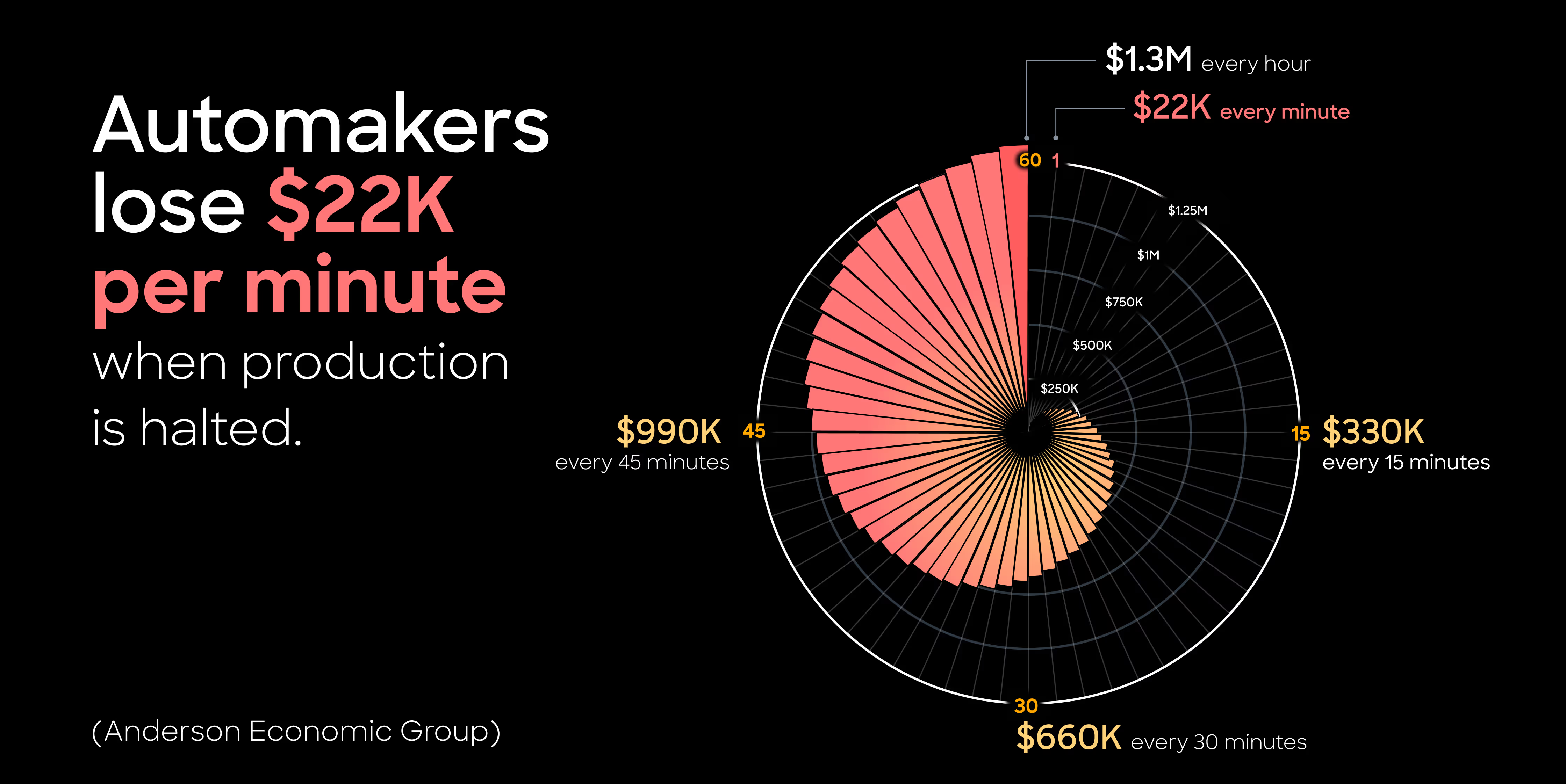
Supplier miscommunication on designs causes major downstream production issues
Supplier miscommunication on designs causes major downstream production issues
This article is part of the CoLab Research Reports series, where we publish findings from both engineering leader surveys and aggregated, anonymized CoLab data. To subscribe and receive reports to your inbox, click here.
It’s no surprise that supply chain problems cause major downstream production issues for OEMs. A look at the aerospace industry over the last few years reveals just how deeply suppliers affect OEM production, quality, profitability and market share.
Boeing is perhaps the starkest example. At the time considered revolutionary, its move to outsource the majority of its product design and parts manufacturing resulted in – most notably – the January 2024 incident where the exit door of the 737 Max 9 blew off at 16,000 feet. Both before and after this incident, Boeing had to recall multiple units and delay delivery due to supplier quality issues.
Downstream issues steal the focus from root cause problems… and it’s costing companies millions
While the example is extreme, it was also no surprise when 250 engineering leaders agreed that supplier miscommunication during product development (pre-production) also causes major downstream problems.
Specifically:
- Product development delays (31% of respondents)
- Long lead times (28%)
- Unbudgeted costs (18%)
And recurring quality issues and high cost of goods affecting gross margins weren’t far behind.
When faced with supplier issues, however, manufacturing companies don’t examine early stage product development processes. Instead, they move to diversify supply chains, create new supplier programs and even bolster the suppliers they already have with better manufacturing capabilities and skilled workers.
This is a mistake.
By putting out fires downstream at the very tip of the problem, companies miss a massive opportunity to root out problems at the source: how engineers interact with suppliers during product design stages.
So, what happens? Manufacturing companies spend more time, more money and more effort solving the symptom rather than the cause. Because manufacturing companies don’t understand how supplier miscommunication during early product development causes these major downstream issues, they don’t focus on solving it.
This is not only inefficient, it’s also costing these companies millions of dollars.
Let’s examine how.
Supplier miscommunication during early product development costs companies millions
1. Product launch delays
For engineering leaders, this was the top downstream issue caused by supplier miscommunication. And it makes sense. Engineers have few KPIs directly attributable to their processes, but product development deadlines are the most explicit.
But, how exactly does supplier miscommunication contribute to this problem?
The root cause:
During product development, engineers bring suppliers in to give feedback on processes like DFM and RFQs. However, these processes are riddled with administrative headaches and ensuing complications.
During DFM, suppliers often misinterpret design specs because design intent isn’t properly defined. Or, because engineers wait too long to get supplier feedback on RFQs, so suppliers can’t respond in time for the next iteration. These delays often cause unnecessary rework.
Then, the back-and-forth between meetings, phone calls and emails only delays iteration cycles further. Constantly pressured to push designs through the cycle faster, engineers force design versions through product development that might have manufacturability or cost errors. This causes late-stage design changes, which are a major culprit for product launch delays.
The impact:
Two examples from the aerospace industry underscore the impact of supplier miscommunication during design:
- An Airbus A380 wiring bundle miscommunication led to multi-year delays. This stemmed from a few issues, but most prominently mismatched CAD systems between the German and French supplier teams.
- $1.5B revenue loss from Boeing 787 delays due to coordination issues with suppliers and outsourcing design engineering work.
2. Long lead times
The root cause:
Long lead times frequently stem from either a complete lack of early supplier engagement or poor supplier communication during critical product development stages.
The most frequent causes of long lead times are incorrect components or materials ordered and delayed responses (outside of uncontrollable factors, like shipping delays and lack of resources).
This makes sense and goes hand-in-hand with product development delays. When engineers and suppliers fail to communicate or don’t communicate early and often with complete understanding, errors multiply. These errors not only affect the product launch deadline, they also affect the lead times for certain components.
The impact:
In 2021, General Motors identified an issue with engine valve lifters in certain vehicles. Although the supplier supposedly met the manufacturing specifications, the back-and-forth resulted in a 3-week lead time increase. This doesn’t seem that impactful except that it also forced GM to miss a critical product development window.
Similarly, a recent Deloitte study revealed 40% of supply chain companies identified late delivery as their biggest problem, often due to simple miscommunication. When we look at how late delivery affects product development, we see a delay as little as 6 months can cut product profitability by 33% over the life of the product.
3. Unbudgeted costs
The root cause:
Unbudgeted costs during product development come from myriad places. The most common being late-stage rework, increased parts costs (stemming from poor DFMA) and increased overhead.
Supplier miscommunication plays a role in each of these to varying degrees. Admin-intense processes and lack of proper tech tools leads to poor engineer-supplier communication. Engineers know the process is too hard, so they put it off as long as possible or don’t do it at all. And suppliers know engineers often lack proper design intent or context so communication is slow and unproductive.
This leads to late-stage rework, increased parts costs and increased overhead all because supplier feedback comes in too late.
The impact
According to McKinsey, late-stage design changes increase total development cost by 15–35%, especially in heavily regulated sectors like aviation and medical devices.
Furthermore, the cost of design change curve highlights how late-stage changes increase product costs exponentially the later those changes occur. This means an error caught during a first shipment authorization is 100,000x more expensive than one caught in design.
4. Recurring quality issues
The root cause:
Recurring quality issues are among the most insidious issues stemming from supplier miscommunication. And it’s often the fault of poor processes and improper tools, not the fault of people.
Quality issues often stem from a supplier’s misunderstanding of specifications. This isn’t surprising considering most specifications are given over 1,000+ row spreadsheets, in poorly worded emails or using CAD screenshots buried in PowerPoints. Because the supplier doesn't fully understand design intent and doesn’t have the full product context to provide feedback, specifications get muddled.
Furthermore, suppliers and engineers often get caught in a loop of defect–rework–defect. This is again, due to lack of clarity between engineering teams suppliers and supplier QA teams.
The impact:
The automotive industry is rife with recurring quality issues (though this is because automotive OEMs must publicize any quality issue or defect). Automotive News covered a 2022 warranty cost of over $500M+ tied to supplier error. In 2014, General Motors had to recall an entire product line due a faulty ignition switch resulting in $4B in costs.
Medical device manufacturing is also riddled with quality issues, though it happens less frequently and less severely due to strict regulations. However, quality recalls still occur and they do incredible financial damage to companies. In fact, the direct costs of a single recall can reach up to $600 million, including expenses such as notifying customers, retrieving defective products, and implementing corrective actions.
Beyond these immediate expenses, companies often face indirect costs that can be equally, if not more, damaging. These include litigation fees from lawsuits, harm to the company's reputation and decreased market share. Collectively, these factors contribute to an estimated annual cost of $5 billion for the medical device industry due to product recalls.
5. High COGS
The root cause:
Supplier miscommunication is more clearly at the root cause of high COGS than other downstream metrics. Why? Because headaches like emergency parts procurement, premium shipping costs due to delays, and material waste from incorrect production runs all stem directly from a failure to communicate on some critical product issue.
This is even more pronounced in product development. 1 in 10 engineering leaders say high COGS and margin impact stem from miscommunication during product development. This could be as simple as an RFQ mistake, incorrect specifications or improper part naming. Even a failure to engage suppliers early for DFM can drastically increase COGS. Mainspring Energy proved this when they used CoLab for early supplier engagement in design and reduced BOM costs by 50% for a single product.
Early and collaborative engagement with suppliers during early product development is critical for engineering teams to reach the staggering cost reduction and launch deadlines companies demand.
The impact:
A Deloitte report notes misalignment with tier-1 suppliers can increase COGS by up to 12% in automotive manufacturing.
Similarly, Supply Chain Insights released an analysis of medical device manufacturers where four out of five companies experienced increasing inventory levels over a decade. Often stemming from supplier miscommunication issues on parts inventory and delivery scheduling, these higher inventory levels tie up capital and increase storage costs, contributing to higher COGS.
The business case for refocusing efforts on supplier engagement during early product development
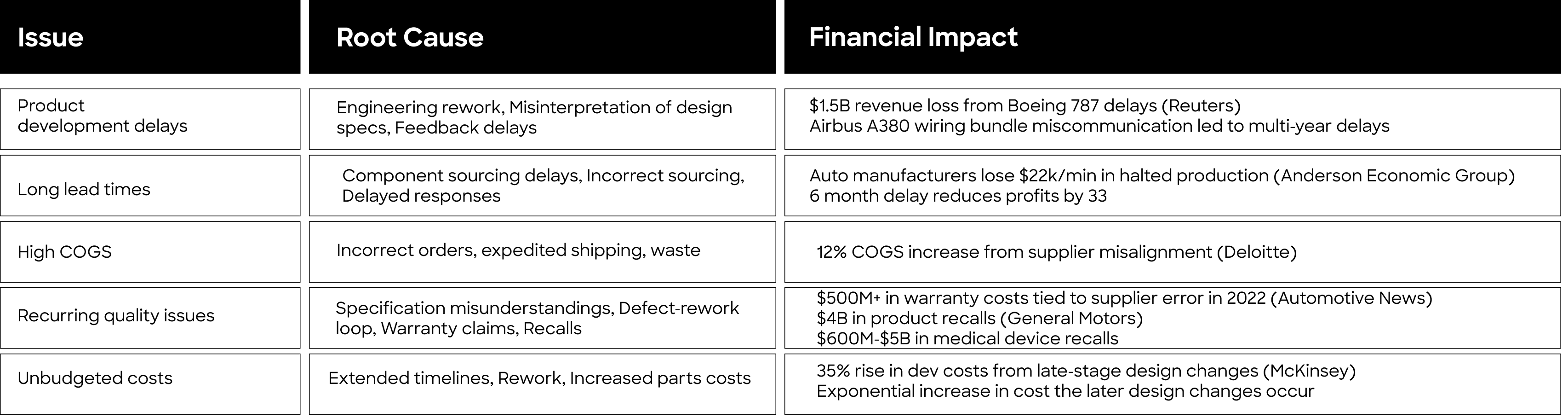
The results here are clear. Supplier miscommunication (or, often, a complete lack of supplier involvement) during early stage product development costs companies far more than the fires they’re putting out now.
Fires like supplier shipping delays, parts defects and material shortages are the tip of the iceberg. Those are urgent problems, of course, but also outside your control as an OEM. What’s in your control? Engaging with suppliers early in the design stages of product development.
Collaborating with suppliers during early product development helps engineering teams avoid downstream problems, like product development delays, long lead times, unbudgeted costs, recurring quality issues and high COGS.
By re-focusing your efforts away from what’s urgent, but not in your control to what’s not urgent but has incredible upside value, your company can avoid the major downstream supplier miscommunication problems plaguing engineering teams… and the company’s bottom line.
The only question is: Will you be Company A or Company B?
Quantifying the impact of design review methods on NPD
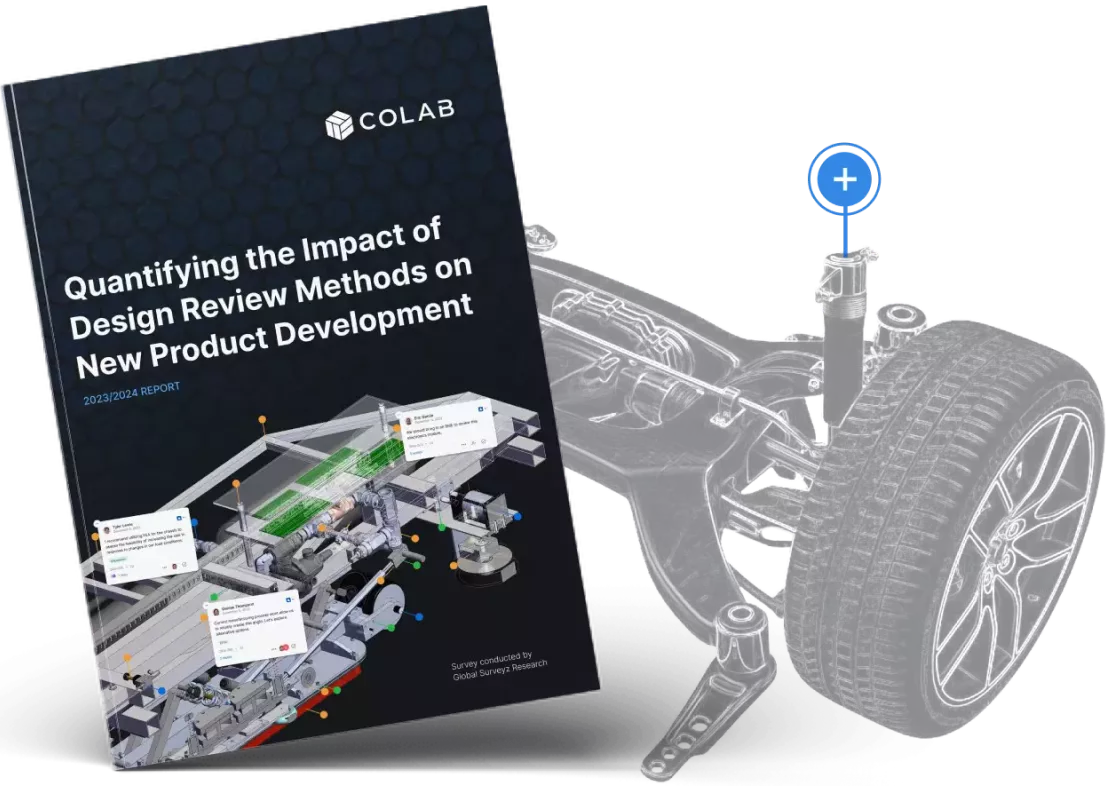