The pressure to do more with less has never been higher for engineering teams.
- More projects launched, less headcount
- More collaboration, less resources
- More cost targets, less components
Not to mention, the PD process itself has never been more complex. Higher complexity assemblies, more global teams involved and increased scrutiny from company leadership.
Define the problem
These problems are not solved with 10% efficiency gains in your current process. Better meetings, better PLM workflows, better markup. These are band-aid solutions.
Engineering leaders today agree that while design review is the #1 predictor of a product launching on-time, 90% of product launches are delayed due to late-stage design changes.
So, what engineering teams need is a complete overhaul of the design review process: a root cause failure analysis. You don’t have time for this, so we did the heavy lifting for you.
The root cause analysis here correlates the root problem with what engineering leaders reveal in research and what engineering teams tell us everyday: design review is the major bottleneck for engineering teams launching products on-time.
.webp)
Collect the data
According to both quantitative and qualitative research, here’s what we know about how teams conduct design reviews today and why it fails.
Despite having a PLM or PDM, most engineering teams do not use these tools for design review.
71% of engineering leaders admit to not using PLM during NPD at all
Engineering teams conduct design reviews in many places – none of which are reliably traceable
“We’re trying to use Teams to share files. Then we do a Teams meeting and screen share CAD. Sometimes people speak up, sometimes they don’t. It’s a mess, honestly.”
Because teams document design feedback in untrackable places, most feedback is lost and never actioned
43% of all design feedback is never documented, and therefore never addressed
Because design feedback is lost, engineering teams delay product launches and miss major top-down targets.
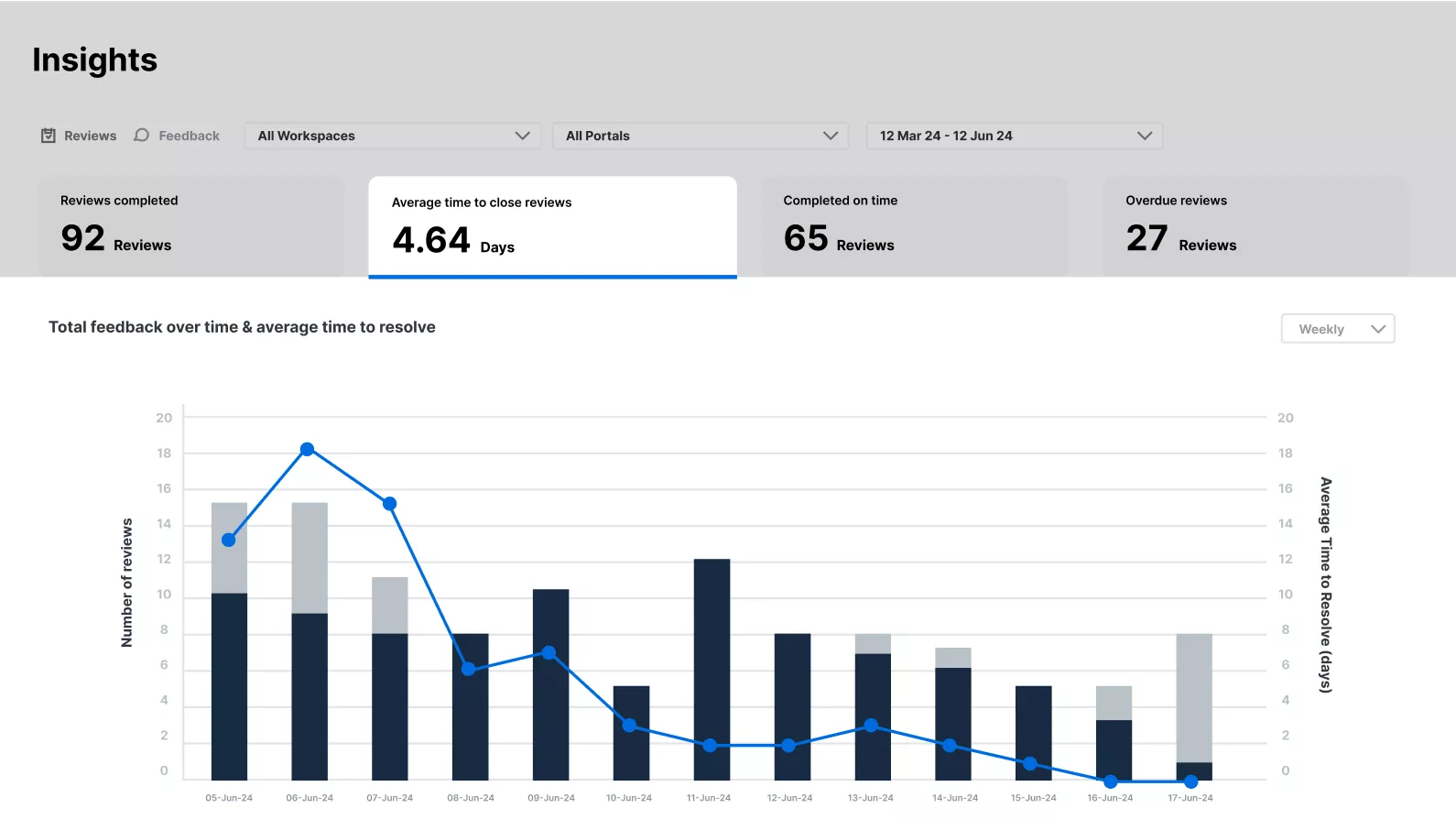
Identify the root causes
The reason design reviews fail is engineering teams do not have a single tool for documenting and tracking design feedback and decision-making.
More than half of all engineering leaders agree that better tools are needed to:
- Document design feedback
- Manage product data
- Communicate design intent
- Track and implement design feedback
- Communicate design changes
And this makes sense.
When we look at how engineering teams conduct the entire product development process: they have CAD for interacting with product designs, PLM for housing product data… and nothing in-between. No tool or system for engineers to interact with other engineers.
So this is why teams work outside CAD and PLM during PD cycles. Because there’s no place for them to go just to do design reviews.
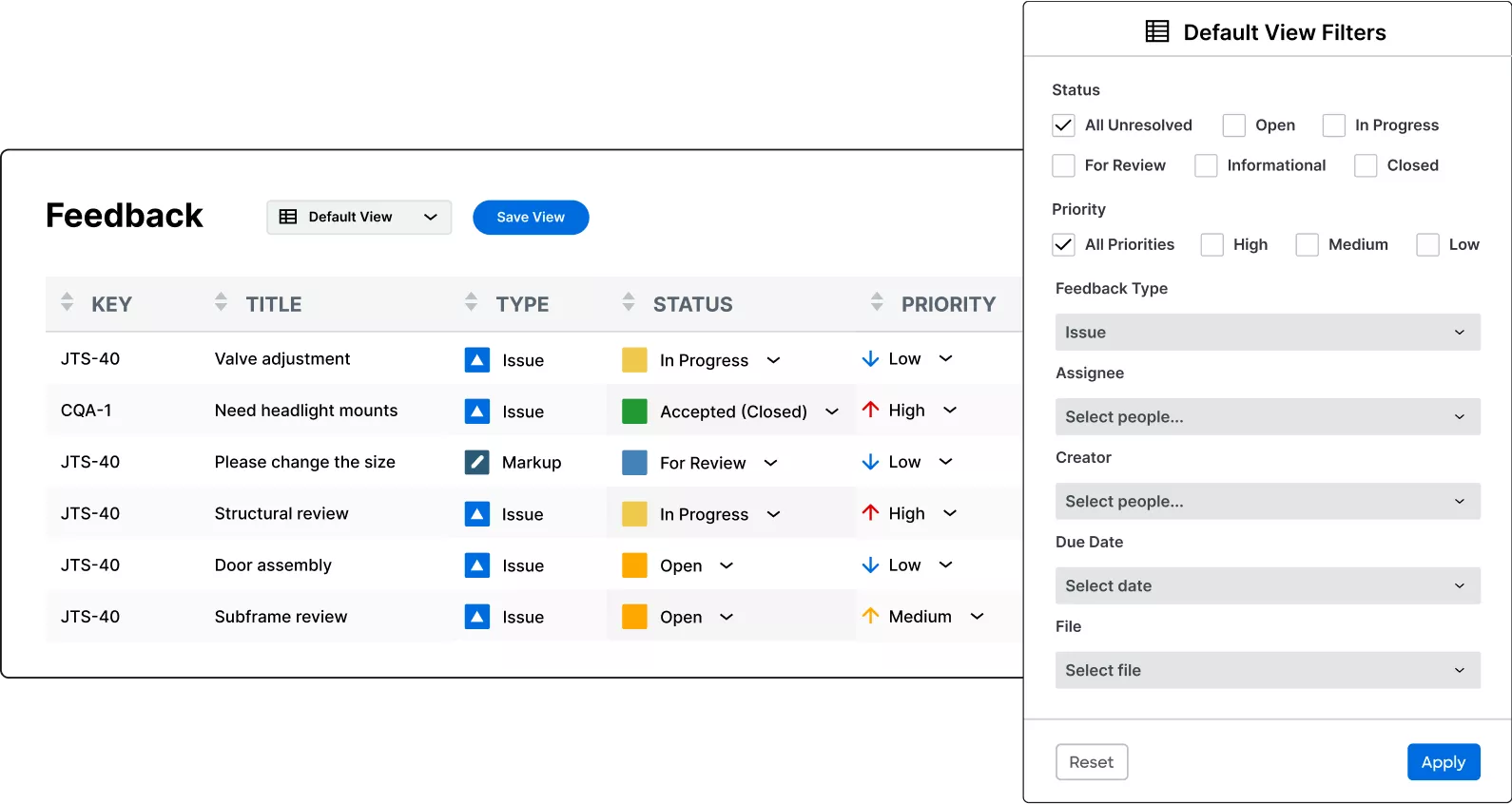
Investigate solutions
The question remains: what is the tool or system for design review?
It’s a Design Engagement System, or DES.
A DES is a system purpose-built to help people engage – not just with data, but with each other – to make great design decisions. And when it comes to a DES, CoLab is the only one selected by companies like Schaeffler, Ford Pro, Hyundai, Komatsu and Polaris.
These companies choose CoLab because, like a DES, it’s purpose built for fast, effective design review. Using CoLab as their DES, multiple engineers, designers, and other stakeholders can review designs together and build off one another's feedback.
CoLab makes it easy to review the right data – 3D models and 2D drawings – with all the right people, capture useful feedback, and track issues through to action. CoLab pulls together design discussions previously lost in emails, spreadsheets, and notebooks into a single platform that integrates back into PLM.
Moreover, with CoLab’s customer support team, no engineering team is left to configure these processes alone. Your CoLab team is a partner throughout your DES journey.
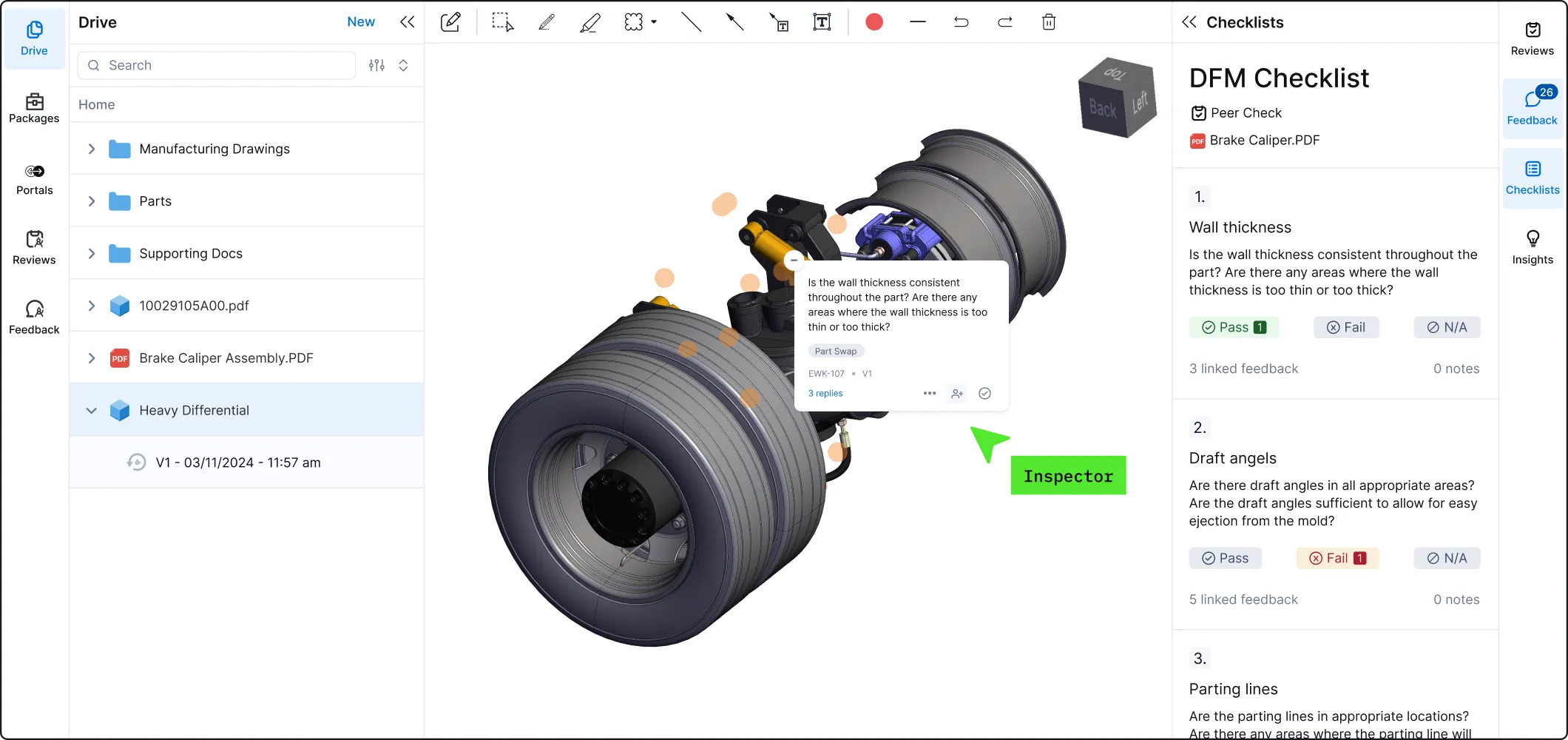
Engineering teams are transforming how they work with CoLab
What’s next?
If you’re ready to see how a DES can transform the way your engineering team works, here’s how the process works with CoLab.
- Every conversation starts with a discovery call. During this call, a technical expert will understand your team’s challenges with design review today
- Then, we’ll tailor a demo to address those challenges. This demo includes you, of course, but also some key members from your team who can speak to your challenges in greater detail and vet CoLab as the solution.
- Finally, we do a workshop with more members of your team. This is the fun part! During this workshop, your team will each have temporary CoLab licenses and participate in a sample design review. You and your team will be guided through key features and use cases right inside the CoLab platform.