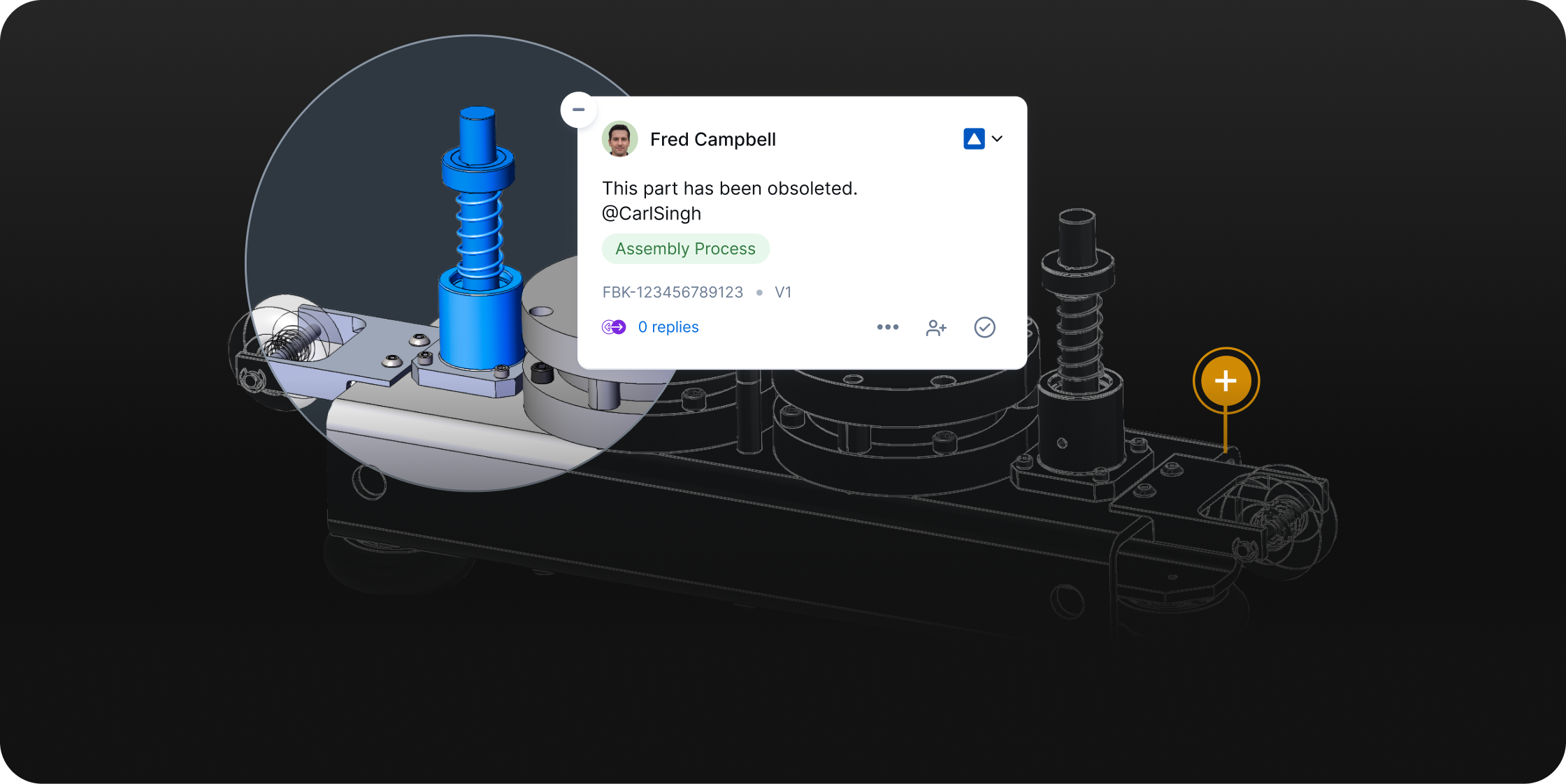
60% of late-stage errors could be prevented with better design review
60% of late-stage errors could be prevented with better design review
This article is part of the CoLab Research Reports series, where we publish findings from both engineering leader surveys and aggregated, anonymized CoLab data. To subscribe and receive reports to your inbox, click here.
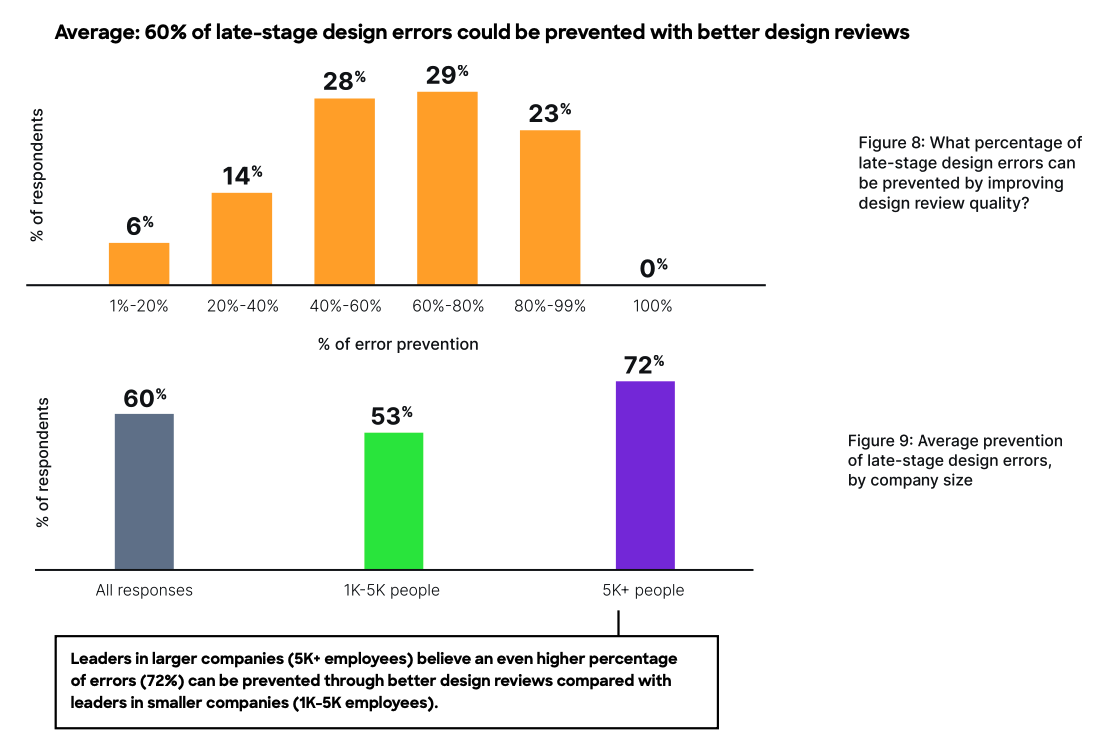
Late stage design changes cause 90% of companies to delay product launches.
When we examine late stage design changes, then, it should be regarded as a systemic product development problem. It’s also one completely in your team’s control.
Now, late stage design changes occur for any number of reasons:
- An RFQ from a supplier that came in over budget
- Poor material selection
- Unnecessarily complicated BoMs
- Manufacturability problems
The issue engineering teams endure over and over again is identifying and fixing these before testing, validation or pre-launch gates.
This study reveals a potential solution. Engineering leaders believe, on average, 60% of late stage errors could be prevented with better design reviews.
Nearly 1 in 4 engineering leaders believe THIS
While the 60% average is notable, the right side of this bell curve is most revealing. 23%, nearly 1 in 4, engineering leaders believe 80-99% of late stage design errors could be prevented with better design reviews. Meaning 1 in 4 engineering leaders believe better design review would essentially eliminate late stage design errors.
This may sound obvious, but anyone who’s been in product development knows how complicated this undertaking actually is.
Doing design review better is tricky:
- More meetings means more admin work for engineering teams, because tracking and following up on issues is all manual.
- Better use of PLM means added permissions and training for a team who’s already overburdened with the current workload.
- Giving more people access to CAD means higher security risk. Models and files are often shared via email, Sharepoint or Onedrive with little control on what happens to those files once they’re downloaded.
- Getting external folks involved too early can cause miscommunication. Oftentimes, CAD is too immature, but companies force engineers to share it with manufacturing or suppliers before a drawing. This can cause misinterpretation and confusion, especially when it comes to DFM or BoMs.
These problems (among others) mean design review is rarely prioritized as a “need to solve.” Not to mention, there’s no universally accepted way to conduct design reviews. Design reviews processes vary wildly across companies even in the same industry.
Nevertheless, better design reviews remain a top contender for improving or eliminating late stage design errors.
The larger the company, the greater the opportunity
In Figure 2 here, we see the larger the company, the greater the opportunity to improve design review.
For engineering leaders at companies with 5K+ employees, more than 70% of late stage design errors could be prevented with better design review.
This is significant because it also matches with how markets and industries tend to shift. Industry leaders with greater capital and greater resources tend to recognize problems earlier and dedicate resources to solve them.
As larger companies adopt new methods, processes and technology, the greater industry follows suit. This is how major breakthroughs like the assembly line, lean manufacturing and enterprise technology become widely accepted.
Meaning what we’re seeing here is an early trend. Larger companies see the problem: late stage design errors. And they see the solution: better design reviews. What we’re just starting to see now is how those large companies solve the “do better design reviews” challenge.
Companies like Ford, Schaeffler, Schneider Electric and Komatsu solved the design review problem with one important step: recognizing that traditional methods of design review don’t cut it anymore.
Design review can’t be done in spreadsheets, meetings or through markups in PowerPoint. It must be done by accepting that a better tool is required to facilitate better design reviews.
That tool is a Design Engagement System, or DES. And it’s the tool these large companies choose to do better design reviews.
However, this doesn’t mean the opportunity for slightly smaller companies isn’t there.
Companies with 1,000-4,999 employees realize that more than half of all late stage design errors could be prevented with better design reviews. So, it’s not that the recognition isn’t there, it’s that these companies might not realize the impact oif a potential solution, might not know a solution exists or don’t have the resources to solve this challenge.
Regardless of the size of your company though, this research exposes the breadth of this problem. It’s not just your engineering team suffering through this. The entire industry recognizes this problem. The question now is: what are you going to do about it?
Summary
Let’s review the results here:
- On average, engineering leaders believe 60% of late stage design errors could be prevented with better design reviews.
- Large companies believe this to a greater percentage (72%): that late stage design errors could be prevented with better design reviews.
- Nearly 1 in 4 engineering leaders believe better design reviews could prevent more than 80% of late stage design errors.
- In aggregate, engineering leaders have identified the solution to more than half of late stage design changes: better design reviews.
About the survey
To get greater insight into the state of complex product development processes, we commissioned a survey of 250 full-time employees, 50% of which are Engineering Managers or Directors, and 50% of which are VPs or C Level Executives.
Respondents work in the manufacturing industry, specifically in industrial equipment, heavy machinery, automotive, and consumer hardware, and are split across the US, the UK, and Western Europe.
All respondents work at companies with 1,000+ employees that have already invested in a PDM or PLM system.
This report was administered online by Global Surveyz Research, a global research firm. The respondents were recruited through a global B2B research panel, invited via email to complete the survey, with all responses collected during October 2023. The average amount of time spent on the survey was 5 minutes and 44 seconds. The answers to the majority of the non-numerical questions were randomized, in order to prevent order bias in the answers.
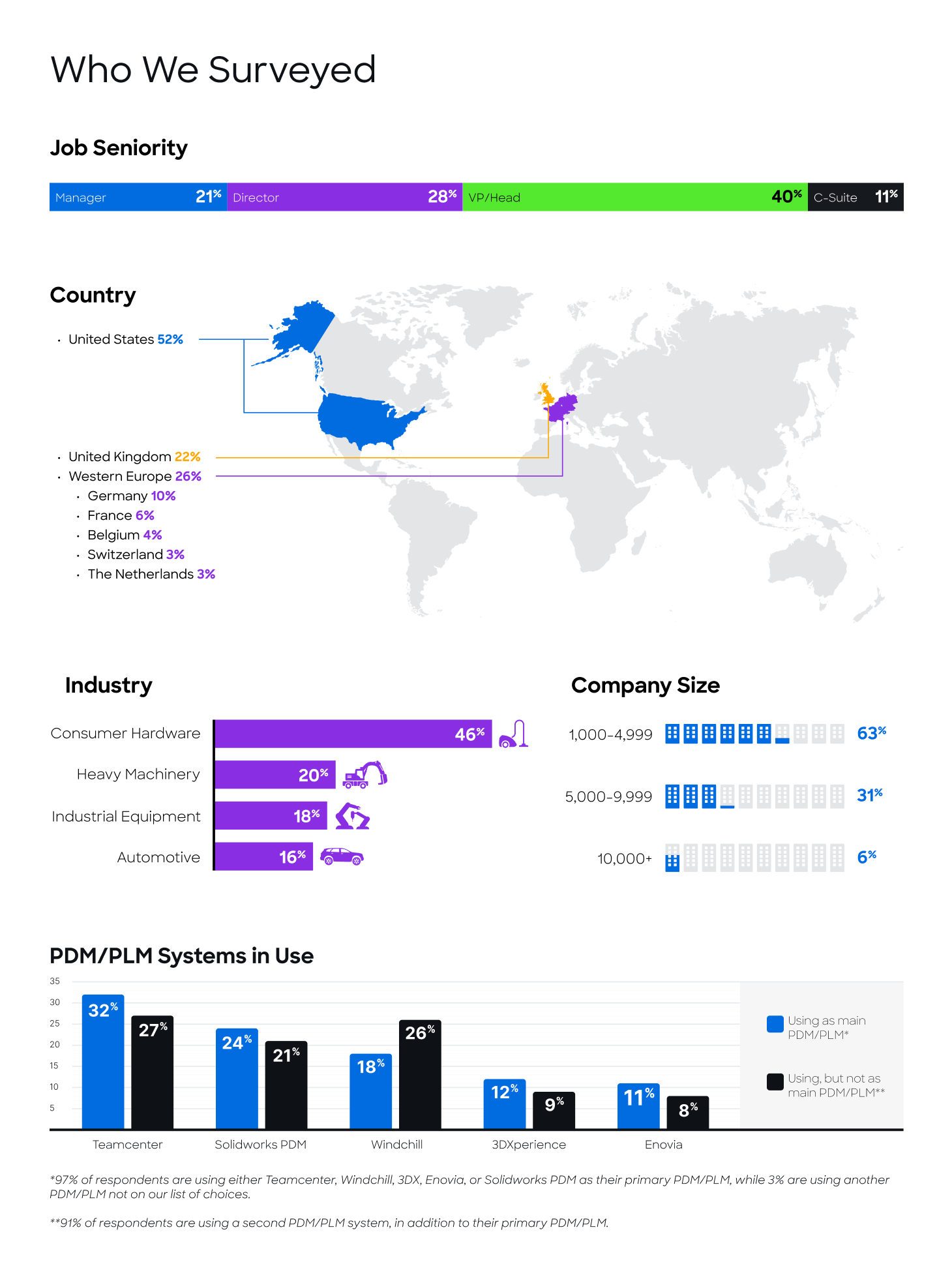
Quantifying the impact of design review methods on NPD
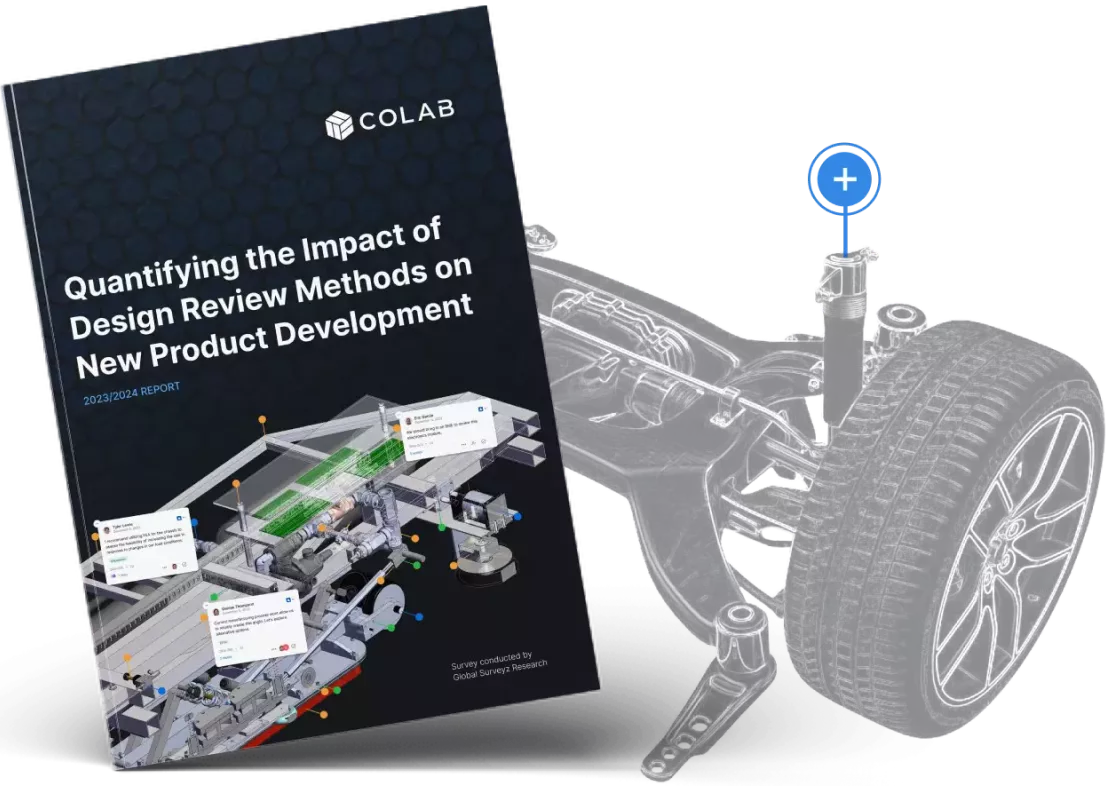