How to execute an effective DFM review with your suppliers
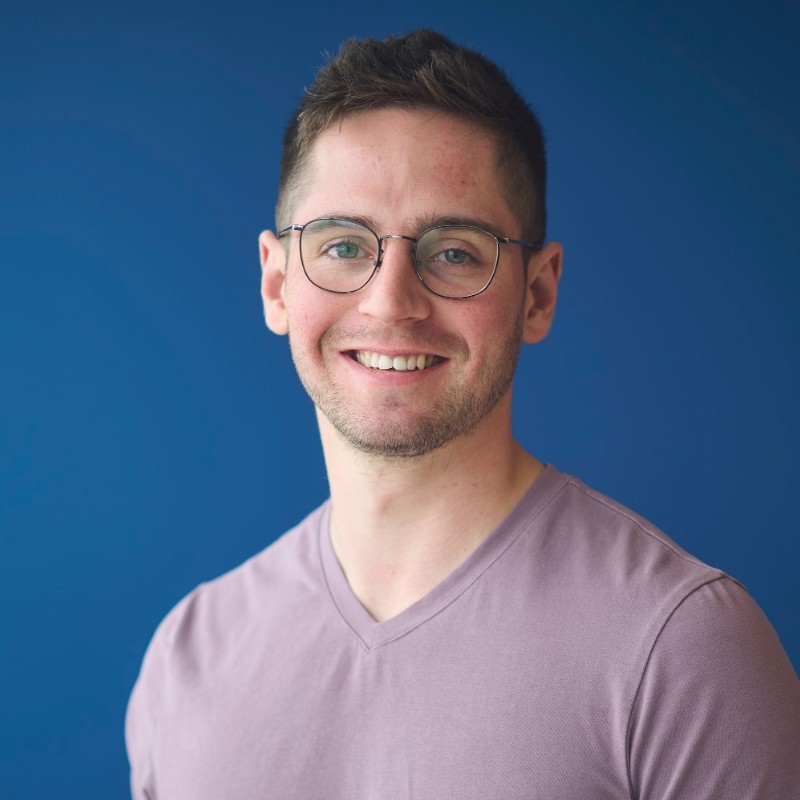
Liam Waghorn
March 21, 2024
2
min read
For most companies, DFM is an afterthought.
Engineers throw the design over the stage gate wall to their suppliers. Then, they find out too late that a part isn’t toolable or the tolerances are too tight on a critical component.
With CoLab, engineers can invite their suppliers into a design review well ahead of a design freeze. Because CoLab lets you share 3D files in a simple interface. That way you can get manufacturability feedback, even from people that don’t have CAD or PLM licenses.
In this video, Liam walks us through a supplier DFM review.
Often, suppliers work with 2D drawings and rarely get access to 3D models.
In this example, we've given them the drawing for this particular part, but also the 3D model. Using CoLab to conduct this DFM review means:
- Your IP stays within your control because you’re not sending files over email.
- You don't have to worry about creating derivative formats like STP files so that the supplier is able to access a model.
- Your supplier doesn’t need a specific CAD or PLM license to access the model. They can access and leave feedback without purchasing their own CoLab license.
Giving your suppliers simultaneous access to the 2D drawing alongside the 3D model means you’re also receiving feedback on tolerances and part codes.
Once the review is complete, you can pass this markup on to the internal engineering team.
The important thing to note here is:
- You sent a file package to your supplier with both 2D drawings and 3D models
- The supplier accessed this without a complicated licensing agreement
- The supplier left feedback for your internal engineering team
- The internal engineering team confirmed the supplier suggestion
- The supplier can now act on this feedback
All in a matter of minutes.
Now, meetings are no longer your only option for DFM. With CoLab, DFM is a continuous process – rather than an afterthought.
How to Run an Effective DFM Review: A Step-by-Step Guide
1. Set Clear Objectives and Criteria
Why It Matters: A well-defined goal keeps the DFM review focused on the aspects of the design that will most influence manufacturability, cost, and quality. Today, most companies throw DFM PowerPoints to suppliers and leave the context to them. This isn’t the fault of the engineering team though. The process for engineers to engage suppliers fails to account for speed and thoroughness.
A better process facilitated by more effective tools can help engineers provide the right context so suppliers can both answer the basic DFM request while also offering expert advice.
How to Do It:
- Identify Top Priorities: Are you aiming to reduce part count, simplify assembly steps, or improve tolerances for high-speed production? Determine what success looks like before the meeting.
- Create a DFM Checklist: Prepare a standardized list of considerations—material compatibility, tool accessibility, draft angles, wall thicknesses, and so forth.
- Set a Timeframe: Keep the session concise. A focused, one-hour DFM review often yields better results than a sprawling half-day meeting.
Key Takeaway: Clarity up front sets the tone. Everyone enters the DFM review knowing exactly what outcomes you’re aiming for.
2. Involve the Right Stakeholders Early
Why It Matters: A DFM review isn’t just for designers and suppliers. The best DFM reviews also involve key internal teams, like buyers and Supplier Development Engineers. By keeping everyone on the same page throughout the DFM review, both internal team members and the supplier benefit from a more collaborative relationship.
How to Do It:
- Include Manufacturing Experts: Operators, toolmakers, and production managers offer practical insights on handling, machine limitations, and cycle times.
- Invite Suppliers to the Table: If working with external partners, their knowledge of tooling constraints, lead times, and cost drivers grounds discussions in real-world capabilities.
- Assign Roles: Decide who leads the session, who provides input, and who approves final changes. Clear roles prevent confusion.
Key Takeaway: Broad, early involvement leads to stronger design solutions and fewer surprises down the line.
3. Use Visuals, Real-Time Markups, and CoLab for Centralized Feedback
Why It Matters: Screenshots and notes can only convey so much. Yet this is often all a supplier has to work with when providing expertise. This makes the relationship between OEM and supplier more transactional than collaborative. By providing access to the most up-to-date data and centralizing all feedback in a single location, OEMs can bring more collaboration to the supplier relationship.
How to Do It with CoLab:
- 3D Models on Display: Share your CAD models through CoLab’s web-based platform. Stakeholders can review and comment directly on the 3D geometry—no file conversions or separate software needed.
- Contextual Feedback: Mark up specific features, propose changes, or flag concerns right on the model. CoLab’s centralized workspace ensures everyone sees these insights immediately.
- Version Control: Automatically track revisions, so all participants know which iteration they’re reviewing. This eliminates confusion and streamlines decision-making.
Key Takeaway: By using CoLab to visualize designs and capture feedback in context, you turn theoretical talk into concrete action steps everyone can follow.
4. Validate Ideas with Quick Feasibility Checks
Why It Matters: When someone suggests a design tweak—thickening a wall or changing a material—you want real-time validation, not a days-long wait for follow-up.
How to Do It:
- In-Meeting Judgement: If the manufacturing lead says a feature might be tricky to machine, consider a quick back-of-the-envelope calculation or a short simulation run to confirm.
- Supplier Insights in Real-Time: Ask suppliers directly through CoLab’s integrated environment: “If we add draft here, can we avoid a secondary operation?” Their immediate input informs next steps.
- Iterate Promptly: Don’t chase perfection in one session. Capture proposed changes and, if needed, schedule a brief follow-up after testing suggested alterations.
Key Takeaway: Rapid validation transforms DFM reviews into dynamic problem-solving sessions rather than drawn-out debates.
5. Document Decisions, Assign Action Items, and Preserve Knowledge
Why It Matters: Great discussions mean little if no one remembers what was agreed upon. Clear documentation ensures follow-through and builds institutional knowledge. Preserving expertise from both the OEM and supplier also builds a robust database for AI use cases later.
How to Do It with CoLab:
- Central Repository: Store all final decisions, annotated screenshots, and related documents directly in CoLab. Everyone knows where to find the latest information.
- Action Tracking: Assign tasks—like confirming tooling compatibility or material tests—to team members within CoLab, setting deadlines and automatically tracking progress.
- Historical Data: Keep these records for future projects. Over time, your DFM best practices become a reference library, accessible whenever you’re tackling a similar engineering challenge.
Key Takeaway: With CoLab’s digital trails and task management, you ensure that nothing slips through the cracks. Past DFM insights become fuel for continuous improvement.