Communicating design intent: strategies for effective collaboration with local and global suppliers
Transitioning to work with local and global design partners presents unique challenges and opportunities. Eric Burbank will explore how to enable partners to efficiently focus on their expertise while sharing internal knowledge and insights. He'll demonstrate how iRobot leverages CoLab for design feedback, alignment, and concept sharing. Additionally, Eric will address the crucial aspect of change management, offering actionable tips from his extensive experience in organizational transformation.
Eric Burbank is the Mechanical Engineering Manager for New Product Development at iRobot. As an enthusiastic consumer product leader, Eric brings a creative drive to solve problems and a big-picture perspective. He has led the ideation, engineering, design, manufacturing ramp, and launch activities for numerous robotic vacuum cleaners, developing a deep understanding of customer value and targeted feature sets. Eric is also passionate about making work an enjoyable and engaging environment where teams can thrive.
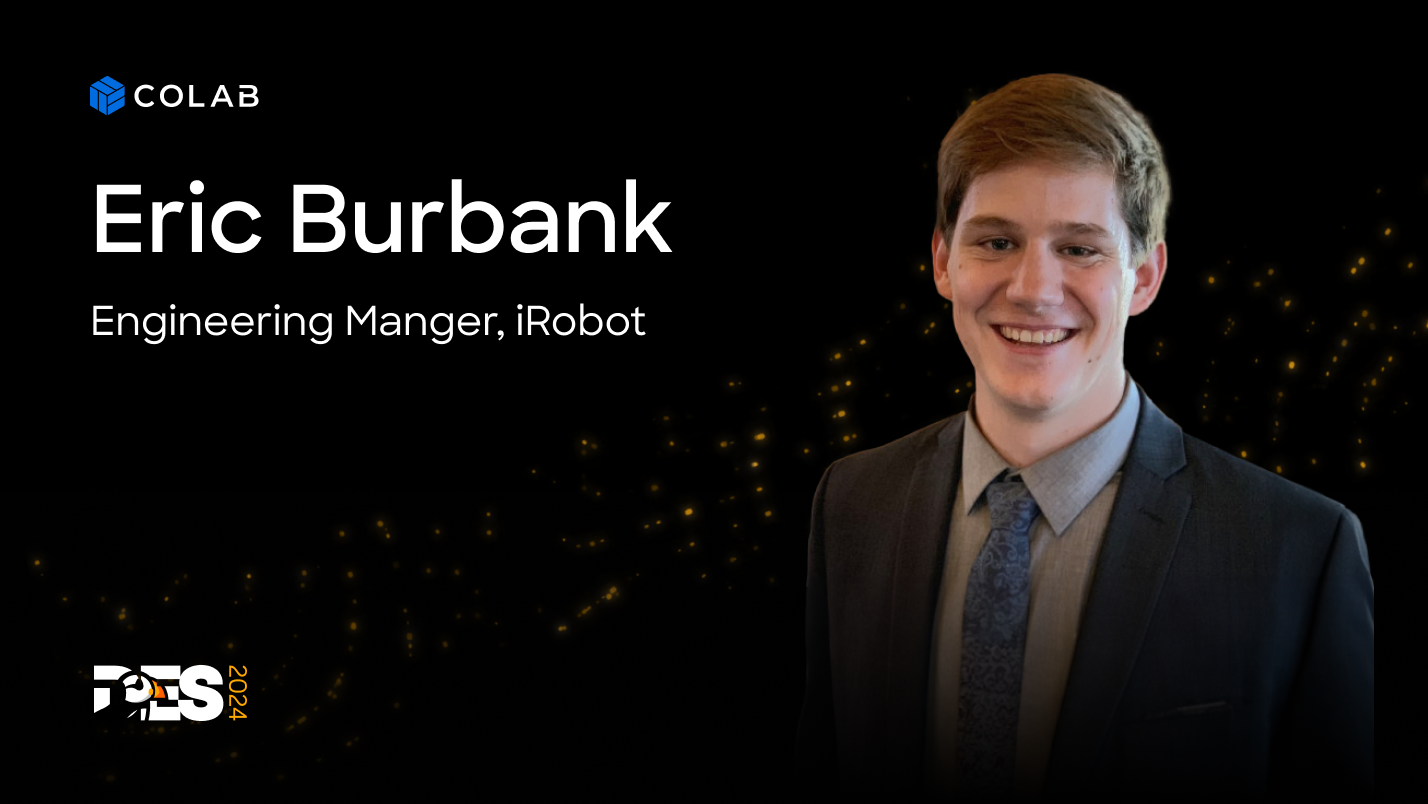
Eric Burbank, Mechanical Engineering Manager for New Product Development at iRobot, shared his experiences and strategies for integrating ODM (Original Design Manufacturer) and OEM (Original Equipment Manufacturer) partners into iRobot’s development processes. With a focus on improving efficiency and leveraging external expertise, Eric highlighted the importance of clear communication, organizational alignment, and adaptable processes. His talk provided valuable insights into navigating the complexities of transitioning from in-house engineering to collaborative partnerships while maintaining product quality and innovation.
Key Insights
Transitioning from In-House to ODM/OEM Collaboration
- Shifting to External Partners: As iRobot moved from traditional in-house engineering to leveraging ODM and OEM partners, the organization faced challenges in communication, quality control, and maintaining product integrity. Defining clear roles and expectations was essential to making this transition successful.
Core vs. Context Work
- Understanding Strengths: iRobot identified areas of core competency, such as product testing and system design, and contrasted them with context work, like component sourcing and manufacturing, which could be outsourced to partners. This clear distinction allowed iRobot to focus on their strengths while relying on partners for complementary expertise.
Efficient Design Review Processes
- Leveraging Collaborative Tools: Using tools like CoLab, iRobot improved their design review processes by enabling more effective communication and reducing manual work. This facilitated a seamless exchange of design feedback between internal teams and external partners, reducing errors and accelerating development cycles.
Challenges in Maintaining Design Integrity
- Ensuring Consistency and Quality: Outsourcing parts of the design process introduced complexities in maintaining design consistency and meeting quality standards. Eric emphasized the importance of having robust processes and frequent touchpoints to ensure that partners adhere to iRobot’s stringent requirements.
Tactical Tips
Clearly Define Core and Context Areas
- Assess Your Expertise: Distinguish between areas where your organization excels (core) and areas that can be effectively handled by partners (context). This clarity helps in deciding what to keep in-house and what to outsource, ensuring that your internal resources are used optimally.
Implement Collaborative Tools for Design Reviews
- Streamline Feedback: Use platforms like CoLab to centralize design reviews, allowing for better tracking, reduced manual effort, and faster iteration cycles. This helps in maintaining alignment and avoiding the pitfalls of fragmented communication.
Invest in Leadership Alignment and Support
- Secure Top-Down Sponsorship: Leadership approval is different from active sponsorship. Ensure that leaders not only approve new processes but are actively involved in supporting and communicating these changes across the organization.
Foster a Culture of Adaptability and Learning
- Be Open to Evolution: Transitioning to ODM/OEM collaboration and adopting new tools is a learning process. Encourage teams to share experiences and learnings openly, and be willing to iterate on processes based on feedback.
Prepare for Organizational Resistance
- Manage Change Proactively: Moving to a collaborative model can be met with resistance from teams used to traditional processes. Implement change management strategies that include clear communication, training, and support to help teams adapt.
More of
Presentations
Sign up for Design Engagement Summit 2025
Join industry leaders and innovators for a day of creativity and collaboration. Don't miss out on this exclusive event!