How to Improve Automotive Profitability Through VA/VE
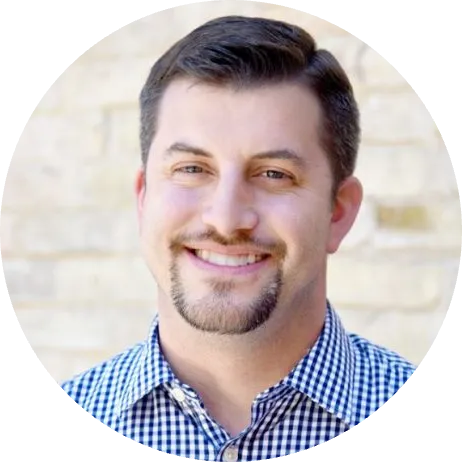
Adam Kimmel
November 1, 2022
4
min read
The automotive industry is notoriously competitive. Cars are one of the most significant expenses in consumers’ budgets, and price is often at the forefront of a buying decision. And while OEMs have shifted the competition from pure engineering capabilities to technology-fueled user experience (UX), their customers are unwilling to pay a monthly subscription fee for the added features.
The challenge for car makers then becomes: how can they deliver improved UX at the cost the consumers have grown accustomed to paying?
Value analysis (VA) and value engineering (VE) are two powerful tools to generate funding for UX. Adopting a VA/VE mindset is an ideal fit for automotive OEMs for two primary reasons:
- Car manufacturers have outstanding engineering horsepower already in place
- They produce capitalized volumes at a scale that delivers massive savings for a small design change
The following sections outline some areas automotive OEMs can leverage the power of VA/VE to improve their offer to consumers in a highly competitive—and dynamic—landscape.
VA or VE?
While design engineers often combine the terms (VA/VE), the subtle difference between VA and VE is the lifecycle phase during which the team targets redesign. VE occurs during the initial design, and VA comes in following the commercial launch. For context, VA may target the closure of an existing aftermarket oil recharge, while VE may look to integrate plastic components of a center console of a new design pre-launch.
VA and VE focus not on cost savings alone but on increasing the value ratio of a component or process by increasing function, decreasing cost, or both. A cost waterfall (Pareto) chart helps prioritize the effort to maximize the ROI of a design change. This assessment is especially critical for design changes requiring capital outlay. In addition, VA/VE considers the entire value chain, from product design through manufacturing and supply chain.
Automotive supply chain and VA/VE
Although an OEM’s headquarters are in one country, components or assemblies occur around the globe to realize the lowest-possible total cost of ownership for the consumer. The challenge with this approach is the continuously-changing landscape of global supply. The design or procurement team often decides where to source a component and does not revisit it for several years. Another common occurrence is for an initial design to undergo a recall and patchwork design fix without integrating the function into the design to optimize its cost profile.
As technology and electrification permeate the automotive space, several areas are ripe for VA/VE analysis.
Material selection and sourcing
In addition to a popular approach, Procurement teams take to increase purchasing terms and decrease supplier lead times, changes in the composition of cars create opportunities for optimized material sourcing. For example, some automakers are securing agreements for EV battery lithium supply, creating market advantages in both pricing and availability in the event of unplanned disruption.
Some additional options for VA/VE material sourcing optimization include material selection. Some questions:
- Are all metal components the same grade of steel or aluminum (or could the components align to the same grade) for a volume- or supply-based pricing advantage?
- Are any components overdesigned based on performance prediction validation or safety data? Often initial designs include a safety margin in material selection that may be design-optimized following the collection of real-world data
- Are there metal components [that do not deliver safety enhancements] that may be redesigned in plastic to reduce weight and cost? Reduced weight is a hidden VA/VE benefit because it requires less fuel or power to propel the vehicle.
Thermal management
There are many thermal management (heat transfer) opportunities in automotive. While this complex problem requires specialized engineering, an OEM’s VA/VE design team has the chops to evaluate it. Electrification has created two new opportunities:
- The battery needs to operate around room temperature (25-35°C) for maximum efficiency and range
- Passenger comfort no longer benefits from the waste heat available from combusting the gasoline
Engineers looking for value improvement can assess the HVAC heat exchanger designs for opportunities to reduce costs based on the load conditions provided by the new operating points. For example, do the heat exchangers need to withstand the same pressure rating? Is the material grade still appropriate for the application, given the lower peak temperatures?
In addition, the ideal thermal management solution would likely integrate battery thermal management and passenger comfort. This integration would avoid the need for two discrete cooling loops and potentially integrate heat exchange functions into fewer components. Finally, routing heat flows around the passengers could add local comfort while providing an opportunity to reduce cabin bulk heat loads (and component size in kind). Local occupant temperature control enhances UX, so this feature could improve function and reduce cost.
Vehicle autonomy
While autonomous driving has not progressed at the rate of electrification, the opportunity for the vehicle to handle removing manual functions provides opportunities for value improvement. For example, the gear shift and parking brake functions may integrate into the control panel. This change could reduce components inside the cabin, enabling increased passenger space while reducing material content.
In addition, once OEMs achieve full autonomy, that state creates a significant opportunity for comprehensive cabin redesign for user experience. By removing mechanical components, designers can reconsider their specifications by comparing the needs of the new application with the cost Pareto.
Tips for your next initiative
The most effective way to conduct VA/VE in a complex, dynamic industry like automotive is to take a holistic view, following the time-tested steps:
- Look at the cost Pareto as the guide for where to place your resources
- Gather market and consumer data to confirm the direction
- Review the manufacturing process, supply chain map, and trends to begin ideating
- Collect capital data to understand realistic opportunities to pair design changes with capital updates
- Consider unique features for the application, such as the increased emphasis on UX that automotive OEMs are pursuing
- Employ a collaboration software like CoLab to enhance the speed and quality of VA/VE efforts
Final thoughts
With any design change effort in automotive, quality and safety are paramount. It is tempting to consider massive changes to realize substantial cost savings, but any change should consider long-term consumer safety and brand equity. Engaging and collaborating with key internal and external stakeholders ensures in the most effective way possible, will deliver a winning project.