How to optimize your engineering design review process for ISO 9001:2015
.webp)
Meagan Campbell
November 9, 2022
11
min read
If you’re an engineering leader at a large company following ISO 9001 requirements, you likely have some degree of responsibility for overseeing and continually improving design processes. (Same goes for standards that are similar or adjacent to 9001, such as ISO 13485.)
Let’s say you’ve been tasked with making some improvements to the design review process, either in preparation for an upcoming ISO audit or as a result of recent audit findings. Or perhaps you simply have a specific goal to improve design reviews for your team and you need to know how to make changes while staying ISO compliant.
Either way, and no matter how long you’ve been working within an ISO 9001 environment (or not), it’s a complicated standard that can be challenging to interpret. Since it’s globally recognized and can apply to organizations of any size or type, the language is broad and general enough to be applied across vastly different businesses. And while that’s good for standardization, it’s bad for the average person who just wants to know, in simple terms, what they actually need to do.
Because, even if there’s ultimately a quality leader or team who’s primarily responsible for the ISO audit process, the requirements still impact how the engineering team works. But by better understanding quality standards like ISO 9001 from an engineering-specific context, you’ll have the knowledge you need to spot ways your design reviews can be improved — without documentation getting in the way or slowing you down.
So what do you actually need to know?
This article breaks down some key information about what ISO 9001:2015 means for your design review processes, along with a few best practices your engineering team can follow to keep auditors happy.
ISO 9001 and what it really means for engineering teams
Assuming you already understand that ISO 9001 is an international QMS standard and that you have some basic understanding of what certification involves, it’s still helpful to start with a refresher on the foundational concepts.
ISO, the International Organization for Standardization, follows seven quality management principles (QMPs). These seven QMPs form the basis for ISO 9001, along with other quality management standards. The seven quality management principles of ISO are:
- Customer focus
- Leadership
- Engagement of people
- Process approach
- Improvement
- Evidence-based decision making
- Relationship management
Ultimately, ISO 9001 is about having an effective QMS in place that makes sure your processes are doing what they’re supposed to do, and that you’re meeting and improving your own quality goals (whatever they are). It means you’re defining your processes, documenting them, reviewing them, and improving them. It also means that your customers can trust that you’re a company that puts out a reliable product.
When implemented properly, a solid QMS helps your team avoid and minimize errors while also making sure you’re continually improving your processes.
In reality though, keeping up with the documentation that comes along with ISO 9001 can pose a challenge — especially when teams are in a crunch to deliver on time and on budget (not to mention dealing with all the curveballs and external pressures that inevitably interfere with even the best-laid plans).
But the good news is: it doesn’t necessarily have to be that way.
ISO released a guidance document that notes, “It is stressed that ISO 9001 requires (and always has required) a ‘Documented quality management system’, and not a ‘system of documents’.”
ISO 9001:2015 is meant to allow an organization “flexibility in the way it chooses to document its quality management system” so that each organization can “determine the correct amount of documented information needed in order to demonstrate the effective planning, operation and control of its processes and the implementation and continual improvement of the effectiveness of its QMS.”
That means your processes are still up to you. ISO doesn’t want you to become overly focused on paperwork any more than you do. You just need to be able to show your work.
So how can you make reviews more productive and efficient, while still maintaining robust traceability and proper documentation? In other words, how can you speed up the review process without dropping the ball on ISO requirements? First things first, let’s take a look at what those requirements actually are.
What are the ISO 9001:2015 requirements for design review?
Design reviews play a crucial role when it comes to ISO 9001:2015 certification. For engineering teams, clause 8.3 Design and development of products and services is one of the most relevant sections of the ISO 9001:2015 standards. In particular, subclauses 8.3.4 and 8.3.6 contain the important information you’ll need to ensure your review processes always stay ISO compliant.
.png)
Subclause 8.3.4 Design and development controls covers the controls in your design process, including design reviews, and sets out standards for the review process.
.png)
Subclause 8.3.6 Design and development changes covers any design changes that come up during the design process, and sets out similar standards for the change review process.
.png)
Although it’s written in the typical legalese you’d expect from such a wide-reaching international quality standard, a little common sense goes a long way when interpreting the requirements. After all, there’s likely lots of overlap between what ISO 9001 lays out and what you consider to be your own fundamental principles of quality engineering design. It’s just that, with ISO 9001 — the devil’s in the documentation.
You’ll notice that both of the subclauses above refer to retaining “documented information” on all your review activities. In the context of ISO 9001, documented information has a very specific meaning that’s defined in clause 7.5 Documented information.
There are two buckets when it comes to documented information: documented information explicitly required by ISO, and any documented information your organization determines necessary for your QMS to be effective. Under subclause 7.5.3 Control of documented information, documents can be in any form or type of medium (as long as they meet all outlined requirements).
Again, there really is a lot of flexibility within these requirements for organizations to structure things according to their unique needs and circumstances.
So when it comes to determining your own team’s approach to ISO 9001 documentation across different types of design reviews, keep in mind this guidance from ISO: “Analysis of the processes should be the driving force for defining the amount of documented information needed for the quality management system, taking into account the requirements of ISO 9001:2015. It should not be the documented information that drives the processes.”
Engineering design review best practices to meet what ISO 9001 auditors look for
Okay, so now what? Even with all that context on what ISO is, how it works, and what it requires… how and where do you actually start to take action on optimizing your design review processes, in line with ISO 9001?
Sadly, if we told you there were “8 easy steps” for getting there, we’d be charlatans. There’s no one-size-fits-all checklist, and there are no silver bullets. Remember, ISO 9001 is as much about continuous improvement as it is about customer focus. Quality management is not a “one and done” kind of thing.
That means nobody can determine or dictate your exact action plan or next steps for you. But by gaining a deeper understanding of ISO 9001:2015, you’re able to make better-informed decisions about your engineering processes and how to improve your design reviews.
Here’s what ISO has to say about the overall goal of the audit process, specific to clause 8.3: “The objective of auditing the design and development process is to determine whether it is managed and controlled to enable products and services to meet their intended use and specified requirements."
When it comes to design reviews specifically, auditors “should verify that the overall design and development process is controlled in accordance with the organization’s original plan, that it is being reviewed and that the design and development reviews take place at appropriate planned stages.”
These are the considerations auditors make when evaluating your design review process:
.png)
If we had to boil down all the ISO 9001 requirements for design reviews into three key points, it largely comes down to being able to answer “Yes” to these three questions:
- Do you have a defined process for when and how design reviews occur?
- Is your process thorough, systematic, and effective?
- Can you provide records that show a clear history of your processes being followed?
While there may be slightly more to it, those are the core pillars of a review process that’s compliant with ISO 9001:2015.
But what are the best practices that make for a truly effective design review process?
No matter how mature or modern your processes already are (or not), any engineering team can apply these three design review best practices to improve effectiveness:
- Standardize your review process. For many engineering teams today, lack of standardization means nobody follows the exact same design review process. But when you define a repeatable process with a consistent set of steps, you lessen the cognitive effort it takes to facilitate reviews — which means more brainpower stays available for the important stuff, like actual design.
- Centralize review information in one place. The more scattered your review process is across tools like email, chat, spreadsheets, slideshows, PDFs, etc… the more likely things are to slip through the cracks. When you consolidate reviews into a central hub, everything becomes more organized and more efficient. So the next time you need to track down who approved a particular design decision and why, you won’t have to spend hours or days sifting through messy email chains and random chat threads.
- Leverage automatic tracking and histories. Remember how we said the devil’s in the documentation? Well, thanks to the magic of technology, documenting your reviews doesn’t have to actually mean creating an entirely separate workflow and set of steps. By incorporating a little strategic automation, you can document your review history as you do the work. No extra admin or paperwork needed!
How cloud-based collaboration can support your ISO 9001 goals
Given the flexibility ISO 9001 offers for how you structure your processes and the emphasis on keeping documented information of your review activities, it follows that there are many different tools you can potentially incorporate into your design reviews.
Beyond core programs like your CAD and PLM systems, most engineering teams today are also using or considering options for cloud-based collaboration software. Part of the problem, though, is the sheer number of options available — most of which aren’t tailor-made for collaborating on mechanical design. That means collaboration tools that work great for other industries (think SharePoint, Jira, Asana, etc) don’t always meet the needs of engineers sharing and reviewing 3D CAD files.
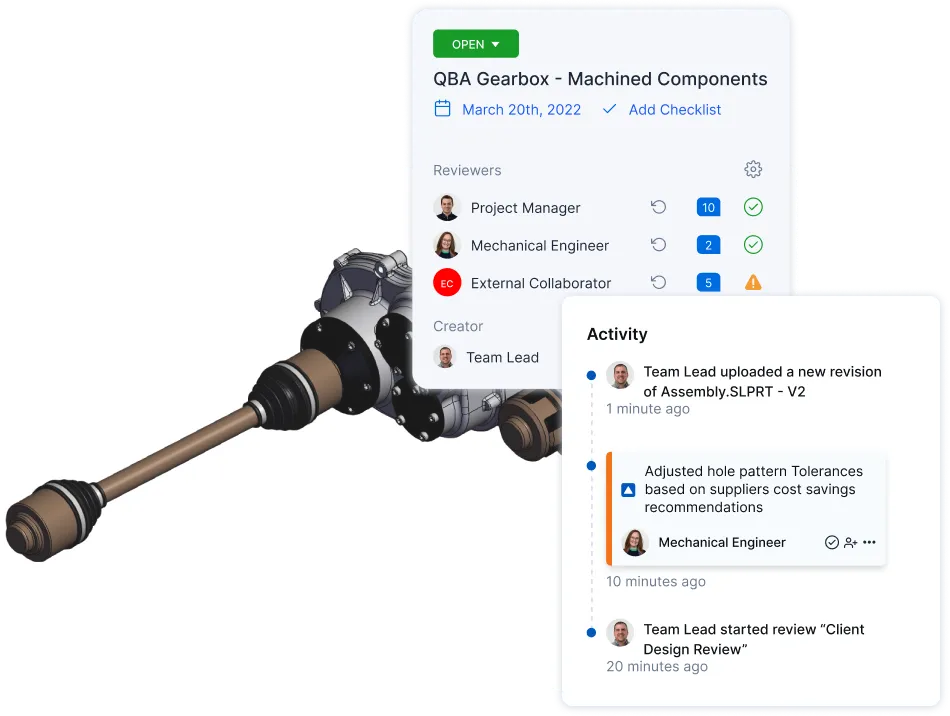
Kraken Robotics, a global leader in marine technology, achieved ISO 9001:2015 certification in February 2021. On the path to meeting ISO 9001’s requirements, the Kraken team started using CoLab for design reviews in 2019.
"ISO certification focuses on documentation and traceability,” explains Greg Walsh, Mechanical Team Lead with Kraken Robotics. “CoLab is a big help with that. With CoLab, we document histories of everything automatically just by doing the work."
Since CoLab is easily accessed from any web browser and integrates directly with SolidWorks, adopting the tool enabled a better workflow for reviews. “We knew what our quality requirements were, and CoLab allows us to meet those goals in an efficient way through a very lean process,” says Walsh. “For me, this is a one-stop-shop for design reviews.”