What happens when one company fixes their design reviews and the other one doesn’t?
Find out what happens to company B...
This is the story of two hardware companies.
Both of their engineering teams are feeling overwhelmed by the amount of admin work required to complete even the simplest design reviews. And as products get more complex every year, the bottleneck keeps getting worse. Review cycles are getting slower and errors are slipping through the cracks.
One of these companies (we’ll call them Company A) decides to invest in fixing the root cause
They start small, picking one new product development program and focusing on reviews in the middle of their Stage Gate process. Here’s how things started out:
Reviews had to take place in meetings, because it was the only way to show cross functional teams the CAD. So they were having lots of long meetings, with one person sharing their screen, and everyone else asking, “can you turn the model this way?” or “can you zoom in there?” One person would get stuck taking notes – usually by marking up a Powerpoint presentation with CAD screenshots in it. After the meeting, they’d have to comb through the Powerpoint to make sure all the issues got resolved. And if any of these admin steps were missed, issues would slip through the cracks.
.webp)
First, they fix their design review pre-reads
Company A invests in a software that lets them share CAD ahead of their meetings. The software lets you open CAD in your web browser, so you don’t need any special licenses or a powerful computer to use it. By clicking a link in their email inbox, reviewers are brought straight into an interactive review environment – with a simple toolbar for exploring the CAD.
Now their engineers can review CAD before their design review meetings. They have time to quietly, thoughtfully identify issues. They can even resolve simple issues before the meeting begins. This gives them the opportunity to focus on complex issues or trade offs during live meetings.
The manufacturing and supply chain teams like the system too. Now they can point out risks – like a part not being toolable – by commenting directly on the model. They don’t have to wait for the production drawing to show up on their desk for redlines. They have a seat at the table early in the process.
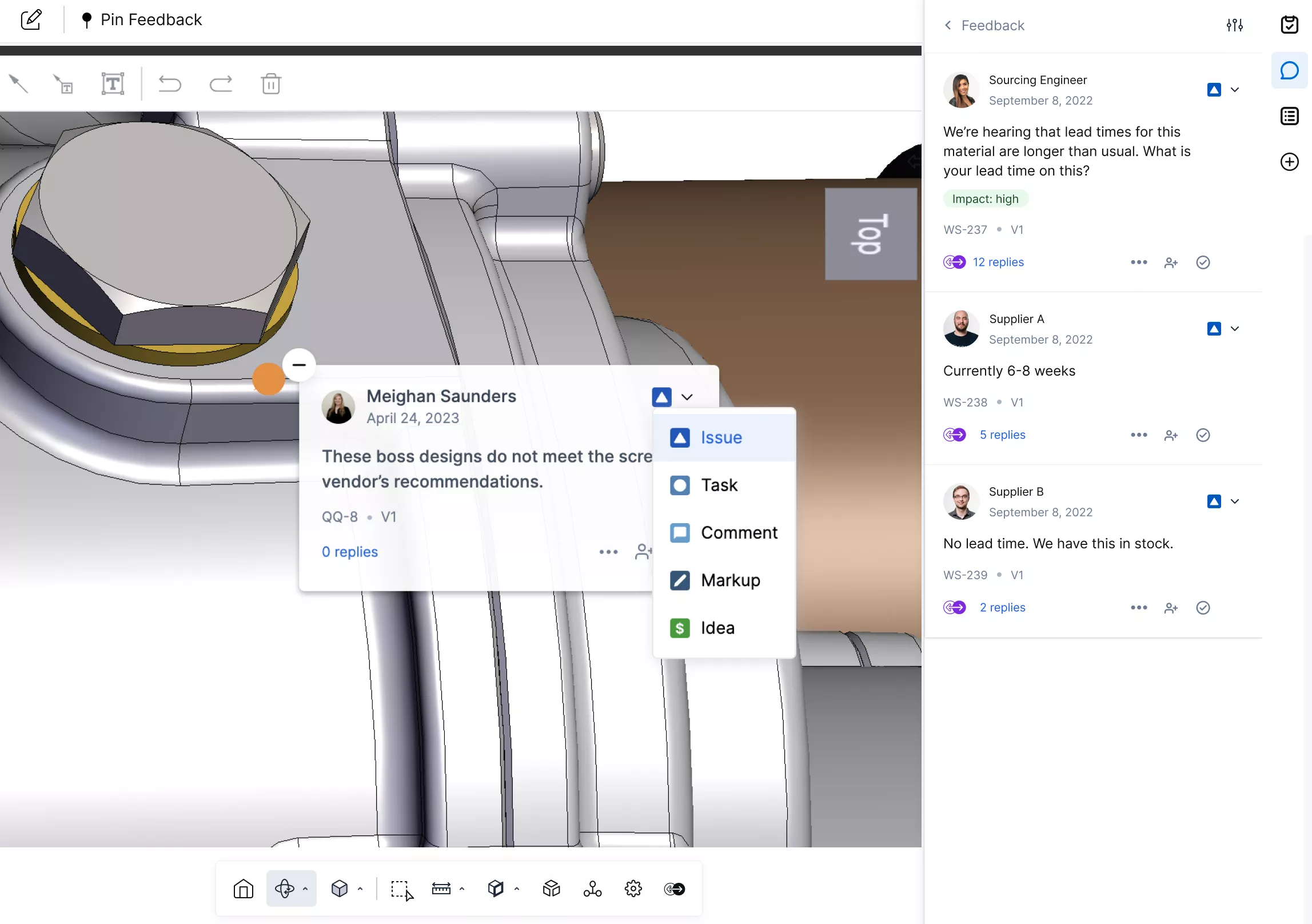
They also improve documentation and tracking
The new system also eliminates a lot of the admin work that the engineering team has gotten used to slogging through. Now, issues are documented and organized automatically as a byproduct of completing the review in the interactive workspace. Every comment is saved with the view state the reviewer saw when they made the comment. So design intent is always clear.
Managers can keep track of which reviews are in progress and complete. And they can assign issues to team members to ensure they get resolved. Instead of making spreadsheets and Powerpoints all day, their engineers can focus on solving problems.
.webp)
For Company A, things start getting better
Within weeks, engineers are feeling happier and more productive. Review cycles start to speed up – issues that used to take 6-8 weeks to resolve are fixed within days. Everyone feels like they are covering each design in more detail – higher quality reviews.
Within a few months, as their NPD projects move into the pilot build phase, they start seeing even more impressive results. It turns out, they did cover those designs in more detail. And as a result, they caught more errors earlier. Pilot builds start going more smoothly, with fewer rework cycles.
They launch new products on time. Customers love the products, because they are high quality. And Company A sees very few RMAs or warranty claims. Their gross margins for the new product are strong, and they can reinvest some of that money back into R&D.
Company B decides to stick with the status quo
Sure, their engineers complain about early morning and late night meetings with suppliers. And they do spend a lot of time on Powerpoints and spreadsheets. But it’s not that big of a deal, right?
Company B keeps relying on meetings to find issues. Some of their engineers engage and chime in on these meetings, but some stay quiet. Sometimes, the manufacturing team is able to join and provide their feedback. But other times, they’re just too busy.
They keep documenting issues using Powerpoint – or a free CAD viewer – then discussing how to resolve them in more meetings (or over email). Sometimes, they receive comments back on an outdated version of the Powerpoint, so they have to do the work over again. Sometimes, a critical issue gets buried in an email chain and pops up again later during a pilot build.
.webp)
For Company B, things get worse
Design cycles take longer than initially planned. Then, the team has to go through several rework cycles, to fix the issues that slipped through the cracks. They rework models and drawings and reorder parts from their suppliers. Then they rework the prototypes to resolve the issues.
Finally, they launch their product to market – just a little late. The product does OK, but they run into a few quality issues. RMAs and warranty claims drag down their gross margins, so they have less money leftover to reinvest in new product development for the next generation product.
%20(Medium).webp)
Over 5 or 10 years, these differences compound
Years later, if you compare Company A and Company B, you’ll see two very different businesses. Company A has a strong track record – not only of launching products on time, but launching quality products that customers love. Meanwhile, Company B launches fewer products, because their early launches created too much sustaining engineering burden on the back end. After years of compounding impact, it will be hard for Company B to catch up to Company A.
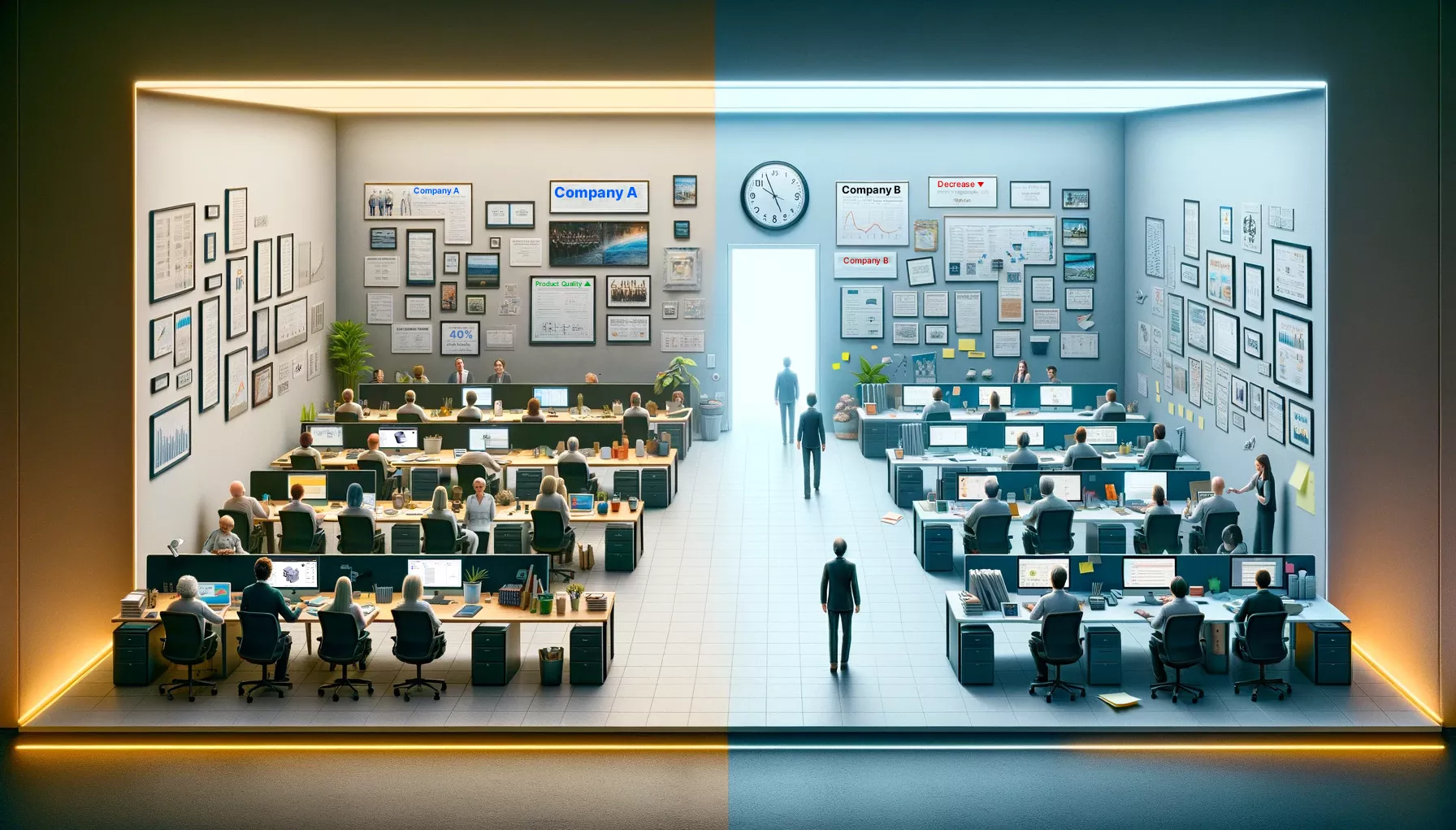
How engineering teams work together matters
Your most important product decisions are made everyday in design reviews. And as products get more complex, you need more specialized expertise from people located all over the world. Many companies have not reinvented how they approach reviews to account for globalization or complexity. So today, these reviews are a bottleneck – and a place where issues frequently slip through the cracks.
We built CoLab to help teams reinvent how they work together and make decisions, so they can build better products faster.
Engineering teams are transforming how they work with CoLab
Better products start with better design conversations.
If you’re ready to see how CoLab can transform the way you work with suppliers, here’s how the process works.
- Every conversation starts with a discovery call. During this call, a technical expert will understand your team’s challenges with design review today
- Then, we’ll tailor a demo to address those challenges. This demo includes you, of course, but also some key members from your team who can speak to your challenges in greater detail and vet CoLab as the solution.
- Finally, we do a workshop with more members of your team. This is the fun part! During this workshop, your team will each have temporary CoLab licenses and participate in a sample design review. You and your team will be guided through key features and use cases right inside the CoLab platform.