Adapting engineering workflows for global and remote teams
.webp)
Meagan Campbell
May 8, 2023
11
min read
Developing a complex product involves massive amounts of collaboration. For most engineering teams today, that includes collaborating across multiple teams, locations, disciplines, and time zones.
Manufacturing has become global. In fact, it has been “becoming global” for a very long time. Production sites today are often on a different continent than engineering offices, which means working around time zone clashes and potential language barriers.
Then the Covid-19 pandemic accelerated the adoption of remote work for all industries, including engineering teams. In a 2022 report, McKinsey found that more than half of Americans have the opportunity to work from home at least one day a week and more than one-third of Americans have the option to work from home five days a week. That means engineering companies need to be prepared to accommodate increasing employee demands for hybrid and remote work options.
Fortunately, technology is making it easier for companies to adapt to the changing landscape. Primarily enabled by the cloud, new digital solutions are coming from both traditional technology providers (like large CAD/PLM vendors) as well as specialized providers (like CoLab). With the right technology in place, companies can create the infrastructure they need to offer remote work options and collaborate globally.
This article explores the current state of remote and global collaboration for product development teams, and how engineering leaders can effectively navigate the challenges that come with it.
The business impact of remote collaboration
So what’s the big deal? Lots of collaboration is “messy” and difficult. Why would remote collaboration be any different? Why does it matter?
The truth is, challenges with remote collaboration can cause significant delays during new product development (NPD). Legacy design processes and unspecialized communication tools that used to be merely frustrating are now becoming a liability. As more design collaboration happens digitally, teams that cannot or do not adapt their workflows will have a very hard time competing for talent and market share.
Most engineering teams are still grappling with yesterday’s status quo for design collaboration.
Take the example of Jeremy Andrews, mechanical engineer and CoLab’s CTO and co-founder. While working for Tesla on the Model 3 program, Andrews was collaborating closely with a supplier on Design For Manufacturing (DFM) for several plastic injection molded parts. The collaboration process was driven entirely by PowerPoints and emails, sending updated decks back and forth to exchange feedback and revisions. As a result, relatively simple reviews could end up taking weeks to complete.
And if simple parts on a complex mechanical system can take 8+ weeks to review, what’s the impact on time-to-market of this happening across an entire program?
This isn’t a Tesla-specific problem. The way mechanical teams work together is changing, but most teams are still grappling with yesterday’s status quo for design collaboration. That’s why the companies that are fastest to figure out this industry-wide transition will quickly pull ahead of the pack.
An OnShape report asked engineering leaders about causes of delays and challenges with product design collaboration. The two biggest sources of friction were from collaborating with 1) external suppliers and 2) non-CAD stakeholders.
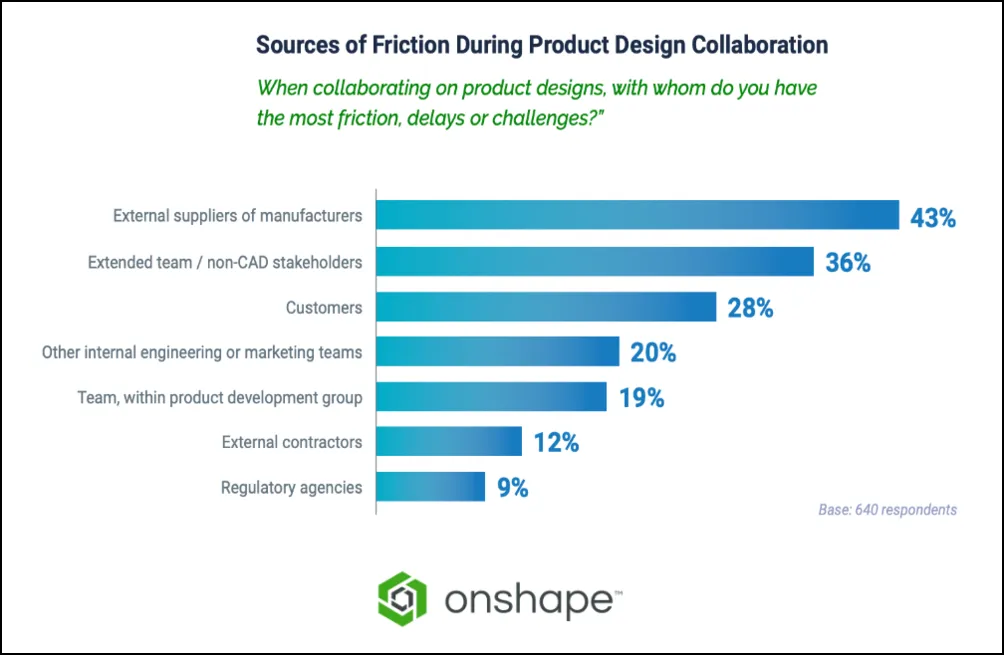
While collaboration challenges aren’t unique to global and distributed teams, those challenges are magnified when collaborating remotely. It’s the canary in the coal mine, so to speak. The upside: when you solve collaboration problems for your remote teams, everyone will benefit.
After all, well-executed collaborative efforts can have a dramatic impact on engineering business results. In a McKinsey report, one consumer goods company had been bleeding market share for years and was determined to get back on track. The company put together a multifunctional team to collaborate with a wide range of stakeholders over the course of a six-week sprint. The team gathered insights, discussed and brainstormed ideas, and then aligned on product redesign choices.
Over just 6 weeks, the results of this focused collaboration included:
- Time-to-market for new products dropped by 40-60%
- Margins improved by 6% in the first six months after the sprint
- Market share was put on track to rise by 8-10% over the course of two years
No matter what metrics you’re focused on, making targeted improvements to your collaborative processes can help you move the dial in a big way. But first, let’s break down what we really mean when we say “collaboration” in an engineering context.
The state of digital workflows for engineering collaboration
Collaboration is becoming a little buzzword-y, in that people frequently refer to it and teams actively strive to improve it. But whenever someone uses the term “collaboration,” especially in the engineering context, it means a slightly different thing each time. So before you can start solving collaboration challenges, it’s important to define and align on what collaboration means for your own team.
CoLab believes that, within an engineering company, collaboration fundamentally breaks down into two core components: sources of truth, and decision-making and communication.
The two core components of engineering collaboration
Source of truth
- Having the up-to-date product data you need to make informed decisions, and with everyone making decisions based on the same dataset.
For example:
- Version control (check in/check out)
- Product data management
- BOM management
- Document management
- Change notifications
Decision-making and communication
- The process of actually making decisions and communicating design intent, ultimately determining the information that feeds back into your sources of truth.
For example:
- Design reviews
- Identifying issues (root causes)
- Complex problem-solving — identifying design solutions
- Conveying or clarifying design intent
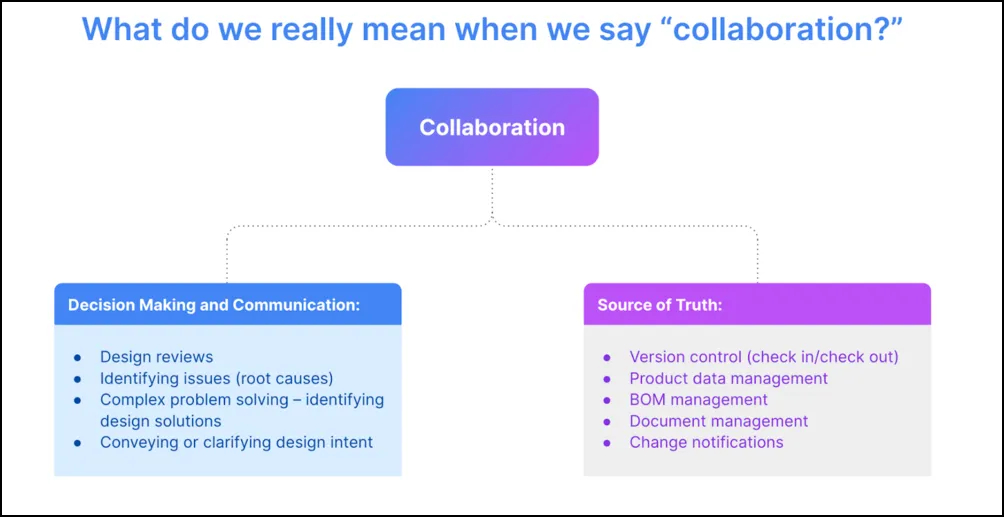
The next digital frontier for engineering teams
Historically, the majority of systems and tools for engineering collaboration have focused on sources of truth. (Think PLM.)
But decision-making and communication are where engineering collaboration truly happens.
Unfortunately, the most common forms of communication lack design context and weren’t built for engineers. Meanwhile, the tools that were built for engineering teams function mainly as a source of truth, but don’t get used for things like design review.
Most communication and decision-making workflows are still overlooked in engineering.
In a 2022 survey of engineering leaders: 89% reported using a PDM/PLM solution, yet only 12% reported actually using their PLM system for conducting design reviews.
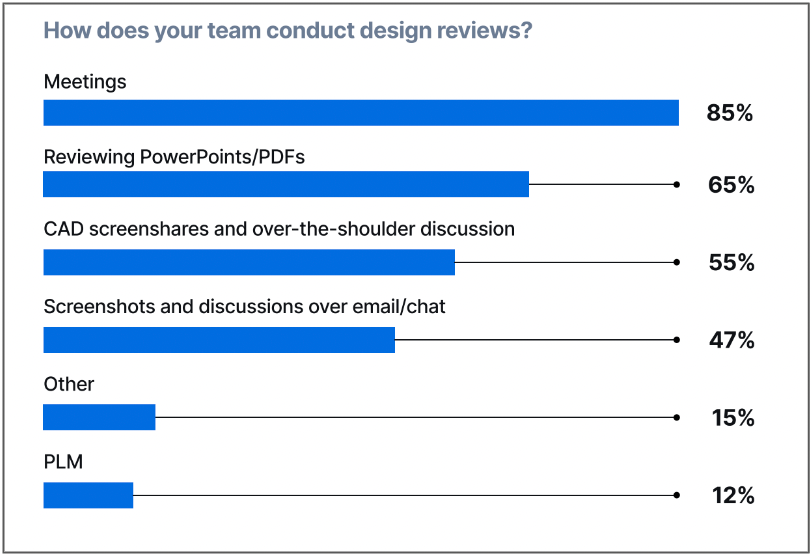
That’s because, while PLM does a great job filling its role as a source of truth, it’s not well-suited for the other aspects of engineering collaboration. So engineering teams have been relying on a range of unspecialized and generic tools to help bridge the gap — stringing collaborative processes together out of piecemeal solutions like email, Teams, Sharepoint, Excel, PowerPoint, Asana, Jira, Adobe, and on and on.
What does this all mean? It means that most communication and decision-making workflows are still overlooked in engineering. There are well-developed solutions for product design and well-developed solutions for product data, but very little that’s been specifically built for product decision-making. While this impacts all teams, the challenges are amplified when there’s global and remote collaboration involved.
So to start optimizing those collaborative workflows in “the messy middle” of the design process, the first step is to clarify precisely what collaboration challenges your team is facing.
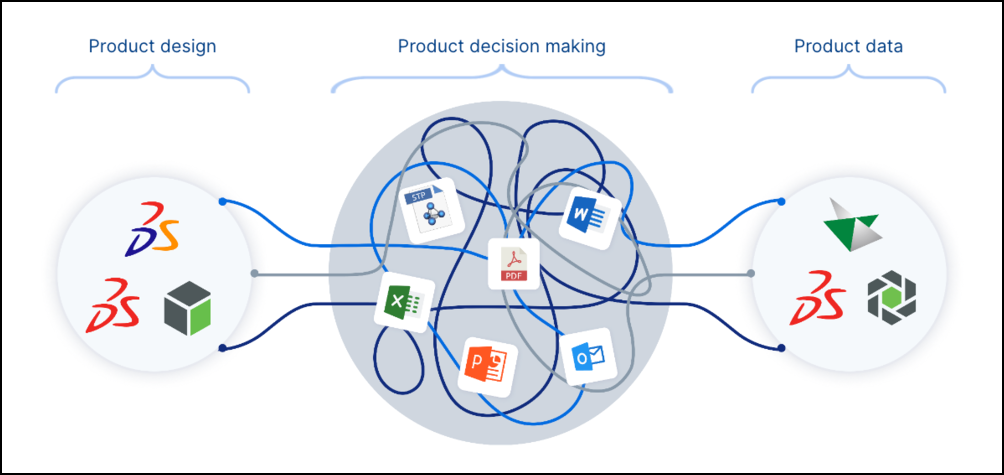
Two core challenges for remote and global teams
Collaboration is a broad term, so it can encompass many different processes and pain points.
But when it comes to the decision-making and communication aspects of engineering collaboration, there are currently two core challenges: access to data, and feedback experience.
Access to data
Historically, the engineering world has resigned itself to a belief that there’s a necessary tradeoff between IP security and efficiency. In other words, it’s become generally accepted that your workflows can either be secure or efficient — just not both. While this was never strictly true, it’s certainly not true with the technology that’s now available in today’s world.
Yet many teams are still held back by the limitations around engineering data, how it’s shared, and what can be accessed by whom:
- Collaborators don’t have access to certain technical data unless they have access to PLM
- Suppliers and manufacturing teams are typically not users within your PLM system
- Non-CAD users must download software to look at technical data
As a result, engineers are spending too many hours on trivial tasks related to sharing files and feedback. Continually re-exporting the latest version and trying to keep suppliers up-to-date. Taking screenshots of 3D CAD for yet another PowerPoint deck. Emailing a file you know you already sent because it’s easier than combing through the clutter again. Even skirting around security procedures in order to “just get it done.”
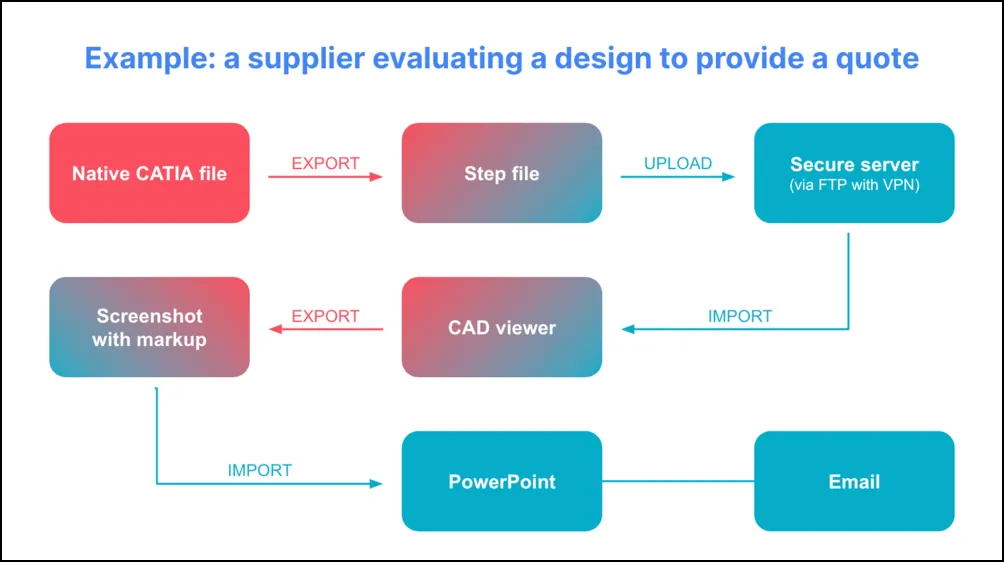
While emailing files back and forth was a pretty revolutionary way to communicate about engineering in the 90s, the time has come for more sophisticated design collaboration methods.
Today’s engineering teams must figure out where and how cloud-based solutions fit into their bigger picture. Securely sharing designs and 3D CAD with any stakeholder, at any point in the design process, needs to get to the point where it’s a seamless process — even when you’re juggling ongoing conversations about multiple parts, with dozens of revisions and collaborators involved.
Without that foundation in place, you’ll always have a built-in bottleneck that slows down any collaboration.
Feedback experience
Access to data is one challenge, but engineering collaboration goes beyond just sharing files.
While the design data itself is necessary for collaboration, it’s not sufficient on its own. To get the input and expertise you need from collaborators, you need to provide the right information in the right context. How will each collaborator interact with the model? What do they need to know? How will they communicate feedback to you?
Exchanging design feedback back and forth is often not a smooth process. For most teams today, it still feels like endless loops of meetings and messages. That’s why it’s so important to consider the feedback experience you’re creating for collaborators, and how you can improve it. Streamlining the feedback process is the best way to make the most of all the collective expertise available to you. By making design reviews frictionless, you’ll also make them more engaging and even fun.
But when there’s too much friction involved in figuring out how to efficiently provide feedback, it raises the cognitive load required to complete the task. That makes it harder to leave high-quality feedback, so you end up with generic “looks good” comments instead of thoughtful input. That can lead not only to missed mistakes, but also missed opportunities for innovation.
In other words: if you don’t make it easy for people to give meaningful and in-depth design feedback, you’re unlikely to get it.
Conclusion
So how can we solve for the challenges of remote and global engineering collaboration?
PLM software has been well-established as the system of record for product data. What teams need now is a system of engagement for product decision-making. That’s why CoLab is the world’s first design engagement system, built specifically for engineering teams that develop complex products and want to move faster while catching more mistakes.
CoLab addresses the issues engineering teams face with data access and feedback experience in several ways:
- Simple, secure sharing: Push drawings or models to CoLab, set the appropriate permissions, and invite any collaborator to open and view files right within their web browser. Whether you need to create a package of files for review, get quick input from a non-CAD user, or do a technical deep-dive on a design issue — CoLab makes it easy to share the right data with the right people, all from one central hub.
- Feedback in context: CoLab lets you pin issues and comments directly on any 2D or 3D file, which means feedback is always linked to the full mechanical context of the design. You can flip back through past revisions and feedback, and you can see other reviewers’ feedback populate in real-time — which means the historical context is always right there at your fingertips, too.
- Automatic tracking: When you use CoLab for sharing data and having design conversations, your feedback is automatically tracked and organized as you do the work. Without any extra admin, every comment goes into an auto-generated overview that can be filtered and customized. That way, you’re always just a click away from a bird’s-eye view showing all your feedback and reviews.
You don’t need to use a design engagement system like our customers do. But the alternative for most teams is usually a “homegrown” and/or patchwork process that strings together multiple tools, often relying on a combo of general-purpose apps like Sharepoint, Excel, Asana, Adobe, PPT, Teams, etc. Aside from being inefficient, that kind of unstandardized approach to design collaboration is nearly impossible to scale as the business grows.
So while you don’t have to use a tool like CoLab, you do need to put thought into how to solve these issues within your organization.
No matter what tools your team uses, your collaborative processes need to align with your business goals. That means you need to understand what those processes are, and whether they’re currently effective or not. Then you can start to figure out where you need to adapt your workflows: Are there repetitive tasks you can automate? Do you have a real-time way to collaborate on design? Is knowledge getting shared across teams and departments?
There are so many advancements and innovations in software and technology that it’s impossible to keep up with everything. Sometimes it’s hard to know if something is revolutionary, still years away from being relevant, or just a passing fad. But that’s why it’s so crucial to figure out your long-term solution for the basic challenges of remote, global design collaboration.
Because until those core collaborative workflows are frictionless — there’s always going to be a ceiling on your team’s ability to innovate and move faster.