Still unfreezing design freezes?
GET A DEMO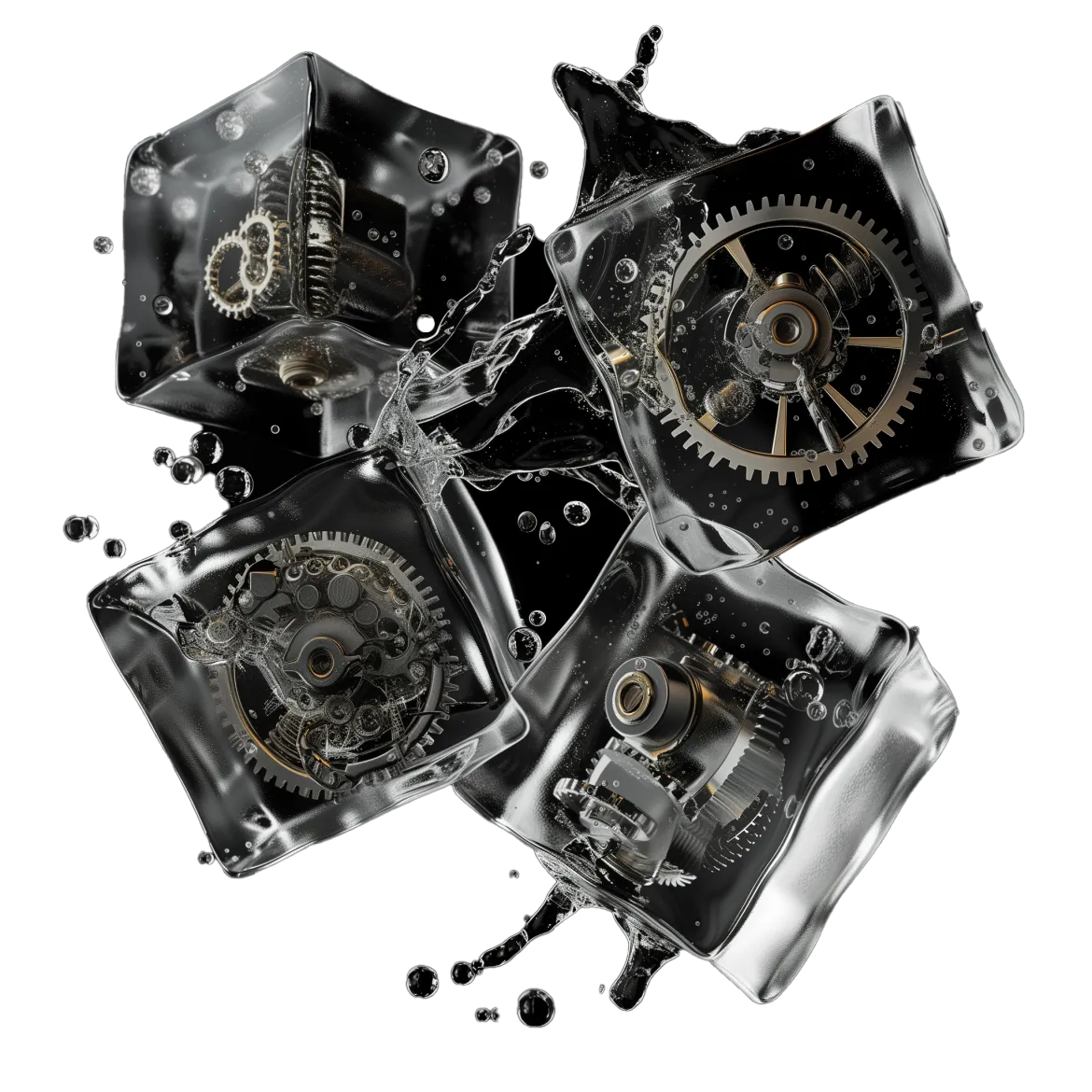
NPD today is like trying to build a race car using only tools from the Stone Age. The desired outcome is too complex for the tools and processes at hand. NPD teams need a new way to facilitate the entire product development process. So design freezes stay frozen.
NPD teams face impossible expectations
NPD teams today must:
- Ensure the product meets the functional requirements at every stage of design
- Source components from suppliers who can meet the forecasted demand
- Meet all regulatory and compliance standards
This means collaborating with teams of engineers, internal cross-functional teams, manufacturing partners and suppliers to launch products on time and on budget.
But the way engineering teams facilitate and track the bulk of NPD tasks is through spreadsheets, meetings and PowerPoint decks. So, it’s no wonder that engineering leaders estimate 43% of all design feedback is never tracked or actioned. Which leads to 90% of all companies delaying NPD launches due to late-stage design changes.
The processes and tools can’t meet the NPD project’s complexity. And design freezes don’t stay frozen.
The problem with NPD today
So, we have two major obstacles making collaboration during NPD nearly impossible:
- Internal processes
- Internal tools
Internal processes
It’s no wonder that most engineering teams don’t actively involve their suppliers or production team during early NPD stages. That “process” is usually a meeting that looks something like this:
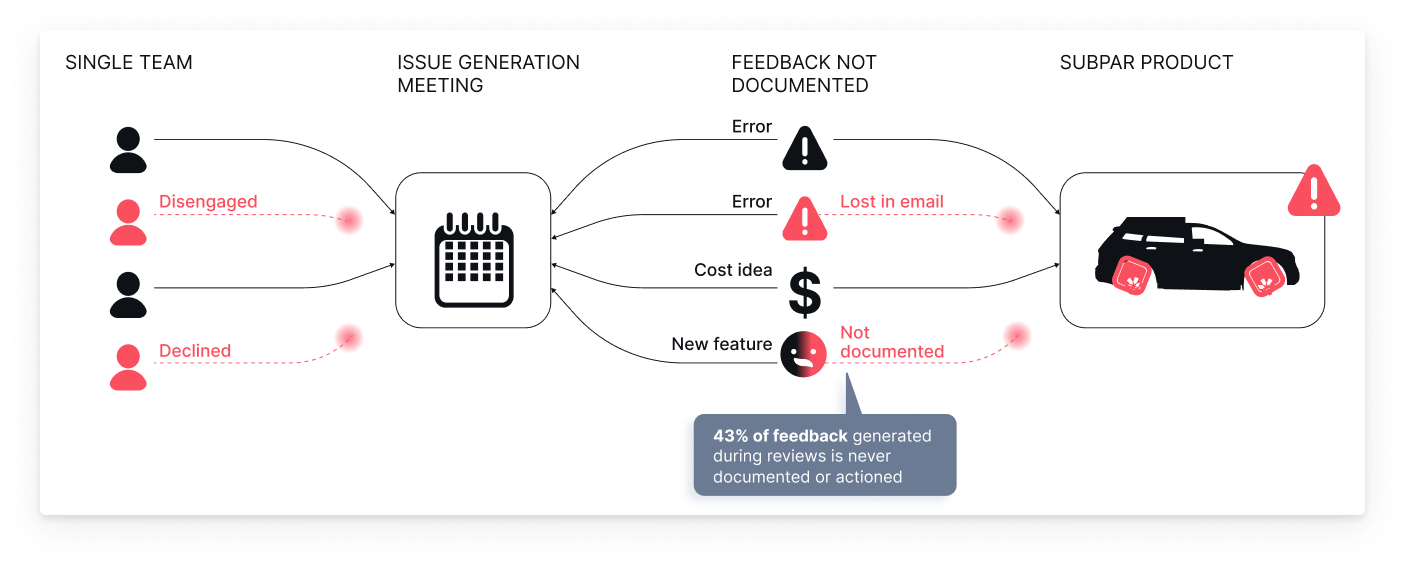
And this is just the first meeting. Every subsequent meeting follows the same frustrating loop. And more and more design feedback is lost because it’s just not documented in that NPD spreadsheet.
So, while you know any change you make early is going to save a ton of time and money, you wait until the very end because it’s not easy to get that early feedback.
It’s not easy for engineers to look at the same model. It’s not easy to share the same BOM across suppliers. It’s not easy to record feedback in a searchable, automatic way.
The rate of change during development is so high, that there isn’t a good way to collaborate between engineering team members and suppliers in a simultaneous, asynchronous environment.
Internal software
Aside from the broken internal processes, internal software systems are not equipped to handle engineering, supplier and production collaboration.
If we look at the product development process through a software lens, we see three major “systems” in use: CAD, PLM and DES.
CAD
For initial conceptual design and analysis, engineers use CAD. And it works. During the typical stage gate process, CAD makes the most sense in the early stages. Engineers interface with a specialized tool for product design and analysis.
At this early stage, there are also fewer team members involved and the process is engineering-heavy. Therefore, CAD makes the most sense as the software system of choice.
PLM
PLM systems are a vital cornerstone for engineering and manufacturing teams, particularly within large-scale enterprises.
Companies revere PLM systems for their ability to house official documents, manage various workflows, and safeguard access to vital information.
However, PLMs are rigid—as they should be. But, they are too rigid for middle stage gate steps when reviews are more fluid. PLM instead should fall much later in the product development process.
In fact, in a recent survey of 250 engineering leaders, 71% report they do not use their PLM for product development. Despite 100% of survey respondents having a PLM or PDM in place.
DES
DES stands for Design Engagement System. If we look at CAD and PLM based on how and where they’re leveraged in the stage gate process: CAD is early (and evolves throughout), PLM is later when the design is ready for a freeze.
DES is leveraged in the critical middle stages where collaboration among engineering teams, suppliers and production teams is most critical.
You can use a DES to evolve a design using feedback from key stakeholders. Once an engineer creates a first CAD design revision, they need feedback from SMEs to improve that design.
A Design Engagement System like CoLab is purpose-built to let SMEs review CAD and provide feedback. Teams that don't use a dedicated DES system, typically use a mix of other tools like:
- PowerPoint
- Excel
- Word
- Notebooks
Rather than using a dedicated DES, most teams are using the above mix to perform critical design reviews.
As a result, product development teams experience the following design review headaches:
- Teams are forced to rely on meetings to generate feedback because sharing CAD files is too difficult.
- The alternative to a meeting is building a PowerPoint with screenshots, which is admin intensive and occasionally fails to communicate design intent.
- When a meeting does occur, documenting the feedback from that meeting is admin intensive: you need the PowerPoint or you use a spreadsheet and lose all the visual context of the 3D model.
Because the design review process is so painful, we're relying on people to brute force product development.
DES as the solution to unfreezing late-stage design freezes
It’s easier said than done to simply retool your stage gate process by replacing what you have now with a system for collaborative feedback and iteration during the middle stage gate steps.
But it’s critical for teams experiencing frequent design freeze unfreezing in their NPD processes.
Like eliminating waste in a lean manufacturing facility, teams can replace their antiquated multi-step processes with a DES where this is possible.
As a DES designed to work with your PLM and CAD systems, CoLab makes it easy for SMEs to provide useful design feedback and automate all documentation and tracking.
Moreover, aside from eliminating, or at least reducing design freeze unfreezes, a dedicated DES can solve other symptoms of poorly adopted systems and processes.
- Promote collaboration between teams and people in complex environments. The world is different today. In-person design review meetings, manual mark-ups and on-prem software are relics of antiquated product development processes. Engineering teams have adequately addressed challenges like conceptual design and analysis with CAD. And, controls and data housing with PLM. But the way engineering teams collaborate during the design process needs to evolve with how humans interact and collaborate online today.
- Bring risk forward. Everyone wants to catch preventable mistakes earlier in the stage gate process, but few companies actually avoid late-stage design changes. Much of the collaborative design review process happens too late. Production teams aren’t consulted until the final prototype. And suppliers have only a few opportunities in the stage gate process to add real value. But with a DES, companies can move much of the risk associated with design changes forward into the middle product development stages.
- Reduce expensive design changes. Often because production teams or suppliers aren’t brought on until later in the stage gate process, they find expensive errors too late in the design review. This means the engineering team is forced to unfreeze the design and move back to an earlier stage.
- Remove administrative barriers within the review process. Yes, design reviews should be thorough and intense. But the administrative burden of it can be drastically reduced. You can intelligently automate non-value added work (like documenting and tracking feedback), so your team can focus on the value added aspects of a design review.
We’re not saying the transition to a DES will be easy. We’re saying the most forward-thinking companies today are moving to DES environments as their preferred method for design reviews.
CoLab as a DES
When it comes to a DES, you have a few options. But CoLab is the only one selected by companies like Schaeffler, Ford Pro, Hyundai, Komatsu and Polaris.
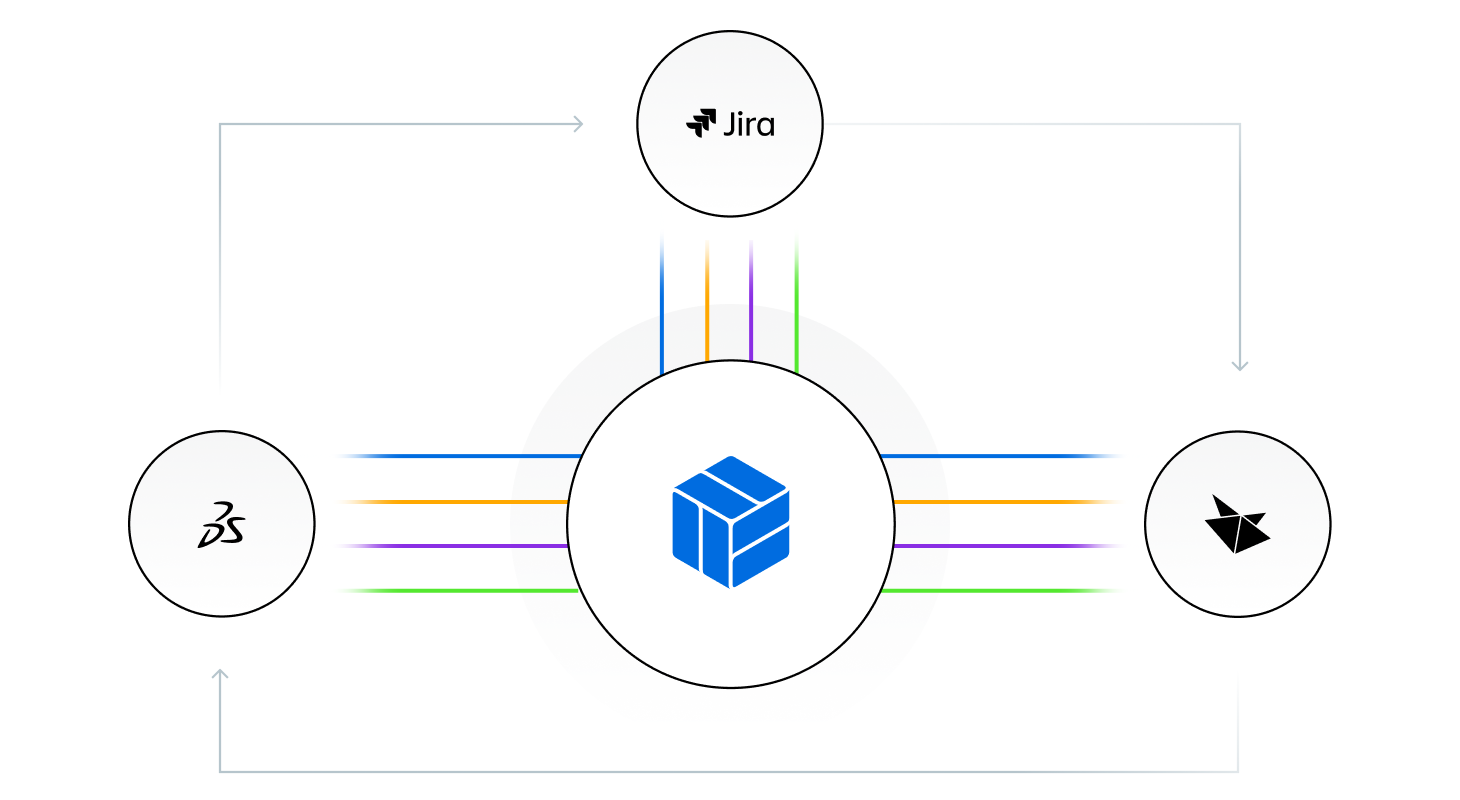
These companies choose CoLab because, like a DES, it’s purpose built for fast, effective design review. Using CoLab as their DES, multiple engineers, designers, and other stakeholders can review designs together and build off one another's feedback.
CoLab makes it easy to review the right data—3D models and 2D drawings—with all the right people, capture useful feedback, and track issues through to action. CoLab pulls together design discussions previously lost in emails, spreadsheets, and notebooks into a single platform that integrates back into PLM.
Moreover, with CoLab’s customer support team, no engineering team is left to configure these processes alone. Your CoLab team is a partner throughout your DES journey.
Case Studies
“The way we were doing our work is the same way that everyone else has traditionally been doing their work. Take screenshots [of a design], put that into a slide deck, and send that slide deck around for comments. Then you’re getting 10 people in a conference room for an hour. That's how we were doing things, but we knew there had to be a better way.”
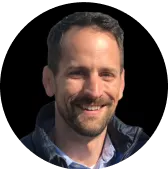
What’s next?
If you’re ready to see how a DES can transform the way your engineering team works, here’s how the process works with CoLab.
- Every conversation starts with a discovery call. During this call, a technical expert will understand your team’s challenges with design review today
- Then, we’ll tailor a demo to address those challenges. This demo includes you, of course, but also some key members from your team who can speak to your challenges in greater detail and vet CoLab as the solution.
- Finally, we do a workshop with more members of your team. This is the fun part! During this workshop, your team will each have temporary CoLab licenses and participate in a sample design review. You and your team will be guided through key features and use cases right inside the CoLab platform.