Most manufacturing companies are missing their biggest opportunity to improve product quality.
You know quality is critical: it drives gross margins, customer satisfaction, and much more. And you’re probably doing a lot to improve quality already. But are you doing everything you can? Many hardware companies are missing one of the biggest opportunities to increase quality, because it’s hiding upstream of where they usually look for quality opportunities:
In their engineering design process.
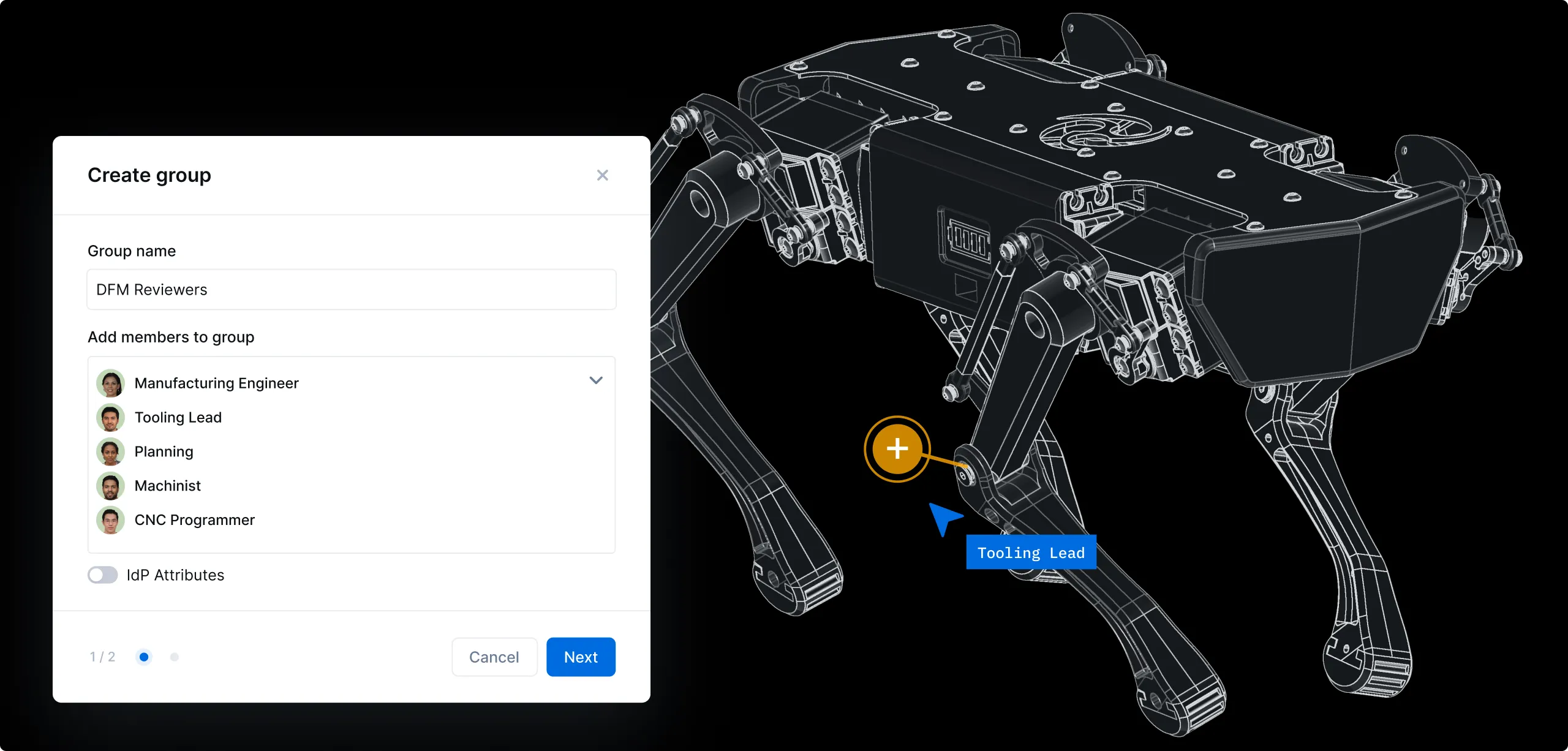
Design quality drives product quality
Engineering and manufacturing leaders know that design quality is crucial to product quality. But day to day, most companies spend way more time optimizing their manufacturing processes for quality than they spend optimizing their design process for quality. As a result, we are left with robust manufacturing processes, while issues and errors in design are still slipping through the cracks.
Here’s a stat that might surprise you:
According to a survey of 250 engineering leaders, 43% of issues identified during design reviews are never documented or addressed.
That’s too many opportunities for a quality issue to make it into production. And we know why it’s happening.
What if you could fix quality issues before they happen?
You can. And it starts by fixing the leakiest part of your quality funnel: upstream, during new product development, when valuable design feedback that can prevent quality issues goes unnoticed.
But why is that happening? There’s two reasons:
First, you’re not including the right subject matter experts (SMEs) in critical design reviews.
Quality is a team sport. And design quality can’t be the sole responsibility of the engineering team. What if your quality team, your production team, and even your suppliers have valuable expertise that you’re not tapping in to?
The fact is: most design teams aren’t tapping into this cross-functional expertise. For example, only 20% of engineering teams report that they get useful design feedback from most or all of their suppliers.
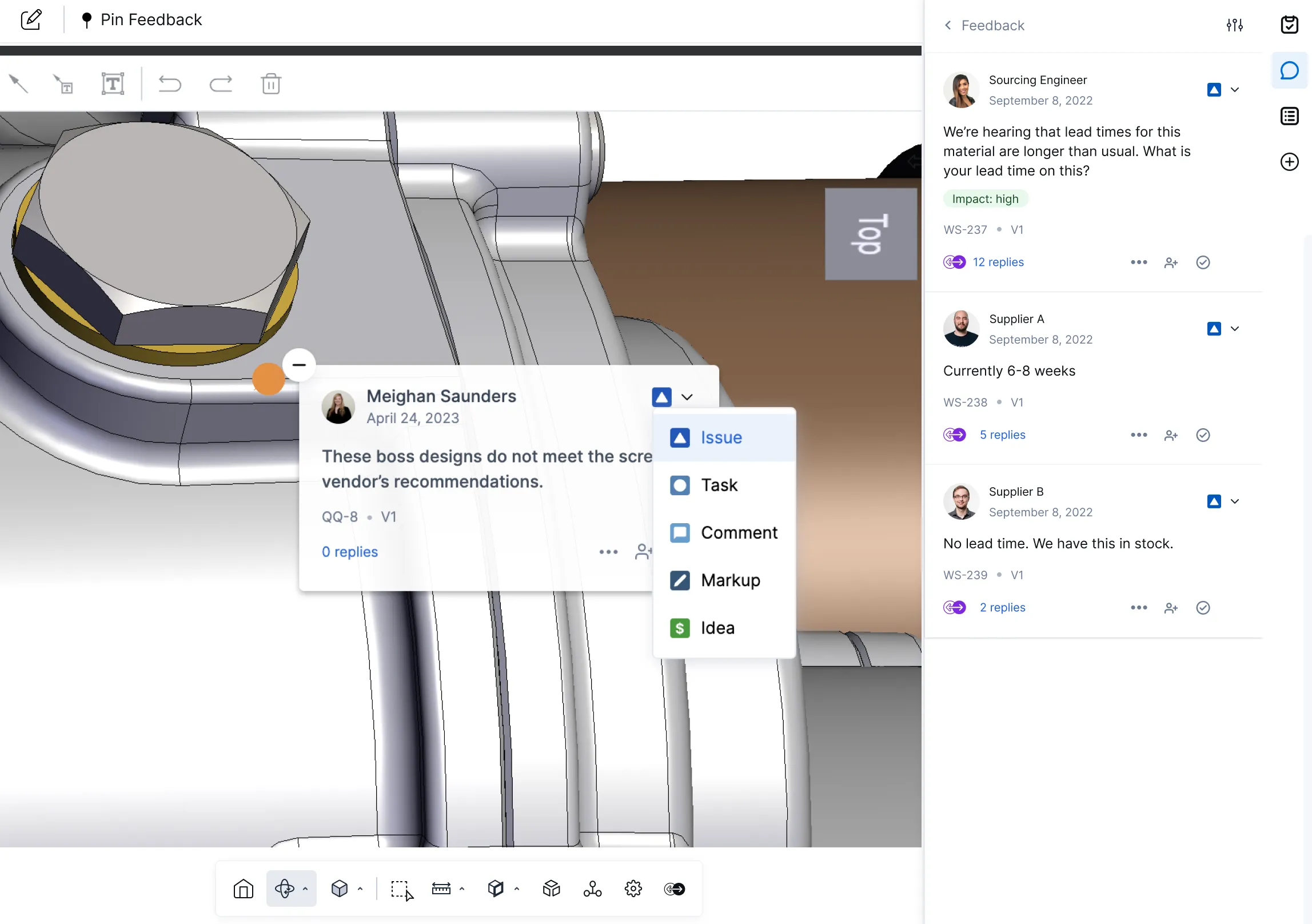
At the end of the day, there’s just not a lot of options to get this feedback:
You can organize a big meeting, but it can take weeks to align everyone’s calendars. Outside of meetings, cross functional team members often don’t have access to CAD. So they’re left waiting until there’s a production drawing. And at that point, a lot of design decisions have already been locked in. The few teams that do try to bring cross functional SMEs into the design process early are stuck using workarounds, like Powerpoint slides with CAD screenshots. These workarounds are not only a pain to set up, they’re a pain to keep track of. What happens when there’s a new version of the CAD? The whole PowerPoint becomes obsolete in a second.
There’s a better way:
Imagine if you could securely share the latest revision of CAD with anyone - whether they have a license or not. Imagine if reviewing a design and leaving feedback was as simple as…
- Clicking a link in your email and opening a web browser like Google Chrome
- Browsing a model and looking for any errors (or potential quality issues)
- Dropping a pin and writing a comment if you find anything
With CoLab, it is that easy:
Second, documenting and tracking design review feedback is too admin intensive.
We’ve heard from plenty of manufacturing teams who tell us that they do give feedback during product development. But in the end, they keep seeing the same errors that they’ve already pointed out. It’s not that the engineering team doesn’t care. There’s a reason why 43% of feedback from design reviews never gets actioned:
- Feedback is captured in handwritten notes, Excel spreadsheets, and emails – without any context to help clarify design intent. This makes it impossible to follow up later.
- Sometimes, the engineering team goes through the trouble of taking screenshots of CAD, so reviewers can mark them up in Powerpoint. But these screenshots can quickly become out of date.
- If feedback requires more discussion, that often happens over email – with no centralized tracking, it’s really easy for things to get lost.
This is why, when you do a review in CoLab, the software tracks and organizes everything automatically for you, as a byproduct of doing the work. Through automation, we’re helping engineering teams action the 43% of issues that normally slip through the cracks. See how it works!

Integrations
You don’t need yet another disconnected software solution. That's why CoLab does two things:
- It integrates with your CAD and PLM software to create a connected tech ecosystem.
- It replaces the 5-10 apps you use to complete a single process workflow with 1-2 apps (CoLab + PLM, for example)
CoLab supports more than 70 file types, including native and neutral CAD and integrates with many PLM/PDM systems.
Aside from engineering system integrations, CoLab also integrates with Jira and supports security protocols, like SSO, user permissions and more.
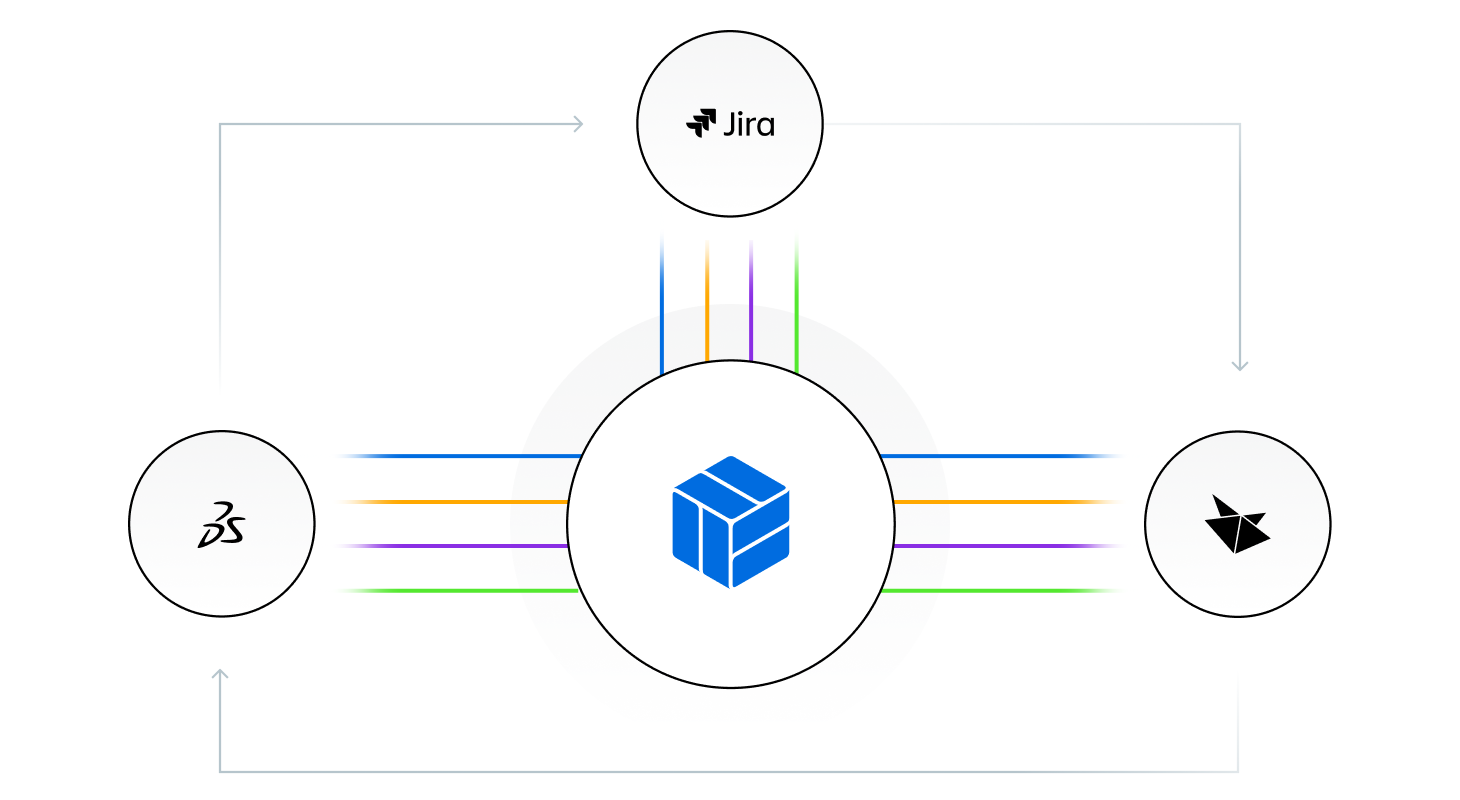
Case Studies
“ISO certification focuses on documentation and traceability. CoLab is a big help with that. With CoLab, we document histories of everything automatically just by doing the work. Everything else is stored in a paperless digital record,”
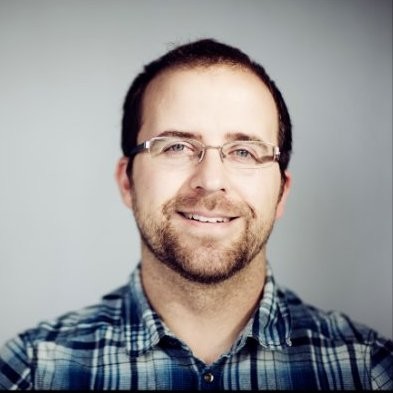
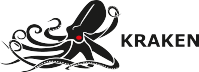
Better products start with better design conversations.
If you’re ready to see how a DES can transform the way your engineering team works, here’s how the process works with CoLab.
- Every conversation starts with a discovery call. During this call, a technical expert will understand your team’s challenges with design review today
- Then, we’ll tailor a demo to address those challenges. This demo includes you, of course, but also some key members from your team who can speak to your challenges in greater detail and vet CoLab as the solution.
- Finally, we do a workshop with more members of your team. This is the fun part! During this workshop, your team will each have temporary CoLab licenses and participate in a sample design review. You and your team will be guided through key features and use cases right inside the CoLab platform.