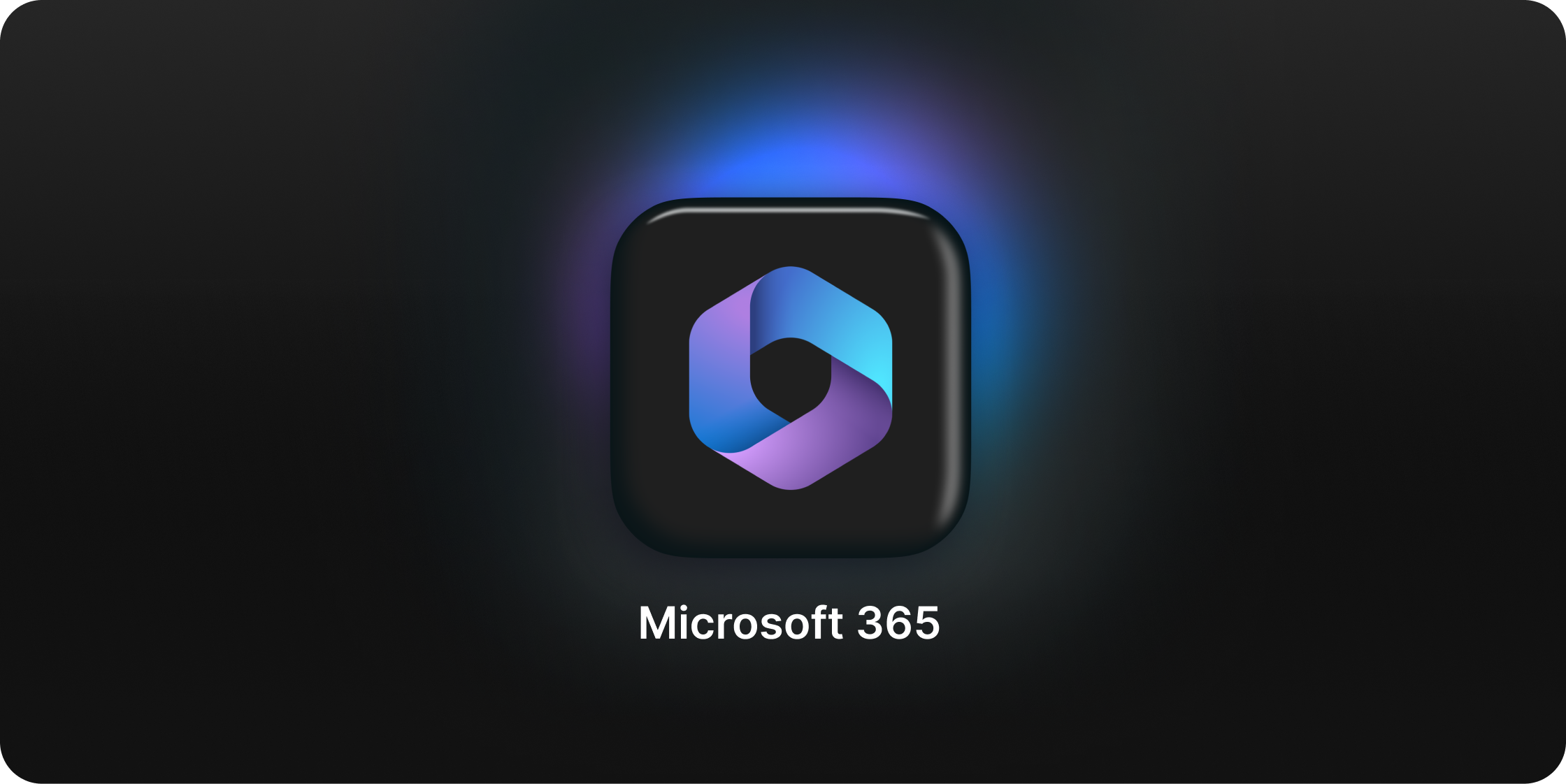
What tools do engineering teams use to document design feedback?
What tools do engineering teams use to document design feedback?
This article is part of the CoLab Research Reports series, where we publish findings from both engineering leader surveys and aggregated, anonymized CoLab data. To subscribe and receive reports to your inbox, click here.
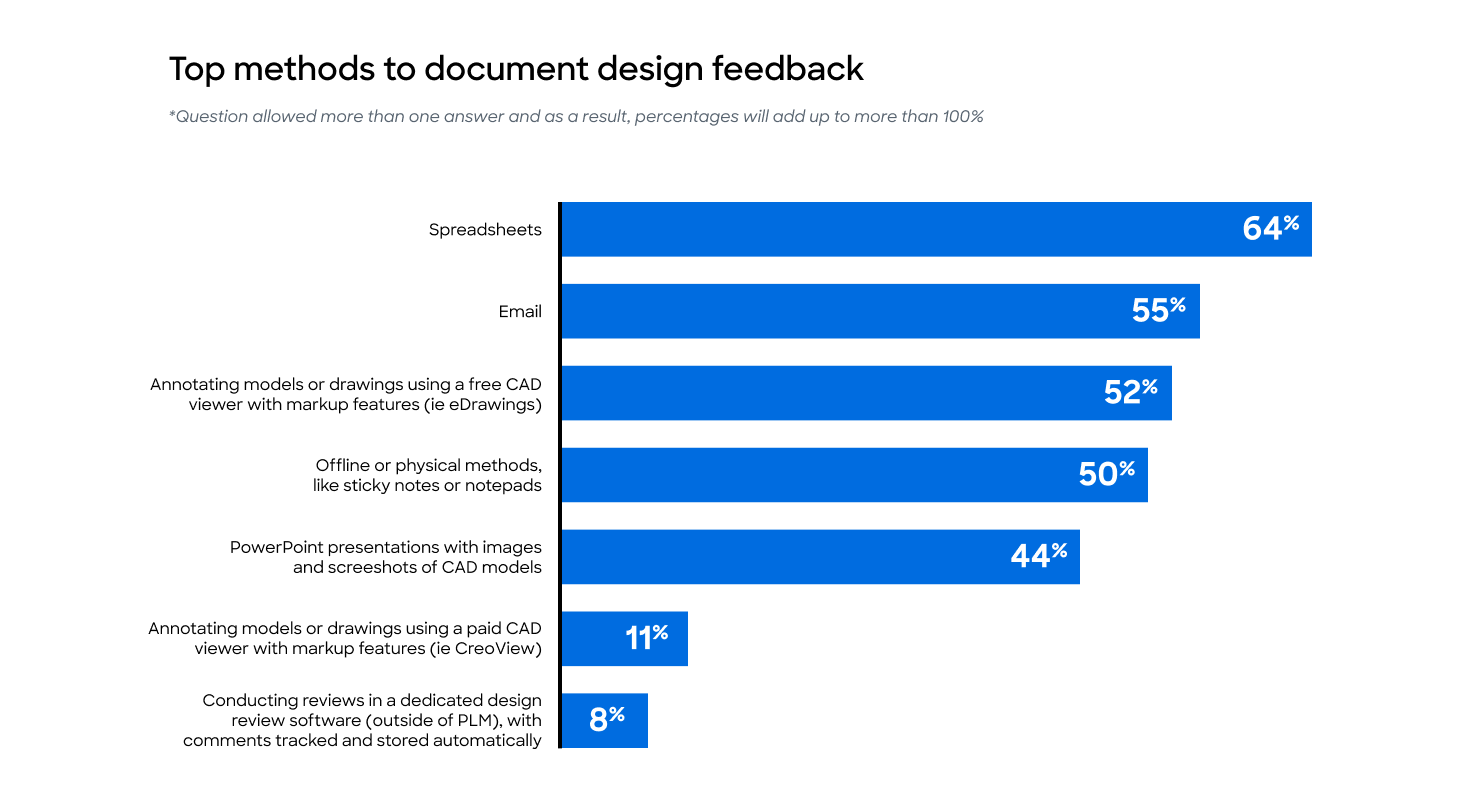
I would be shocked if anyone else is shocked by the results here. By an overwhelming majority, the top methods for documenting design feedback are:
- Spreadsheets
- Free CAD viewers with markup tools (often used in conjunction with PowerPoint)
- Manual notes
Ask an engineering leader this same question 10 years ago and you would have gotten a similar answer.
Is there an inherent problem in this status quo?
Maybe, maybe not.
If, like most engineering teams, you use these methods for documenting design reviews AND also:
- Delay product launches due to late stage design changes
- Suffer through unnecessary rework during product development
- Lose track of nearly half your design decisions
Then, yes. There’s a problem with the status quo.
First, let’s dive a bit deeper into the results.
“99% of the engineering world is run on spreadsheets.”
This is a running joke for our CEO, Adam Keating, during customer meet-ups. Turns out that number is closer to 64% – for design review anyway.
There is no inherent problem in spreadsheets themselves. Most teams use spreadsheets. Data analysis, brainstorming, issue tracking: they’re all valid spreadsheet uses.
The problem with spreadsheets is the almost pigheaded determination to use spreadsheets well beyond their feasible capability. We’ve seen teams tracking design review issues using 1000+ rows, 50+ columns with links, screenshots, references and so many broken formulas that it’s now someone’s part-time job just to maintain them. It would haunt the dreams of most project managers.
But this isn’t even a spreadsheet’s downfall. It’s that spreadsheets rely on manual, human intervention. A human has to input the screenshots and external links. A human has to type out or CTRL+X, CTRL+V every issue. A human has to create the formulas that keep the spreadsheet running. You get the picture.
And because it’s manual, it’s not only prone to error (hello, #REF! error), it’s burning engineers out.
We talk to engineering leaders and individual contributors every day and you can feel the frustration in their voice when they talk about tracking issues in spreadsheets. Why? Because this is not why they got into engineering. Tools like this are part of the job, sure. But when 20-25% of an engineer’s day is spent on non-value add work like this, they feel it. We feel it. And I’m sure you do, too.
“We use Microsoft’s PLM for design review: Outlook + PowerPoint.”
IYKYK. Email is still the preferred communication channel for discussing design issues and sending design files.
As this study shows, most teams use some combination of the tools listed here to document design feedback. For most engineering teams, this workflow looks something like this:
- Engineer takes screenshots of CAD and puts those on slides in a PowerPoint deck
- Engineer sends PowerPoint via email for review
- Reviewers add markup and comments to each slide
- Reviewers send file back to engineer via email
And then the cycle starts all over. Not to mention, the engineer spends the next 2-3 days reconciling all the PowerPoint file versions to capture critical feedback. The not so critical feedback? Well, it’s okay if a few of those slip through the cracks.
Much like the inherent problems with spreadsheets, the “Microsoft PLM” suffers from the same dire consequences:
- Lost feedback leading to late stage design changes and rework
- Engineer burnout from too much non-value add, administrative tasks
- Unnecessary risk due to manual entry and human error
Yet, engineering teams live with it. Why? Because the problem isn’t big enough… yet. They’re not able to tie lost feedback to rework, so it gets ignored. Engineers aren’t leaving in droves (just your best ones), so it gets ignored. The unnecessary rsk hasn’t hit the bottom line, so it gets ignored.
But, the best engineering teams in the world don’t wait for the big problem. They use these signals to diagnose the root cause issue. Then, they get to work to solve it.
The solution is simple, but not easy
The problems are clear. Spreadsheets, the Microsoft PLM, free CAD viewers, manual notes. They all come with the same issues: too much admin work, too much manual intervention, not enough real problem-solving and collaboration.
The solution is what’s not as clear.
For engineering leaders in this same survey,most agree that the solution is a better tool for design reviews. But, no one is sure what exactly that tool is, or even what it should exactly do.
So, they live with the problems of running status quo design reviews. They live with them until the small problems become big problems and maybe even until those big problems become catastrophic problems. Because living with the problem is easy.
But what if that better tool does exist? It does and it’s a Design Engagement System. The solution doesn’t end at the tool, however. That would be easy. A true solution is simple. A Design Engagement System is certainly easy, but it requires a mindset shift within your engineering organization. A shift focused on working more effectively across your team, your organization and your supply chain. And along with that shift comes a new way of working. New processes, workflows, culture – and, of course, new tools.
See? Simple. Just not easy.
See how a Design Engagement System works.
About the survey
To get greater insight into the state of complex product development processes, we commissioned a survey of 250 full-time employees, 50% of which are Engineering Managers or Directors, and 50% of which are VPs or C Level Executives.
Respondents work in the manufacturing industry, specifically in industrial equipment, heavy machinery, automotive, and consumer hardware, and are split across the US, the UK, and Western Europe.
All respondents work at companies with 1,000+ employees that have already invested in a PDM or PLM system.
This report was administered online by Global Surveyz Research, a global research firm. The respondents were recruited through a global B2B research panel, invited via email to complete the survey, with all responses collected during October 2023. The average amount of time spent on the survey was 5 minutes and 44 seconds. The answers to the majority of the non-numerical questions were randomized, in order to prevent order bias in the answers.
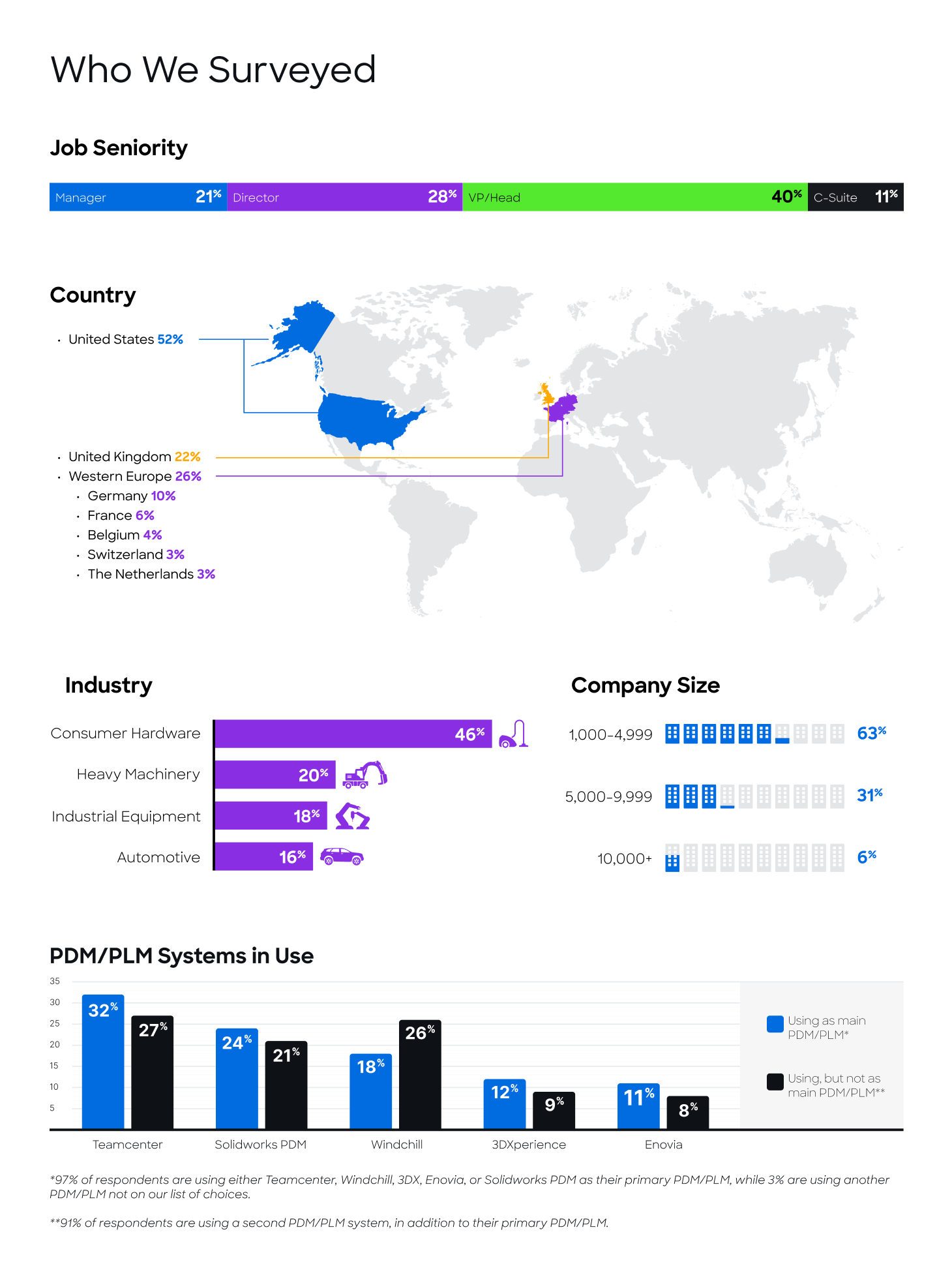
Quantifying the impact of design review methods on NPD
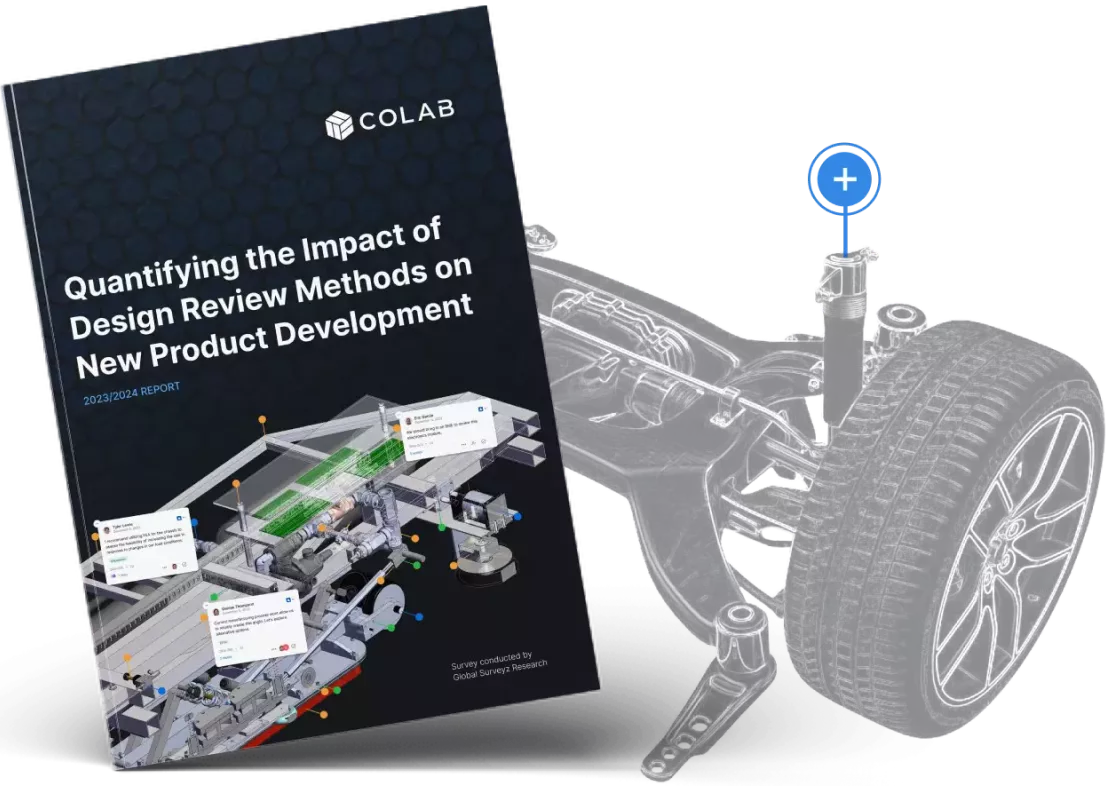