The way you’re doing design reviews is holding you back
Engineering teams are expected to achieve more with the same resources while also being held back by traditional ways of working. We call this Design review 1.0, the status quo, and it results in subpar products.
We want you to run your best design reviews ever. And you can, with Design Review 2.0
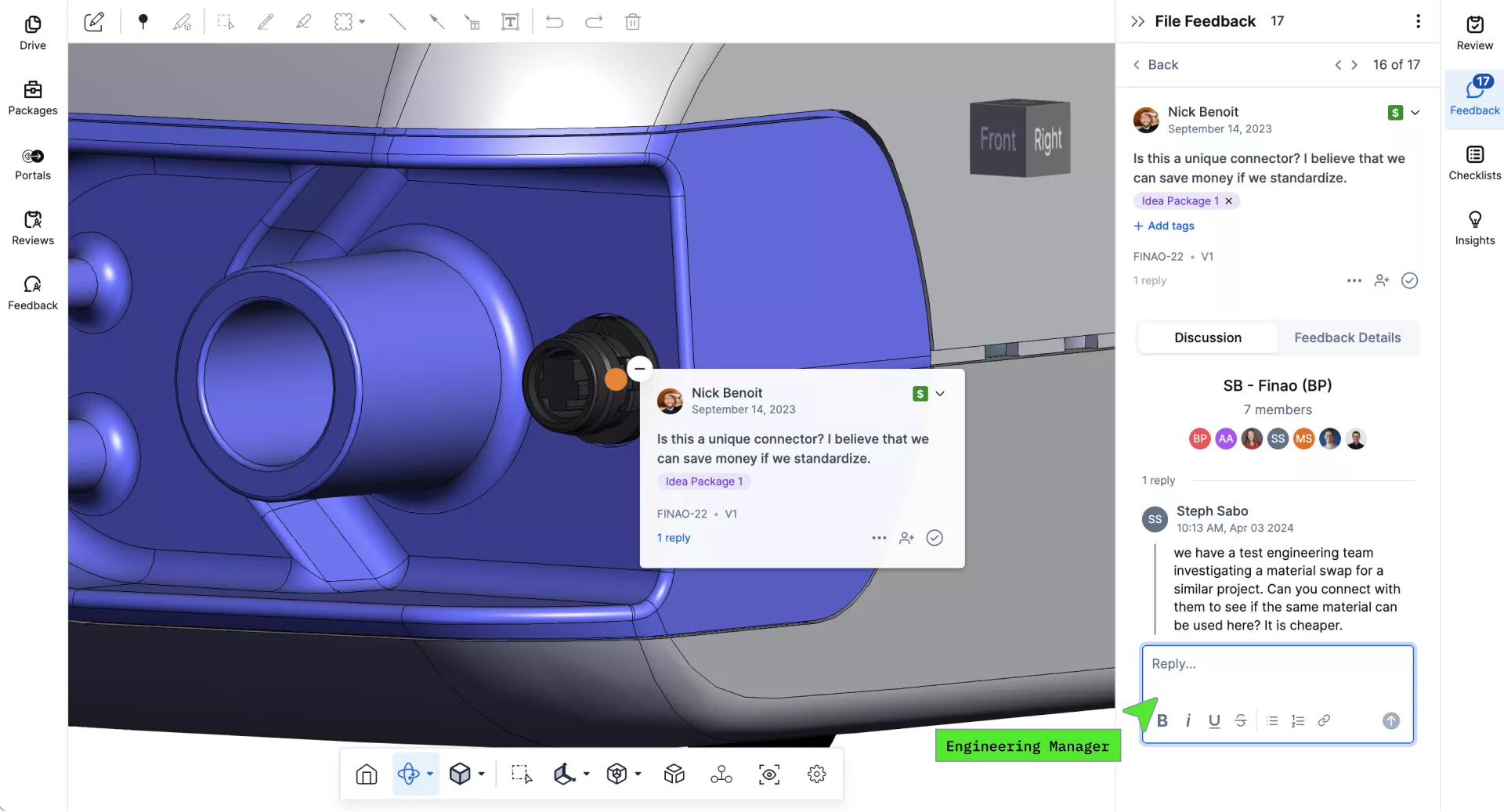
Your most critical product decisions are made everyday in design reviews.
But as teams and assemblies get more complex, the way teams conduct design review looks the same as it did 10-20 years ago.
Then, what happens?
- 43% of design feedback is never actioned or addressed
- 90% of companies are seeing product launch delays due to late-stage design changes.
- Most engineering leaders agree that better design review would prevent late stage changes
These aren’t problems that are solved with more meetings, better PLM workflows or increased pressure to keep PowerPoint design review decks and spreadsheets up-to-date.
These are problems that require a completely new way for engineering teams to work together.
If you want to keep doing design review the way you’ve always done it, you don’t just have frustrated engineers or long PD cycles. You have quality testing failures, expensive ECRs, high warranty claim volume, loss of customer trust, and high engineering turnover.
Design Review 1.0 is the status quo. Design Review 1.0 is design decisions lost in email threads, hours-long issue generation meetings, frequent late stage design changes.
Design Review 1.0 is why CoLab exists. CoLab is Design Review 2.0.
“The way we were doing our work is the same way that everyone else has traditionally been doing their work. Take screenshots [of a design], put that into a slide deck, and send that slide deck around for comments. Then you’re getting 10 people in a conference room for an hour. That's how we were doing things, but we knew there had to be a better way.”
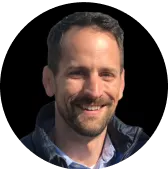
Introducing Design Review 2.0
Design review effectiveness (quality + speed) is the #1 predictor of product development velocity. We want to help you run your best design reviews. So, your team can work together better. Here’s what that looks like:
When you make active participation easy, you maximize useful feedback.
Design review meetings should be your best opportunity to generate problem-solving ideas. Instead, they often become long meetings where only a few people participate and it’s only to point out more issues. It makes sense: only the person screen sharing CAD can really interrogate the model. They are doing a design review and everyone else is just watching one.
Using CoLab, everyone can interrogate the model on their own screen, while seeing other people’s feedback populate in real time. It’s engaging – and dare we say fun? Teams who use CoLab generate more feedback from more participants.
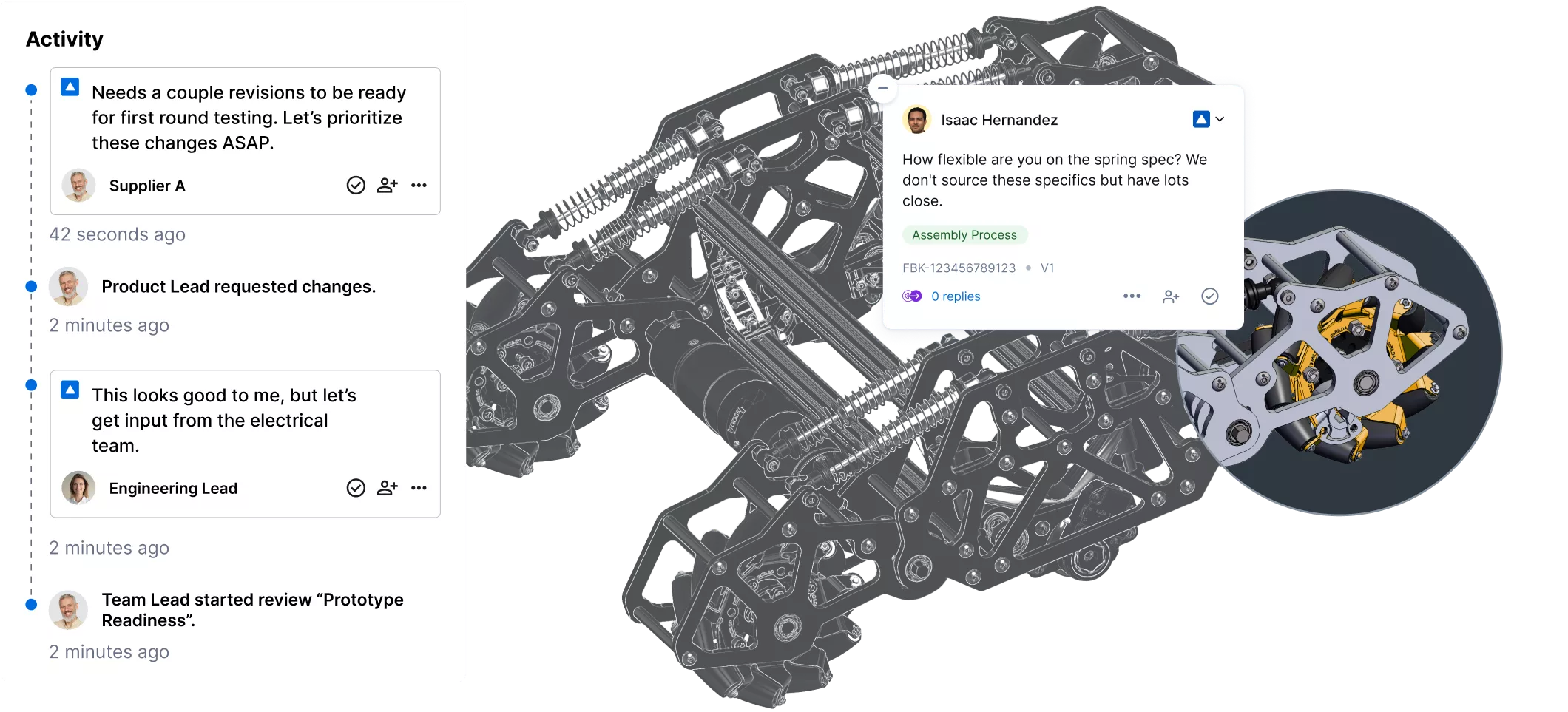
Thoroughly documenting feedback shouldn’t be a chore.
Most teams document their design feedback in spreadsheets, emails, or PowerPoint slides. Some teams even use free CAD viewers with markup features.
Problem is – this approach turns documentation into an administrative task. The more thoroughly you document, the more work you create for yourself and your team. And the more places they need to sift through to find the information that matters.
It disincentivizes thorough documentation and leaves room for errors to slip through the cracks.
With CoLab, reviews and decision making get tracked automatically as you do the work. Engineers can do what they do best, and CoLab will support them with record-keeping in the background.
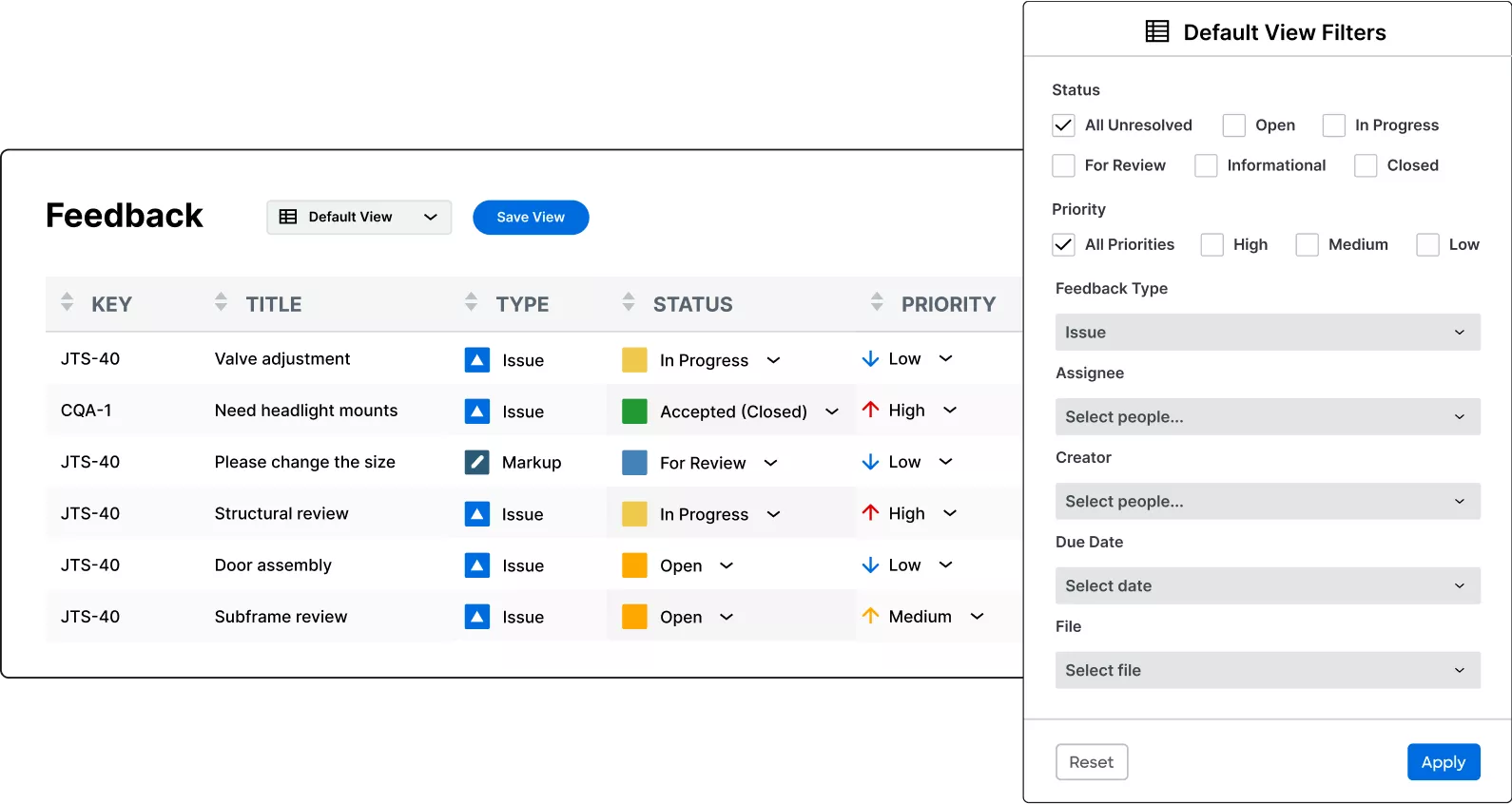
Engineering teams get the data to objectively improve the review process.
Pinpointing bottlenecks in the review process – or understanding the real impact of continuous improvement – has always been a challenge. Why? Because engineering work takes place across untrackable communication channels. It’s not auditable, and you can’t get data on what’s happening and why.
CoLab’s gathers data about all of the human-to-human interactions that power your product decision making. That means you can objectively improve how your team evolves a design from concept to production validation.
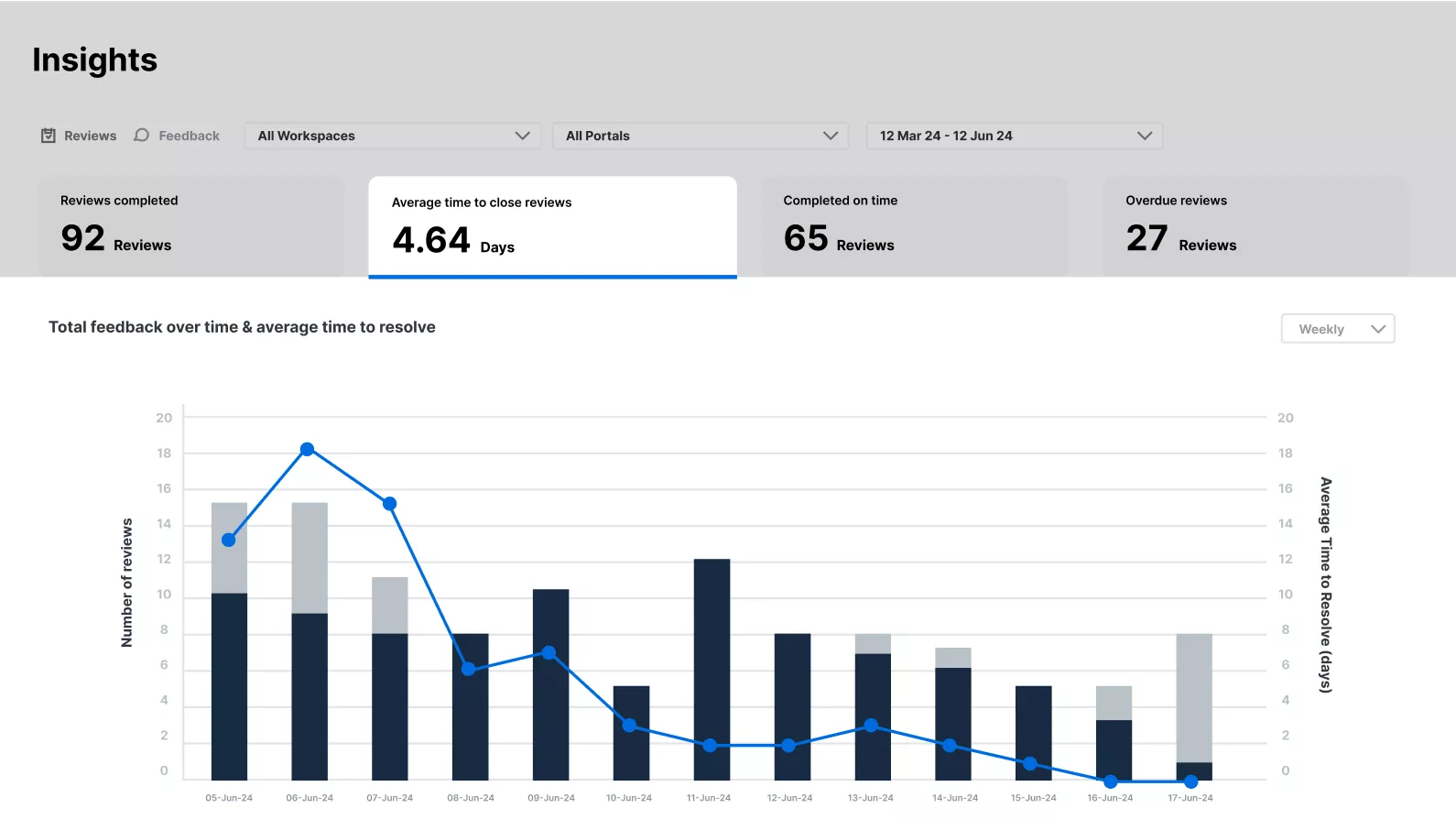
Design Review 2.0 enables you to:
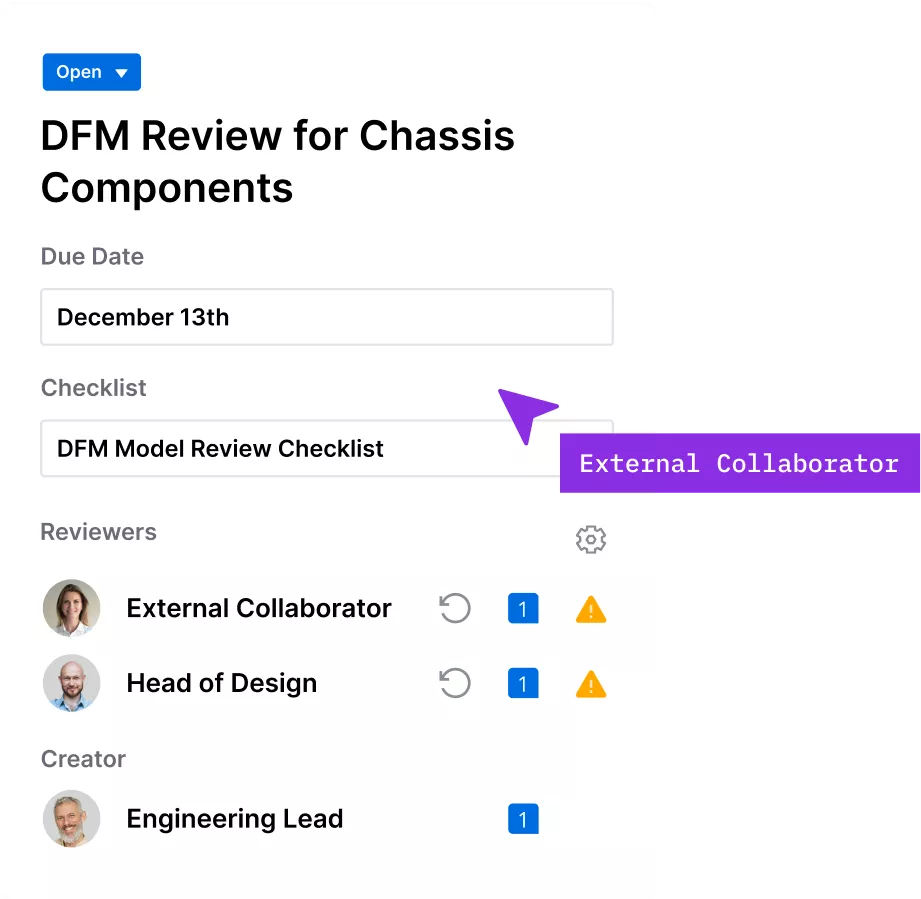
Engineering teams are transforming how they work with CoLab
What’s next?
If you’re ready to see how a DES can transform the way your engineering team works, here’s how the process works with CoLab.
- Every conversation starts with a discovery call. During this call, a technical expert will understand your team’s challenges with design review today
- Then, we’ll tailor a demo to address those challenges. This demo includes you, of course, but also some key members from your team who can speak to your challenges in greater detail and vet CoLab as the solution.
- Finally, we do a workshop with more members of your team. This is the fun part! During this workshop, your team will each have temporary CoLab licenses and participate in a sample design review. You and your team will be guided through key features and use cases right inside the CoLab platform.