What is PPAP?
The Production Part Approval Process (PPAP) is a standardized procedure used primarily in the automotive industry but applicable to various manufacturing sectors. It ensures that the suppliers understand and meet the manufacturer's requirements during the production phase.
Key Components:
- Supplier Evaluation: Determining the supplier's capability to meet specific requirements.
- Design Review: Ensuring the product design meets required standards.
- Material Selection: Choosing appropriate materials to align with design specifications.
- Prototype Development: Creating physical or virtual prototypes for testing and validation.
- Testing and Validation: Conducting rigorous tests to ensure quality.
- Final Production Approval: Gaining necessary approvals for mass production.
- Continuous Improvement: Regularly evaluating and improving the process for sustainability and quality.
The main objectives of PPAP include:
- Ensuring Alignment: PPAP ensures that the suppliers' production processes, materials, and products align with the agreed-upon specifications.
- Minimizing Risks: By thoroughly evaluating the suppliers' capabilities, PPAP helps in identifying and mitigating potential risks.
- Enhancing Quality Control: PPAP implementation provides a structured approach to quality management, emphasizing continuous improvement and compliance.
The Importance of PPAP in Manufacturing
In manufacturing, particularly in the automotive industry, consistency, compliance, and quality are paramount. PPAP serves as a bridge between manufacturers and suppliers, fostering collaboration and ensuring that the finished parts meet the required specifications.
Here's why PPAP is essential:
- Customer Satisfaction: By adhering to quality standards, PPAP helps in building trust with customers, ensuring that the delivered products meet their expectations.
- Regulatory Compliance: PPAP follows recognized standards like ISO and IATF, aiding in regulatory compliance.
- Cost Efficiency: Effective PPAP implementation can lead to cost savings by minimizing errors, reducing rework, and avoiding costly delays
.
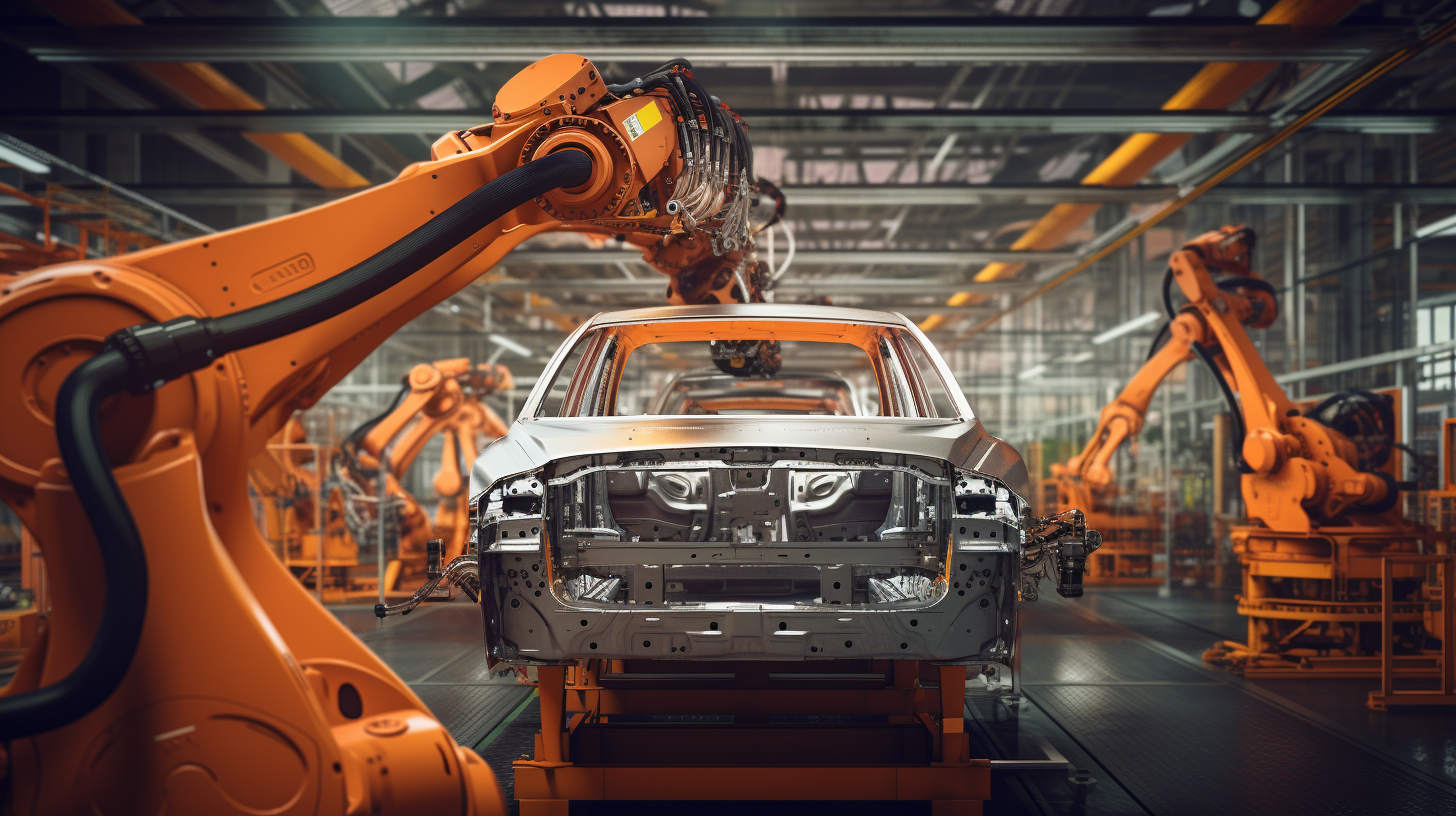