or one component passing through another. CAD has some built-in checks, but there is no substitute for human review.
Risk management – the team member naturally considers risks from each area – it's their problem if something goes wrong. The design team thinks through hurdles during the process but will not likely catch every one, especially for areas they don't know as well.
Better product confidence – the technical review is the first time people look at the design critically. Looking at the documentation, CAD, and drawings let you see how others interpret the design. Is it clear? Can the design absorb drawbacks from a manufacturing process? You'll know these answers much better after the review.
Can the supplier comprehend and translate the design package into a finished component or assembly? The design is the technical contract between the customer and supplier to define the rules of the game to ensure both sides win.
Technical review process
During the review, team members play lead and support roles based on the activity. These reviews can use many tools and formats, with the most effective improving collaboration between team members.
ISO 9001 directs the design review to follow these basic steps:
- Present design: design team (LEAD) presents design details to the reviewers. The best practice is for the lead designer to send information ahead of time so the group can prepare. The lead designer or engineer drives the process and is the single point of contact.
- Feedback: the multi-function team (SUPPORT) provides feedback according to their area(s) of expertise. The input can be in the proactive or reactive categories described above, on specific low-level design features or high-level process or design intent.
- Collect and rank feedback: the design team orders the input based on several factors, including how easily the changes are to include, how critical they are to primary design function and safety, and how they affect cost and timing for production.
- Research and evaluate opportunities: at least some recommended changes usually require follow-up research. The design team actions this work, learns what it will take to include, and frames the change's details.
- Report findings: the design team presents their findings and recommendations to the review team for alignment.
- Include or reject change: the review team decides whether to include or ignore the change opportunities based on the design team's proposal.
- Final approval: once all changes are worked through, the review team agrees to freeze the design and release it for manufacturing. A technical stakeholder owns decision rights for final design approval.
What questions should the technical review answer?
Effective design reviews answer a range of guiding questions to ensure the design team has thoroughly thought through the details.
These include:
- Does the design meet the specification and customer requirements?
- What are the known risks of the design? Is there any historical knowledge that can indicate the significance of the threats?
- Are there deal-breaking flaws that must be changed?
- What are the materials of the construction and manufacturing approach, and do the design tolerances fit that strategy?
- Can the design and manufacturing process meet the production volume and project timeline?
- Is any part of the design subject to IP or trade secret constraints?
Conclusion
Effective technical supplier relationships are vital to the success of contract manufacturing. Designs are becoming more and more complex, so using a supplier technical review can address many pitfalls of the part geometry before any cutting any material.
Supporting the design team with experts like subject matter specialists, quality engineers, supplier manufacturers, product marketers, and operations leads can add decades of expertise to a product design. Effective design reviews add this knowledge efficiently during the assessment for manufacture, with enough time and support for the design team to include the reviewers' feedback and include it in the design.
Effective collaboration is essential to this process. And while design reviews usually happen in person, they are occurring more and more virtually to include global and remote team members. This asynchronous method reduces in-person meetings and allows any relevant expert – anywhere, any time – to collaborate in the technical review.
Technology can enable virtual collaboration. The most effective equipment gives the team the feel of an in-person meeting with the flexibility of an independent, efficient process…almost like the technology isn't there at all.