Why engineering teams use PLM + CoLab to improve design quality
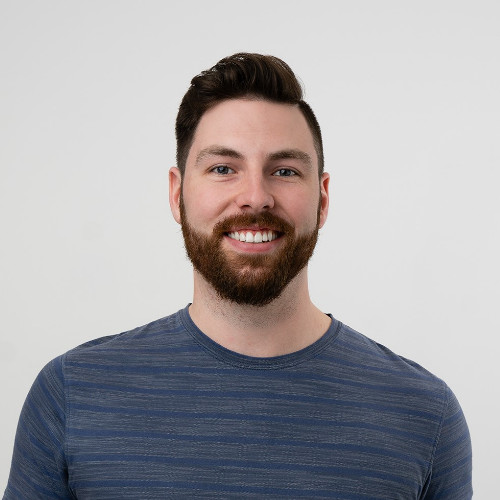
Adam Keating
April 22, 2024
7
min read
The most common question we get from engineering teams who already have a robust PLM in place is: Why do I need PLM and CoLab?
Now, we could give you the spiel about how PLMs are excellent at what they’re built for: records, data housing and controls. And as such, PLM’s rigid architecture isn’t built for effective multi-stakeholder reviews.
And then we could follow that up with how CoLab is purpose-built to facilitate engaging design reviews with multiple stakeholders.
But, rather than try to convince you with “the pitch,” here are three companies that use PLM + CoLab to do more effective design reviews with internal teams, customers and suppliers.
Schaeffler uses PLM + CoLab to optimize design reviews across 300+ engineers
With innovation, agility and efficiency as core business drivers, Schaeffler soon turned their focus to improving engineering efficiency.
Challenge
Recognizing that design review quality is a strong predictor of product development speed and manufacturing efficiency, Schaeffler challenged its digitization and engineering teams to optimize design reviews.
Three opportunities quickly surfaced:
- Maximize the amount of feedback and action items captured during review
- Simplify issue tracking and review management
- Make it easy to reference historical design decisions
As a PTC partner, Schaeffler knew PLM’s benefits: data management, records housing and information control. They also knew PLM’s shortcomings when it came to design review.
Solution
Using CoLab to address these gaps instead, Schaeffler rolled out a 50-user pilot focused on design review, tooling review and design guideline approval.
Now, Schaeffler teams could review designs either live or asynchronously by interrogating CAD and creating feedback in CoLab that syncs back to PLM.
Furthermore, the feedback generated during reviews is automatically documented and organized into a database of action items. That means design reviews, plus any discussion of follow up actions all happens in one place.
As a result, Schaeffler engineers can easily capture customer feedback and ensure that it gets resolved by the next revision.
And the results speak for themselves.
Impact
CoLab made it easy for Schaeffler’s engineering team to capture feedback from more of their subject matter experts. As a result, they’re building a better end product: “Colab helps to improve quality,” remarks Chief Engineer Max Podschwadt. “It provides more team members with easier access to review models and prints, which leads to overall better reviews.”
Automatically documenting design decisions as a part evolves also allows Schaeffler to achieve robust design quality, without the admin headache.
This is one of the reasons that Schaeffler’s 50 user pilot quickly grew to 300 users.
Finally, realizing the importance of connected systems, the digitalization team is working closely with CoLab to plan a phased roll out of CoLab’s Windchill PLM integration.
Schneider Electric uses PLM + CoLab to lower NQC by 15%
With a legacy paper-based process for peer checks and an increasingly remote team, Schneider Electric’s EcoFit Canada team was desperate to go digital for design reviews.
Challenge
In the process of doing custom design work for power equipment, the EcoFit team used peer checks in the final design stages before sharing with other departments. And these were all tracked manually on paper.
The team was fed up.
Naturally, the Schneider team began looking into what functionality was available with their existing tech solutions.
“We did start sharing files and 3D models across the network. We started to use what we could,” says Ivan Filipic, Director of EcoFit Canada.
“Even right now, the best 3D CAD/PLM tools that we have are very cumbersome. You need to be very good with that tool to be able to provide that feedback within it,” Filipic points out. “Only highly-trained people that are very familiar with the tool can really do it.”
Ultimately the EcoFit team realized it was time to rethink their peer check process and the technology used to do it.
Solution
After looking into CoLab, it was the exact solution the Schneider Electric EcoFit team needed.
At first, CoLab did its duty and got the team’s peer checks out of paper and into the digital world. Then, the use cases evolved.
Beyond digitizing their peer checks, adopting CoLab has also simplified how the EcoFit team shares, reviews, and collaborates on design work in general. That’s been particularly useful for senior leaders to stay connected to day-to-day engineering operations with minimal time and effort.
Overall, Schneider Electric didn’t just digitize their design review process — they also made design review more engaging and effective.
Impact
Since adopting CoLab, Schneider Electric has saved time and money by speeding up review cycles and avoiding potential mistakes earlier in the design process.
Peer reviews are more efficient, and more people are involved in providing design feedback. There’s also better communication tracking and revision history.
And ultimately, that all resulted in fewer quality issues. Which meant a reduction in Non-Quality Costs (NQC) — the costs associated with quality escapes, such as rework or scrapped parts.
Just within the first year of using CoLab, the EcoFit team lowered NQC by 15%.
Hyundai Mobis uses PLM + CoLab to land a multi-million dollar OEM contract
The Hyundai Mobis team recognized that a few improvements to their engineering collaboration process would have a real impact on the business.
Challenge
Hyundai Mobis knew the simplest, most effective way to improve engineering collaboration was to find a better way to share design files with internal and external stakeholders.
The right solution would make it easy for the team to do three main things:
- Access and share any file without compromising on rigorous security standards.
- Give customers and prospects a better way to collaborate on any 3D CAD model
- Let engineers focus on strengthening supplier-customer relationships
With the need to collaborate across a range of different file formats and CAD tools, it was complicated to get the right person the right access to the right file at the right time.
And without a standardized, secure way to share these files, simple accessibility was becoming a time-consuming challenge.
As everyone also had different PLM systems, using a single one for file sharing wouldn’t be feasible and wouldn’t meet security standards.
Solution
With team members in both the United States and South Korea, plus OEM customers all over the world, CoLab enabled seamless global design collaboration for Hyundai Mobis.
The Mobis team could now securely share and review 3D files and drawings with anyone.
And while file sharing is much simpler and faster, security is still paramount. Not only does CoLab uphold the Mobis team’s rigorous security standards, the user experience is built with security in mind every step of the way.
The added benefit of CoLab’s multiple PLM integrations was icing on the cake.
Impact
Leveraging CoLab during a major bidding process gave Hyundai Mobis an extra competitive advantage. Ultimately, Hyundai Mobis won a substantial long-term partnership with Fiat Chrysler Automotive.
But, the Hyundai Mobis team can point to other cost wins, too.
Using CoLab has also been a cost-effective way to make files and information more accessible across the company. CoLab makes it possible for anyone to view and manipulate a design in 3D without needing direct access to a CAD or PLM system.
The Hyundai Mobis team has put a positive ROI on CoLab versus a CAD + PLM + UG + add-ons.
And since CoLab is so easy to roll out and use, the Mobis team didn’t have to go through months and months of painful implementation before starting to see this value.
Your PLM alone isn’t enough
It’s not time to ditch your PLM system.
Like we said earlier, PLMs are excellent at what they’re built for: records, data housing and controls. As such, they’re great for use cases like accessing data and files, controlling revisions and releasing formal changes.
What PLM is not effective for is the design review process itself. In recent research, 71% of engineering leaders admit their teams don’t use PLM during product development at all. The workflows are simply too rigid to allow for conversations, iterative feedback and many design participants.
So, what’s the solution? Most engineering leaders recognize that better tools are needed to address this gap.
That tool is a Design Engagement System (DES). As a DES, CoLab facilitates frequent, trackable collaboration among all key stakeholders during the design review process. Furthermore, CoLab is purpose-built for having multiple stakeholders giving, receiving and acting on critical design feedback in real-time.
CoLab also works with PLM systems, giving engineering teams a central place to have the meaningful, productive discussions that get better products to market faster.
What’s next?
If you’re ready to see how a DES can transform the way your engineering team works, here’s how the process works with CoLab.
- Every CoLab DES conversation starts with a discovery call. During this call, a technical expert will understand your team’s challenges with design review today
- Then, we’ll tailor a demo to address those challenges. This demo includes you, of course, but also some key members from your team who can speak to your challenges in greater detail and vet CoLab as the solution.
- Finally, we do a workshop with more members of your team. During this workshop, your team will each have temporary CoLab licenses and participate in a sample design review. You and your team will be guided through key features and use cases right inside the CoLab platform.