90% of teams see product launch delays due to late stage design changes
The pressure to do more with less has never been higher for engineering teams.
- More projects launched with less headcount
- More collaboration with less resources
- More cost targets with less components
Not to mention, the PD process itself has never been more complex. Higher complexity assemblies, more global teams involved and increased scrutiny from company leadership means the way engineers bring products to market matters.
And yet, 90% of teams see some percentage of product launches delayed due to late-stage design changes.
On average, engineering leaders estimate that 7% of all product launches are delayed for this reason.
This isn’t just stressful, it’s costing you serious resources. Errors caught later in the NPD process mean more time, money and resources spent on mistakes that could have been mitigated much earlier, much faster for much less cost.
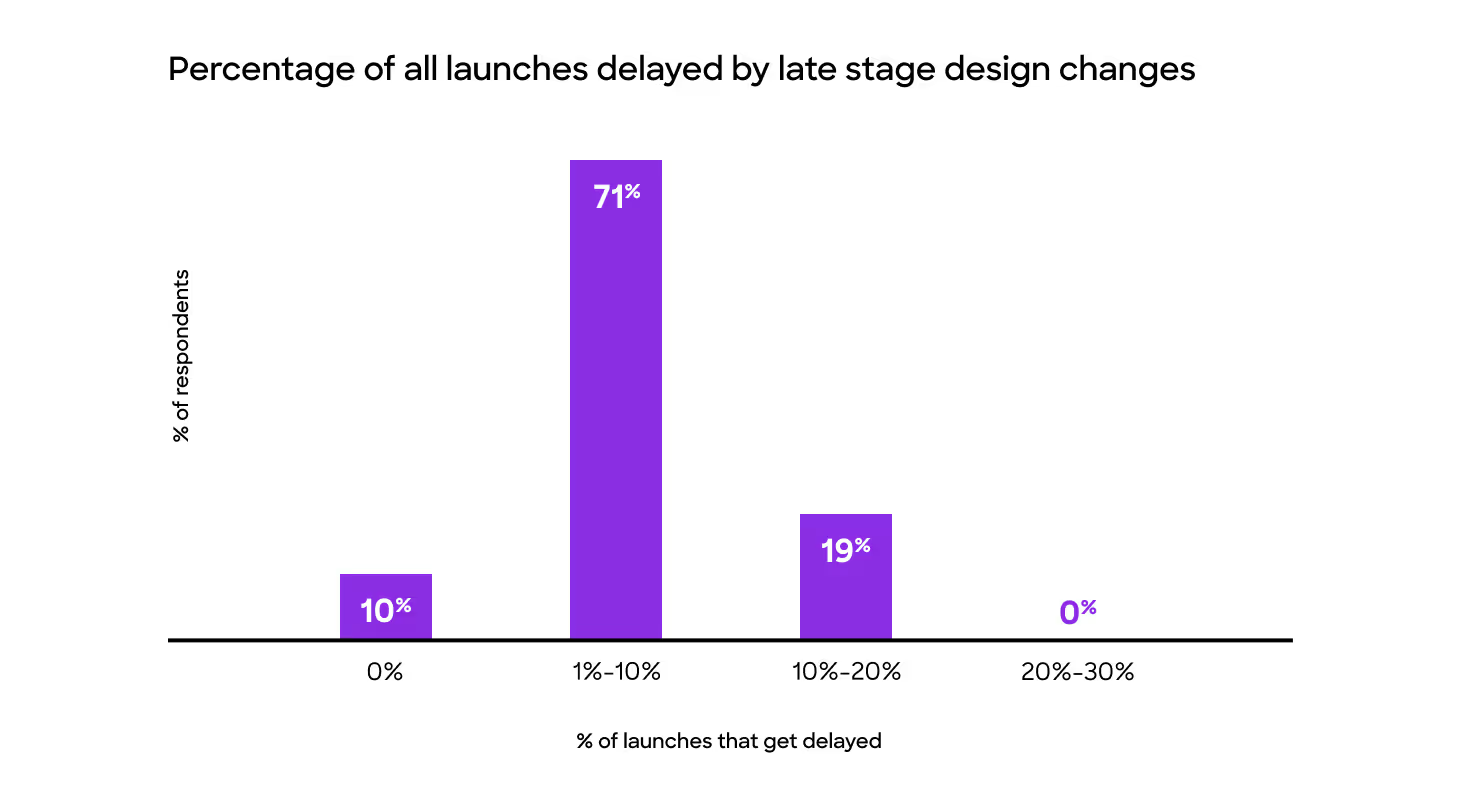
Design review quality is the #1 predictor of whether a product will launch on time
So, what’s the answer to solving product launch delays? Or even project milestone delays?
Improving the team’s ability to generate thorough feedback and catch mistakes ranked higher than improving:
- Requirements tracking: Tracking and responding to shifting requirements
- Resource management: ensuring the right people and subject matter experts are assigned to the project
- Project management: Tracking the team’s progress and improving visibility into next steps.
This isn’t surprising. Most engineering leaders know thorough reviews --especially early in the design process -- prevent rework and expensive downstream changes.
Which means this question is more important than ever: If we know the vast majority of companies delay product launches due to late stage design changes and engineering leaders acknowledge that better design reviews would prevent last stage design changes: what’s wrong with the way we’re doing design reviews?
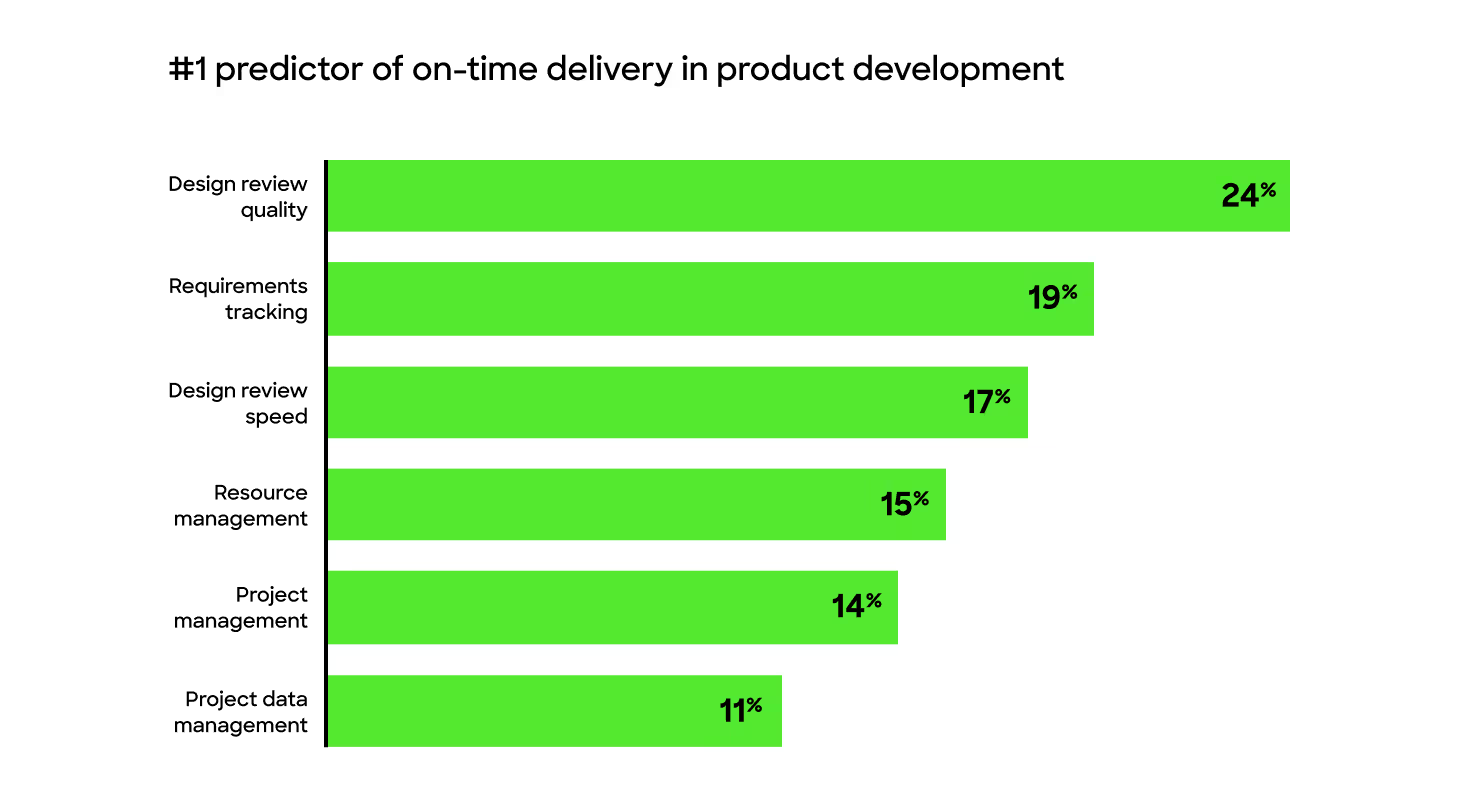
The design review process is killing engineering productivity
The way engineering design reviews are done today is killing NPD time to market. Not to mention engineering productivity.
Not the design reviews themselves but the way engineers do design review.
We can see from the graphs here that design review is done in mostly in spreadsheets, email and screenshot markup tools.
This creates a host of problems:
- Wasted time: In Figure [XX] here, you see a whopping 87% of engineers spend multiple hours to days finding relevant info about a single design decision. Spread that over multiple decisions and multiple projects and you have hundreds of hours wasted just searching through these disconnected tools.
- Manual tracking: These systems each require heavy, manual human effort to maintain. Information in spreadsheets is typed out or copy and pasted. Markups are done by hand, then recorded elsewhere for correction. Email is impossible to track and sort.
- Too much effort: Let’s not forget why we’re all here. Engineers love building great products and solving challenging problems. We hear all too often, “I didn’t do this to become a PowerPoint engineer.” These processes aren’t just killing productivity, they’re destroying engineering morale.
The combination of all this means critical design decisions are lost. Which leaves us with another critical question: Is the design review process really the reason for late stage errors?
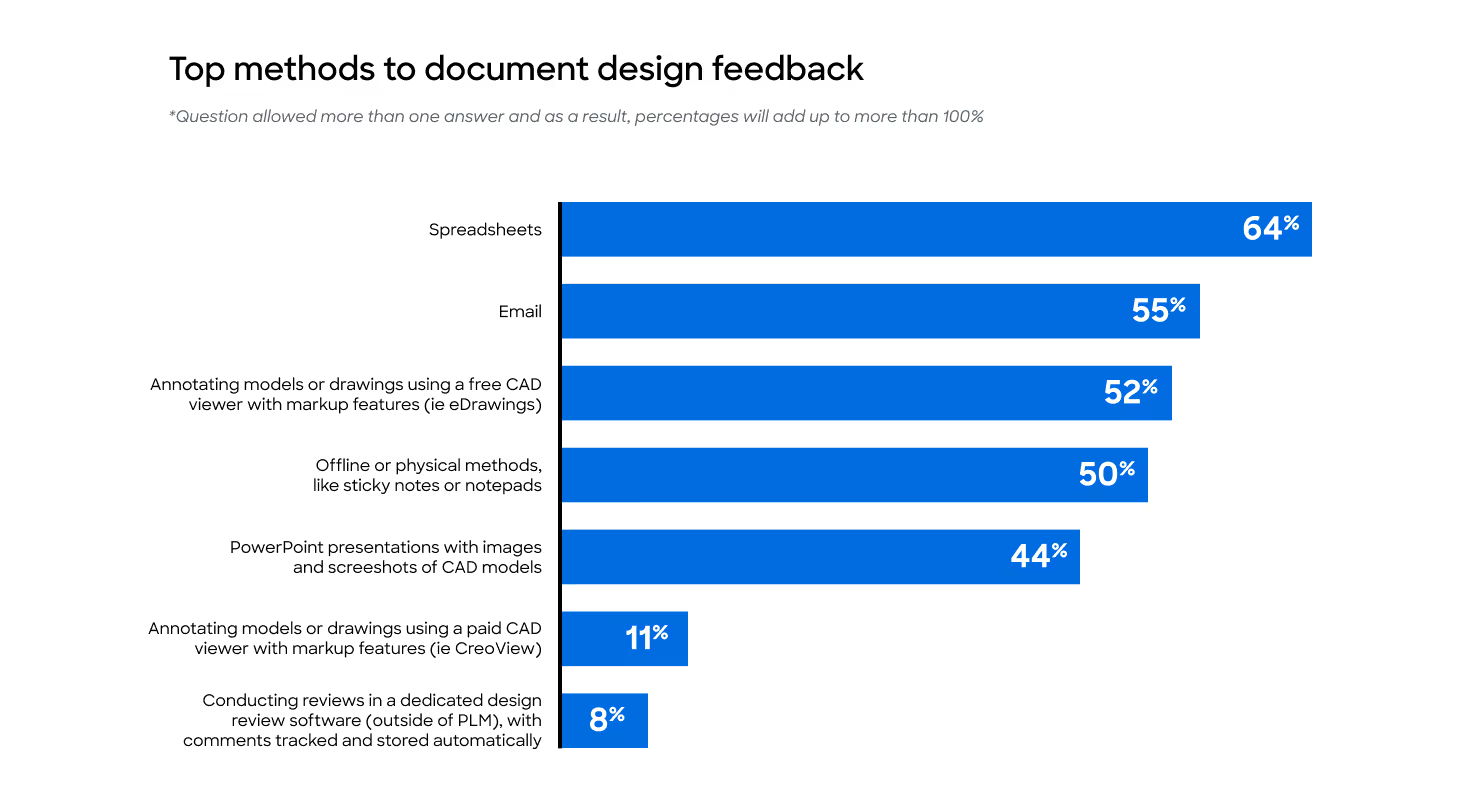
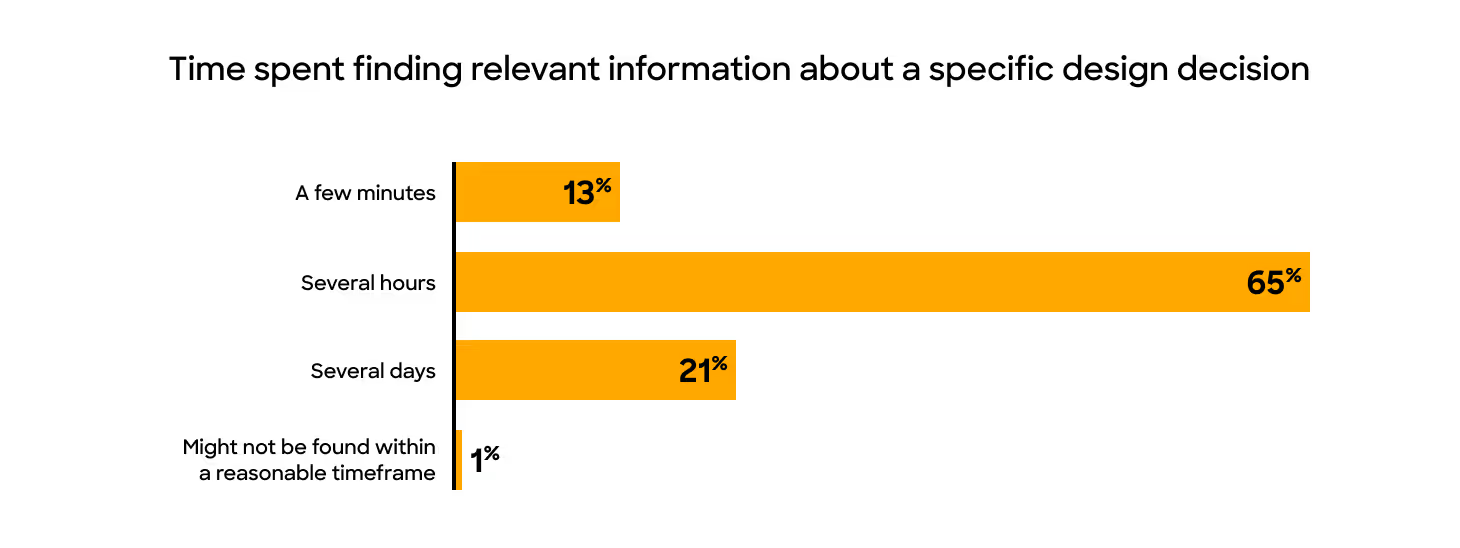
Lost design decisions cause late stage errors
Feedback is the currency of new product development. Yet all that time and effort put into gathering feedback is wasted. According to engineering leaders, 43% of all design decisions are lost.
And only 1% of companies feel confident that all feedback generated during reviews is tracked and addressed.
The most frustrating thing about this? Despite efforts to bring partners from manufacturing, supply chain and other external parties, nearly half this feedback is gone. This is especially exasperating for production partners who see the same errors they pointed out in design cropping up in production.
Now, back to our original conundrum.
- Most companies delay product launches due to late stage design changes.
- Most engineering leaders believe design review quality is the best indicator of an on-time launch.
- The design review process is disjointed, cumbersome and excessively time-consuming.
- As such, nearly half of all design decisions are lost in the mess of gathering design feedback.
There has to be an answer. For engineers who love a problem to solve, they also know there must be a better way.
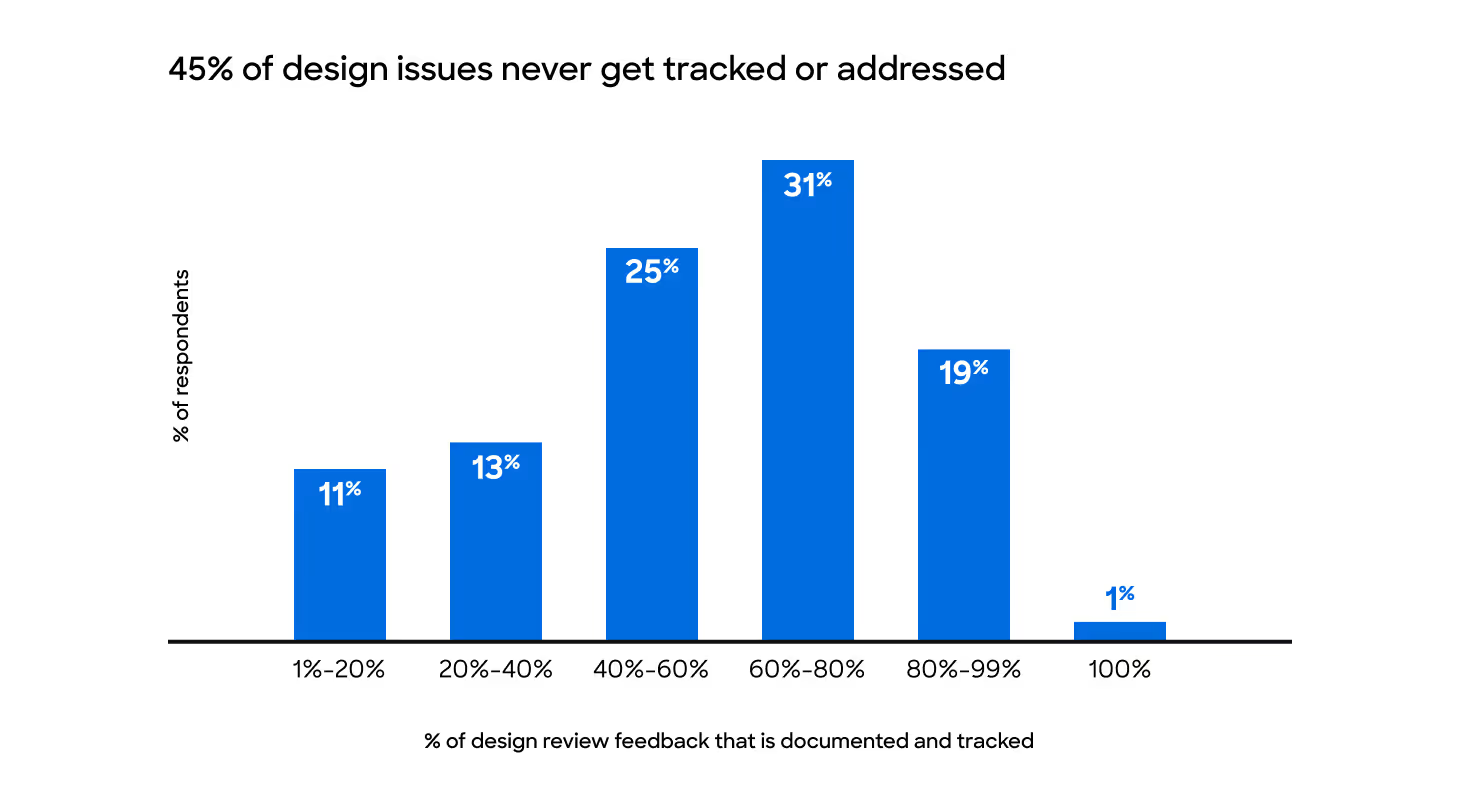
A tool specific to design review is the answer
One answer to solving the nearly ubiquitous product launch delay problem is clear: a better tool is needed for design review.
Every engineering leader who participated in this survey had a PLM, PDM or both. Yet, more training on PLM or expanding PLM access made up only 13% of strategies to prevent NPD delays.
When we look at these potential solutions, an interesting trend emerges:
- Better tools to document design feedback: 19%
- Better tools to communicate design intent: 15%
- Better tools to track and implement design feedback: 13%
- Better tools to communicate design changes: 12%
Most engineering leaders (59%) prescribe better tools for design review as the most effective strategy for prevent delays.
If that tool is not the PLM or PDM and it’s not the mess of disjointed tools used today -- what is it?
It’s a tool purpose-built for facilitating better design reviews. That tool is a Design Engagement System.
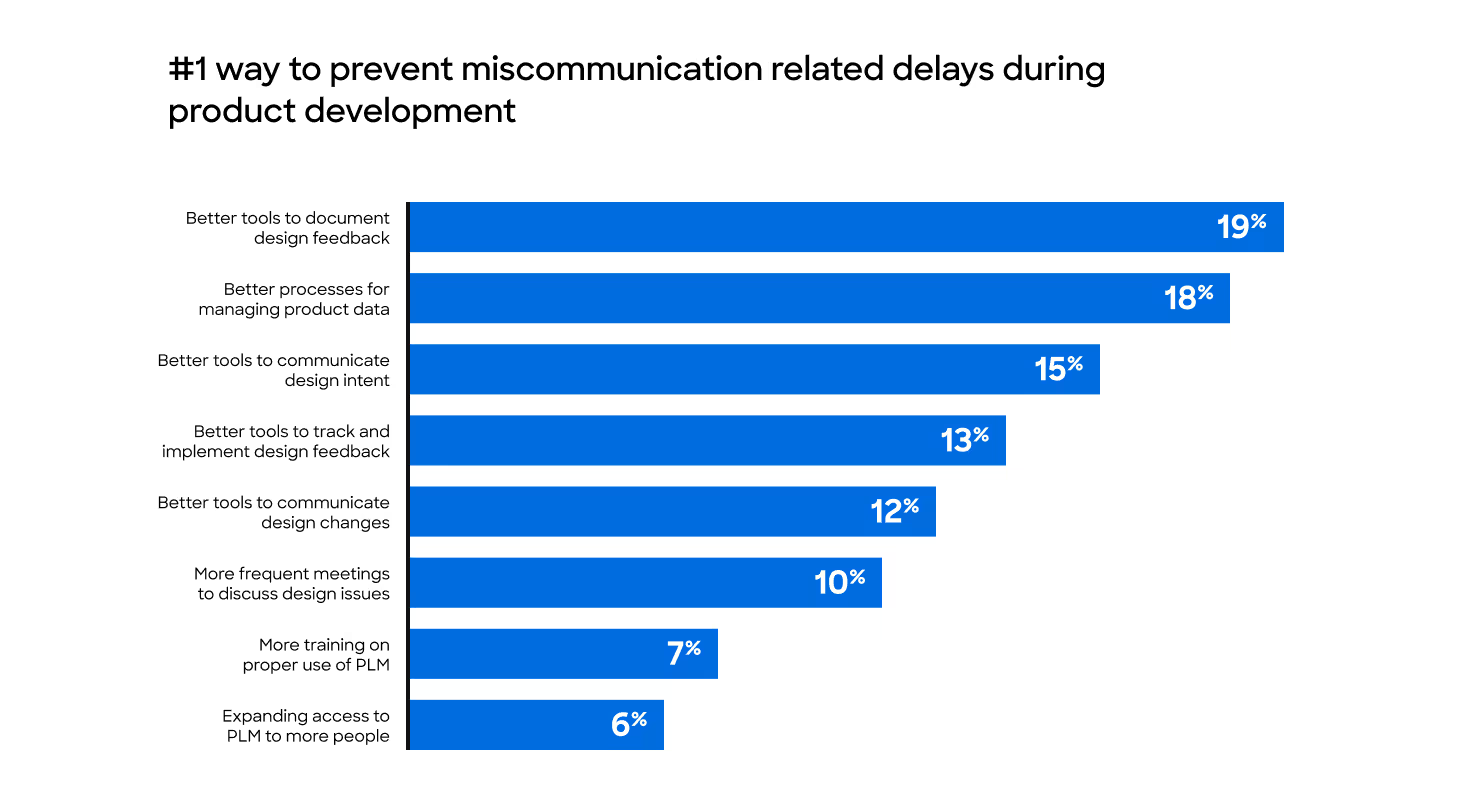
Report methodology and interviewee profile
To get greater insight into the state of complex product development processes, we commissioned a survey of 250 full-time employees, 50% of which are Engineering Managers or Directors, and 50% of which are VPsor C Level Executives.
Respondents work in the manufacturing industry, specifically in industrial equipment, heavy machinery, automotive, and consumer hardware, and are split across the US, the UK, and Western Europe.
All respondents work at companies with 1,000+ employees that have already invested in a PDM or PLM system.
This report was administered online by Global Surveyz Research, a global research firm. The respondents were recruited through a global B2B research panel, invited via email to complete the survey, with all responses collected during October 2023.
The average amount of time spent on the survey was 5 minutes and 44 seconds. The answers to the majority of the non-numerical questions were randomized, in order to prevent order bias in the answers.
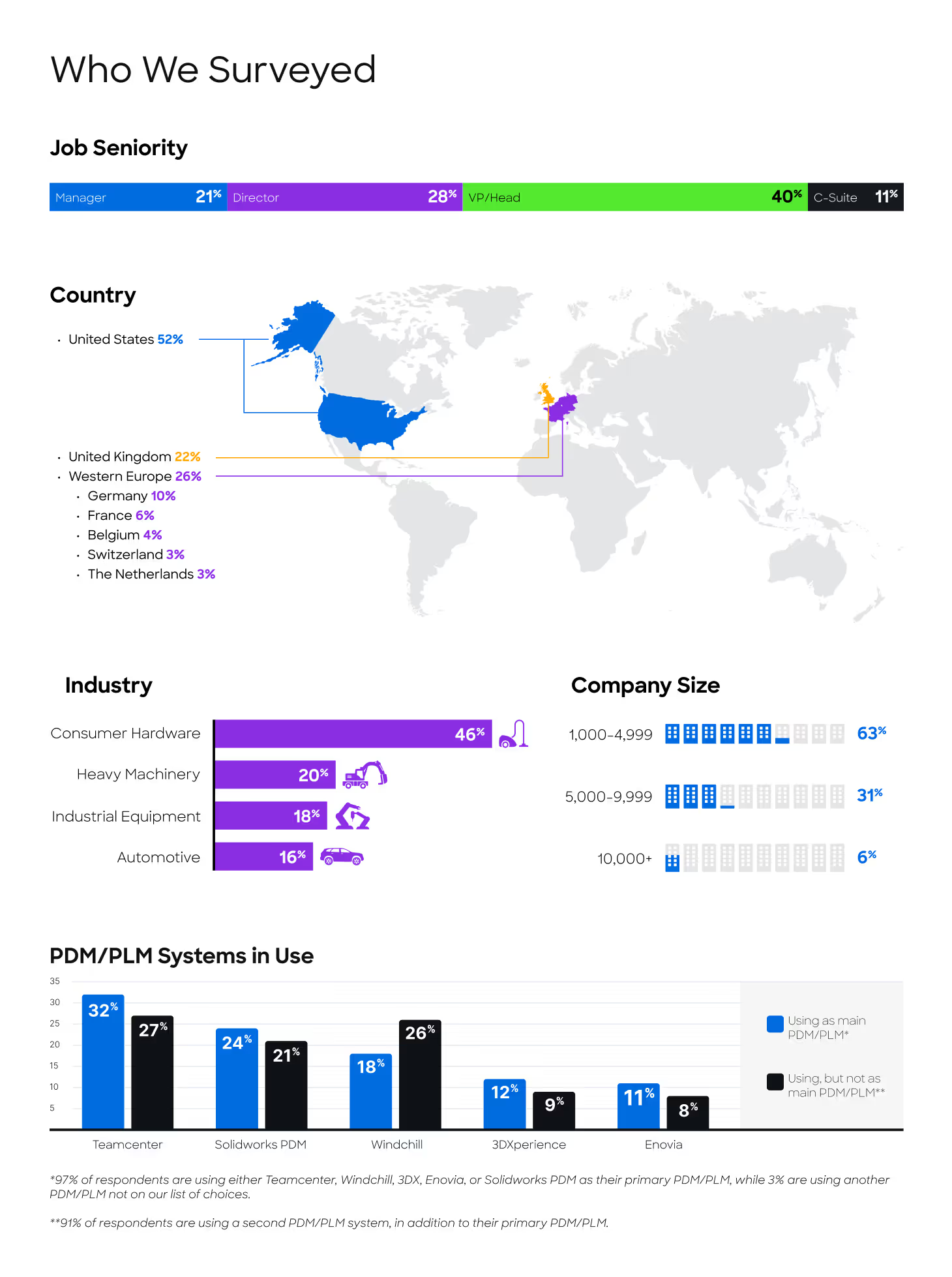