
23% of engineering time spent on non-value-added work
23% of engineering time spent on non-value-added work
This article is part of the CoLab Research Reports series, where we publish findings from both engineering leader surveys and aggregated, anonymized CoLab data. To subscribe and receive reports to your inbox, click here.

“I didn’t go to school to be a PowerPoint engineer.”
We hear this from engineers all the time. And when it comes to engineering leaders, it gets worse.
“I might have 3, 5, 10+ design reviews and NPD projects to track and it takes me hours just to figure out the status of one.”
In short, you’re wasting too many engineering resources on non-value-add work. On average, nearly a quarter of time on non-value-add work. And, 1 in 2 engineering leaders believe it’s anywhere from 20% to 39% of time wasted.
When we look at the tasks that drain time better spent on high value work, it looks something like this:
- Meetings
- Tracking down issues, feedback or other communication buried in disjointed apps
- Waiting: for suppliers, for next steps, for feedback…
Some non-value add work is inevitable. 23% should send off alarm bells.
Non-value-add work: how much is too much?
In manufacturing, non-value add work has clear definitions and measurements. Everything a company and its employees do either adds or does not add value to what your company sells.
In manufacturing, waste is the opposite of value. Because most manufacturing companies abide by lean manufacturing principles, they define waste as follows:
- Waiting (idle) times
- Excess motion (transportation)
- Handling (moving things)
- Excess or useless inventory
- Overprocessing
- Overproduction
- Defects
These waste categories are measurable and therefore improvable.
Engineering is more complex. Because people, as opposed to machines, do much of the work in engineering disciplines, “waste” is a more nuanced topic.
Despite this nuance, one waste category for engineering teams is clear: time.
Time spent in meetings, time spent searching for feedback, time spent providing feedback, time spent waiting – these are all significant sources of engineering time spent. And time wasted.
The question that needs to be answered for your team is: how much time waste can our engineering team realistically tolerate before it starts detracting value from the company.
We’d argue that 23% of time is not just detracting value, but draining value at an almost catastrophic speed.
And when this happens, a few common problems emerge:
- Engineering turnover is high
- Late stage rework
- Project milestones get delayed
- Delayed product launches
- Increase in customer complaints or warranty claims
These seem like manufacturing problems or leadership problems, but, in many cases, these can be traced back to major holes in engineering processes.
Starting with the root cause issue: Design reviews
If we narrow the focus of our discussion to product development, which can include NPD, DFM, and/or VA/VE, the earliest phases are where engineering non-value-add work goes from minimal to peak.
Design reviews are one of the earliest processes in the early phases of product development where engineering teams notice non-value-add work increasing significantly.
This isn’t surprising. Because during design reviews, teams need to collaborate with many stakeholders: other engineering teams, cross-functional teams, suppliers and/or customers.
And it’s during this collaboration where non-value-add work creeps up at a staggering rate.
Meetings, Teams chats, emails – these are the modes of collaboration most frequently used by engineering teams today. It’s also where feedback starts slipping through the cracks.
Schaeffler also noticed this trend and initiated an investment in improving their design reviews. Realizing design review quality is a strong predictor of both product development speed and manufacturing efficiency, Schaeffler focused on reducing non-value-add work during design reviews in three ways:
- First, they wanted to maximize the amount of valuable feedback and action items captured in design reviews.
R&D Business Analyst at Schaeffler, Lewis Bragdon explains, "I've spent a lot of time in design reviews and I’ve seen how information can fall through the cracks.”
Documenting and tracking design review feedback is a major challenge for many engineering teams. Not to mention a significant source of non-value-add work. So, Schaeffler knew this needed to be a priority.
- Second, Schaeffler saw an opportunity to simplify review management, driving speed and efficiency.
Lewis goes on to say, “Time is a really big issue–managing everything: all of the information, action items, who is responsible, the deadlines. We saw the opportunity to have all the information in one place, not have information in so many different locations.” By focusing on making issues easier to find and in a single place, Schaeffler hoped this would eliminate much of the non-value-add work during design reviews.
- Finally, the digitalization team wanted to give Schaeffler engineers an easy way to reference historical design decisions.
They envisioned a system where any engineer could look up why a decision was made, with the context of the CAD version used to make that decision.
Lewis goes on to explain: “There’s confusion that happens when you don't know which iterations of CAD files were considered or when a specific design decision was made. Especially when the only documentation you have was in emails or Teams chats, or a verbal discussion in a conference room.”
This is an especially critical villain of non-value-add work. Often teams have no idea why as assembly was built the way it was built. So, you waste time making the same product mistakes over and over.
To solve this issue, Lewis Bragdon and the digitalization team at Schaeffler knew this would take an entirely new way for their engineering team to work together and with outside stakeholders.
Identifying a solution: Process + Tools
To begin improving design review, it’s important to document where the current process stands and where it can be improved. Furthermore, as part of this documentation, you should be noting the tools your team uses at each stage of the design process.
For most teams, this is CAD for product design, PLM for product data and record-keeping, and then a hodgepodge of tools for facilitating and tracking design collaboration.
This is where most teams need to improve.
Rather than a hodgepodge for collaboration, teams should identify a single platform for this activity. This platform is a Design Engagement System, or DES.
Schaeffler recognized a dedicated system was needed and chose CoLab as the DES to facilitate design collaboration.
Schaeffler’s digitalization team initially launched CoLab to 50 users focused on design review, tooling review, and approval of design guidelines.
Now, Schaeffler teams can:
- Review designs either live or asynchronously. Because CoLab is cloud-based, any reviewer with access can open a model in their browser – without waiting 30 minutes for a model to upload.
- Interrogate CAD and create feedback directly on 3D models. “The way that the conversation happens on the model–it is sort of effortless,” says Lewis. “The interface is easy to use and the tasks can be assigned right there on the model geometry.” With CoLab, any reviewer can manipulate a 3D model and leave feedback right in the context of the markup, no CAD license required.
- Have design conversations with any reviewer any time. Conversations take place in CoLab discussion threads, which are associated with a 3D model and a specific view state. This is essential for communicating design intent and for highlighting high-priority issues.
- Track every comment as an issue – automatically.. “CoLab makes it easy to understand why the design decisions were made and be able to go back and reference that information," explains Lewis. Every issue is cataloged into a searchable, filterable database. Then, when you find an issue you want to investigate, just click it and you’re brought right to the feedback and the file it was left on.
These capabilities are a critical part of reducing non-value-add work for Schaeffler’s engineering team.
And they’re the major reason why Schaefller plans to expand CoLab to their global teams.
What you need to (almost) eliminate non-value-add work
Let’s do a quick summary.
- Too much engineering time is spent on non-value add work: 23% on average.
- Spending valuable engineering resources on-value add work contributes to major downstream issues, like rework, launch delays and engineering turnover.
- Major enterprise companies, like Schaeffler, Komatsu, Ford are shifting their focus to solving the root cause issue of downstream problems – upstream engineering processes.
- The lowest hanging fruit for upstream engineering process improvement is design review.
- A Design Engagement System is the best tool for facilitating a design review process overhaul.
If you’re ready to explore ways your team can (almost) eliminate non-value-add work in the early phases of product development, consider prioritizing the below capabilities that a DES solves for.
Centralized Documentation and Feedback
A key feature of a Design Engagement System is its ability to centralize documentation and feedback. Instead of engineers spending hours searching for lost information or piecing together feedback from various sources, all relevant data is stored in a single location. This centralized approach not only saves time but also ensures that engineers have the most up-to-date information at their fingertips.
Real-Time Collaboration
A DES facilitates real-time collaboration, allowing engineers to communicate and document decisions as they happen. This eliminates the need for lengthy meetings and follow-up emails. Engineers can collaborate on designs, share feedback, and resolve issues in real-time. By minimizing the time spent on back-and-forth communication, engineers can focus more on designing and less on managing information.
Automate Issue Management
Automating issue management is another powerful aspect of a DES. What are manual tasks today, like documenting changes, updating status reports, and tracking progress are automatically done by a DES. This is essential to eliminating one of the greatest culprits of non-value-add work: issue tracking. Automating this not only improves productivity and reduces the risk of errors, it gives engineers time back to do what they do best: engineer quality products.
Detailed Audit Trails
For tasks that require rigorous documentation, such as compliance and audits, a DES provides detailed audit trails. Every action and decision is automatically logged, creating a comprehensive record that can be easily accessed when needed. This feature eliminates the need for engineers to manually compile audit reports, saving time and reducing stress. With detailed audit trails, organizations can ensure compliance and accountability without diverting engineers from their primary responsibilities.
The largest engineering teams in the world are already taking steps to transform the way their engineering teams do design review. And seeing significant downstream improvement as a result.
About the survey
To get greater insight into the state of complex product development processes, we commissioned a survey of 250 full-time employees, 50% of which are Engineering Managers or Directors, and 50% of which are VPs or C Level Executives.
Respondents work in the manufacturing industry, specifically in industrial equipment, heavy machinery, automotive, and consumer hardware, and are split across the US, the UK, and Western Europe.
All respondents work at companies with 1,000+ employees that have already invested in a PDM or PLM system.
This report was administered online by Global Surveyz Research, a global research firm. The respondents were recruited through a global B2B research panel, invited via email to complete the survey, with all responses collected during October 2023. The average amount of time spent on the survey was 5 minutes and 44 seconds. The answers to the majority of the non-numerical questions were randomized, in order to prevent order bias in the answers.
CoLab Research Hub publishes the latest research, tech data and trends to give engineering leaders the resources they need to launch better products, faster.

Quantifying the impact of design review methods on NPD
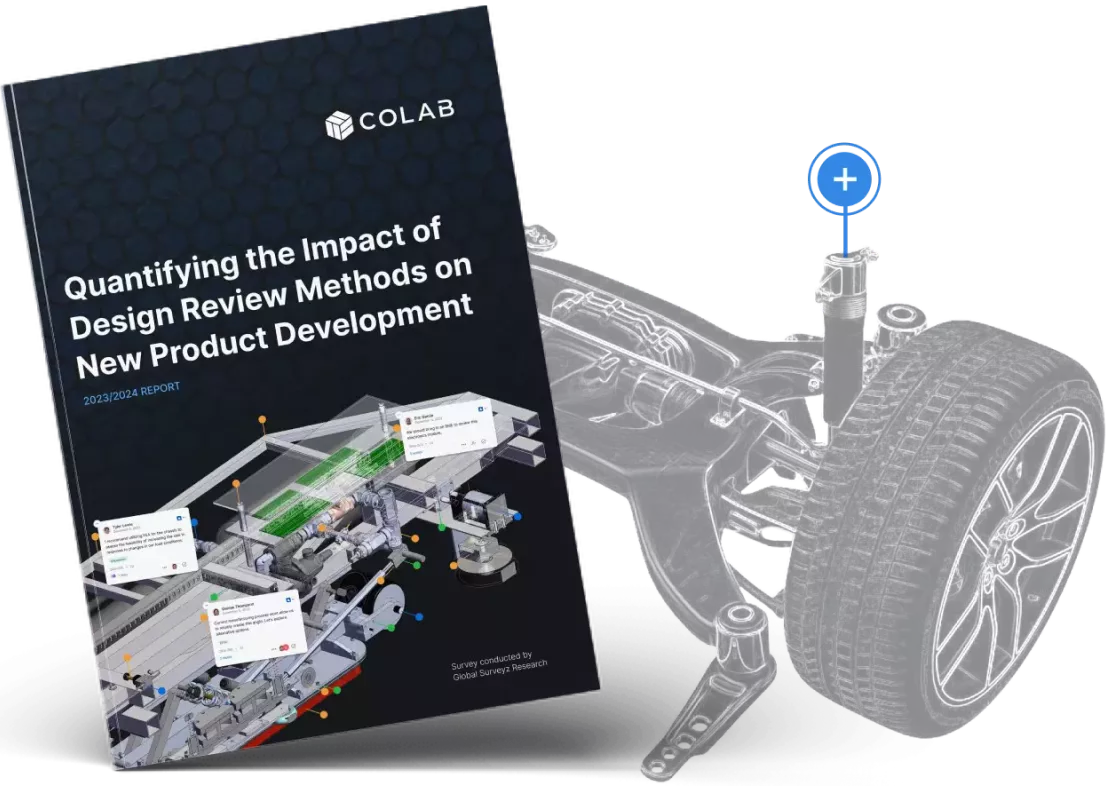