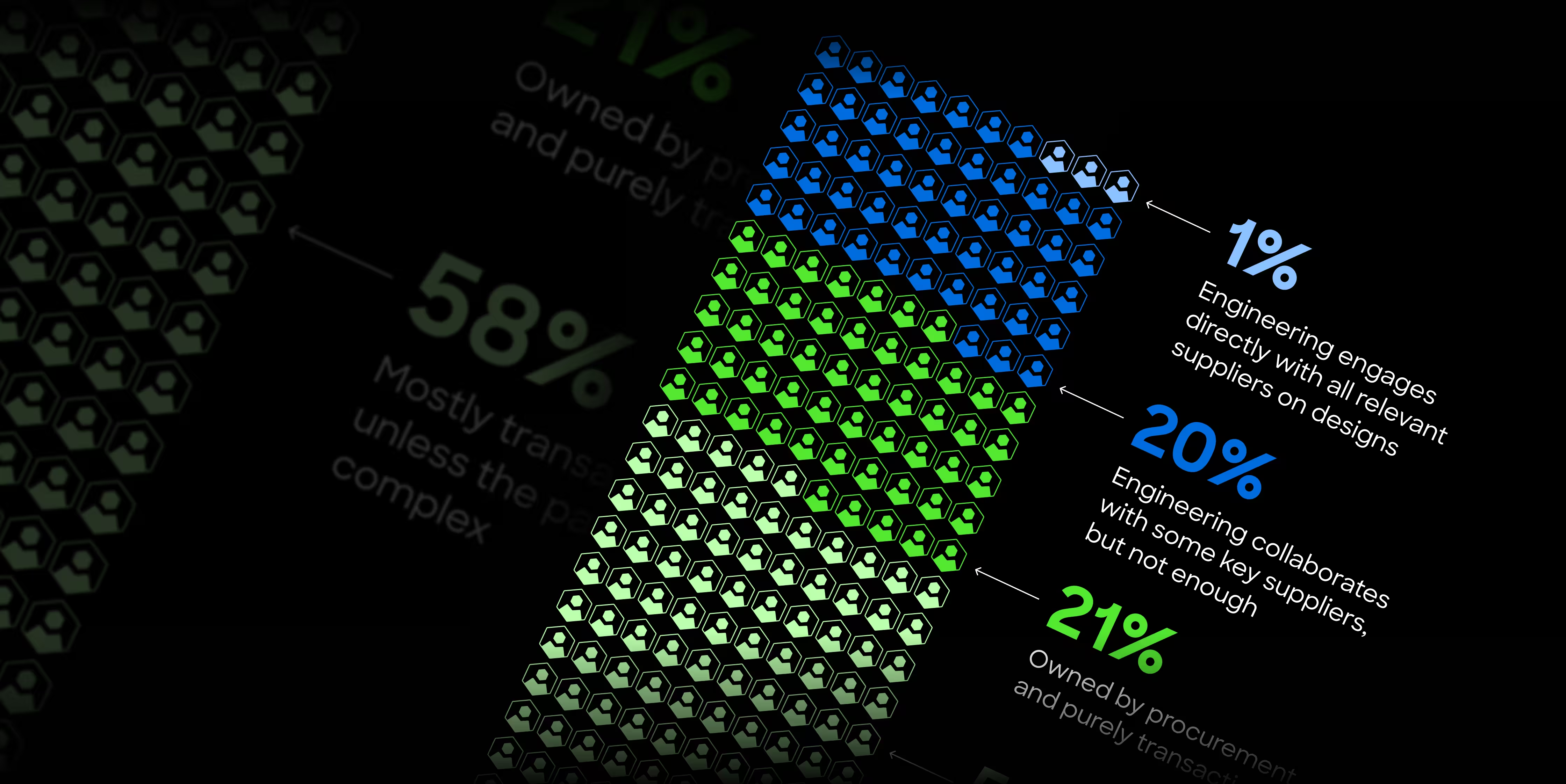
Only 1% of engineering teams collaborate with all relevant suppliers on designs
Only 1% of engineering teams collaborate with all relevant suppliers on designs
This article is part of the CoLab Research Reports series, where we publish findings from both engineering leader surveys and aggregated, anonymized CoLab data. To subscribe and receive reports to your inbox, click here.
No company is immune to organizational silos. And manufacturing companies are no exception. But nowhere is this clearer than the gap between engineering (the people designing the product) and procurement (the people managing how goods for that product get sourced and bought).
Each of these departments own different sides of the product development cycle. Engineers = NPD/NPI and Procurement = later NPD stages thru post NPI. As such, the product development process operates much like a waterfall. Engineers identify the parts that need to be sourced by external suppliers. They may even do some initial supplier sourcing. Procurement finds and works with the suppliers to get those parts brought into the company.
This waterfall approach worked when companies and products were much less complex. It had little effect on the speed and quality of product development. That’s no longer true today.
Products, companies and supply chains are more complex than ever. Yet the tools and processes teams use haven’t evolved with that complexity. So, engineering leaders reveal problems like:
- Engineers are not getting the design input they need from suppliers
- 90% of supplier feedback comes in too late
- And, the subject of this article: Only 1% of engineering teams engage directly with all relevant suppliers on designs
In this article, we’ll do a deep dive on:
- The tools and processes engineering teams use to collaborate with suppliers (if they do at all).
- Why those tools and processes no longer work and how we know they don’t work.
- The downstream effects of poor engineering-supplier relationships during NPD.
Current state: How engineering teams collaborate with suppliers
There’s two ways to examine how engineers collaborate with suppliers today: aggregated data and individual reports.
When we look at the data, here’s what we see:
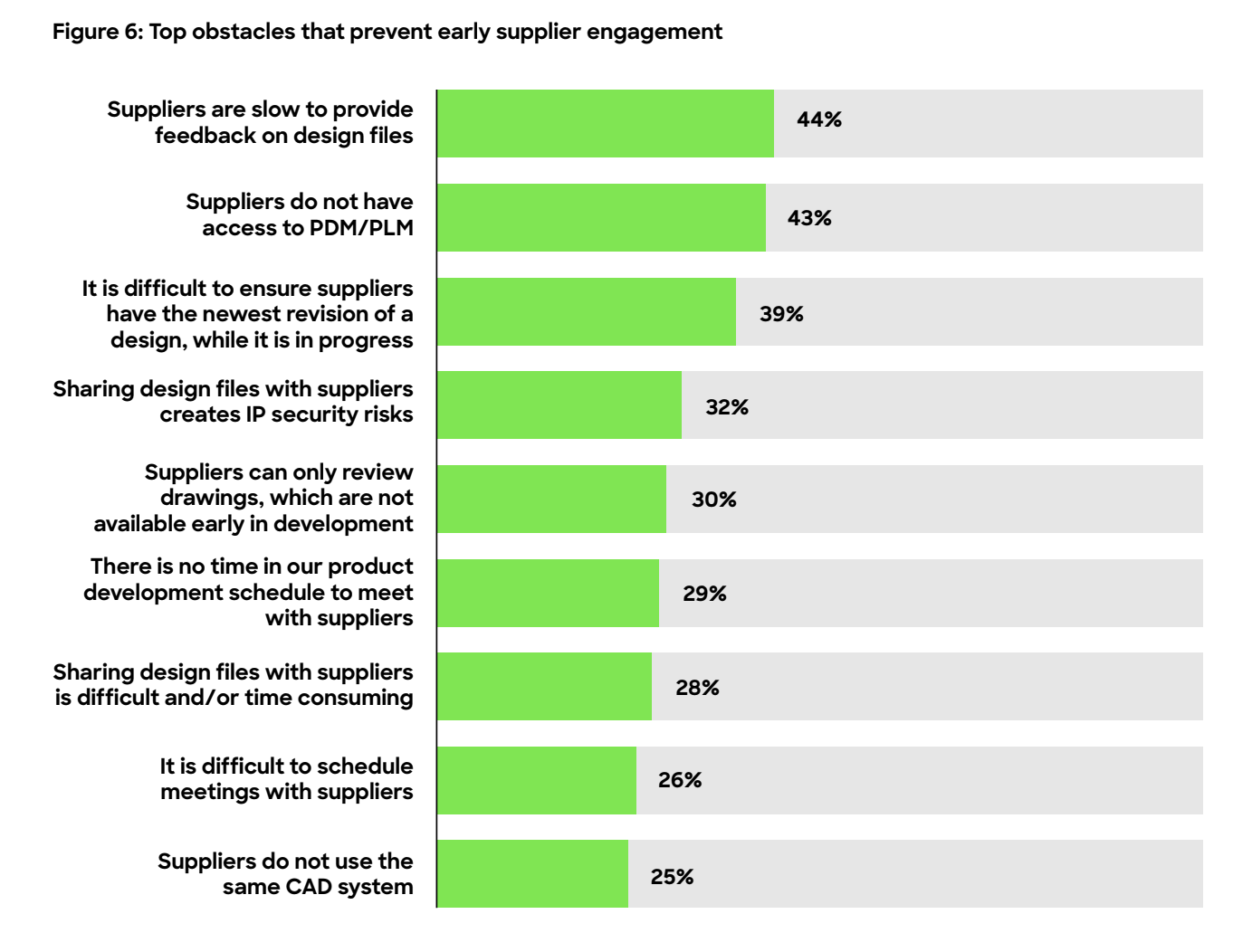
While these are mostly problems engineers experience (which we’ll discuss later), we still see hints at the tools and processes they use as well.
- PLM/PDM
- CAD
- Design files (STP, PDF or native CAD)
- Meetings
- Email or phone
Meaning the process is likely sequential. Engineers create a file package, maybe drawings, maybe CAD. They send those files over email or discuss the files in a meeting. They wait for supplier feedback.
This may be the only time this process occurs or it may happen 2-3 more times as the design gets revised.
Now, what do individual engineering leaders have to say?
In a few recent talks: The State of DFM in 2024, Turning Suppliers into Partners Panel and How BISSELL is Transforming Design Reviews, a few tool and process themes emerge.
TPI Composites: Spreadsheet checklists sent back-and-forth over email
The engineering team at TPI Composites used spreadsheets to conduct DFM reviews with suppliers. The spreadsheet would contain the project requirements, then TPI would send that off to suppliers with manufacturability feedback. This process would continue sequentially over many spreadsheets.
“To do DFM, it was Excel spreadsheets. We would send those out to a group of people around the globe, populate a spreadsheet with various requirements and capabilities. Then send the spreadsheets back to the customer to review and approve.’”
— Tyler Phillips, Director of Global Engineering, TPI Composites
BISSELL: CAD screenshots in PowerPoints sent over email or shared drives
For BISSELL, the supplier DFM process looked a little different. Jeff’s team would take screenshots of CAD, put those screenshots in a PowerPoint and then add notes for suppliers. These PowerPints would then be sent back-and-forth over email and OneDrive. Because the process was sequential, this also meant the files would get large. So large in fact, that they would crash their internal systems. Not to mention, version control wasn’t perfect, so the team often had to reconcile multiple revisions across many global suppliers.
“We did a lot of cutting and pasting of screenshots of CAD and then putting it into a PowerPoint or Excel document. The team had a hard time trying to keep track of all those changes. And then the documents get so large especially in PowerPoint, we were literally crashing the system.”
— Jeff Melick, Associate Director of Technical Services, BISSELL
Ford Pro: Phone calls, meetings and in-person visits to validate physical models
For Simon Robinson, collaborating with his global suppliers meant a lot of travel, a lot of meetings and a lot of physical parts. Simon explains that for most of For Pro’s converter partners and suppliers, they wouldn’t see anything – drawing or model – until the product was already in production. Then, Simon would travel to suppliers or partner locations with the physical product across the globe to gather feedback. Without a great interface for sharing design data, Ford Pro defaulted to tools and processes that worked when the world was less complex.
“Because the tools are limited, time zones are hard to contend with, and company systems are siloed, we did a lot of in-person meetings. We just couldn’t find an open interface to share data securely. There was a year where I went through 300 airports traveling with physical parts.”
— Simon Robinson, Chief Engineer, Ford Pro
From the aggregated data, we already saw some of the frustrations and obstacles that hold engineers back from engaging suppliers on early designs. But, with the added color of how real engineering teams engage suppliers, the conclusion is clear. The current state no longer works for engineers or suppliers.
Why the current state no longer works
We already saw in Figure 6 above that the same challenges plaguing TPI Composites, BISSELL and Ford Pro are what prevents aggregate engineering teams from engaging with suppliers on designs.
- The process is too slow.
- Suppliers don’t have the same technology systems as OEMs, whether that be PLM, PDM, CAD or file sharing.
- File sharing is difficult in general because security risk is high and keeping track of revisions is nearly impossible.
- It’s difficult and time-consuming to meet with suppliers.
When we asked engineering leaders what keeps their teams from co-designing products with suppliers and tapping into their expertise more frequently, similar frustrations came up.
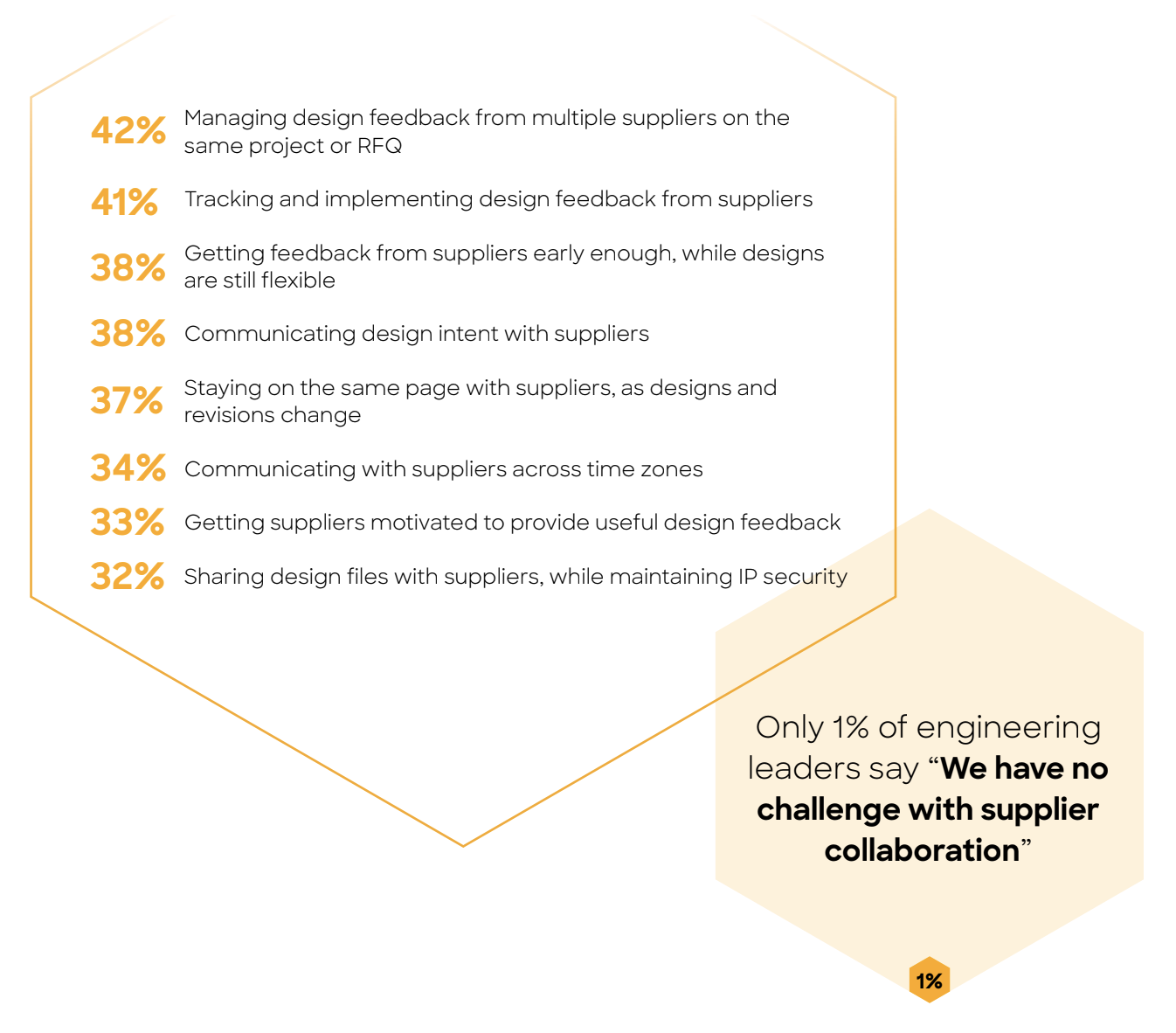
These themes match, almost perfectly, with what we heard in the live panel sessions with engineering leaders at TPI Composites, Ford Pro, iRobot, Mainspring Energy and BISSELL Homecare and what we saw in Figure 6.
The following problems with the tools and processes engineers use to collaborate with suppliers is what keeps them from engaging and co-designing with suppliers earlier in product development.
1. Manual, fragmented workflows
Engineering teams used a mix of Excel, PowerPoint, email, and meetings to share files and gather feedback from suppliers. This doesn’t seem problematic in and of itself, but because these tools are fragmented and require intense manual effort, the process is slow and arduous.
Additionally, because these tools require manual input, the process is sequential. This means suppliers and engineering teams are left waiting for feedback on this or that issue. This drastically inflates iteration cycles and contributes to the aggregate engineering data that says, “Because it’s slow, we just don’t do it.”
2. Lack of version control and traceability
Related to the issues above, because engineering teams must use manual workflows and fragmented tools, this means version control is nearly impossible and feedback gets lost. In fact, recent survey data estimates that 43% of all design review feedback is lost and never documented.
Without centralized systems, engineering leaders struggle to track which feedback or file version is current—especially across global teams. This theme was especially apparent in each of the Panels, where engineering leaders said things like:
“We were often asking: ‘Which spreadsheet do you have? Which revision of the documents do you have?’ and we’d all be working from different ones.”
— Tyler Phillips, Global Director of Engineering, TPI Composites
“It was always: ‘Who had the record of truth? Is it on my hard drive or somebody else’s?’”
— Jeff Melick, Associate Director of Technical Services, BISSELL
“Trying to keep it all together when one team moves faster than another leads to disconnected supplier strategies.”
— Eric Burbank, Engineering Manager, iRobot
3. Slow feedback cycles due to timezone barriers
Manual processes and communication delays across time zones slowed design progress significantly, often wasting days on back-and-forth clarification.
“You lose days trying to get design intent and context shared in a manual fashion.”
— Eric Burbank, Engineering Manager, iRobot
“We’re spread across three continents… just keep it constantly moving… if you miss, you’re waiting a full other day to get that feedback.”
— Kevin Walters, Global Director of Hardware Engineering, Mainspring Energy
“It's a huge admin burden trying to track all the information, and make sure all the feedback is actioned.”
— Matt Lane, Former Group Lead, Tesla
4. Suppliers get brought in too late to provide useful feedback
Suppliers were often brought in after key design decisions had been made. This is a mistake and engineering leaders admit as much. Preventing suppliers from providing design feedback means missing out on early manufacturability ideas or cost-saving opportunities. Suppliers are in a unique position to make impactful product decisions when the cost of change is low: in design as opposed to post-production.
“Historically, converters wouldn’t see any product until we had physical production running.”
— Simon Robinson, Chief Engineer, Ford Pro
“Too often I saw just a straight communication like ‘Give me a quote and we’ll purchase it’ versus a fluid discussion.”
— Tyler Vizek, former Engineer at Lockheed Martin
“When suppliers didn’t understand the context, it’s almost impossible for them to provide solutions.”
— Eric Burbank, Engineering Manager, iRobot
5. Difficulty capturing and reusing lessons learned to improve processes
While this didn’t come up in the aggregate survey data, this came up frequently during the Panel discussions. Engineering teams struggle to reuse knowledge from past projects because feedback and design history are buried in disjointed places. So, now engineers not only don’t tap into the knowledge of their supplier base today, but they miss out on the learnings from the past.
This also means engineering teams have almost no data to improve their processes today. When the feedback, documentation and lesions learned are centralized, that data isn’t available for large-scale analysis and improvement. Often engineering teams are so behind on how they conduct design reviews, they rarely stop and think “How can I improve design reviews?”
“Later on, you forgot why we made those changes because those slides are now deposited someplace else.”
— Jeff Melick, Associate Director of Technical Services, BISSELL
“We have a Lessons Learned database, but it’s not always consolidated. It’s been kind of handed down through the folks.”
— Tyler Phillips, Director of Global Engineering, TPI Composites
“Trying to actually measure the results of DFM is extremely challenging… because most places don’t even have that feedback consolidated in one spot.”
— Tyler Vizek, former Engineer at Lockheed Martin
The downstream effects of poor engineer-supplier engagement
When we look at the aggregate survey data, engineering leaders reveal a few key downstream effects of poor supplier communication.
Product development delays and long lead times topped the list. This makes sense. Engineering is rarely measured against business-level KPIs. But, product development speed and how fast suppliers can get parts to make the product tie directly back to engineering efforts. Problems like high COGS and recurring quality issues are more nebulous and can be attributed to varying factors, like supplier quality, geopolitical issues and business strategy. While some engineering leaders, like VPs or Senior Directors may be responsible for some part of COGS or quality, it’s less common for the majority of engineering leaders.
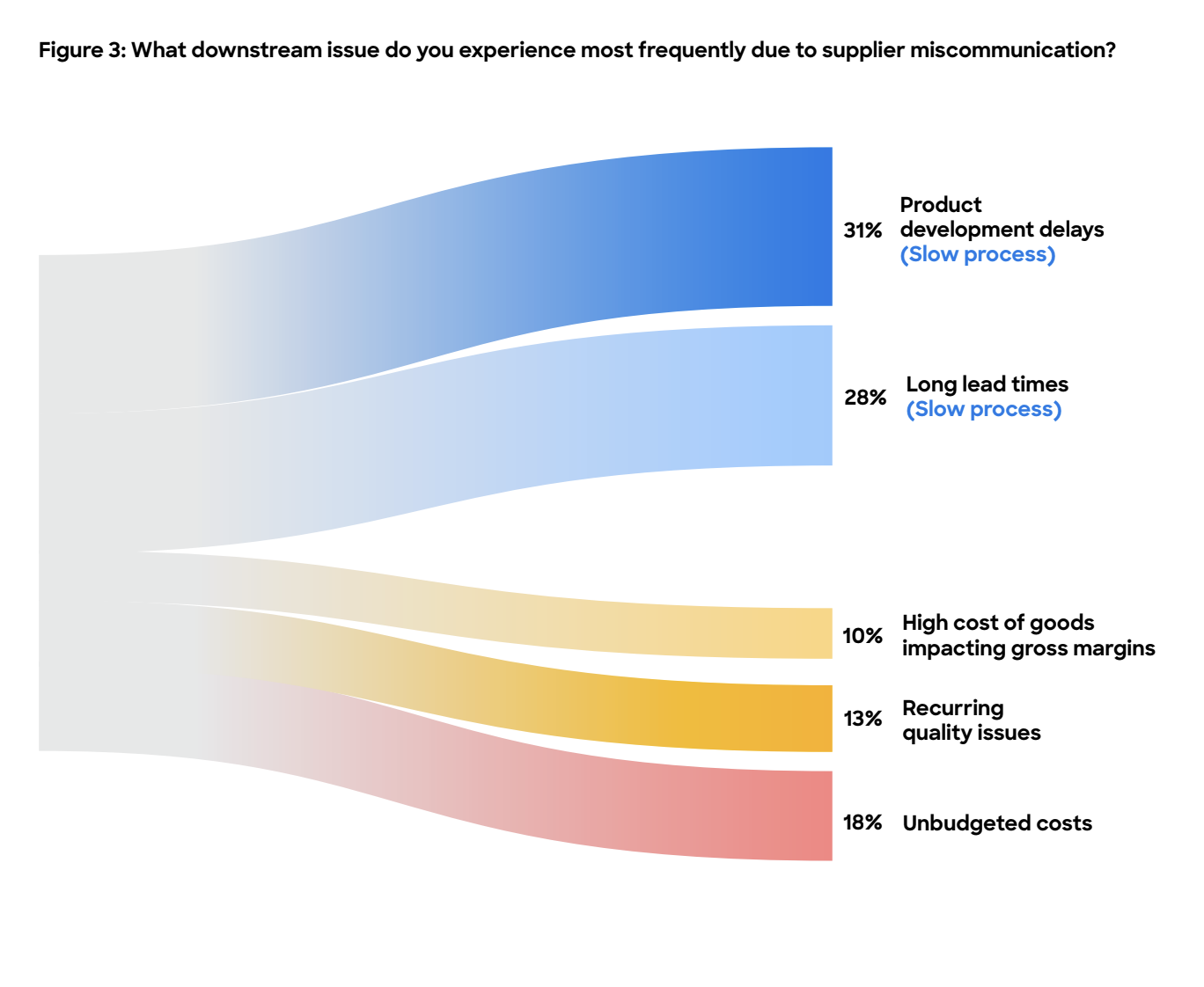
So, let’s dig into how product development delays and long lead times cause downstream issues.
Product development delays
Delaying a product launch by 6 months decreases its lifetime profitability by 33%. This means any delay reduces a product’s lifetime profitability by some percentage. The question engineering leaders need to answer is by how much and to what extent?
From the aggregate survey data and the engineering leader testimonials, we know the processes and tools engineers use to engage suppliers contributes to these delays. Waiting for feedback, confirming everyone’s using the right documentation and managing the process is so time consuming, most engineers avoid it.
This causes myriad product launch timeline problems. If you do try to engage suppliers, it’s slow and so slows down product development timelines. If you don’t engage suppliers early, you risk late-stage design changes and rework, which also slows product development timelines.
Either way, the legacy tools and processes engineers are forced to use to engage suppliers slows product development, which affects product launch deadlines and reduces lifetime product profitability.
Long lead times
Whether a lead time is long or short is actually arbitrary. The number itself doesn’t tell us anything about whether that lead time is good or bad. The sentiment of the lead time depends on whether the lead time positively or negatively correlates with prototyping or production time. A two-week lead time might be horrible for an engineering team who wants to get prototyping started in 6 days. While a two-week lead time for a team who needs to get to production in 6 weeks is a dream.
Since lead times are directly correlated with product development milestone timelines, what makes the lead time good or bad depends on how early and how effectively you communicate with your suppliers.
And considering about 1 in 4 engineering leaders say long lead times is the downstream issue they experience most frequently due to supplier miscommunication – it’s safe to say many engineering teams are not communicating early, often and effectively. We also see this in the engineering leader testimonials. Some teams, like Ford Pro, don’t communicate with their partners until the product is already in production.
Long lead times are directly correlated with product development delays and product development cost overruns.
Moving from transactional to reciprocal
Supplier relationships are nuanced. Procurement owns much of the supplier relationships and, in some cases, won’t let engineering interact with suppliers directly. Then, the legacy tools and processes engineering team use when they can interact with suppliers slows product development, is prone to errors and drastically increases the admin burden on engineers.
The answer is simple, but it’s not easy: Your team needs new tools and new processes to break down the barriers between engineers and suppliers.
The engineering teams seeing 30% reduction in lead times, 2x faster product development cycles and 4x more efficient supplier review cycles are doing just that.
Here’s how:
- Start slow with a small pilot.
Start slow and start small if you’re ready to change early supplier engagement. Select a single supplier and a single project. Mike Shipulski, former Director of Engineering at Hypertherm, conducted a DFMA project with a key regional supplier and brokered a deal advantageous for both the supplier and Hypotherm.
It resulted in massive profitability for both parties. The product took off thanks to faster time-to-market. And Hypertherm benefited from design-to-cost principles led by the supplier during the design phase. This opened the door for the engineering team to explore similar partnerships with other suppliers.
- Implement modern collaboration tools.
To bridge the supplier engagement gap, manufacturers need more than just better email tracking or more meetings. They need a Design Engagement System (DES): a purpose-built platform where engineers and suppliers can collaborate on CAD together in real-time.
A DES lets engineers and suppliers:
1. Share design files with anyone.
It should be easy to share design files with the people you need feedback from—without compromising your IP security or downloading half a dozen CAD viewers. And with CoLab, it is easy. Securely push drawings or models to CoLab and set the appropriate permissions. Then use a simple link that lets anyone open and view files, right in their web browser.
-p-2000.webp)
2. Reference the right files, feedback, and design history every time you make a decision.
Assembling engineering files for a design review can take hours. Sometimes, key files are left out of a package. Not to mention design history, which may be buried in old emails, slide decks, or spreadsheets.
By doing your work in CoLab, you’ll automatically create a centralized database of reviews and feedback across every revision of every file. Need to bring a new SME up to speed? Reviewers can quickly toggle between files and see all relevant feedback in the context of the model.
3. Replace sequential workflows with engaging reviews.
Reviews are often sequential, with one person creating markups, then sending them to the next person. This can lead to duplicate feedback, comments that contradict one another, and even late stage errors.
With CoLab, you can review files together and see other people’s feedback populate in real-time. Instead of sending static markups back and forth, reviewers can interact with each other via discussion threads.
4. Automate the design review admin
Documenting feedback during a design review is manual and time consuming. And the more context you capture, the more admin work it takes. It’s no wonder that 43% of all feedback from design reviews is never documented at all.
That’s why CoLab automatically tracks and organizes design feedback, as you do the work. Leaving feedback during a review creates a unique object that is automatically organized into a database and assigned its own URL.
Now, what?
If you’re ready to start closing the supplier design engineering gap and get more feedback from a greater percentage of your supplier base, learn more about CoLab here.
Quantifying the impact of design review methods on NPD
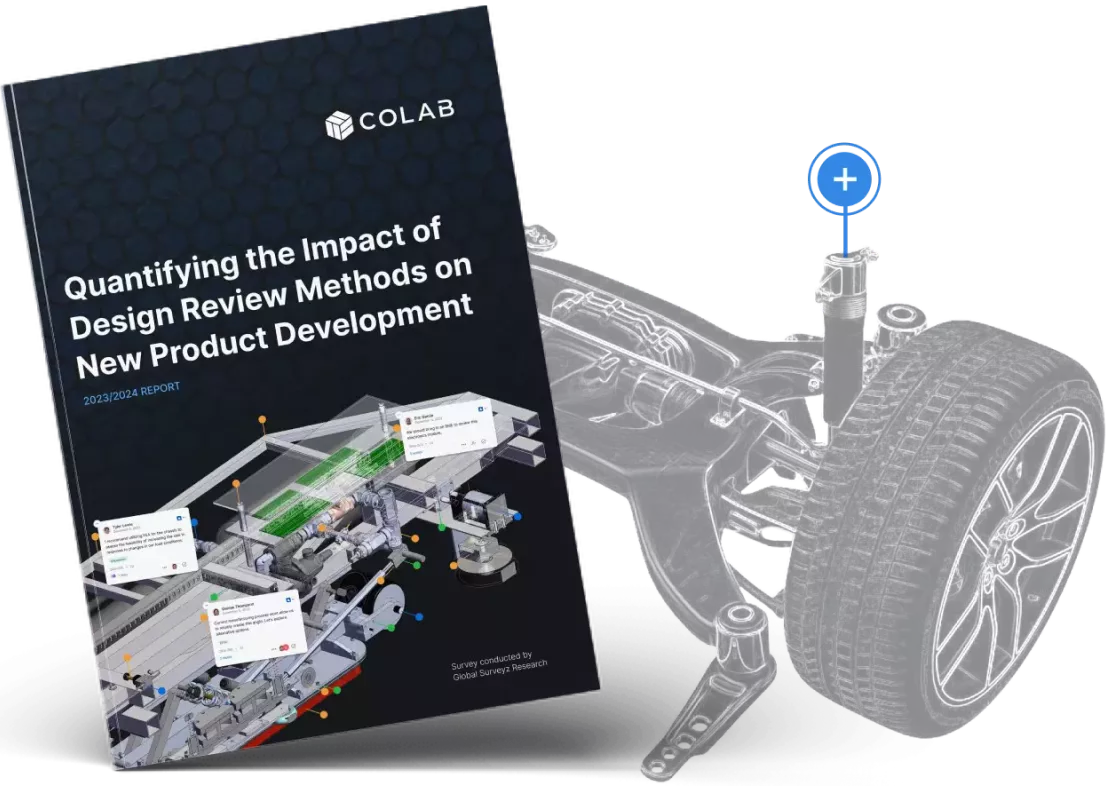